Molding plays a critical role in medical contexts, particularly in obstetrics and healthcare. Precision mold medical products are essential in the creation of medical devices, where exact specifications and biocompatibility are required. These medical molding products play a key role in the development of medical devices, ensuring they meet the high standards necessary for safety and functionality.
Low-Volume to High-Volume Production Capabilities
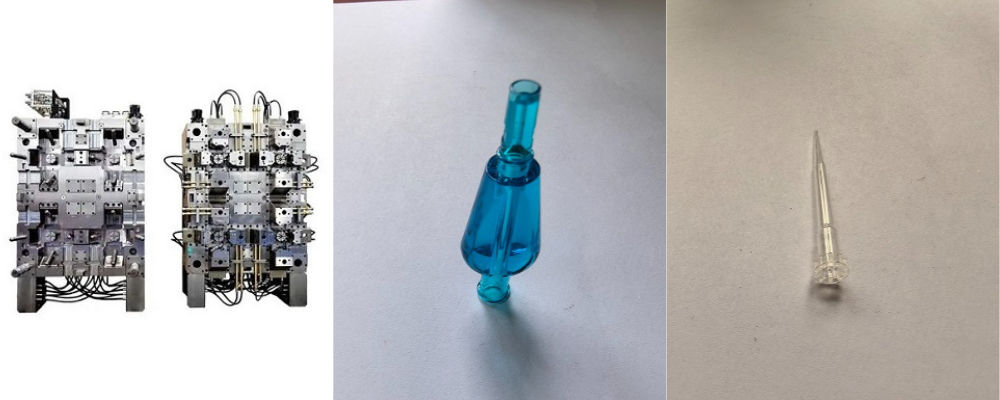
Attributes | Details |
---|---|
Place of Origin | Dongguan, Guangdong, China |
Brand Name | LY Medical Injection Mold |
Product Name | Medical Injection Mold |
Color | Customized Colors |
Certification | ISO9001:2015 |
Service | OEM\ODM |
Plastic Material | ABS/PP/PS/PE/PVC/PA6/PA66.....etc |
Mold Life | 300000~1000000 Shots |
Tolerance | 0.005~0.1mm |
Customized Surface Process | Polishing, Die Custing, Brushing, Anodizing Etc |
Feature | Sustainable |
Selling Units | Single item |
Molding Definition in Medical: Medical Injection Molding Explained
Medical injection molding is a specialized process used to manufacture high-precision, sterile, and functional components for medical devices and equipment. This technique, which involves injecting molten material into a mold to create various parts, is crucial in the production of items used in healthcare, from simple tools like syringes to complex devices like surgical instruments and implants. The following sections will delve into the key aspects of medical injection molding, explaining its process, materials used, applications, and advantages within the healthcare industry. Understanding this technology is essential for appreciating how it contributes to the creation of reliable, safe, and effective medical products.
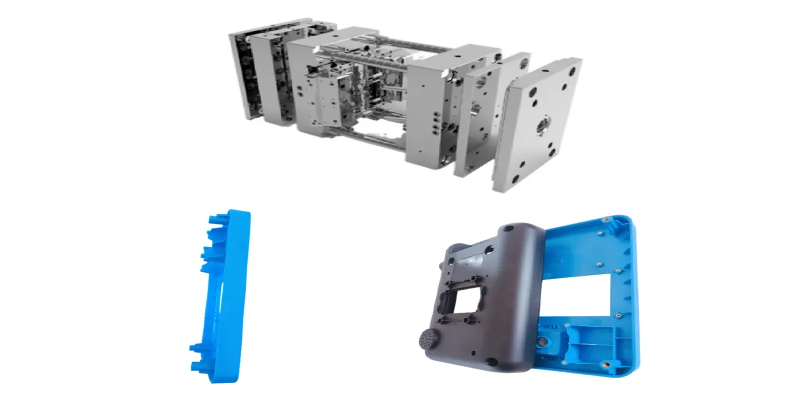
Process Overview of Medical Injection Molding
Medical injection molding is a highly controlled manufacturing process that begins with the preparation of the raw material, typically a thermoplastic or thermoset material. The material is heated until it becomes molten and then injected under high pressure into a precisely designed mold. The mold itself is made to match the exact shape of the desired product. Once the material has cooled and solidified, the mold is opened, and the finished component is ejected. The process is repeated continuously, allowing for high-volume production of consistent, high-quality parts.
In medical molding applications, the process must adhere to strict quality standards and regulations to ensure that each part is safe for patient use. Sterilization is also an important consideration in medical molding to prevent contamination, and often additional steps are taken, such as the use of medical-grade materials and adherence to FDA or ISO standards.
Regulatory Compliance and Quality Control
Given the critical nature of medical devices and components, regulatory compliance is an essential part of the medical injection molding process. Manufacturers must adhere to strict regulations such as the FDA’s 21 CFR Part 820 (Quality System Regulations) and ISO 13485 (Medical Devices Quality Management Systems). This ensures that the molds, materials, and final products are tested and meet the necessary standards for patient safety.
Throughout the production process, quality control is integral, with rigorous testing to check for defects, sterility, and functionality. Inspections may include visual checks, mechanical testing, dimensional analysis, and testing for contamination, ensuring that each part is of the highest quality and meets safety standards.
Medical injection molding is a versatile, efficient, and precise process used to manufacture critical components for the medical industry. From syringes and implants to diagnostic tools and packaging, this method enables the mass production of high-quality, consistent, and safe products. The process relies on a careful balance of materials, mold design, and strict regulatory adherence to ensure that the final products meet the stringent requirements of the healthcare sector. By providing advantages such as high-volume production, material flexibility, and design complexity, medical injection molding plays an essential role in modern healthcare innovation.
Molding Definition in Medical Manufacturing: Types, Advantages, and Applications
Medical injection molding is a crucial manufacturing process used to produce high-precision plastic components for healthcare applications. This process ensures consistency, sterility, and cost-effectiveness in mass production. Various molding techniques cater to different medical needs, from intricate surgical tools to biocompatible implants. Each method has its own advantages, limitations, and applications. Below, we explore the primary types of medical injection molding and their significance in the healthcare industry.
Conventional Injection Molding: Standard Process for Mass Production
Conventional injection molding is the most widely used technique in medical manufacturing. It involves melting thermoplastic materials and injecting them into a mold cavity under high pressure, where they cool and solidify into the desired shape.
