Metal Injection Molding (MIM) is a transformative manufacturing process widely used in the production of complex and high-precision metal components. The process is particularly beneficial in industries such as medical devices, where intricate designs, biocompatibility, and reliability are essential. By combining fine metal powders with binders, MIM can produce highly detailed parts that are both durable and cost-effective. This method is increasingly popular for making small yet critical components in medical equipment, such as surgical instruments, implants, and diagnostic tools. In this article, we will explore the MIM process, its benefits for medical applications, the materials used, and its advantages over other manufacturing methods. Metal injection molding medical offers a sustainable, scalable method for producing precise, biocompatible, and complex parts for medical devices.
Low-Volume to High-Volume Production Capabilities
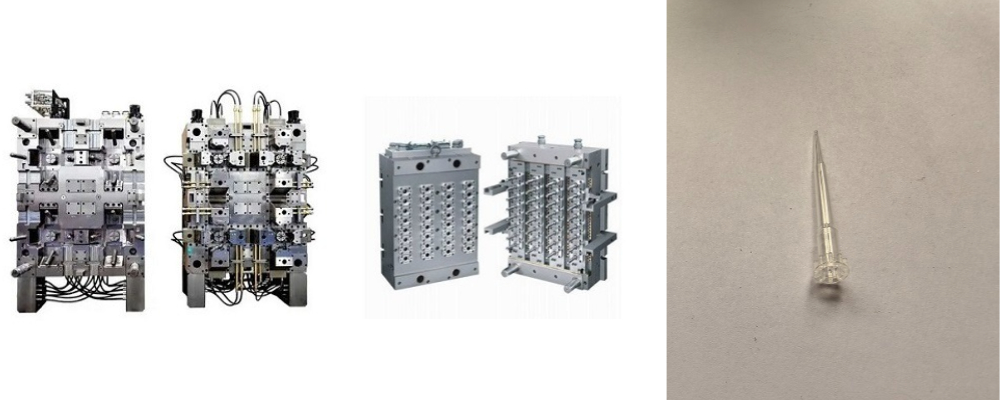
Attributes | Details |
---|---|
Place of Origin | Dongguan, Guangdong, China |
Brand Name | LY Medical Injection Mold |
Product Name | Medical Molding |
Technology | Injection Molding |
Plastic Processed | PP, PC, ABS, PET, PVC, FRPP/PVC, PPR, EVA, HDPE, MLLDPE, EPS, PA, Polystyrene, PE, LDPE, EVOH, HDPE/PP, ABS/PP, PE/PP, Polylactic Acid, TPU |
Size and Weight | According to customer/drawing requirements |
Tolerance | ±0.02-0.04 mm |
Certificate | ISO9001:2015 |
Drawing Format | .igs/.stp/.x-t/.step/.stl/.sldprt/.dwg/.dxf |
Surface Finishing | Matt/ Texture/ Polishing/ UV Coating/ Rubberizing ,etc |
Advantages | One-stop shopping |
Selling Units | Single item |
What is Metal Injection Molding in the Medical Industry?
Definition of Metal Injection Molding (MIM)
Metal injection molding medical procedures are advanced manufacturing methods that combine finely powdered metals with polymer binders to form intricate parts, particularly valuable for high-precision applications. In metal injection molding medical production, this process creates a feedstock that can be molded similarly to plastic, making it possible to achieve the fine detail required for medical components. After the feedstock is injected into molds and cooled, it undergoes debinding to remove polymers, leaving only metal behind. The final product is then sintered, creating dense, durable, and complex shapes that are well-suited for medical-grade requirements, supported by the precision of medical injection molding techniques.
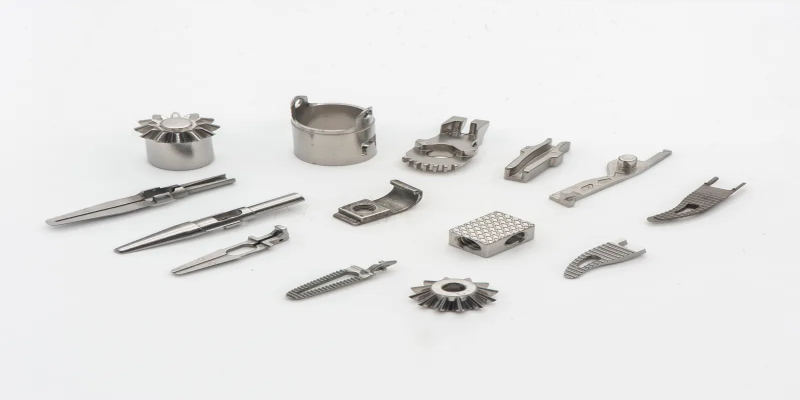
Benefits of MIM for Medical Applications
Metal injection molding medical applications allow for the efficient production of small, detailed, and precise metal components, ideal for devices that require a high level of accuracy. This method supports the medical industry by providing components with complex geometries and a high surface finish, essential for parts like surgical tools, implants, and diagnostic instruments.
The Metal Injection Molding Medical Procedure
Step-by-Step Process
The metal injection molding medical procedure is a specialized process that creates precise, small metal parts required in the medical field. The steps involved are intricate and carefully monitored to ensure high-quality outcomes.
