China medical plastic parts factory has become a cornerstone in the global manufacturing landscape, showcasing unparalleled expertise in the production of high-quality medical components. With China’s robust industrial base, advanced technologies, and cost-efficient production processes, these factories lead the way in meeting the growing demands of the healthcare industry. The importance of selecting a reliable China medical plastic parts factory cannot be overstated. Precision, hygiene, and compliance with international standards such as ISO 13485 are critical for ensuring safety and effectiveness in medical applications. From cleanroom injection molding to advanced quality control, these factories are equipped to deliver excellence. Partnering with a trusted China medical plastic parts factory guarantees dependable, innovative solutions for a wide range of medical needs. FUJIU Medical Injection Mold is a leading China medical plastic parts factory, offering high-quality, biocompatible injection molding for medical devices.
Low-Volume to High-Volume Production Capabilities
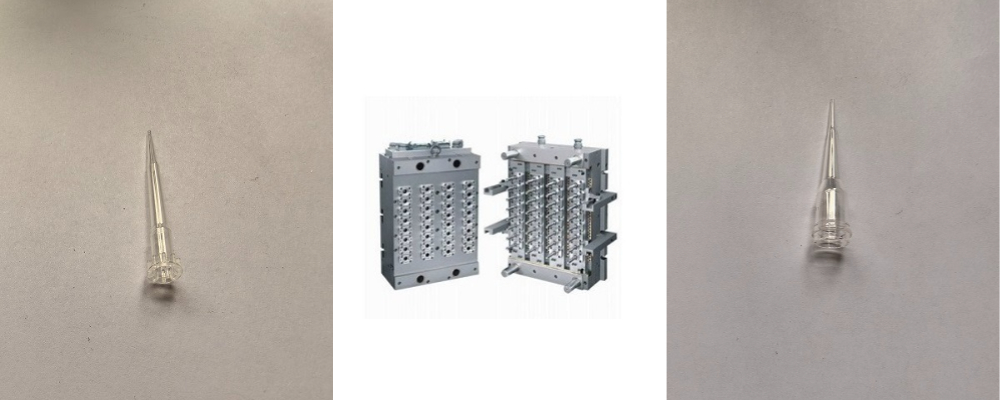
Attributes | Details |
---|---|
Place of Origin | Dongguan, Guangdong, China |
Brand Name | LY Medical Injection Mold |
Product Name | Medical Plastic Parts Injection Molding |
Molding Mode | Plastic Injection Mold |
Product Material | Plastic |
Processing Service | Molding, Cutting |
Surface Treatment | Original, Matte or Customized Surface Texture |
Color | Customized |
Size | Customized |
Length | Customized |
Service | OEM ODM |
Logo | Customized Logo Acceptable |
Certification | ISO9001 |
Tolerance: | +/-0.01mm / OEM |
Drawing Format: | 2D/(PDF/CAD) And 3D(IGES/STEP) |
Selling Units | Single item |
Packing Details | Outer Packaging Carton Inner Packaging According to Customer Requirement |
Port | According to Your Requirement |
China Medical Plastic Parts Factory: What Are Medical Plastic Parts?
Medical plastic parts are essential components made from various medical-grade plastics designed to meet the stringent requirements of the healthcare industry. These parts are widely produced by a China medical plastic parts factory, leveraging advanced technologies to ensure safety, precision, and reliability.
Definition and Importance of Medical Plastic Parts
Medical plastic parts refer to injection-molded or machined plastic components used in medical devices and equipment. Their importance lies in their ability to meet the healthcare sector’s rigorous demands for sterility, durability, and cost-efficiency. A China medical plastic parts factory specializes in producing these components to ensure compliance with international standards like ISO 13485 and GMP, ensuring they are suitable for critical applications.
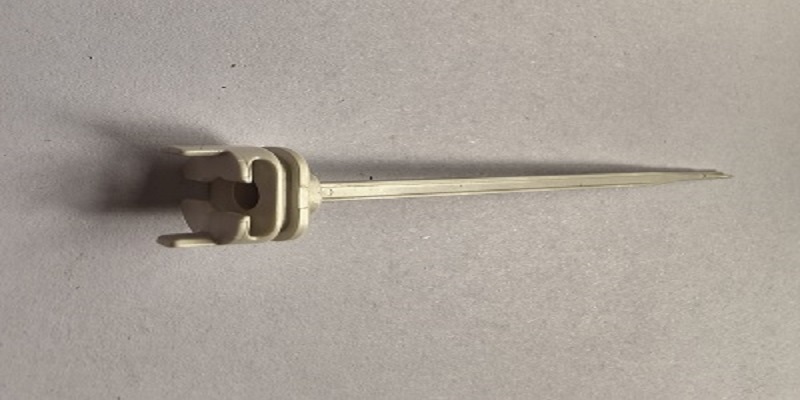
Types of Medical Devices Made from Plastic
A China medical plastic parts factory manufactures a wide variety of components for medical devices, including:
- Syringes: Disposable and reusable syringes for precise drug delivery.
- IV Sets: Durable and sterile tubing for intravenous therapy.
- Diagnostic Tools: Housings and components for imaging and testing equipment.
- Respiratory Devices: Plastic parts for masks and ventilators.
- Prosthetics and Orthotics: Lightweight, durable components for mobility aids.
These plastic parts are designed to meet specific medical requirements, from flexibility to chemical resistance.
Why Plastic is Commonly Used in the Medical Industry
The widespread use of plastic in the medical field stems from its unique properties:
- Lightweight: Plastic reduces the overall weight of medical devices, making them easier to use and transport.
- Durable: High-impact resistance ensures that devices can withstand rigorous use in healthcare environments.
- Cost-Effective: Mass production by a China medical plastic parts factory significantly lowers manufacturing costs without compromising quality.
- Hygienic: Plastics used in medical applications are non-porous and easy to sterilize, ensuring compliance with hygiene standards.
By relying on the expertise of a China medical plastic parts factory, healthcare providers can access high-quality, innovative solutions tailored to their needs.
China Medical Plastic Parts Factory: Why China?
China stands as a global leader in manufacturing, particularly in the realms of plastic medical molding and the medical industry. A China medical plastic parts factory epitomizes this leadership, combining advanced technology, vast production capacity, and unmatched expertise to meet international demands.