Advantages:
- High production efficiency with fast cycle times
- Excellent repeatability and precision
- Suitable for complex and detailed designs
- Wide range of biocompatible materials available
Limitations:
- High initial tooling costs
- Design modifications can be expensive
- Not ideal for extremely small or intricate components
Applications:
- Syringes and IV components
- Diagnostic test kits
- Medical casings for devices like inhalers and pumps
Micro Injection Molding: Precision for Miniature Components
Micro injection molding is a specialized process designed for producing extremely small and intricate medical parts with high precision. This method uses ultra-small mold cavities and specialized machinery to manufacture components with dimensions in the micrometer range.
Advantages:
- Ability to produce components with tight tolerances
- Reduced material waste due to precise injection control
- Ideal for high-volume production of small parts
Limitations:
- Requires advanced tooling and machinery
- Higher manufacturing costs due to precision demands
- Limited to specific applications that justify the cost
Applications:
- Microfluidic devices
- Tiny surgical instruments
- Miniature implants and drug delivery components
Liquid Silicone Rubber (LSR) Molding: Flexibility and Biocompatibility
LSR molding is a process used for medical-grade silicone parts that require flexibility, durability, and biocompatibility. Liquid silicone rubber is injected into heated molds, where it cures into the final shape.
Advantages:
- Excellent biocompatibility and resistance to chemicals
- Can withstand extreme temperatures and sterilization processes
- Soft and flexible, making it ideal for wearable medical devices
Limitations:
- More complex processing than thermoplastics
- Higher material costs compared to standard plastics
- Requires specialized molding equipment
Applications:
- Catheters and tubing
- Medical wearables and prosthetic components
- Seals and gaskets for medical equipment
Overmolding: Enhancing Functionality with Multi-Material Integration
Overmolding is a technique where a second layer of material is molded over an existing part, creating a composite component with improved functionality, such as enhanced grip or cushioning.
Advantages:
- Increases durability and patient comfort
- Reduces assembly time by integrating multiple materials in one step
- Enhances grip and ergonomics for medical instruments
Limitations:
- More complex molding process
- Requires careful material compatibility selection
- Longer cycle times compared to single-material molding
Applications:
- Surgical instrument handles
- Soft-touch medical device casings
- Ergonomic grips for dental and orthopedic tools
Insert Molding: Combining Plastic with Other Materials
Insert molding involves placing a preformed component, such as a metal insert, into the mold before injecting plastic around it. This process is used to create hybrid medical components that require enhanced strength and functionality.
Advantages:
- Stronger and more durable than separately assembled components
- Reduces assembly time and improves product integrity
- Ideal for medical devices requiring metal-plastic integration
Limitations:
- Higher manufacturing complexity
- Precision alignment of inserts is critical
- Limited design flexibility due to insert placement constraints
Applications:
- Needle hubs for syringes
- Electrical connectors in medical devices
- Surgical tools with integrated metal reinforcements
Medical injection molding plays a critical role in the production of safe, precise, and cost-effective medical components. Each molding technique—whether conventional injection molding, micro molding, LSR molding, overmolding, or insert molding—offers unique benefits tailored to specific medical applications. By understanding the strengths and limitations of these processes, manufacturers can select the most suitable method to meet the stringent requirements of the healthcare industry. Medical molding services provide expertise in these various techniques, ensuring that the final products are of the highest quality, meet regulatory standards, and are optimized for their intended use in the medical field.
Molding Definition in Medical: Materials Used in Medical Injection Molding
Medical injection molding is a precise and highly controlled process that involves the creation of medical devices and components from various materials. The choice of material is crucial in determining the final product’s performance, safety, and compliance with medical standards. In the medical field, materials need to meet specific criteria, including biocompatibility, sterility, and durability. This section will explore the different types of materials commonly used in medical injection molding, their properties, and their respective roles in producing medical products. The materials vary depending on the application, ranging from disposable medical devices to long-term implants. Let’s break down the most commonly used materials in medical injection molding and their advantages.
Thermoplastics in Medical Injection Molding
Thermoplastics are the most commonly used materials in medical injection molding due to their versatility, ease of processing, and biocompatibility. These materials can be melted and reformed multiple times, making them ideal for high-volume manufacturing. Thermoplastics also provide the flexibility to produce complex and intricate designs while maintaining strength, durability, and clarity.
Common Thermoplastic Materials:
- Polypropylene (PP): This material is widely used for medical applications such as syringes, IV connectors, and diagnostic devices due to its excellent chemical resistance, low cost, and ease of sterilization. PP is non-toxic and can be easily molded into complex shapes.
- Polyethylene (PE): Known for its flexibility and chemical resistance, PE is commonly used in applications such as medical tubing, catheters, and drug delivery systems. It is also used for packaging purposes like sterile bags and containers.
- Polycarbonate (PC): Polycarbonate is a strong, transparent material often used for components requiring clarity, such as surgical instruments, medical housings, and diagnostic devices. Its durability and resistance to impact make it ideal for high-strength applications.
- Polyvinyl Chloride (PVC): PVC is used for medical products such as blood bags, tubing, and intravenous (IV) sets. It is valued for its flexibility, low cost, and ability to be sterilized. It can be formulated for rigid or flexible applications depending on the specific needs.
Elastomers and Rubber in Medical Injection Molding
Elastomers, also known as rubbers, are materials known for their flexibility, stretchability, and resilience. They are widely used in the medical industry for components that need to seal, cushion, or stretch without breaking. Elastomers provide a good balance of performance and comfort, making them ideal for medical devices that come into direct contact with the skin or other body parts.
Common Elastomer Materials:
- Thermoplastic Elastomers (TPE): TPEs are used in medical injection molding due to their ability to combine the elasticity of rubbers with the processability of plastics. They are commonly used for creating seals, gaskets, and flexible connectors for medical devices like catheters and surgical tools.
- Silicone Rubber: Silicone is a highly biocompatible elastomer that is resistant to heat, chemicals, and aging. It is used in medical applications like tubing, seals, and implants. Its softness and flexibility make it ideal for sensitive applications such as contact lenses, drainage tubes, and prosthetics.
- Butyl Rubber: Butyl rubber is used for medical seals and stoppers due to its excellent air barrier properties, making it suitable for creating closures for pharmaceutical products or IV bags.
Bioabsorbable Materials in Medical Injection Molding
Bioabsorbable materials are designed to break down over time within the human body, making them especially useful for temporary implants or devices that need to dissolve after fulfilling their purpose. These materials are often used in medical applications such as surgical implants, stents, and drug delivery systems, where permanent implants are unnecessary or undesirable.
Common Bioabsorbable Materials:
- Polylactic Acid (PLA): PLA is a biodegradable plastic often used in medical devices like sutures, stents, and drug delivery devices. It is derived from renewable resources like corn starch and can safely degrade in the body without causing harm.