- Injection of Metal Feedstock
The process begins with a carefully prepared mixture, or feedstock, made by combining finely powdered metal with polymer-based binders. This feedstock is injected into a high-pressure mold, similar to plastic injection molding, allowing intricate shapes and details to be formed. For metal injection molding medical applications, this precise shaping is essential for components used in sensitive medical devices. - Creation of “Green Parts”
Once the feedstock is injected and cooled within the mold, the initial parts, known as “green parts,” are formed. These green parts maintain the general shape of the final product but still contain the binder material that must be removed. At this stage, excess material such as runners and gates are trimmed away to refine the part’s shape. - De-Binding Process
To transform green parts into “brown parts,” a de-binding process is used to remove the polymer binder. This step is critical for metal injection molding medical products because it helps achieve a pure metal structure, eliminating impurities that could affect the part’s function and reliability in medical environments. The de-binding leaves only the metal particles, forming a porous, brown structure. - Sintering for Density and Strength
The final step is sintering, where the brown parts are heated to a high temperature in a controlled atmosphere. During sintering, the metal particles bond together to form a dense, non-porous structure, ideal for medical-grade parts that require both durability and strength. This heating also results in minor shrinkage, which is accounted for during earlier stages to ensure the final part meets exact specifications.
Comparison with Other Methods (such as metal injection molding vs. die casting)
When comparing metal injection molding vs. die casting, particularly for medical purposes, several differences emerge. Metal injection molding medical parts can achieve a higher level of detail than die-cast parts, as MIM supports finer shapes and allows for complex geometries that die casting might struggle with. Additionally, metal injection molding medical components often involve less material waste due to the high precision of MIM, making it an ideal choice when working with expensive materials. The MIM process is better suited for producing intricate parts in high volume, whereas die casting may be more cost-effective for simpler designs and lower precision needs.
Metal Injection Molding Medical Uses
Applications of MIM in the Medical Industry
Metal injection molding medical applications have transformed the production of small, complex components critical to the functionality and safety of many medical devices. The MIM process enables the creation of intricate parts with precise dimensions, making it ideal for components that need to perform accurately within high-stakes medical environments.
One significant use of metal injection molding medical technology is in surgical instruments, where precision and durability are essential. Surgical tools such as forceps, clamps, and scissors benefit from MIM’s ability to produce strong, complex shapes that withstand repeated sterilization and usage. Another application is in endoscopes and laparoscopic tools, which require small, intricate parts to navigate delicate areas of the body safely and effectively.
MIM is also highly valuable for dental tools and components, including orthodontic brackets and parts for dental surgery equipment, where detailed features and biocompatibility are crucial. Additionally, orthopedic implants, such as knee, hip, and spine implants, are commonly produced using MIM. These implants require robust, biocompatible materials to integrate with the human body and function reliably over time. The MIM process also supports the production of parts with complex internal structures, which are essential for components like joint replacements and prosthetics.
Advantages of MIM in Medical Applications
Metal injection molding medical applications offer several advantages that are uniquely suited to the demands of the medical industry. Enhanced design flexibility is a major benefit, as MIM allows for intricate geometries and complex shapes that would be difficult or impossible to achieve with other manufacturing methods. This flexibility is especially valuable when creating components for minimally invasive surgical tools and diagnostic equipment, where space constraints and detailed designs are essential.
Another advantage is the superior strength and biocompatibility of MIM-produced parts. Medical components must endure repetitive use, sterilization processes, and, in the case of implants, integration with body tissues. MIM materials can be chosen and processed to ensure that they meet stringent medical standards for both durability and biocompatibility, essential for safe use in or on the human body.
Metal injection molding medical processes also offer material efficiency and cost-effectiveness in high-volume production. By minimizing waste and maximizing the use of expensive materials, MIM supports cost-effective manufacturing, even for intricate parts. This efficiency is particularly beneficial when using costly biocompatible metals, such as titanium or stainless steel, commonly required in medical devices. Overall, MIM offers a reliable, flexible, and efficient solution for producing high-quality medical components that meet rigorous industry standards.
Precision Metal Stamping for Medical Devices
What is Precision Metal Stamping for Medical Devices?
Precision metal stamping for medical devices is a specialized process used to create high-precision, durable metal components that meet the stringent requirements of the medical industry. Unlike general stamping, precision metal stamping for medical applications is engineered to produce extremely accurate parts with complex geometries and tight tolerances. This makes it an essential technique for manufacturing components used in devices such as pacemakers, surgical instruments, and implantable devices.
Key Benefits of Precision Metal Stamping for Medical Devices
Precision metal stamping for medical devices offers several advantages that are critical to the production of medical-grade parts:
- High Accuracy: Precision metal stamping achieves exacting tolerances, ensuring that every component meets the strict specifications required for medical use. This accuracy is vital for parts that must perform reliably in critical applications, such as surgical tools or implant components.
- Material Efficiency: The process is highly efficient, minimizing material waste, which is especially beneficial when working with expensive, biocompatible metals required in medical manufacturing.
- Scalability for Mass Production: Precision metal stamping is ideal for high-volume production, as it can produce large quantities of consistently high-quality parts, which is essential for medical device manufacturers.
Applications of Precision Metal Stamping in Medical Devices
The versatility of precision metal stamping makes it suitable for producing a wide range of components used in the medical industry, including:
- Surgical Instruments: Components like forceps, clamps, and scissors benefit from the high precision and durability achieved through metal stamping.
- Implantable Devices: Metal stamped parts are commonly used in cardiac and orthopedic implants, where biocompatibility and long-lasting performance are essential.
- Diagnostic Equipment: Precision-stamped metal parts are integral to various diagnostic tools, providing structural integrity and reliability in devices such as imaging systems and handheld testing instruments.
While precision metal stamping offers many benefits for the production of medical devices, it is often used in conjunction with other advanced manufacturing techniques, such as metal injection molding medical processes. This combination, along with the use of precision mold medical, supports the production of complex, high-performance components essential for modern medical technology.