China’s Position as a Global Manufacturing Leader
China’s dominance in manufacturing stems from its well-established infrastructure, skilled labor force, and commitment to innovation. A China medical plastic parts factory benefits from these strengths, producing high-quality medical components with efficiency and precision. By integrating China medical precision machining into their processes, these factories can achieve the intricate designs and tight tolerances required for medical-grade plastic parts used in everything from diagnostic tools to surgical instruments.
China’s factories, equipped with state-of-the-art machinery and cleanroom facilities, have earned a reputation for producing components that meet stringent global standards like ISO 13485. These facilities not only ensure product quality but also provide reliable scalability, making them an essential part of the international healthcare supply chain.
Advantages of Choosing China-Based Factories
Cost Efficiency
A China medical plastic parts factory offers unparalleled cost advantages. The ability to source raw materials locally, coupled with streamlined production processes, reduces costs without sacrificing quality. This cost efficiency allows manufacturers to provide competitive pricing for bulk orders, making China an attractive destination for medical companies worldwide.
Large-Scale Production
China-based factories are equipped to handle large-scale production demands. Their high-capacity facilities ensure that plastic medical device manufacturers can meet global healthcare needs swiftly and reliably. This scalability is particularly crucial during emergencies, such as pandemics, when demand for medical supplies surges.
Advanced Technology
A China medical plastic parts factory utilizes cutting-edge technology, including:
- Precision Injection Molding: Ensures the production of intricate and durable medical components.
- Cleanroom Facilities: Certified environments for sterile manufacturing, crucial for medical-grade products.
- Mold Flow Analysis Software: Optimizes mold design to enhance efficiency and reduce waste.
- Rapid Prototyping and CNC Machining: Provides quick turnaround for custom medical plastic parts.
These technological advancements enable China to remain a trusted leader in medical plastic manufacturing, offering innovative solutions to meet diverse healthcare requirements.
By partnering with a China medical plastic parts factory, businesses can leverage these advantages to achieve superior product quality and cost-effective solutions for the medical industry.
Technology and Innovations in Medical Plastic Molding
A China medical plastic parts factory is at the forefront of technology and innovation, revolutionizing the production of high-quality medical components. These factories combine advanced tools, processes, and expertise to meet the exacting standards of the medical industry while ensuring efficiency and precision.
Cutting-Edge Technologies for High-Quality Production
Modern China medical plastic parts factory facilities employ state-of-the-art technologies to ensure every component is manufactured with precision and reliability. These include:
- Precision Injection Molding Machines: Capable of producing intricate designs with tight tolerances, essential for medical applications.
- Automation and Robotics: Automated systems streamline production, enhance consistency, and reduce human error.
- Sustainable Practices: Factories incorporate energy-efficient processes and waste reduction techniques to align with global environmental standards.
These innovations position China as a leader in delivering reliable solutions to the global medical industry.
Cleanroom Injection Molding (ISO Class 7 & 8)
One of the most critical technologies utilized by a China medical plastic parts factory is cleanroom injection molding. This process ensures the sterility and precision of medical components by manufacturing them in controlled environments:
- ISO Class 7 & 8 Cleanrooms: These certified environments maintain strict control over airborne particles, humidity, and temperature, meeting the highest hygiene requirements.
- Applications: Cleanroom facilities are essential for producing sensitive medical items such as syringes, IV components, and surgical tools.
- Benefits: Ensures product safety, reduces contamination risks, and meets global regulatory standards.
Advanced Software for Mold Design and Flow Analysis
A China medical plastic parts factory leverages advanced software to optimize production processes.
- Mold Design Software: Facilitates the creation of detailed 3D models, ensuring that molds meet exact specifications before production begins.
- Mold Flow Analysis: Simulates the flow of molten plastic within the mold, identifying potential issues such as air pockets or uneven distribution. This ensures efficient, defect-free production from the outset.
These tools minimize errors, reduce production costs, and enable the creation of complex, high-performance medical parts.
Rapid Prototyping and CNC Machining
To meet the demands of innovation and customization, a China medical plastic parts factory employs rapid prototyping and CNC machining.
- Rapid Prototyping: Produces functional prototypes quickly, allowing for design validation and iterative improvements before full-scale production.
- CNC Machining: Delivers high-precision parts by using automated tools to shape plastic and metal materials with extreme accuracy.
These technologies enable factories to adapt to evolving medical industry needs, ensuring flexibility and speed without compromising quality.
By integrating these advanced technologies, a China medical plastic parts factory continues to set the benchmark for innovation and quality in medical plastic molding.
Quality Control and Certifications in a China Medical Plastic Parts Factory
In the medical industry, quality control is non-negotiable, and a China medical plastic parts factory exemplifies stringent measures to meet global standards. From raw materials to the final product, these factories ensure that every stage of production adheres to meticulous quality assurance protocols, enabling them to deliver medical-grade components that are safe, reliable, and compliant with international regulations.
Importance of Quality Control in Medical Plastic Manufacturing
Quality control is critical in the production of medical plastic parts due to the sensitive nature of their applications. A China medical plastic parts factory incorporates rigorous inspection processes to eliminate defects and maintain uniformity. Factors such as contamination, structural integrity, and dimensional accuracy are closely monitored. This level of precision ensures that products such as syringes, diagnostic tools, and surgical instruments perform their intended functions without compromise.
Key Certifications for Medical-Grade Products
To establish credibility and meet industry demands, a China medical plastic parts factory complies with a range of globally recognized certifications:
- ISO 13485: Specifies requirements for a comprehensive quality management system in medical device plastic manufacturing.
- GMP (Good Manufacturing Practice): Guarantees that products are consistently produced and controlled according to stringent quality standards.
- CE Certification: Ensures products meet EU safety, health, and environmental protection requirements, allowing exports to European markets.
- FDA Compliance (where applicable): Required for medical devices intended for the U.S. market.
These certifications demonstrate a factory’s commitment to delivering medical parts that meet rigorous quality and safety benchmarks.
Steps Taken by Leading Factories
- Incoming Material Inspections: Verifying the quality of raw materials, such as medical-grade plastics, before production begins.
- In-Process Monitoring: Real-time monitoring of critical parameters during manufacturing to prevent defects.
- Final Product Testing: Ensuring each finished part undergoes dimensional and functional testing.
Additionally, these factories utilize advanced equipment such as CMM (Coordinate Measuring Machines) and optical inspection systems to achieve unparalleled precision. Cleanroom environments further reduce the risk of contamination, critical for products like surgical instruments and IV components.