- Polycaprolactone (PCL): This bioabsorbable polymer is used in the creation of temporary implants that gradually degrade over time. It is often used for drug delivery systems, as it can be tailored to release therapeutic agents at controlled rates.
- Polyglactin (Vicryl): Widely used in absorbable sutures, Vicryl is a co-polymer of lactic acid and glycolic acid that naturally dissolves in the body over time.
Bioabsorbable materials offer the advantage of reducing the need for surgical removal of implants and minimizing long-term complications.
Biocompatible Polymers in Medical Injection Molding
Biocompatible polymers are essential in medical injection molding because they are specifically designed to interact safely with the human body without causing adverse reactions. These materials are ideal for implants, prosthetics, and devices that must come into direct contact with biological tissues.
Common Biocompatible Polymers:
- Polymethyl Methacrylate (PMMA): Also known as acrylic, PMMA is a transparent, rigid polymer often used for medical device housings, lenses, and components that require clarity and biocompatibility. It is commonly used for contact lenses, intraocular lenses (IOLs), and dental materials.
- Polyetheretherketone (PEEK): PEEK is a high-performance polymer that is used for demanding applications, such as orthopedic implants and spinal fusion devices. It is highly biocompatible, resistant to wear, and able to withstand high temperatures and sterilization processes.
- Polyamide (PA) / Nylon: Nylon is a durable and flexible material used for making medical products such as surgical meshes, medical packaging, and drug delivery components. It offers excellent wear resistance and can be sterilized by autoclaving.
These polymers are specially engineered to meet the strict standards of the medical industry, ensuring that they do not cause harmful reactions when implanted or used within the body.
Specialty Materials in Medical Injection Molding
In addition to the standard thermoplastics, elastomers, and bioabsorbable materials, there are several specialty materials used in medical injection molding that provide unique properties for specific medical applications. These materials are tailored to meet the needs of highly specialized devices or advanced medical technologies.
Common Specialty Materials:
- Carbon-Filled Polymers: Carbon fillers can be added to polymers like polypropylene or PEEK to enhance their strength, conductivity, or radiation resistance. These materials are used in diagnostic devices, such as X-ray and MRI equipment, where radiation shielding or electrical conductivity is required.
- Glass-Filled Polymers: Glass fibers can be integrated into plastics like polypropylene or nylon to increase the material’s strength and rigidity, which is essential for structural components of medical devices that require high mechanical performance, such as bone screws or orthopedic implants.
- Conductive Polymers: Conductive materials, often used in electronics embedded within medical devices (e.g., pacemakers or monitoring systems), allow the efficient transfer of electrical signals, which is critical for their function.
Specialty materials are often selected for their ability to meet highly specific requirements of the medical device, such as resistance to radiation, high tensile strength, or the need to conduct electricity.The choice of materials used in the medical injection molding process is fundamental to the performance, safety, and compliance of medical products. Whether it’s thermoplastics, elastomers, bioabsorbable materials, biocompatible polymers, or specialty materials, each type plays a critical role in ensuring that medical devices function properly and meet stringent regulatory requirements. By understanding the properties and applications of these materials, manufacturers can select the right material for each product, whether it’s a disposable syringe, a long-term implant, or a complex diagnostic device. The versatility and precision offered by these materials are why the medical injection molding process is the go-to process for creating high-quality, reliable medical components.
Molding Definition in Medical Industry: Applications of Medical Injection Molding
Medical injection molding is a highly versatile manufacturing process that plays a critical role in producing a wide range of medical components and devices. This technology ensures precision, sterility, and cost-effectiveness, making it indispensable in the healthcare sector. Medical injection molding is used to create disposable medical supplies, surgical instruments, diagnostic equipment, and even implantable devices. The applications of this process extend across various medical fields, each with specific requirements and benefits. Below, we explore the major applications of medical injection molding and their significance in modern medicine.
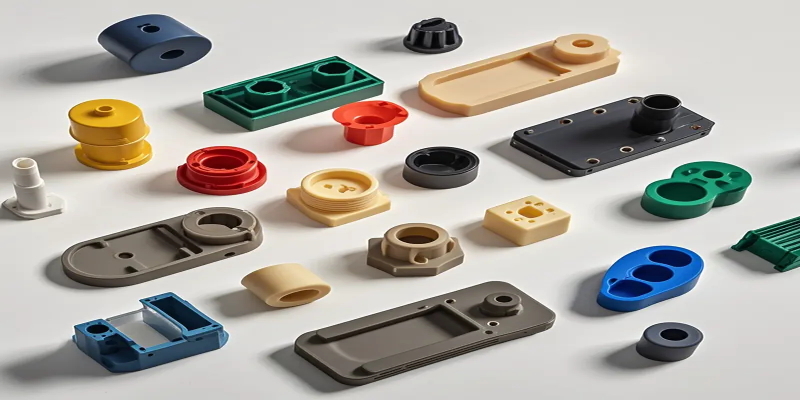
Disposable Medical Supplies: Ensuring Safety and Mass Production
Disposable medical supplies are crucial for infection control and patient safety. These items must be produced in large quantities while maintaining strict hygiene standards. Medical injection molding enables the efficient mass production of single-use medical products with consistent quality and precision.
Applications:
- Syringes and IV components – Ensuring sterility and accurate dosage delivery
- Specimen cups and vials – Used for laboratory testing and sample collection
- Blood collection tubes – Designed for safe blood sample storage and analysis
- Catheters and tubing – Essential for fluid and medication delivery in patients
Surgical and Diagnostic Instruments: Precision and Reliability
Surgical and diagnostic instruments require high precision and durability to ensure accurate medical procedures. Injection molding allows for the production of lightweight, ergonomic, and biocompatible tools that enhance medical professionals’ efficiency.
Applications:
- Scalpel and forceps handles – Designed for easy grip and maneuverability
- Endoscopic components – Used in minimally invasive surgeries for internal examinations
- Speculum and retractors – Essential for gynecological and surgical procedures
- Lab pipettes and microplates – Used for precise fluid measurement and medical research
Medical Device Housings and Casings: Protecting Sensitive Equipment
Many medical devices require durable, lightweight, and impact-resistant housings to protect their internal components. Injection molding enables the production of enclosures that meet strict industry regulations while providing electrical insulation and chemical resistance.
Applications:
- Casings for diagnostic devices – Used in blood analyzers, glucose monitors, and imaging machines
- Inhalers and nebulizers – Devices for respiratory treatments and medication delivery
- Housings for pacemakers and defibrillators – Protecting electronic components from external damage
- Dental equipment covers – Ensuring sterility and durability in dental tools
Implantable Medical Devices: Biocompatibility and Long-Term Performance
Implantable medical devices must be made from biocompatible materials that can safely interact with the human body over extended periods. Advanced medical injection molding techniques allow for the creation of intricate, lightweight, and durable implants.