Metal Injection Molding for Medical Devices
Overview of Metal Injection Molding for Medical Devices
Metal injection molding for medical devices is a specialized manufacturing method that enables the production of intricate, high-precision metal components essential for various medical applications. Unlike traditional machining or casting methods, MIM offers the ability to produce small, detailed parts with complex geometries, which are often required in modern medical devices. This method combines finely powdered metal with a binder material to create a moldable feedstock, allowing for the production of medical-grade components that meet stringent quality and performance standards.
Key Applications in Medical Devices
- Surgical Instruments: Metal injection molding for medical devices is used to create components for precise and durable surgical tools, such as forceps, clamps, and scissors. These parts must withstand repeated sterilization while maintaining functionality and biocompatibility.
- Implants: MIM is ideal for producing small, complex parts used in orthopedic and dental implants. The ability to mold biocompatible metals, such as titanium and cobalt-chromium alloys, ensures that the resulting implants are safe and long-lasting within the body.
- Diagnostic Equipment: In diagnostic and imaging tools, MIM provides components that are lightweight yet strong, enabling consistent performance in demanding medical environments.
Advantages of Metal Injection Molding for Medical Devices
- High Precision: Metal injection molding for medical devices achieves high tolerances, which are crucial for producing parts that require exact dimensions and functionality. The use of a medical device injection mold ensures that these parts are manufactured with the utmost accuracy, meeting the stringent standards needed for medical applications.
- Material Versatility: The process allows for the use of a wide range of metals, such as stainless steel, titanium, and other biocompatible materials suitable for use in the human body.
- Cost-Effectiveness: MIM is efficient for high-volume production, offering cost savings in comparison to traditional machining methods, especially when producing small, intricate parts.
Metal injection molding for medical devices is transforming the medical manufacturing landscape by providing a reliable, precise, and scalable solution for creating high-quality medical components. As part of this transformation, metal injection molding medical continues to play a key role in advancing the precision and functionality of medical devices, ensuring better performance and reliability for healthcare applications. The use of medical parts injection molds further enhances this process by enabling the production of complex, high-precision components that meet the stringent demands of the medical industry.
Materials Used in Metal Injection Molding for Medical Devices
Overview of Common MIM Materials
In the metal injection molding medical process, selecting appropriate materials is crucial for creating parts that meet rigorous medical standards. Common materials include stainless steel, titanium alloys, and cobalt-chromium alloys, each offering unique properties that enhance device performance in medical settings.
- Stainless Steel: Known for its corrosion resistance and strength, stainless steel is often used in metal injection molding medical applications where durability and longevity are essential. Surgical instruments, such as scissors, clamps, and dental tools, frequently rely on stainless steel because it withstands repeated sterilization and resists rust, maintaining safety and functionality over time.
- Titanium Alloys: Titanium is highly valued for its lightweight nature, biocompatibility, and resistance to corrosion. In metal injection molding medical applications, titanium alloys are often chosen for implants and prosthetic components. These alloys are compatible with human tissue, reducing the risk of rejection, and they have a high strength-to-weight ratio, making them ideal for implants that need to integrate seamlessly with bone and other body structures.
- Cobalt-Chromium Alloys: Cobalt-chromium is known for its extreme hardness and wear resistance, making it suitable for orthopedic implants and components in high-wear areas. Metal injection molding medical parts made from cobalt-chromium alloys can endure the friction and pressure common in joint replacements, providing a reliable, long-lasting solution for patients.
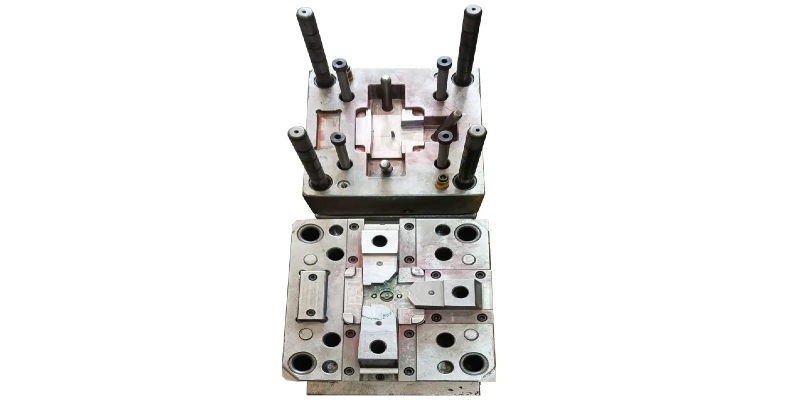
Choosing the Right Material for Medical MIM
Selecting the right material in medical metal injection molding production requires careful consideration of the device’s functional requirements. Critical criteria include strength, corrosion resistance, biocompatibility, and compatibility with human tissue.
For surgical tools, where high durability and resistance to corrosion are needed, stainless steel is an optimal choice. For implants that require integration with body tissues, titanium alloys are ideal due to their biocompatibility and lightweight nature, allowing them to function harmoniously within the body. In orthopedic applications, cobalt-chromium provides the necessary hardness and wear resistance for joint implants that will face continuous movement and pressure.
Material selection in metal injection molding medical applications not only affects device performance but also impacts patient safety and the product’s lifecycle. Medical molding products must resist body fluids and sterilization processes, both of which are standard in medical environments. Additionally, choosing materials that meet strict medical standards ensures that parts will perform reliably in high-stakes applications, such as implants and surgical tools.