Commitment to Industry Standards
A China medical plastic parts factory understands the importance of adhering to international quality and regulatory requirements. By maintaining high standards and obtaining the necessary certifications, these factories ensure they remain trusted partners for global medical device companies. This dedication to quality not only safeguards the end users but also enhances the factory’s reputation in the competitive medical manufacturing sector.
Services Offered by a China Medical Plastic Parts Factory
A China medical plastic parts factory offers a comprehensive suite of services designed to cater to the stringent demands of the medical industry. From initial concept design to finished product assembly, these factories employ advanced technologies and skilled expertise to provide high-quality, cost-effective solutions.
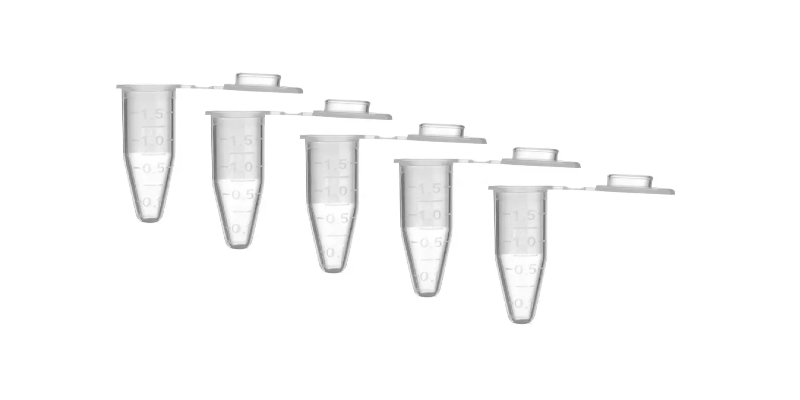
Mold Design and Development
One of the core strengths of a China medical plastic parts factory is its ability to design and develop precision medical molds tailored to specific medical applications. Using state-of-the-art CAD software and mold flow analysis tools, engineers create molds that ensure optimal performance, minimal waste, and flawless production cycles. These molds are critical for producing components like diagnostic tools, IV parts, and surgical instruments with unparalleled accuracy.
Product Design and Prototyping
Top manufacturers in China provide product design and prototyping services to help clients refine their ideas. Rapid prototyping techniques such as 3D printing and CNC machining allow for quick production of functional prototypes. This iterative process ensures the final product meets the required specifications and performance standards before mass production begins.
Injection Molding and Overmolding
A China medical plastic parts factory specializes in a variety of injection molding techniques, including:
- Standard Injection Molding: For high-volume production of precise and durable medical parts.
- Insert Molding: Incorporating metal or other materials into plastic parts for enhanced functionality.
- 2K Injection Molding: Utilizing two materials or colors in a single mold to create complex components.
- Overmolding: Adding an additional layer of material onto an existing part to improve grip, aesthetics, or functionality.
These techniques are ideal for producing components like syringes, surgical handles, and diagnostic equipment.
Medical Device Assembly and Packaging
Beyond manufacturing, a China medical plastic parts factory often provides medical device assembly and packaging services. Factories are equipped with cleanroom environments to ensure sterile assembly of multi-component devices. Proper packaging solutions are also offered to protect products during transportation and storage while complying with industry regulations.
Cleanroom Injection Molding
Cleanroom facilities are a hallmark of leading manufacturers in the medical plastic industry. Many China medical plastic parts factories operate ISO Class 7 and 8 cleanrooms to produce sterile components for applications like surgical instruments and laboratory consumables. These controlled environments ensure that parts meet hygiene and contamination-free standards essential for medical-grade products.
Comprehensive Service for Global Clients
By offering these diverse services under one roof, a China medical plastic parts factory provides end-to-end solutions for global medical companies. Their capabilities streamline the manufacturing process, reduce lead times, and maintain the high-quality standards that the medical industry demands. These factories are not just production hubs—they are partners in innovation and precision.
How to Choose the Right China Medical Plastic Parts Factory
Selecting the right China medical plastic parts factory is critical for ensuring the success of your medical product manufacturing. The medical industry demands precision, hygiene, and reliability, so partnering with a factory that meets these requirements is paramount. Here are the key factors to consider:
Quality Standards and Certifications
The most reliable factories prioritize stringent quality control processes and possess the necessary certifications to produce medical-grade components. Look for certifications such as:
- ISO 13485: Ensures compliance with medical device manufacturing standards.
- GMP (Good Manufacturing Practices): Guarantees that products are consistently produced and controlled to quality standards.
- CE Marking: Indicates conformity with EU safety, health, and environmental requirements.
Certifications reflect the factory’s ability to produce parts that meet global regulatory and safety requirements. Choosing a factory with these credentials ensures your products will be safe, reliable, and market-ready.
Production Capabilities and Technology
The technical capacity of a China medical plastic parts factory is another critical factor. Evaluate their:
- Mold Design and Engineering Tools: Advanced CAD and simulation software for mold flow analysis and error prevention.
- Cleanroom Facilities: Factories with ISO Class 7 or 8 cleanrooms are ideal for manufacturing sterile medical components.
- Precision Equipment: CNC machining, EDM (Electrical Discharge Machining), and automated injection molding machines ensure high-quality output.
Factories that integrate modern technology are better equipped to handle complex designs and high-volume production while maintaining strict quality control.
Experience in Producing Medical-Grade Components
Experience is essential when selecting a China medical plastic parts factory. Manufacturers with a strong track record in the medical industry are more likely to understand the specific needs of this sector, such as producing parts for syringes, diagnostic devices, or surgical tools.
Customer Service and After-Sales Support
Responsive and reliable customer service is a hallmark of a good manufacturing partner. Ensure the factory offers:
- Clear Communication: Transparency during the design, prototyping, and production phases.
- Technical Support: Guidance on material selection, compliance with industry standards, and troubleshooting.
- After-Sales Service: Assistance with product modifications, warranty claims, or addressing any manufacturing concerns.
Good customer service not only smooths the manufacturing process but also builds trust and ensures long-term collaboration.
Additional Considerations
- Scalability: Can the factory handle both small prototype runs and large-scale production
- Cost Efficiency: Does the pricing reflect competitive value without compromising quality
- Customization: How flexible is the factory in accommodating unique project requirements
Role of a China Injection Molding Medical Parts Factory
A China injection molding medical parts factory plays a crucial role in producing high-quality, precision medical components. These factories specialize in advanced medical injection molding processes to create products such as syringes, diagnostic tools, and IV components. Equipped with state-of-the-art machinery, cleanroom environments, and rigorous quality control measures, these factories ensure sterile and reliable manufacturing. Their ability to handle large-scale production with consistent results makes them essential for meeting the growing demands of the medical industry.