Applications:
- Orthopedic implants – Components like knee and hip replacements
- Dental implants – Artificial tooth roots that integrate with the jawbone
- Drug delivery implants – Devices that release medication over time inside the body
- Bioresorbable implants – Temporary implants that dissolve as the body heals
Wearable Medical Devices: Enhancing Patient Monitoring and Comfort
Wearable medical devices are becoming increasingly popular for continuous health monitoring. These devices require soft, flexible, and biocompatible components that can be comfortably worn by patients. Injection molding helps create durable and ergonomic wearable medical products.
Applications:
- Smart insulin pumps – For continuous blood sugar monitoring and insulin delivery
- Heart rate and ECG monitors – Used in fitness and cardiac health tracking
- Hearing aids – Compact and comfortable devices for hearing enhancement
- Electrode patches for biofeedback devices – Monitoring muscle and nerve activity
Medical injection molding is an essential process in the healthcare industry, enabling the mass production of high-quality, sterile, and precise medical components. From disposable medical supplies and surgical instruments to implantable and wearable medical devices, this technology supports a wide range of applications that improve patient care and medical outcomes. By leveraging advanced molding techniques, manufacturers continue to innovate and enhance the safety, efficiency, and accessibility of modern medical devices.
Molding Definition in Medical: The Difference Between Medical Injection Molding and Casting
Both medical injection molding and casting are manufacturing processes used to produce medical components and devices, but they differ significantly in terms of technique, materials, and applications. Understanding these differences is crucial in determining the appropriate method for producing a particular medical device or component. The following sections will explore the key distinctions between these two methods, examining how each process works, the types of materials they use, their advantages, and the kinds of medical applications they are best suited for. This comparison will help clarify why medical injection molding is often the preferred choice for mass production and precision in the healthcare industry, while casting may be used for specific applications requiring different properties or functionality.
Process Overview: Injection Molding vs. Casting
The first major difference between medical injection molding and casting lies in the fundamental processes involved. Both methods aim to create precise and consistent parts, but they achieve this through different techniques, material handling, and pressure application.
Medical Injection Molding:
In medical injection molding, material (usually thermoplastics or thermosets) is heated until molten and then injected under high pressure into a precisely designed mold. The material fills the mold cavity and solidifies as it cools. After cooling, the part is ejected from the mold. The process is fast, efficient, and suitable for mass production, especially when uniformity and high precision are required.
Casting:
Casting involves pouring or injecting a liquid material (typically metal, plastic, or resin) into a mold, where it is left to harden over time, usually by cooling or chemical curing. The mold may be made of metal, sand, or other materials, depending on the casting process (e.g., sand casting, die casting). Once the material has solidified, the mold is removed to reveal the part. Casting is generally slower than injection molding and may not be as efficient for high-volume production.
Materials Used in Injection Molding vs. Casting
The materials used in medical injection molding and casting also differ, as the processes require specific types of substances to optimize their performance and the final product’s functionality. Both methods require careful material selection based on the end-use of the medical device.
Materials in Medical Injection Molding:
Medical injection molding primarily uses thermoplastic polymers (like polypropylene, polyethylene, polycarbonate) or thermoset resins. These materials are favored for their versatility, ability to be molded into complex shapes, and high volume production capability. Thermoplastics can be easily melted and remolded, which allows for efficient recycling and flexibility in manufacturing. Additionally, these materials are often biocompatible, making them suitable for medical applications like syringes, surgical instruments, and implants.
Materials in Casting:
Casting materials vary more widely and include metals (such as stainless steel, titanium), ceramics, and even certain resins or polymers. In medical casting, metals are commonly used for implants, prosthetics, and some surgical tools that require strength and durability. For example, titanium or stainless steel is often cast for orthopedic implants due to its strength and biocompatibility. Casting is also used for creating highly detailed parts where a specific material characteristic, such as hardness or the ability to withstand high stress, is needed.
Precision and Detail: Molding vs. Casting
The level of precision and the complexity of detail achievable through each process differ, which makes one method more suitable for certain medical products than the other.
Precision in Medical Injection Molding:
Medical injection molding is known for its high precision, producing parts with tight tolerances and exact dimensions. Because the material is injected under pressure, it fills the mold cavity completely, ensuring that the final part is uniform and defect-free. Injection molding is ideal for creating intricate, small, and complex components such as syringes, IV connectors, and small surgical tools where consistency and detail are crucial. The process is capable of producing thousands or even millions of identical parts, making it an excellent choice for mass production.
Precision in Casting:
While casting can also achieve high precision, it is generally less precise than injection molding, particularly for complex or delicate parts. Casting tends to be better suited for producing parts that do not require extremely tight tolerances or intricate detail. While casting can be used for larger parts or components made from metals, it may not be as well-suited for producing small, complex medical devices where high precision is required, as in the case of delicate diagnostic tools or implantable devices.
Production Speed and Efficiency: Molding vs. Casting
The speed of production and overall efficiency of the two methods are significant factors in deciding which process to use for medical device manufacturing. Speed is especially critical in high-volume manufacturing for the healthcare industry.
Speed and Efficiency in Medical Injection Molding:
Injection molding is a fast and efficient process, especially for high-volume production. Once the mold is created, the material can be injected quickly, and cooling times are relatively short. The high-speed cycle times make injection molding ideal for mass production of medical components like disposable syringes, gloves, or IV tubes. Additionally, the process requires minimal post-production handling, as parts are often ejected directly from the mold and are ready for use with little additional work.
Speed and Efficiency in Casting:
Casting is generally slower than injection molding due to the time required for materials to cool and solidify. While it can be used for low-volume or specialized production, casting typically involves longer lead times. Additionally, casting requires more finishing work, such as polishing, sanding, or machining, especially when producing parts with complex geometries. This makes casting less efficient for mass production compared to injection molding.
Applications in the Medical Industry: Injection Molding vs. Casting
Each process has distinct applications based on the needs of the medical device. The choice between injection molding and casting depends on the required material properties, part complexity, and production volume.
Applications of Medical Injection Molding:
Injection molding is ideal for manufacturing small, intricate, and disposable medical components that require high precision. Typical applications include:
- Syringes, needles, and catheters – requiring uniformity, sterility, and consistency.
- IV sets, drug delivery devices, and diagnostic tools – which must be mass-produced with consistent quality.
- Orthopedic and dental components – such as trays, sterilization containers, and prosthetic parts.
Injection molding is particularly useful when large volumes of identical parts need to be produced quickly and cost-effectively.