Metal Injection Molding Machines and Equipment
Overview of MIM Machines
Metal injection medical molding manufacturing relies on specialized machines designed to handle the unique demands of this complex process. MIM machines are engineered to operate under high pressure and high temperature conditions, which are essential for effectively shaping and bonding metal powder particles into intricate components. These machines are equipped to inject metal feedstock — a combination of powdered metal and binders — into molds with extreme precision, ensuring that even the smallest details are accurately replicated. The high-pressure injection is critical for filling all areas of the mold, especially for medical parts with complex geometries and thin walls that require exact tolerances.
Key Features and Specifications
Metal injection molding medical equipment is built with features that enhance precision and reliability, addressing the rigorous standards necessary in medical device production. Key specifications include:
- Precision Control: Medical-grade MIM machines offer advanced control systems that regulate injection speed, temperature, and pressure, ensuring consistent quality. This precision is vital for medical components where dimensional accuracy is paramount, as even minor deviations can impact device performance and patient safety.
- Temperature Management: Effective temperature control throughout the injection and sintering stages is crucial, as variations can lead to inconsistencies in part density and structure. Metal injection molding medical equipment incorporates high-temperature capabilities, allowing parts to be sintered to a dense, non-porous finish that meets medical standards for strength and durability.
- Automated Quality Monitoring: Many MIM machines in medical applications come equipped with automated quality monitoring systems that detect any irregularities in the molding process, ensuring each part meets strict specifications. This technology reduces the risk of defects, which is essential for components that will be used in medical environments.
Examples of typical machinery used in metal injection molding medical production include precision injection molding machines designed for micro-molding, where very small parts require intricate detailing. These machines are commonly found in the production of surgical tools, dental instruments, and other small medical devices, providing the high accuracy and consistency needed for these critical applications.
The equipment used in the metal injection molding medical process not only ensures the precise formation of complex shapes but also supports the high-volume production demands of the medical industry. With automated systems and strict control over molding conditions, MIM machines help manufacturers achieve the consistent quality required for medical devices, supporting innovation and reliability in healthcare products.
Leading Metal Injection Molding Medical Companies in the Medical Field
Overview of Major Players in Medical MIM
The medical sector relies on specialized companies that provide metal injection molding medical services to meet the exacting requirements of the healthcare industry. Leading metal injection molding companies in this field focus on delivering high-precision parts that are critical for medical devices, surgical instruments, and implants. Some of the top players in the medical MIM market are:
- Company A – Known for its expertise in manufacturing small, highly intricate components used in medical applications, such as endoscopic instruments, surgical tools, and dental devices. The company’s focus on quality and compliance with regulatory standards like ISO 13485 has made it a trusted name in the metal injection molding medical industry.
- Company B – Specializes in producing titanium and stainless steel medical parts, offering solutions for orthopedic implants, dental implants, and diagnostic equipment. Their capabilities include the ability to work with complex geometries, delivering parts that meet both biocompatibility and sterilization requirements.
- Company C – A leader in custom solutions for medical device manufacturers, this company provides extensive material selection and specialized molding techniques for creating medical-grade components with exceptional strength and durability. Their focus on continuous process improvement ensures that they meet or exceed industry standards.
These companies have earned their reputation through a combination of technical expertise, state-of-the-art equipment, and a deep understanding of the regulatory requirements for medical products. Their ability to produce medical-grade components with complex geometries, superior strength, and biocompatibility has made them leaders in the metal injection molding medical field.
What to Look for in a Medical MIM Provider
When choosing a metal injection molding medical provider, it’s important to consider several key attributes to ensure the company can meet the high standards required for medical device manufacturing:
- Compliance with Medical Standards: A reputable provider must demonstrate strict adherence to medical regulations such as ISO 13485 (quality management for medical devices), FDA approvals, and other industry-specific certifications. These certifications ensure that the company can produce medical parts that meet regulatory and safety requirements.
- Precision Capabilities: Medical device manufacturers need a MIM provider with the capability to create components with extremely fine tolerances and intricate geometries. The provider should have advanced MIM equipment and expertise in molding tiny, complex shapes that are common in medical applications, such as surgical instruments and diagnostic equipment.
- Expertise in Material Selection: Different medical devices require specific materials based on their intended use, such as biocompatible metals like stainless steel, titanium, and cobalt-chromium. A capable provider should offer a wide range of materials, along with guidance on selecting the right one based on the device’s requirements for strength, corrosion resistance, and tissue compatibility.
- Customization and Prototyping Capabilities: As the demand for custom medical devices increases, it’s important to work with a provider who offers prototyping services to test designs before full-scale production. The ability to iterate designs quickly can save both time and costs in the development of new medical devices.
- Experience in High-Volume Production: In addition to precision and customization, medical MIM providers must be able to handle large production volumes efficiently without compromising quality. A provider experienced in high-volume production can deliver consistent, high-quality parts at scale, which is crucial for large medical device manufacturers.
When selecting a metal injection molding medical provider, these attributes are essential to ensure that the final products meet the demanding standards of the medical industry, delivering high-performance, reliable, and safe components for healthcare applications.
How Metal Injection Molding Medical Compares to Die Casting for Medical Parts
Metal Injection Molding (MIM) and die casting are both popular manufacturing methods used to produce metal parts, but they differ significantly in their suitability for different applications. When it comes to medical parts, precision, complexity, and material performance are key factors that influence the choice of manufacturing method. Below is a comparison of metal injection molding medical and die casting, highlighting their advantages and limitations for medical applications.