The Importance of a China Medical Parts Mold Factory
A China medical plastic parts factory is the backbone of precision manufacturing for medical-grade components. These factories focus on designing and producing molds using advanced technologies like CAD software, mold flow analysis, and CNC machining. High-quality molds are critical to achieving accuracy and consistency in the final products. Factories in delivering custom mold solutions tailored to specific medical requirements. Their expertise ensures the molds are durable, efficient, and optimized for high-volume production, forming the foundation for superior medical injection molding.
Common Medical Grade Plastics Used by China Medical Plastic Parts Factory
In the medical device manufacturing industry, the use of high-quality, biocompatible plastic materials is essential to ensure safety, durability, and performance. A China medical plastic parts factory typically uses a variety of medical-grade plastics for injection molding to meet the diverse needs of the healthcare industry. These materials are selected based on factors like sterility, strength, flexibility, and the specific requirements of the medical device being produced. The following sections will explore the most commonly used medical-grade plastics and their applications in the production of medical devices.
Polycarbonate (PC)
Polycarbonate is a widely used material in the medical industry due to its excellent clarity, impact resistance, and durability. It is commonly used for products like medical device housings, diagnostic equipment, and IV components. Polycarbonate is known for its high tensile strength and ability to withstand sterilization processes, such as autoclaving. In a China medical plastic parts factory, polycarbonate is often chosen for its versatility, allowing for both rigid and transparent parts. It also offers biocompatibility, making it suitable for direct contact with patients.
Polypropylene (PP)
Polypropylene is another key material used in medical injection molding, particularly for its chemical resistance, low cost, and ease of processing. It is commonly used for products such as syringes, medical containers, and surgical instrument components. PP is resistant to acids, bases, and alcohols, making it ideal for medical devices that need to withstand harsh environments. Due to its excellent resistance to bacterial growth, polypropylene is also widely used in the packaging of medical supplies. Its relatively low density makes it a lightweight choice for disposable medical devices.
Polyethylene (PE)
Polyethylene, especially high-density polyethylene (HDPE) and low-density polyethylene (LDPE), is frequently used in medical plastic parts manufacturing due to its resistance to moisture, chemicals, and temperature fluctuations. HDPE is often used in medical bottles, and LDPE is used in flexible medical devices like tubing and bags. Both variants offer excellent biocompatibility, making them suitable for single-use products that require sterilization. PE’s resistance to wear and tear also contributes to its suitability for medical packaging and fluid storage applications in a China medical plastic parts factory.
Polyvinyl Chloride (PVC)
Polyvinyl chloride is commonly used in the medical industry for both rigid and flexible applications. Rigid PVC is used in the production of medical tubing, blood bags, and infusion sets, while flexible PVC is used for items like gloves, IV bags, and catheter tubing. PVC is durable, resistant to chemicals, and easy to sterilize, which makes it a popular choice for medical devices. However, it is often combined with plasticizers to enhance flexibility, particularly in applications where a softer, more pliable material is required.
Acrylonitrile Butadiene Styrene (ABS)
Acrylonitrile Butadiene Styrene (ABS) is a tough and impact-resistant plastic commonly used in medical devices like respiratory components, diagnostic tools, and surgical instruments. ABS is known for its strength and ability to endure high stress without breaking or deforming. It also offers excellent dimensional stability, making it ideal for devices that require precise, reliable parts. ABS can also be sterilized, adding to its appeal in the medical sector. In China medical plastic parts factories, ABS is used when a balance between cost and high-performance material properties is needed.
Polymethyl Methacrylate (PMMA)
Polymethyl methacrylate, also known as acrylic, is used primarily for applications that require optical clarity, such as medical devices with transparent components. PMMA is frequently used in the production of light housings, lens assemblies, and display panels for medical equipment. It offers excellent transparency, UV resistance, and can be easily molded into complex shapes. It is also a preferred material for items requiring high aesthetic appeal, such as medical equipment housings.
Medical-Grade Silicone
Medical-grade silicone is a highly versatile and biocompatible material known for its flexibility, chemical resistance, and low toxicity. It is used in a variety of medical devices, including implants, catheters, and seals. Silicone can withstand high temperatures, is resistant to ultraviolet light, and is often chosen for products that need to remain flexible over time. Its softness and ability to conform to the body make it ideal for applications in implants, wearable devices, and prosthetics. A China medical plastic parts factory often utilizes medical-grade silicone for both patient contact and non-contact applications.
A China medical plastic parts factory uses a variety of medical-grade plastics to produce injection-molded components for the healthcare industry. Materials such as polycarbonate, polypropylene, polyethylene, PVC, ABS, PMMA, and medical-grade silicone are selected based on their unique properties and the specific needs of the medical devices being manufactured. These materials are essential to ensure the safety, functionality, and regulatory compliance of the medical products that rely on them.
Product Design Team Requirements at China Medical Plastic Parts Factory
When providing medical injection molding services, the product design team of a China medical plastic parts factory plays a crucial role in ensuring that the manufactured parts meet the highest standards of safety, functionality, and regulatory compliance. These requirements encompass various aspects, including regulatory knowledge, material selection, design for manufacturability, quality control processes, and communication with clients. The design team must focus on creating functional, precise, and cost-effective designs while maintaining the strictest standards for medical applications. Below are the key aspects that the design team must consider when offering these services.
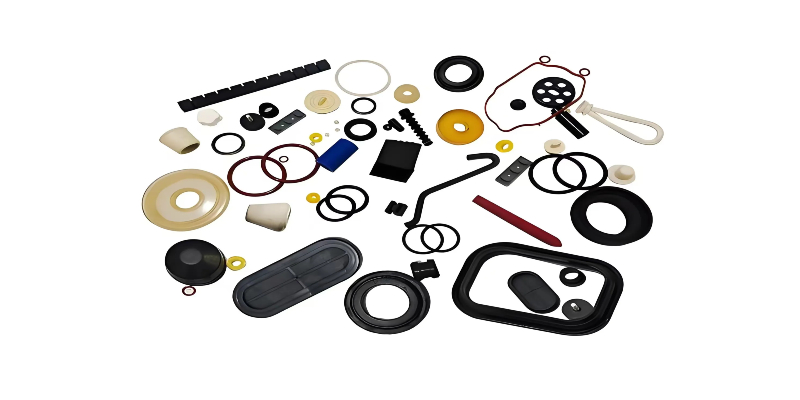
Regulatory Compliance and Certification Requirements
The design team must be highly knowledgeable about the regulatory standards governing medical devices, especially the rigorous requirements set by international authorities like the FDA, ISO 13485, and other regional health regulations. Ensuring that the product meets all legal and safety standards is a foundational requirement when providing medical injection molding services.