Applications of Casting in the Medical Industry:
Casting is often used for creating larger, more durable medical components or implants that require specific material properties like strength and resistance to wear. Common applications include:
- Orthopedic implants (e.g., hip replacements, knee implants) – often made from metals like titanium or stainless steel for strength.
- Prosthetics and joint replacements – where casting can create complex shapes with materials that require high strength.
- Dental crowns and bridges – where casting can be used to create precisely formed restorations.
Casting is ideal for situations where materials like metals or ceramics are required and when the part size or material characteristics make injection molding unsuitable.
Cost Considerations: Injection Molding vs. Casting
The cost-effectiveness of each process varies, and the decision is often influenced by production volume and material requirements.
Cost Considerations for Medical Injection Molding:
Injection molding generally has higher upfront costs due to the creation of molds and the equipment required for the process. However, these costs can be offset by the efficiency and speed of mass production. For large-scale production of medical devices, injection molding is typically more cost-effective, as the cost per unit decreases significantly with higher quantities.
Cost Considerations for Casting:
Casting can be more cost-effective for producing small quantities of larger parts or when specific material properties are needed. The initial setup costs for casting (mold and tooling) tend to be lower than injection molding. However, for large production runs, casting may become less cost-efficient due to longer cycle times and more intensive post-production work.
Both medical injection molding and casting have distinct advantages, and their differences make them suitable for different medical applications. Medical injection molding excels in high-precision, high-volume production of small, intricate parts made from thermoplastic materials, while casting is better suited for producing larger, more durable components from metals or other specialized materials. The choice between the two processes depends on factors such as material requirements, part complexity, production volume, and cost considerations. By understanding the differences between injection molding and casting, manufacturers can select the most appropriate method for creating medical devices that meet the required standards of performance, safety, and reliability.
Molding Definition in Medical Manufacturing: Key Design Considerations in Medical Injection Molding
Medical injection molding is a highly specialized process that requires meticulous design planning to ensure the production of safe, reliable, and high-precision medical components. The design phase is critical because medical products must comply with strict regulatory standards, maintain biocompatibility, and offer consistent performance. Several key design factors influence the success of medical injection molding, including material selection, mold design, dimensional accuracy, sterilization compatibility, and manufacturing efficiency. Below, we explore these crucial considerations and their impact on the medical industry.
Material Selection: Ensuring Biocompatibility and Performance
Selecting the right material is one of the most important factors in medical injection molding. The material must be biocompatible, durable, and resistant to chemicals and sterilization methods. Each medical application has specific material requirements to ensure patient safety and product longevity.
Considerations:
- Biocompatibility – Ensuring the material does not cause allergic reactions or toxicity in the human body.
- Sterilization Resistance – Withstanding autoclaving, gamma radiation, or chemical sterilization without degradation.
- Mechanical Properties – Choosing materials with suitable strength, flexibility, and impact resistance.
- Transparency and Coloration – Some applications require clear plastics for visibility, while others need color coding for identification.
Common Materials Used:
- Polycarbonate (PC) – High strength, transparent, and impact-resistant (used in medical device housings).
- Polypropylene (PP) – Lightweight, chemical-resistant, and cost-effective (used in syringes and containers).
- Liquid Silicone Rubber (LSR) – Flexible, biocompatible, and heat-resistant (used in seals and soft medical components).
- PEEK (Polyetheretherketone) – High-performance polymer for implants due to its biocompatibility and strength.
Mold Design: Precision and Efficiency in Production
The mold design determines the shape, accuracy, and quality of the final medical component. A well-designed mold minimizes defects, enhances production efficiency, and ensures consistent quality.
Considerations:
- Gate Placement – Ensuring uniform material flow to avoid defects like warping or voids.
- Cooling System – Optimizing cooling channels to reduce cycle time and prevent uneven shrinkage.
- Ejection Mechanism – Designing for smooth part removal without damage or contamination risks.
- Multi-Cavity Molds – Using multiple cavities to produce high volumes of parts efficiently.
Key Mold Types:
- Single-Cavity Molds – Used for small production runs or complex components.
- Multi-Cavity Molds – Ideal for mass production of identical parts, reducing unit costs.
- Family Molds – Used for producing different parts in one cycle, optimizing efficiency.
Dimensional Accuracy and Tolerances: Meeting Strict Medical Standards
Medical devices require extremely tight tolerances to ensure proper function and compatibility. Even minor dimensional deviations can lead to failure in critical applications.
Considerations:
- Shrinkage Compensation – Accounting for material contraction during cooling to maintain accuracy.
- Wall Thickness Uniformity – Preventing warping and defects by ensuring even material distribution.
- Precision Tolerances – Medical parts often require tolerances within ±0.001 inches.
Application Examples:
- Surgical Instruments – Require tight tolerances to ensure accurate cuts and precise handling.
- Catheter Components – Must be manufactured with exact diameters to ensure proper fluid flow.
- Implantable Devices – Any dimensional error can cause compatibility issues with human tissue.
Sterilization Compatibility: Ensuring Safety and Compliance
Medical products must undergo sterilization to eliminate bacteria and contaminants. The design and material choice must accommodate various sterilization methods without compromising performance.
Considerations:
- Heat Resistance – Materials must withstand autoclave sterilization (steam at high temperatures).
- Chemical Stability – Components should not degrade when exposed to sterilizing chemicals like ethylene oxide.
- Radiation Resistance – Some materials must endure gamma or electron beam sterilization without losing mechanical properties.
Sterilization Methods and Compatible Materials:
- Autoclave (Steam): Polypropylene, PEEK, and stainless steel.
- Ethylene Oxide (EO): Suitable for heat-sensitive plastics like polyethylene and PVC.
- Gamma Radiation: Works well with polycarbonate and PEEK but can degrade some polymers over time.
Manufacturing Efficiency and Cost Optimization
Efficiency in medical injection molding is essential for reducing costs while maintaining high-quality standards. Design choices impact production speed, material waste, and overall manufacturing costs.
Considerations:
- Cycle Time Optimization – Using efficient cooling and ejection systems to speed up production.
- Minimizing Material Waste – Designing molds with minimal runners and gating to reduce scrap.
- Automation Integration – Implementing robotic handling to enhance precision and reduce contamination risks.
Cost-Effective Design Strategies:
- Design for Manufacturability (DFM): Simplifying part geometries to reduce production complexity.
- Use of Recyclable Materials: Implementing sustainable plastics to cut costs and environmental impact.
- Hybrid Molding Techniques: Combining overmolding or insert molding to reduce assembly costs.