Factor | Metal Injection Molding (MIM) | Die Casting |
---|---|---|
Complexity of Design | MIM is ideal for small, intricate, and complex geometries with tight tolerances. | Die casting is better suited for simpler, less complex shapes. |
Precision and Tolerances | MIM offers higher precision and can achieve very tight tolerances, which is crucial for medical parts. | Die casting typically has lower precision, with less ability to handle tight tolerances. |
Material Options | MIM supports a wider range of materials, including biocompatible metals such as stainless steel and titanium, making it ideal for medical applications. | Die casting is typically limited to aluminum, zinc, and magnesium alloys, which may not be suitable for medical-grade parts. |
Surface Finish | MIM parts typically have a smoother surface finish and can be further polished or treated for medical use. | Die casting parts usually require additional finishing processes to achieve a smooth surface. |
Production Volume | MIM is efficient for both low and high-volume production runs, making it versatile for different stages of product development. | Die casting is more suited for high-volume production, but it may not be the best choice for low-volume or prototyping. |
Material Waste | MIM has low material waste, as most of the metal powder is used in the process. | Die casting produces more material waste due to the need for excess metal to fill the mold cavity. |
Lead Time | MIM typically requires longer lead times due to the multiple stages involved (such as de-binding and sintering). | Die casting has faster lead times, especially for simpler parts, due to fewer processing stages. |
Applications in Medical Devices | MIM is used for intricate components in surgical tools, implants, and diagnostic equipment, where precision and biocompatibility are critical. | Die casting is more commonly used for non-medical, high-volume parts that don’t require strict biocompatibility or high precision. |
Advantages of MIM Over Die Casting for Medical Parts
- Precision and Complexity: One of the major advantages of metal injection molding medical over die casting is the ability to produce small, highly complex parts with tight tolerances. This is crucial in the medical industry, where precise components are needed for devices such as surgical instruments, dental tools, and implants.
- Material Versatility: MIM allows for the use of a variety of biocompatible materials, including stainless steel, titanium alloys, and cobalt-chromium, which are critical for medical applications where corrosion resistance, strength, and tissue compatibility are essential. Die casting, on the other hand, is typically limited to aluminum and zinc alloys, which may not meet the specific requirements for medical-grade devices.
- Lower Material Waste: MIM produces minimal material waste since the majority of the metal powder used in the process is incorporated into the final product. This can be especially important in the production of medical components, where material cost is a factor. Die casting, however, requires excess material to fill the mold cavity, leading to higher material waste.
Scenarios Where Die Casting Might Be Preferred
- Simpler Designs: Die casting is ideal for producing parts with simpler geometries and designs, making it a more cost-effective option for components that don’t require the precision and complexity achievable by metal injection molding medical. For instance, parts that require little to no detail or have larger tolerances can be efficiently manufactured using die casting.
- High-Volume Production: Die casting is often the preferred method for high-volume production runs where speed is essential. Due to its faster cycle times, die casting can be more economical for mass-producing parts that don’t require the advanced precision of MIM.
While metal injection molding medical offers superior precision, material versatility, and low material waste, die casting can be a better choice for simpler, high-volume parts that don’t require the same level of detail and biocompatibility. Choosing the right method depends on the specific requirements of the medical parts being manufactured, including their complexity, material needs, and production scale.
The Future of Metal Injection Molding Medical in Medical Applications
The future of metal injection molding medical in the healthcare industry is promising, as advancements in materials and technology continue to evolve. As the demand for precision, biocompatible, and cost-effective solutions grows, MIM is poised to play an even more critical role in the manufacturing of medical devices and components. Below, we explore the innovations and potential growth that will shape the future of MIM in medical applications.
Innovations in MIM for Medical Devices
- Emerging Materials for MIM: One of the most significant advancements in metal injection molding medical is the development of new materials that enhance both the performance and durability of medical components. For example, the incorporation of advanced alloys such as titanium and bioactive ceramics is enabling the production of parts that offer superior strength, corrosion resistance, and biocompatibility. These materials are essential for implants and surgical instruments that must withstand harsh conditions inside the human body.
- Process Advancements: Innovations in MIM processing are also contributing to the future of medical applications. Improvements in sintering techniques, for instance, have led to parts with even finer microstructures, allowing for higher density and mechanical properties. Additionally, advancements in molding technology are increasing production speed, reducing cycle times, and making MIM more cost-effective for both small and large runs of medical components. These innovations are critical as the medical industry continues to demand more complex, customized parts with higher precision and performance.
- Customization and Design Flexibility: The future of metal injection molding medical will also be driven by the increasing need for personalized and patient-specific medical devices. MIM allows for the creation of highly complex geometries that would be difficult or impossible to achieve with traditional manufacturing methods. This opens up possibilities for custom implants, orthopedic devices, and even personalized surgical tools that cater to the unique needs of individual patients.
Potential for Growth in Medical Manufacturing
- Growing Demand for Precision Parts: The healthcare sector is increasingly relying on precision metal components for high-performance devices, such as diagnostic equipment, surgical instruments, and implantable devices. As medical technology advances, the need for small, detailed, and reliable parts is more pronounced than ever. Metal injection molding medical offers a solution that can meet these stringent requirements, making it a key player in the future of medical manufacturing.
- Integration with Emerging Technologies: The demand for metal injection molding medical is also fueled by the growth of emerging technologies like minimally invasive surgeries, robotic surgeries, and wearables. These cutting-edge applications require precision-engineered parts that can withstand high-stress environments while maintaining safety and biocompatibility. MIM is already used in the production of parts for robotic surgical tools and endoscopic devices, and as these technologies evolve, the need for more sophisticated and durable components will continue to rise.
- Cost-Efficiency and Sustainability: As the medical device industry faces pressure to reduce production costs without compromising quality, MIM’s cost-efficiency becomes even more crucial. The ability to produce highly detailed components in a more cost-effective manner, with minimal material waste, positions metal injection molding medical as a sustainable option for the growing demand in medical manufacturing.