To meet regulatory requirements, the team must incorporate design elements that comply with these guidelines. This includes selecting materials that are certified as biocompatible (e.g., ISO 10993 standards), ensuring designs allow for proper sterilization, and including features that facilitate traceability in case of recalls. In China, medical plastic parts factories are held to these standards to guarantee that the medical products they produce are safe for use in healthcare environments globally.
Material Selection and Biocompatibility
Selecting the right material is one of the most important decisions the product design team has to make. The team needs to choose plastics that are not only suitable for injection molding but also biocompatible, durable, and able to meet the specific requirements of medical applications.
For medical injection molding, commonly used materials include polycarbonate (PC), polyethylene (PE), polypropylene (PP), polystyrene (PS), and polyvinyl chloride (PVC). These materials must meet FDA guidelines for biocompatibility and not release harmful substances when in contact with the human body. The design team must evaluate factors such as chemical resistance, tensile strength, and resistance to high or low temperatures. Furthermore, the design of the part must allow for ease of sterilization, as many medical devices need to be autoclaved or undergo other sterilization processes before use.
Design for Manufacturability and Cost Efficiency
Another critical aspect of the design process is ensuring that the product is designed for manufacturability, meaning the design can be efficiently and cost-effectively produced using injection molding techniques. This involves considering factors like part complexity, material flow, mold design, and the overall manufacturability of the part.
In the case of China medical plastic parts factories, the design team needs to balance functional requirements with the potential production costs. They must design parts that are easy to mold, reducing the risk of defects or excessive waste. The design team also needs to consider aspects such as minimizing post-processing and ensuring that the design can be scaled up for large production runs without compromising quality or increasing costs.
Precision and Tolerances for Medical Devices
Precision is a critical factor when designing medical plastic parts for injection molding. Medical devices often require very tight tolerances to ensure proper functionality and patient safety. The product design team must ensure that the design can be manufactured with a high level of accuracy, which can involve detailed simulations and adjustments before finalizing the design.
The team must also consider how variations in mold tooling or material properties might impact the part’s final dimensions. China’s medical plastic parts factories often use advanced software and prototyping methods to verify designs before production, ensuring that all dimensions, including wall thickness, venting, and fit, are within the acceptable tolerance ranges. This attention to detail is essential to avoid complications during manufacturing and to ensure that medical devices function as intended.
Quality Control and Testing Protocols
The design team must work closely with the factory’s quality control (QC) team to implement robust testing protocols for the medical plastic parts. These parts must undergo rigorous testing for functionality, safety, and compliance with medical standards before they are approved for production.
In China’s medical plastic parts factories, product testing may involve mechanical testing (e.g., tensile and compression tests), chemical compatibility testing, and sterilization validation. The design team must ensure that the design allows for the necessary tests to be carried out at various stages of production. Additionally, they should collaborate with the QC team to monitor every stage of the manufacturing process, ensuring that the parts meet the required standards and that the final products are free of defects.
Collaboration with Clients and Prototyping
Effective communication between the product design team and clients is essential for the successful development of medical plastic parts. The design team must understand the client’s specific needs, including the intended use of the product, and translate these requirements into a functional design. The design process often involves several rounds of feedback and revisions.
Prototyping is a critical step in this process. The design team will typically create prototypes or 3D models of the part using advanced technologies like rapid prototyping or 3D printing. These prototypes allow the client to evaluate the design and provide feedback before moving to full-scale production. In China’s medical plastic parts factories, prototyping can help identify potential issues early, reducing costly revisions in the later stages of production.
The product design team of a China medical plastic parts factory plays a vital role in ensuring that medical injection molding services meet all necessary safety, regulatory, and functional requirements. By considering factors such as regulatory compliance, material selection, manufacturability, precision, and quality control, they help create medical devices that are reliable, safe, and effective. Effective collaboration with clients and the use of advanced prototyping and testing further ensure that the final products meet the high standards expected in the healthcare industry.
Production Equipment Requirements at China Medical Plastic Parts Factory
When a China medical plastic parts factory provides medical injection molding services, the production equipment used must meet stringent requirements to ensure the highest standards of product quality, precision, and compliance with medical industry regulations. The choice of equipment directly affects the efficiency, accuracy, and reliability of the manufacturing process. These requirements encompass various aspects such as equipment precision, environmental control, automation, and quality assurance. Below, we explore the key production equipment requirements in a China medical plastic parts factory when delivering medical injection molding services.
Precision Injection Molding Machines
A China medical plastic parts factory must use highly accurate injection molding machines to produce high-quality medical components. These machines need to be capable of precisely controlling critical parameters such as injection speed, pressure, and temperature. The accuracy of these settings is crucial for producing complex, small, and intricate medical parts like syringes, catheters, or implants. Precision machines ensure that parts are molded to exact specifications and meet stringent dimensional tolerances. Additionally, precise molding reduces the chances of defects such as warping or surface imperfections, ensuring the final product’s safety and functionality.
Clean Room Facilities
Given the sensitive nature of medical products, it is essential for production equipment to be used in a controlled environment, specifically clean rooms, to minimize contamination risks. Clean room facilities are necessary to maintain the required air quality standards, ensuring that dust, airborne microbes, and other contaminants do not affect the molding process or the final medical products. In a China medical plastic parts factory, equipment must be maintained in such an environment to adhere to industry regulations such as ISO 13485 and GMP (Good Manufacturing Practice). Clean rooms not only protect the product but also provide a safe workspace for technicians handling delicate components.
Temperature Control and Cooling Systems
Precise temperature control is another critical aspect of medical injection molding. Both the injection molding machines and molds require efficient temperature management to ensure that the plastic material flows properly and cures correctly. In a China medical plastic parts factory, advanced temperature control systems must be installed to maintain stable and optimal temperature conditions during the molding process. This includes both heating elements to keep the material at the right viscosity and cooling systems to help solidify the molded parts quickly and evenly. This temperature regulation helps prevent defects such as short shots, sink marks, and inconsistencies in product quality.