Medical injection molding requires careful design planning to ensure that components meet strict regulatory, safety, and performance requirements. From selecting biocompatible materials and optimizing mold design to maintaining dimensional accuracy and ensuring sterilization compatibility, each factor plays a crucial role in the manufacturing process. By focusing on these key design considerations, medical manufacturers can produce high-quality, reliable, and cost-effective medical components that improve patient care and treatment outcomes.
Molding Definition in Medical: How to Choose the Right Medical Injection Molding Process for Your Project
Selecting the right medical injection molding process for your project involves understanding the specific requirements of the medical device being produced. There are multiple factors to consider, including the complexity of the part, the material choice, production volume, regulatory requirements, and cost constraints. Understanding these elements will help you choose the most suitable molding process, ensuring that your product meets the necessary safety, quality, and performance standards. The following sections will outline the key aspects to evaluate when choosing the right injection molding process for medical device manufacturing, offering insights into material considerations, design complexities, and the desired production outcomes.
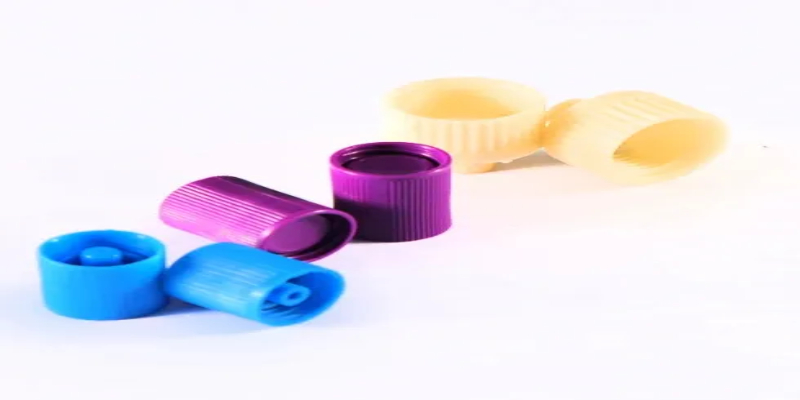
Consider the Complexity of the Medical Device Design
The complexity of the device design is a critical factor when selecting an injection molding process. Medical devices can range from simple components like syringes to highly intricate parts such as surgical tools, diagnostic devices, or implants. The ability to produce complex shapes, maintain precise tolerances, and create detailed features is essential in ensuring the part functions properly and meets regulatory requirements.
Complex Designs and Intricate Features:
For highly intricate designs or parts with multiple features, multi-cavity molds or multi-material injection molding may be the most suitable options. Techniques such as overmolding (molding multiple materials simultaneously) or insert molding (embedding other materials into the part) allow for complex assemblies in a single process. These techniques enable the production of medical devices with multiple components or moving parts that need to fit together precisely, such as housings for diagnostic tools or drug delivery systems.
Simpler Designs:
For simpler designs or single-material parts, such as standard syringes or plastic medical trays, a basic single-cavity injection molding process may suffice, providing cost-effective and efficient production.
Material Selection and Biocompatibility
The material used in medical injection molding plays a vital role in the functionality, safety, and regulatory compliance of the device. Medical devices often require materials that are biocompatible, resistant to sterilization methods, and capable of withstanding wear and tear over time.
Biocompatible and Sterilizable Materials:
If the device needs to come into direct contact with the human body, such as implants, syringes, or surgical instruments, materials like polycarbonate (PC), polypropylene (PP), silicone, or medical-grade thermoplastics are commonly used. In these cases, you must ensure the material’s compatibility with medical standards such as ISO 10993 (biocompatibility) and FDA approval.
Additionally, some devices may need to withstand repeated sterilization processes, such as autoclaving, gamma radiation, or ethylene oxide treatment. Materials like polyethylene (PE) or polypropylene are often chosen for their durability under sterilization.
Determine Production Volume and Cost-Effectiveness
Production volume is a key factor in deciding the right molding process for your medical device. The choice of molding technique can have a significant impact on both production speed and cost-effectiveness. For large-scale production, the molding process must be highly efficient, whereas low-volume or prototype runs might require a different approach.
High-Volume Production:
For large production runs, high-speed injection molding with automated systems is typically the most efficient method. Injection molding allows for quick cycle times and high consistency across large quantities. This process is ideal for products like disposable syringes, IV bags, or diagnostic test kits that require mass production at a low per-unit cost.
Low-Volume or Prototype Production:
For small production runs or prototypes, the tooling costs associated with injection molding may be prohibitive. In this case, rapid injection molding or additive manufacturing (3D printing) might be more suitable. These methods allow you to quickly prototype and produce small batches without the need for expensive mold creation, which can be a significant investment in traditional injection molding.
Evaluate the Regulatory and Safety Requirements
In the medical industry, regulatory compliance is critical. Medical devices must meet stringent standards to ensure safety and effectiveness, such as FDA (Food and Drug Administration) regulations, ISO 13485 (Quality Management Systems for medical devices), and ISO 14971 (Risk Management).
Compliance in Injection Molding:
When choosing the right molding process, you must ensure that the selected material, manufacturing method, and facility meet all relevant regulatory standards. Injection molding is commonly used in medical manufacturing because it offers the ability to produce highly consistent and defect-free parts that meet the rigorous testing and documentation requirements of regulatory bodies. Cleanroom manufacturing might be required for certain products like sterile surgical tools or implants.
Consider the Final Product’s Durability and Performance
The final product’s durability, strength, and performance are essential considerations, especially for medical devices that will undergo stress or use in high-pressure environments. For instance, orthopedic implants, surgical tools, and drug delivery devices must withstand significant mechanical forces.
Material Properties for Durability:
For high-durability medical devices, materials such as PEEK (Polyether Ether Ketone), titanium alloys, or stainless steel (in the case of casting) are preferred due to their mechanical strength, resistance to wear, and ability to withstand extreme conditions.
Injection molding is particularly well-suited for producing parts with tight tolerances and complex geometries, providing the necessary performance in devices like heart valve components, joint replacements, or implantable devices.
Tooling and Lead Time Considerations
The tooling required for injection molding can be costly and time-consuming, especially for complex parts. However, the initial investment in mold creation is typically justified by the reduced per-unit cost in large production runs.
Tooling Costs and Lead Times:
If you’re dealing with high-volume production, the time spent designing and creating molds will pay off quickly as the mold is used to produce thousands or even millions of identical parts. However, for a one-time or low-volume production, tooling costs may become a barrier. In these cases, rapid tooling or soft tooling can be used to reduce costs and lead times, allowing for faster prototyping and initial production.
For projects requiring quick turnaround, consider a quick-turn injection molding approach that uses simpler molds, or other methods such as rapid prototyping or low-volume molding to shorten lead times and reduce upfront costs.