The future of metal injection molding medical is bright, with continued advancements in materials, processes, and technology paving the way for more innovative and efficient solutions in medical manufacturing. As the medical industry demands increasingly complex and reliable components, MIM will remain at the forefront, driving progress in medical device manufacturing and contributing to the development of safer, more effective medical technologies.
Key Takeaways for Metal Injection Molding Medical in Medical Manufacturing
As we explore the growing significance of metal injection molding medical in the manufacturing of medical devices, several key takeaways highlight its role in advancing medical technology and improving production efficiency. Below is a summary of the essential benefits and contributions of MIM to the medical industry.
MIM’s Role in Producing High-Quality Medical Devices
- Precision and Detail: Metal injection molding medical is renowned for its ability to produce highly intricate and precise components that meet the stringent standards of the healthcare industry. From surgical instruments to orthopedic implants, MIM ensures that medical devices are manufactured to exacting specifications, offering exceptional quality and reliability. The process is particularly suited for creating small, complex parts with tight tolerances, making it an ideal choice for high-performance medical applications.
- Biocompatibility and Durability: The materials used in metal injection molding medical, such as stainless steel, titanium alloys, and cobalt-chromium, are specifically chosen for their biocompatibility and durability. These materials are well-suited for medical devices that need to withstand the harsh conditions of the human body, such as implants or surgical tools that require long-lasting performance and resistance to corrosion.
Benefits of MIM in Terms of Precision, Material Efficiency, and Adaptability
- Precision: One of the key benefits of metal injection molding medical is its ability to produce parts with high precision, even with complex geometries. Unlike traditional metalworking methods, MIM allows for intricate details to be molded directly into the part, reducing the need for additional machining. This ensures consistency and accuracy across large batches of components, which is critical in the medical field.
- Material Efficiency: MIM is highly efficient in terms of material usage. Since metal feedstock is combined with binders and injected into a mold, waste is minimized, making it a cost-effective and sustainable option for producing medical devices. The ability to utilize fine-powdered metal in MIM also allows manufacturers to use a variety of alloys that would be difficult to process with other methods, leading to enhanced properties in the final part.
- Adaptability to Complex Designs: Metal injection molding medical offers great flexibility in terms of design. The process enables manufacturers to create complex shapes and structures that are not possible with other manufacturing methods, such as die casting or stamping. This adaptability is crucial in the development of customized medical devices, where precision, functionality, and patient-specific needs are key considerations.
Metal injection molding medical plays a pivotal role in the production of high-quality, durable, and precise medical devices. Its ability to deliver complex designs with high material efficiency and precision makes it a crucial method for meeting the ever-evolving demands of the medical industry. As medical technologies continue to advance, MIM will remain a cornerstone in the manufacturing of next-generation medical devices.
Accuracy of Metal Injection Molding Medical: A Detailed Exploration
Metal Injection Molding (MIM) is rapidly gaining prominence in the medical device industry due to its ability to produce complex, precise, and biocompatible parts at a high scale. Accuracy is a critical factor when it comes to the manufacturing of medical device components, as they must meet exact specifications to ensure optimal functionality, patient safety, and regulatory compliance. The MIM process allows for the production of components that have both intricate geometries and high dimensional precision, making it an ideal solution for the medical field. This comprehensive exploration will delve into the multiple aspects that contribute to the accuracy of metal injection molding medical, examining the process, its benefits, and the technologies that ensure its precision.
Precision in Part Design and Complexity
One of the key aspects that contribute to the accuracy of metal injection molding medical is its ability to handle highly complex and intricate part designs with great precision. The MIM process uses fine powdered metal, which is molded into shapes under high pressure. This process enables the creation of intricate geometries that might be difficult or impossible to achieve using traditional manufacturing methods such as machining or casting.
Medical devices often require components with fine features, undercuts, internal cavities, or thin-walled structures that cannot be easily fabricated with conventional techniques. MIM excels at producing these challenging designs, including delicate, small-scale parts like surgical instruments, connectors, and implants. The molding process itself ensures that each part holds consistent dimensions even for complex shapes, offering a higher level of flexibility in the design phase while maintaining accuracy in the final product. Thus, metal injection molding medical proves to be an excellent solution for producing parts with the necessary design intricacies required by medical applications.
Tight Tolerances and Consistency
The consistency and repeatability of part dimensions are paramount in medical device production. Small deviations in part size or shape can lead to device malfunction, safety risks, or failures. Metal injection molding medical addresses this challenge by offering exceptional precision, particularly in maintaining tight tolerances that meet the stringent requirements set by regulatory bodies such as the FDA.
MIM parts can be produced with tolerances as low as ±0.1mm, ensuring that each component adheres to exact measurements. This is achieved by the combination of high-quality metal feedstocks, advanced molding techniques, and precise equipment used throughout the production process. In addition, MIM processes are highly automated, reducing the likelihood of human error and increasing the consistency of the parts produced across multiple production runs.
The consistency of MIM also extends to mass production, where thousands of identical medical components can be produced with uniform quality. This makes MIM an attractive choice for manufacturers needing large quantities of medical device parts without sacrificing accuracy, repeatability, or quality.
Material Control and Biocompatibility
In the medical device industry, ensuring that parts are biocompatible is of utmost importance. Metal injection molding medical allows manufacturers to have precise control over the material composition of the parts, which contributes to both accuracy and safety. The feedstocks used in the MIM process consist of metal powders combined with binders, and the sintering stage fuses the particles together to create a dense, solid part.