Automation and Robotic Systems
Automation plays a significant role in enhancing the efficiency and accuracy of medical injection molding processes. China medical plastic parts factories often incorporate robotic systems and automated production lines to reduce human error and improve productivity. Robots can handle tasks such as part removal, insertion of inserts, assembly, and packaging with speed and precision. Automation also allows for better repeatability in production, ensuring that each part meets the required standards consistently. Moreover, robots can handle delicate medical parts with care, reducing the risk of contamination or damage during production.
Quality Control and Inspection Equipment
A China medical plastic parts factory must be equipped with state-of-the-art quality control and inspection equipment to ensure that every molded part meets the stringent safety and performance requirements. This includes advanced measurement systems like laser scanners, coordinate measuring machines (CMM), and visual inspection systems. These tools check for critical aspects like part dimensions, surface quality, and the absence of defects. In addition, more advanced testing equipment like X-ray inspection, tensile testing, and leak testing may be used to verify the structural integrity and functionality of complex parts. Continuous inspection ensures that only high-quality, reliable components are produced for medical applications.
Mold and Tooling Equipment
The quality of the molds and tooling used in the injection molding process directly impacts the final product’s performance. In China medical plastic parts factories, high-precision mold-making equipment is essential for manufacturing molds that can produce accurate, durable, and consistent parts. CNC (Computer Numerical Control) machines and EDM (Electrical Discharge Machines) are commonly used for precise mold creation and maintenance. The ability to create complex mold designs is crucial for manufacturing intricate medical components, and maintaining mold quality ensures that each production cycle results in consistent, defect-free products. Regular maintenance and calibration of molds are also vital to maintain production quality.
Compliance with Regulatory Standards
All equipment used in the production process must adhere to local and international standards for medical device manufacturing. A China medical plastic parts factory must ensure that their injection molding machines, production equipment, and facility meet certifications such as ISO 13485, ISO 9001, and FDA regulations. These certifications verify that the equipment is capable of producing medical-grade components that are safe, reliable, and compliant with global medical device standards. Compliance with these regulations is essential to ensure the production of medical devices that can be used in hospitals, clinics, and other healthcare settings with confidence.
The production equipment used by a China medical plastic parts factory in medical injection molding services must meet high standards of precision, environmental control, automation, and regulatory compliance. By using advanced injection molding machines, clean room facilities, temperature control systems, automation, and rigorous quality control methods, these factories ensure the production of safe, reliable, and high-quality medical plastic components. Proper maintenance and adherence to industry standards further ensure that these medical parts meet the exacting demands of the healthcare industry.
How China Medical Plastic Parts Factory Ensures Quality and Compliance
Ensuring quality and compliance in medical injection molding production is a critical responsibility for any factory involved in the manufacturing of medical devices. For China medical plastic parts factories, this involves a combination of stringent quality control measures, adherence to international regulations, continuous monitoring of production processes, and effective collaboration with clients. The overall goal is to produce medical parts that are safe, durable, biocompatible, and able to meet all relevant regulatory standards. Below, we will explore how these factories ensure quality and compliance through various structured approaches, including material selection, manufacturing processes, testing protocols, certifications, and traceability.
Adherence to Regulatory Standards and Certifications
Compliance with international regulatory standards is essential for any medical plastic part manufacturing process. China medical plastic parts factories are required to meet the stringent standards set by regulatory bodies such as the FDA, ISO 13485, ISO 10993, and Good Manufacturing Practices (GMP). These standards ensure that medical devices are safe and effective for patient use.
To achieve this, factories must demonstrate their ability to consistently produce medical components that meet these high standards. China-based factories that specialize in medical injection molding go through a rigorous certification process to prove they comply with all necessary regulations. This includes periodic audits, assessments of the factory’s operational processes, and ensuring that the materials used meet biocompatibility criteria, particularly ISO 10993. Adherence to these standards also ensures that the end products meet the required safety and quality benchmarks for medical applications.
Material Selection and Biocompatibility Testing
The quality and compliance of medical plastic parts heavily depend on the choice of materials, which must meet the requirements for biocompatibility and safety. China medical plastic parts factories are meticulous in selecting raw materials that comply with medical-grade standards. Common materials used in medical injection molding include polypropylene (PP), polyethylene (PE), polycarbonate (PC), polystyrene (PS), and polyvinyl chloride (PVC).
The factory ensures that all materials undergo rigorous biocompatibility testing, as required by international standards such as ISO 10993, to confirm that they do not cause adverse reactions when in contact with the human body. These tests typically assess factors such as cytotoxicity, skin irritation, and sensitivity. Additionally, some materials may undergo specific tests for chemical leaching, especially for long-term medical implants or devices that will remain inside the body. By carefully selecting and testing these materials, China’s medical plastic parts factories ensure the safety and effectiveness of their products.
Quality Control and Inspection Systems
To maintain consistent product quality and meet regulatory standards, China medical plastic parts factories implement strict quality control and inspection systems throughout the production process. These factories utilize advanced inspection equipment to monitor every stage of the injection molding process, from material preparation to final product inspection.
Key components of the quality control system include automated checks for dimensional accuracy, visual inspections to identify surface defects, and tests for mechanical properties such as tensile strength and flexibility. Non-destructive testing methods, like ultrasonic testing and X-ray inspections, may also be employed to detect internal defects. Each batch of parts is thoroughly inspected to ensure it meets the required specifications. This consistent approach to quality control ensures that every product leaving the factory complies with medical device regulations and is free from defects.
Sterilization and Cleanroom Manufacturing
Sterilization is a critical part of ensuring the safety and compliance of medical plastic parts, especially for devices intended for direct contact with patients or for long-term implantation. China medical plastic parts factories that manufacture medical devices for sterile applications operate under strict cleanroom conditions. These controlled environments are designed to minimize the risk of contamination during production and assembly.
In addition to maintaining cleanroom standards, many factories also perform post-manufacturing sterilization procedures on medical parts, depending on the nature of the device. This could involve techniques such as autoclaving, gamma radiation, or ethylene oxide sterilization. These processes ensure that the final products are free from harmful pathogens, bacteria, or viruses, meeting the high standards required for medical use. Ensuring proper sterilization not only guarantees patient safety but also ensures compliance with regulatory requirements set by health authorities around the world.