Choosing the right medical injection molding process requires a comprehensive understanding of the device’s design complexity, material requirements, production volume, regulatory needs, and performance expectations. By carefully evaluating these factors—design intricacy, material biocompatibility, production scale, regulatory compliance, and durability—you can select the optimal molding process that aligns with the project’s objectives. Whether you’re producing high-precision, high-volume devices or low-volume prototypes, understanding the trade-offs and advantages of various injection molding techniques will help you make the most informed decision for your medical device manufacturing needs.
Molding Definition in Medical Industry: How to Choose the Right Medical Injection Molding Manufacturer
Selecting the right medical injection molding manufacturer is a crucial decision that impacts the quality, reliability, and regulatory compliance of medical components. The medical industry has strict standards for safety, precision, and biocompatibility, so choosing a manufacturer requires careful evaluation across multiple factors. From expertise and certifications to production capabilities and quality assurance, various aspects should be considered to ensure a successful partnership. Below, we explore the key criteria for selecting the best medical injection molding manufacturer.
Industry Expertise and Experience: Ensuring Knowledge of Medical Standards
A manufacturer’s experience in medical injection molding plays a vital role in their ability to produce high-quality components. Medical devices require precision and compliance with regulatory standards, making industry-specific expertise essential.
Key Considerations:
- Years of Experience in Medical Injection Molding – Long-standing manufacturers have refined processes and proven reliability.
- Knowledge of Medical Regulations – Familiarity with FDA, ISO 13485, and other medical compliance requirements.
- Previous Medical Projects – Experience with similar products ensures a better understanding of design and functionality.
What to Look For:
- A portfolio of successfully manufactured medical components.
- Case studies demonstrating problem-solving capabilities.
- Experience with various medical applications, from surgical tools to implantable devices.
Certifications and Compliance: Meeting Regulatory Standards
Medical injection molding requires strict adherence to industry regulations to ensure patient safety and product effectiveness. Certifications indicate that a manufacturer follows best practices in production, quality control, and risk management.
Key Considerations:
- ISO 13485 Certification – A critical certification for medical device manufacturing, ensuring consistent quality management.
- FDA Compliance – Necessary for manufacturers producing medical components for the U.S. market.
- Good Manufacturing Practices (GMP) – Ensuring cleanliness, traceability, and process control.
- Cleanroom Capabilities – Facilities with ISO Class 7 or 8 cleanrooms for contamination-free production.
What to Look For:
- Certification documents and audit reports.
- Compliance with country-specific medical regulations (e.g., CE marking for European markets).
- A clear quality management system ensuring traceability of materials and processes.
Manufacturing Capabilities and Technology: Assessing Production Strength
The ability to meet production demands with high precision depends on the manufacturer’s technology and equipment. Advanced machinery, automation, and material expertise contribute to efficiency and consistency.
Key Considerations:
- Injection Molding Equipment – Modern, high-precision machines that support various medical-grade materials.
- Production Volume Capabilities – The ability to handle small batches (for prototypes) and large-scale production.
- Specialized Techniques – Availability of overmolding, insert molding, micro-molding, and liquid silicone rubber (LSR) molding.
- Tooling and Mold Development – In-house mold design and maintenance capabilities.
What to Look For:
- State-of-the-art injection molding machines and automation processes.
- Expertise in handling biocompatible materials such as PEEK, LSR, and medical-grade polycarbonate.
- A flexible approach to accommodate both prototyping and mass production.
Quality Control and Inspection: Ensuring High Standards
Quality assurance is a critical factor in medical injection molding, as even minor defects can compromise safety and performance. A reliable manufacturer must have rigorous quality control measures in place.
Key Considerations:
- In-House Testing and Inspection – Ability to conduct dimensional checks, material testing, and functional validation.
- Traceability Systems – Ensuring full documentation of materials, processes, and batch records.
- Defect Prevention Strategies – Use of Six Sigma, statistical process control (SPC), and lean manufacturing principles.
What to Look For:
- Real-time quality monitoring systems.
- Compliance with strict quality control protocols.
- Use of advanced inspection methods like laser scanning, X-ray, and automated vision systems.
Customization and Design Support: Partnering for Innovation
A good medical injection molding manufacturer should offer design and engineering support to optimize product performance and manufacturability.
Key Considerations:
- Design for Manufacturability (DFM) Support – Assistance in refining designs for cost efficiency and performance.
- Prototyping Capabilities – Rapid prototyping options to test and validate designs before full production.
- Material Selection Guidance – Expertise in recommending the best medical-grade materials based on application needs.
What to Look For:
- A team of experienced engineers and design consultants.
- Rapid prototyping services, including 3D printing and soft tooling.
- Collaboration in mold design optimization to reduce production costs.
Supply Chain and Logistics: Ensuring Timely and Cost-Effective Delivery
Efficient supply chain management ensures timely production and delivery of medical components without delays or material shortages.
Key Considerations:
- Raw Material Sourcing – Reliable access to high-quality medical-grade plastics and elastomers.
- Production Lead Times – Ability to meet deadlines without compromising quality.
- Inventory Management and Warehousing – Offering just-in-time (JIT) delivery and storage solutions.
What to Look For:
- A transparent supply chain with reliable material suppliers.
- Track record of on-time deliveries and logistics efficiency.
- Cost-effective shipping and warehousing solutions.
Cost Efficiency and Pricing: Balancing Quality and Budget
While cost should not be the sole deciding factor, selecting a manufacturer that offers competitive pricing without sacrificing quality is essential.
Key Considerations:
- Total Cost of Ownership (TCO) – Evaluating costs beyond manufacturing, including tooling, maintenance, and logistics.
- Bulk Production Discounts – Assessing cost savings for high-volume orders.
- Efficiency in Manufacturing – Use of automation and lean manufacturing to reduce waste and costs.
What to Look For:
- Transparent pricing structures with no hidden fees.
- Value-added services that enhance cost efficiency (e.g., assembly, packaging).
- Scalable production options to optimize costs based on demand.
Choosing the right medical injection molding manufacturer requires careful evaluation of multiple factors, including expertise, certifications, production capabilities, quality control, and cost efficiency. By selecting a manufacturer with proven experience in the medical industry, strict regulatory compliance, advanced technology, and strong supply chain management, medical companies can ensure the production of high-quality, safe, and reliable medical components. A well-chosen partner not only meets current production needs but also supports long-term innovation and growth in the healthcare sector.