By selecting specific alloys or blends of metal powders, manufacturers can tailor the material properties of the final parts to meet the specific requirements of medical devices. For example, MIM can be used with materials like stainless steel, titanium, or cobalt-chromium alloys, which offer the desired combination of strength, corrosion resistance, and biocompatibility. This precise material control ensures that the final parts not only meet the dimensional requirements but also perform safely in medical applications, such as implants, surgical instruments, or diagnostic devices.
Furthermore, MIM enables a homogeneous material distribution across the part, which ensures that the mechanical properties are consistent throughout. This is particularly important for ensuring the reliability and durability of the parts in demanding medical environments.
Advanced Post-Processing for Enhanced Precision
While metal injection molding medical provides high accuracy during the initial molding and sintering phases, additional post-processing techniques can further enhance the precision of the parts. These post-processing methods include surface finishing, machining, heat treatment, and more, and they allow manufacturers to fine-tune the final part dimensions and surface quality.
Post-processing steps like precision machining can be used to remove any residual binder material left after the sintering phase, ensuring that the part has a smooth, accurate surface finish. Heat treatment can further refine the material properties, such as improving hardness or tensile strength, which may be required for certain medical applications. These post-processing techniques contribute to the overall accuracy of the part, helping it meet the tight standards necessary for medical devices.
Moreover, advanced technologies like 3D scanning and computer-controlled machining can be employed during post-processing to ensure that every part is measured, checked, and verified to meet the exact specifications, minimizing the risk of defects and ensuring high-quality outcomes for mass production.
Metal injection molding medical is an innovative and highly accurate manufacturing method that plays a crucial role in the production of complex, biocompatible components for the medical device industry. By combining precise molding capabilities, tight tolerances, material control, and post-processing techniques, MIM delivers accuracy that meets the rigorous demands of medical device manufacturing. The technology’s ability to create detailed, reliable parts at scale, while maintaining high consistency, makes it an ideal solution for producing the next generation of medical devices.
Key Considerations for Wholesale Metal Injection Molding Medical Components
Metal Injection Molding (MIM) is a highly effective manufacturing method for producing complex, high-precision medical components in bulk. Due to the stringent requirements of the medical industry, wholesale MIM medical production must adhere to strict quality, material, regulatory, and cost considerations. This guide outlines the critical aspects to ensure successful wholesale production of metal injection molding medical parts.
Material Selection and Biocompatibility
The choice of material is a fundamental factor in MIM medical component production. Medical-grade metals must be selected to ensure biocompatibility, durability, and resistance to corrosion.
- Biocompatibility Standards: Materials should comply with ISO 10993 for biocompatibility and FDA regulations for medical use.
- Commonly Used Metals: Stainless steel (316L), titanium, and cobalt-chrome alloys are widely used for their strength and corrosion resistance.
- Surface Treatments: Additional coatings or treatments may be required to enhance biocompatibility and prevent adverse reactions in the human body.
Precision and Design Complexity
Metal injection molding allows for intricate geometries and miniaturized components, making it ideal for medical applications. However, design precision is crucial for functionality and safety.
- Tight Tolerances: Medical devices often require tolerances as low as ±0.01 mm to ensure accurate assembly and function.
- Thin-Walled and Complex Shapes: MIM enables the production of detailed, lightweight components, reducing material waste.
- Post-Processing Considerations: Secondary operations such as machining, polishing, and deburring may be necessary to achieve final specifications.
Regulatory Compliance and Certification
Medical components are subject to rigorous regulatory approvals to ensure safety and effectiveness. Compliance with industry standards is mandatory.
- FDA and ISO 13485 Certification: Manufacturers must follow medical device regulations, including Good Manufacturing Practices (GMP).
- Validation and Documentation: Process validation, material traceability, and detailed documentation are required for regulatory approval.
- Sterilization Compatibility: MIM parts should be designed to withstand common sterilization methods like autoclaving and gamma radiation.
Production Efficiency and Cost Control
While MIM is cost-effective for large-scale production, several factors influence overall efficiency and pricing.
- Batch Production Optimization: Large-volume production reduces per-unit costs but requires careful planning to maintain consistency.
- Tooling and Mold Costs: Initial tooling investments can be high, but long-term savings are achieved through mass production.
- Waste Reduction and Recycling: MIM minimizes material waste, but scrap management and recycling strategies can further improve cost-effectiveness.
Supplier Selection and Quality Assurance
Choosing a reliable supplier is crucial for maintaining consistent quality in wholesale metal injection molding medical parts.
- Experience in Medical MIM: Partnering with manufacturers specializing in medical-grade MIM ensures expertise in compliance and quality control.
- In-House vs. Outsourced Production: Assessing whether a supplier has in-house capabilities for tooling, sintering, and finishing affects lead time and quality assurance.
- Quality Control Measures: Advanced inspection techniques, including X-ray scanning and 3D metrology, ensure defect-free products.
Wholesale metal injection molding medical manufacturing requires a strategic approach to ensure high-quality, compliant, and cost-effective production. By focusing on material selection, precision engineering, regulatory adherence, production efficiency, and supplier reliability, manufacturers can successfully meet the demands of the medical industry while maintaining competitive pricing.
Difference Between Metal Injection Molding and Plastic Injection Molding in the Medical Device Industry
In the medical device industry, the manufacturing of components requires precision, reliability, and high performance. Two popular methods used for producing parts are Metal Injection Molding (MIM) and Plastic Injection Molding (PIM). While both processes share similarities in their basic principles—injecting material into molds to form parts—there are significant differences in the materials used, their applications, and the resulting part properties. This comparison will explore the distinctions between Metal Injection Molding and Plastic Injection Molding medical, covering various aspects such as material composition, design flexibility, performance characteristics, and cost considerations.