Testing Protocols and Performance Validation
China medical plastic parts factories also implement rigorous testing protocols to validate the performance and safety of medical injection molded parts. The testing may include mechanical testing, environmental testing, and biocompatibility tests to confirm that the parts can withstand the physical and chemical stresses they will encounter during use.
Mechanical testing includes evaluating tensile strength, compressive strength, and impact resistance, while environmental testing ensures that the parts perform well under a range of conditions such as extreme temperatures, humidity, or exposure to chemicals. For medical applications, ensuring that the device performs as intended under real-world conditions is essential. By conducting these thorough tests, China-based factories ensure that the medical plastic parts produced are reliable, safe, and capable of performing their intended function throughout their lifespan.
Traceability and Documentation
Traceability is an important aspect of maintaining compliance in the medical device manufacturing industry. China medical plastic parts factories ensure that all products have complete traceability, meaning that every part can be traced back to its material source, production batch, and testing results. This is particularly important for regulatory compliance and quality assurance.
In the event of a product recall, traceability allows manufacturers to quickly identify the affected parts and take necessary corrective actions. Additionally, the factories maintain detailed documentation of all manufacturing processes, inspections, certifications, and testing results. This ensures that they can provide evidence of compliance during audits and inspections. The transparent documentation system fosters confidence with regulatory agencies and clients, ensuring the ongoing quality and compliance of the products.
Ensuring quality and compliance in medical injection molding production is a multi-faceted process that involves a comprehensive approach from material selection to post-production testing. China medical plastic parts factories implement strict measures to meet global regulatory standards such as FDA, ISO 13485, and ISO 10993, while ensuring the biocompatibility and performance of their products. From adhering to quality control standards and sterilization protocols to maintaining traceability and documentation, these factories take every necessary step to guarantee that their medical plastic parts are safe, reliable, and compliant with international regulations.
FAQs about China Medical Plastic Parts Factory
The global medical injection molding market has been experiencing significant growth, driven by increased demand for high-quality medical devices and plastic components. As of recent estimates, the market size is expected to surpass USD 10 billion by 2027, with a steady annual growth rate of around 6-8%. China plays a key role in this sector due to its large manufacturing capabilities and lower production costs. Many companies are turning to China for medical plastic parts manufacturing because of the country’s established infrastructure and advanced technology in injection molding. This growth is fueled by the continuous need for cost-effective, high-precision components such as syringes, surgical tools, and implants, as well as a rising demand for medical equipment in developing nations.
The cost of injection molding in China varies depending on several factors, including the complexity of the mold, material used, production volume, and part design. Typically, the initial mold-making cost can range from USD 2,000 to USD 50,000, depending on the part’s intricacy and material requirements. Production costs per unit in China are relatively low, with a range of USD 0.05 to USD 1.00 per part, based on the volume and material selection. Bulk production significantly reduces per-part costs. Labor costs in China are also much lower compared to Western countries, contributing to the affordability of manufacturing. For medical plastic parts, the additional costs of certifications and quality controls may increase the overall price, but China still remains a cost-effective option for medical injection molding production.
The cost of injection molding per hour varies based on machine size, production requirements, and labor costs. On average, the hourly rate for injection molding in China is between USD 30 to USD 150. This range includes the cost of running the injection molding machine, labor, and overhead costs. Large machines with high output or high-precision capabilities tend to be more expensive per hour due to the increased energy consumption and technical requirements. For medical-grade plastic components, which require high precision and adherence to quality standards, the cost can be on the higher end. Additionally, the complexity of the injection molds and the time required to change or maintain them can affect the overall hourly cost of production.
The medical industry is a significant consumer of plastic materials. In fact, it is estimated that around 15-20% of all plastic production is used in the medical sector. Medical plastic parts include items such as syringes, catheters, diagnostic equipment, drug delivery devices, and implants. Due to the rise of single-use medical products and the demand for lightweight, sterilizable, and cost-effective components, plastic usage continues to increase. In China, where mass production and affordability are key, plastic is extensively used to meet global demand. High-quality plastics like polyethylene, polypropylene, and medical-grade polycarbonate are most commonly used for these purposes due to their durability, biocompatibility, and ability to withstand sterilization processes. The trend toward advanced medical devices also drives continuous innovation in plastic material development.
Injection molding can be highly profitable, particularly when producing large volumes of products. The initial investment in mold creation and machine setup can be high, but once established, the cost per part significantly decreases with higher production runs. In China, the lower labor and operational costs make injection molding especially profitable for manufacturers in the medical sector. After the mold is created, the cost per part can be as low as a few cents, even for complex designs. The scalability of injection molding allows companies to generate high profit margins, especially when mass-producing medical components like syringes, vials, or disposable instruments. Profitability is further enhanced by technological advancements in molding machines, which reduce waste and increase production efficiency. For medical plastic parts, adherence to strict regulations and certifications, such as ISO and FDA compliance, adds to the profit potential as these products have a high market demand.
Injection molding is generally more cost-effective than machining, especially when producing large quantities of identical parts. Injection molding involves creating a mold and injecting molten plastic into it, which allows for high-volume production with minimal material waste and low per-part costs. The cost of labor, material, and machinery is significantly lower compared to machining, which involves cutting, drilling, or milling solid pieces of material from a larger block. For medical plastic parts, injection molding is typically the preferred method due to its precision, speed, and ability to produce complex shapes without the need for additional post-processing. While the upfront cost for creating molds may be high, the per-part costs decrease substantially with volume, making injection molding the more economical choice for large-scale production of medical components in China.
Yes, medical-grade plastic is designed and manufactured to meet strict safety and quality standards. These plastics are biocompatible, meaning they are compatible with the human body and do not cause adverse reactions. They are also resistant to sterilization methods, including autoclaving and gamma radiation, making them ideal for use in medical devices and packaging. In China, where many medical plastic parts are produced, manufacturers must adhere to international standards, such as ISO 13485 and FDA regulations, to ensure that the plastic materials are safe for use in medical applications. Medical-grade plastics are rigorously tested to ensure they meet the necessary standards for safety, strength, and durability. Examples of common medical-grade plastics include polycarbonate, polypropylene, and polyethylene, which are used in devices ranging from syringes to surgical instruments.