FAQs about Molding Definition Medical
In medical terms, molding refers to the process of shaping or forming materials into specific forms or structures for medical devices or products. In the context of medical product injection molding, it involves using molds to manufacture precise components for medical devices such as syringes, IV connectors, catheters, and other critical healthcare tools. The process typically uses thermoplastic materials, which are injected into a mold under pressure to form the desired shape. Medical molding ensures that products meet strict quality standards, are sterile, and are compatible with human use. This method is preferred because of its efficiency, ability to produce high volumes of consistent parts, and the precision it offers, which is essential in the healthcare industry where safety and performance are paramount.
Moulding, often used interchangeably with molding, refers to the process of forming or shaping medical products using a mold, primarily in the context of injection molding. Moulding in medical terms typically pertains to manufacturing items such as medical implants, diagnostic tools, or drug delivery systems. In this process, materials like polymers, resins, or elastomers are heated and injected into a precisely designed mold under controlled pressure. The material cools and solidifies, taking the shape of the mold. Moulding in the medical industry focuses on creating components that meet regulatory standards, ensuring high levels of safety, sterility, and functionality for patient care. Both terms, molding and moulding, are used in the manufacturing of medical products but do not differ significantly in meaning.
Yes, molding and moulding essentially refer to the same process, though the spelling differs depending on regional language variations. In the United States, “molding” is the common spelling, while in the United Kingdom and other English-speaking regions, “moulding” is preferred. Both terms describe the technique of shaping materials, typically through heat and pressure, into desired forms using a mold. In the context of medical product injection molding, the objective is to manufacture high-quality, precise components for medical devices and tools. Whether spelled with an “o” or “u,” molding/moulding in the medical field ensures consistency, efficiency, and safety in the production of critical healthcare products.
Molding defects in the medical product injection molding process refer to imperfections or issues that can arise during the manufacturing of components. Common defects include:
Short Shots: Insufficient material injected into the mold, leading to incomplete parts.
Warpage: Distortion or bending of the molded product due to uneven cooling or improper material flow.
Sink Marks: Indentations that form on the surface due to uneven cooling, usually in thicker sections of the part.
Flash: Excess material that seeps out from the mold, causing rough edges or unwanted projections.
Bubbles or Voids: Trapped air within the mold causing internal cavities or surface blemishes.
These defects can compromise the functionality, safety, and sterility of medical devices. Effective quality control, precise mold design, and the use of suitable materials are critical to minimizing such defects.
The three primary types of molding processes used in manufacturing, including the production of medical devices, are:
Injection Molding: Involves injecting molten material (usually plastic or rubber) into a mold under high pressure, which solidifies to form the desired shape. It’s widely used for medical products like syringes, IV components, and catheters.
Blow Molding: Used primarily for making hollow objects like bottles, this process involves inflating a tube of material inside a mold to form a hollow part. It’s used for some medical containers or bags.
Compression Molding: Material is placed into a mold cavity and compressed, often with heat, to form the part. This process is commonly used for making rubber or thermoset components found in medical seals or gaskets.
Each method has its advantages based on the material, complexity of the part, and production needs in the medical field.
Infusion molding, often referred to as resin infusion molding, is a process used for creating medical parts by injecting resin into a mold. In the context of medical product injection molding, infusion molding involves the use of vacuum pressure to draw resin into a mold cavity, typically made of composite materials. This process is particularly useful for producing large, complex parts that require high-strength and lightweight materials. Infusion molding allows for better control over material distribution and is often used in the medical industry for creating prosthetic components, orthopedic devices, and durable medical parts that require specific material properties. This method can also reduce waste compared to other molding techniques.
Examples of molding in the medical field include the production of various medical devices such as syringes, IV tubes, orthopedic braces, and surgical instruments. For instance, a common example is the manufacturing of a plastic syringe using injection molding, where melted plastic is injected into a mold to create a uniform, precise, and sterile product. Another example includes the production of catheter tips or connectors, where molding ensures that the parts are smooth, accurate, and free of defects. Molding is also used to create packaging for medical products, such as blister packs for pills or sterile trays for surgical instruments. These products are essential in healthcare and benefit from the efficiency and precision molding offers.
The key difference between casting and molding lies in the process and the materials used. Casting involves pouring liquid material, such as molten metal, plastic, or resin, into a mold where it cools and hardens into the desired shape. Molding, on the other hand, involves injecting material into a mold under pressure, which solidifies to form the part. While casting is often used for producing metal or more rigid parts, molding, especially injection molding, is typically preferred for making medical products like plastic syringes, catheters, and other small components. Casting is generally suited for large, thick parts, while molding offers higher precision and is ideal for mass production of small, intricate items in the medical field.
Moulding refers to the process of shaping or forming materials, often using heat, pressure, and molds, to create a desired product or component. In the medical field, moulding (or molding) is used to manufacture medical devices, tools, and other healthcare products. This process is crucial for ensuring that medical components such as syringes, catheters, and implants are produced with high precision, quality, and consistency. Moulding typically uses thermoplastic materials, which are easy to shape and offer flexibility in creating intricate designs. The goal of moulding in the medical industry is to produce components that are safe, functional, and meet regulatory requirements.
The word molding refers to a manufacturing process where materials, often plastic, rubber, or metal, are shaped into a particular form by being injected, pressed, or cast into a mold. In the medical industry, molding plays a vital role in creating precise, standardized components for devices such as syringes, surgical instruments, and implants. The process involves applying heat and pressure to a material to make it take the shape of the mold, ensuring that the final product meets specific design requirements. Molding helps produce high volumes of uniform parts, which is essential in medical manufacturing, where consistency and safety are crucial.
The process of molding, particularly in medical product injection molding, involves several key steps:
Material Preparation: The chosen material, typically a thermoplastic or resin, is heated until it reaches a molten state.
Injection: The molten material is injected into a mold cavity under high pressure, filling it completely.
Cooling: The material is allowed to cool and solidify inside the mold, taking the shape of the cavity.
Ejection: Once cooled, the finished part is ejected from the mold.
Finishing: Any excess material, such as flash or burrs, is removed, and the part undergoes inspection for quality control.
This process allows for mass production of medical components with high precision, ensuring consistency and adherence to stringent quality standards.
The purpose of molding in the medical industry is to produce consistent, high-quality, and precisely manufactured components for medical devices and products. Through molding, manufacturers can create a wide variety of medical tools, such as syringes, catheters, IV connectors, and surgical instruments, with high levels of accuracy and repeatability. Molding enables the production of large quantities of parts in a cost-effective manner while maintaining tight tolerances. It also allows for the use of specialized materials that meet safety, sterility, and durability requirements. The process is essential in meeting regulatory standards, ensuring the safety and reliability of products that are critical for patient care and treatment.
Contact our professional team now for a same-day quote and risk-free project evaluation. Benefit from ISO 8 cleanrooms, advanced machines, and 12-hour fast response in medical injection molding.