Catheters, which are critical medical devices used for a variety of procedures, are made from medical-grade plastics that offer flexibility, biocompatibility, and resistance to friction. Common plastics used for catheters include polyurethane (PU), silicone, polyvinyl chloride (PVC), and thermoplastic elastomers (TPE). Polyurethane is widely used for its durability and flexibility, while silicone is often selected for its softness and biocompatibility, making it ideal for long-term use. PVC is used in some catheter designs due to its flexibility and ease of manufacturing, while TPE is favored for its ability to combine the properties of rubber and plastic. China’s medical plastic parts factories produce catheters with these materials, ensuring that the products meet stringent medical standards for patient safety and comfort.
In the pharmaceutical industry, various types of medical-grade plastics are used to ensure the safe and effective packaging, storage, and transportation of drugs. Polyethylene (PE) and polypropylene (PP) are common for drug packaging, such as bottles, vials, and blister packs, due to their resistance to moisture, chemical inertness, and low cost. Polycarbonate (PC) is used for containers that require transparency, while polyvinyl chloride (PVC) is often used for flexible packaging, including blood bags and IV containers. In China, pharmaceutical companies rely on these high-quality plastics from medical plastic parts factories to ensure that products meet both national and international standards for safety and performance in the healthcare market.
Medicine containers, such as pill bottles, syringes, and vials, are often made from a variety of plastics, depending on the specific requirements for safety, transparency, and resistance to chemical reactions. Common plastics used for medicine containers include polypropylene (PP), polyethylene (PE), polycarbonate (PC), and polyvinyl chloride (PVC). Polypropylene is frequently used for oral medication containers due to its chemical resistance and ease of sterilization. Polycarbonate is often used when transparency is essential, such as in liquid medication containers. In China’s medical plastic parts factories, these materials are carefully selected to ensure that the containers are durable, tamper-resistant, and able to maintain the integrity of the medication inside.
Plastic is a versatile and cost-effective material widely used in medical supplies due to its flexibility, sterilization properties, and ability to be molded into complex shapes. Common medical supplies made of plastic include syringes, IV bags and tubing, catheters, blood bags, surgical instruments, gloves, dressing and wound care products, and implantable devices. Many of these medical supplies are manufactured in China’s medical plastic parts factories, where the materials undergo extensive testing to ensure safety and performance. The use of plastics in medical supplies enables mass production while maintaining strict standards for biocompatibility, performance, and sterility, ensuring they meet regulatory requirements such as those from the FDA and ISO.
Medical plastics are materials specifically designed to be safe and effective in medical applications. They are typically biocompatible and durable under various medical conditions. Common types of medical plastic include polycarbonate (PC), polyethylene (PE), polypropylene (PP), polystyrene (PS), and polyvinyl chloride (PVC). These plastics are commonly used in medical devices, surgical tools, and packaging materials. In China, medical plastic parts factories adhere to rigorous safety and quality standards to ensure that the materials meet both international and local regulatory requirements. Medical-grade plastics are widely used in the production of syringes, blood bags, tubing, and various implantable devices due to their ability to be sterilized, molded into precise shapes, and used in life-saving medical applications.
The hardest plastics used in injection molding are typically high-performance engineering plastics, such as polyetheretherketone (PEEK), polycarbonate (PC), and acrylonitrile butadiene styrene (ABS). PEEK is known for its exceptional hardness, strength, and resistance to high temperatures, making it ideal for medical implants and surgical tools. Polycarbonate (PC) is also considered a hard plastic, with excellent impact resistance and optical clarity, suitable for devices that require durability and precision. These materials are often processed in China’s medical plastic parts factories for applications that demand superior mechanical properties and biocompatibility. While harder plastics provide durability and performance, their molding process can be more complex and costly, requiring high-quality equipment and skilled labor.
The best medical-grade plastic depends on the specific application and performance requirements of the medical device. For example, polycarbonate (PC) is widely regarded for its transparency, toughness, and high impact resistance, making it ideal for items like surgical instruments and diagnostic devices. Polypropylene (PP) is often favored for its chemical resistance and low moisture absorption, commonly used in sterile packaging and disposable medical items. Polyethylene (PE), particularly high-density polyethylene (HDPE), is frequently used for medical containers due to its strength and ability to resist wear. Polyvinyl chloride (PVC) is used in applications like blood bags, tubing, and catheters. In China’s medical plastic parts factories, a combination of these materials is used depending on the device’s requirements, ensuring optimal performance and compliance with international standards.
Medical-grade plastic refers to a specific category of plastic materials that are manufactured to meet the rigorous standards required for use in medical devices. These plastics are engineered to ensure safety, durability, and biocompatibility. Some of the most common medical-grade plastics include polycarbonate (PC), polyethylene (PE), polypropylene (PP), polystyrene (PS), and polyvinyl chloride (PVC). In China, factories specializing in medical plastic parts typically use these materials due to their reliability and adaptability in producing various medical components, such as syringes, IV components, and diagnostic tools. These plastics undergo extensive testing and certification to ensure that they comply with regulations like ISO 10993 and FDA guidelines for medical device safety.
Injection molding, while being a popular manufacturing method in industries like medical plastics, does have some disadvantages. One of the key drawbacks is the high initial cost, which involves expensive molds and tooling. For smaller production runs, this cost can be prohibitive, making injection molding less economical. Additionally, the process has limitations in terms of material choices; some complex materials may not be suitable for injection molding due to difficulty in processing or limitations in achieving specific properties. In China’s medical plastic parts factories, issues such as the potential for uneven material distribution, part warping, and long lead times for mold creation can also affect production efficiency. While injection molding is ideal for high-volume, precision-based medical device parts, these factors can hinder its use in certain applications.
Medical-grade polymers are designed to meet strict safety and biocompatibility standards, which ensure they are not toxic when used in medical applications. However, toxicity can depend on the specific type of polymer, the manufacturing process, and the intended use. Medical-grade plastics, such as polypropylene, polyethylene, and polycarbonate, are widely used in medical devices because they are safe and non-toxic. These materials must undergo rigorous testing to meet international standards such as ISO 10993 for biocompatibility. In some cases, impurities or certain additives in the plastic may pose a risk, but these materials are extensively tested to ensure that they do not cause adverse reactions when in contact with the human body. China’s medical plastic parts factories follow these stringent guidelines to ensure the safety of their products.
Contact our professional team now for a same-day quote and risk-free project evaluation. Benefit from ISO 8 cleanrooms, advanced machines, and 12-hour fast response in medical injection molding.