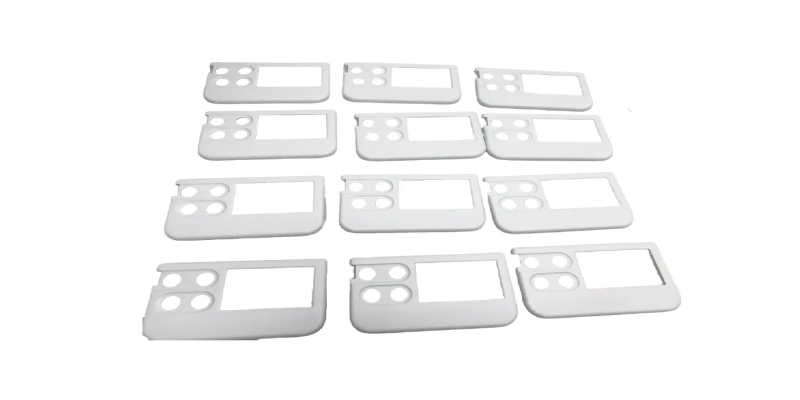
Material Composition and Properties
The first and most fundamental difference between Metal Injection Molding and Plastic Injection Molding medical lies in the materials used. MIM uses powdered metals mixed with binders to form parts, while PIM uses thermoplastic polymers or resins. The material properties of these two methods result in significant differences in the performance and functionality of the parts produced.
Metal Injection Molding medical is used to create parts from materials such as stainless steel, titanium, and cobalt-chromium alloys, which are known for their strength, durability, corrosion resistance, and biocompatibility. These properties make MIM ideal for producing components like surgical instruments, implants, and other devices that require high mechanical strength, resistance to wear, and safety for prolonged contact with human tissues.
On the other hand, Plastic Injection Molding medical uses materials like polypropylene, polyethylene, and polystyrene. These materials are lighter, more flexible, and generally less expensive than metals but lack the mechanical strength and heat resistance that metals provide. Plastic components are often used for disposable medical devices, housings, and parts that do not require high load-bearing capacity.
Design Flexibility and Complexity
Another major difference between Metal Injection Molding and Plastic Injection Molding medical is the ability to design complex geometries. Both processes can produce intricate parts, but MIM allows for more complex shapes and fine details due to its use of metal powders.
Metal Injection Molding medical is well-suited for producing parts with highly detailed, small-scale features, such as thin walls, tiny holes, and complex internal structures. This is because metal powders can be injected into molds with high precision, and the resulting sintering process helps retain the integrity of these delicate shapes. MIM can also accommodate designs that require high dimensional accuracy and tight tolerances, which is critical for medical applications where small variations can have significant consequences.
Plastic Injection Molding, while versatile and capable of producing a wide variety of shapes, has limitations when it comes to achieving the same level of detail as MIM. Plastics typically do not maintain the same precision as metals, especially when it comes to very fine features. However, plastic molding excels in producing parts with simpler geometries or parts that require flexibility or ease of assembly.
Mechanical Properties and Durability
When comparing the mechanical properties of the two methods, Metal Injection Molding medical produces components that are significantly stronger and more durable than those produced by Plastic Injection Molding. This is due to the inherent strength of the metals used in MIM.
MIM parts offer superior tensile strength, hardness, and wear resistance, making them ideal for medical devices that need to withstand high stresses, corrosion, and repeated use. Components like orthopedic implants, dental instruments, and surgical tools benefit from these enhanced mechanical properties. Metal components also maintain their shape and function at high temperatures, making them suitable for medical devices that are exposed to heat or harsh environments.
In contrast, Plastic Injection Molding parts are generally not as strong or resistant to wear and high temperatures as metal parts. Plastics are more prone to deformation under stress and may degrade over time when exposed to chemicals, UV light, or high temperatures. While this makes them less suitable for critical, load-bearing applications, plastic components are commonly used for medical devices that require lower strength and where disposability or flexibility is more important.
Cost and Production Considerations
Cost is often a key factor when choosing between Metal Injection Molding and Plastic Injection Molding medical, as both methods have distinct cost implications. The overall cost of manufacturing parts using MIM tends to be higher than that of PIM due to the higher cost of materials (such as metals) and the more complex production process.
Metal Injection Molding involves additional steps, such as mixing powdered metal with binders, molding, binder removal, and sintering. The sintering process requires high temperatures and extended processing times, adding to the production costs. However, MIM is cost-effective for high-volume production of complex metal parts, as it reduces the need for expensive machining or other post-processing steps.
Plastic Injection Molding, on the other hand, is generally less expensive than MIM due to the lower cost of raw materials and the quicker, simpler manufacturing process. It also requires fewer steps—plastic pellets are melted and injected into molds, and parts are typically ready for use after cooling. PIM is therefore a more affordable option for high-volume production of plastic components, especially when material properties like flexibility or light weight are desired.
Applications in the Medical Device Industry
The choice between Metal Injection Molding and Plastic Injection Molding medical depends largely on the specific requirements of the medical device being manufactured. MIM is commonly used for high-performance components that require durability, biocompatibility, and complex designs. Examples of MIM applications in the medical industry include orthopedic implants, surgical tools, dental devices, and components for diagnostic equipment.
Plastic Injection Molding is typically used for disposable, lower-cost medical devices, such as syringes, IV components, surgical drapes, and diagnostic kits. Plastics are also commonly used for housings, connectors, and components that need to be lightweight and easy to handle.
Both Metal Injection Molding and Plastic Injection Molding medical offer unique advantages depending on the materials, design complexities, and performance characteristics required for a specific medical device. MIM provides superior strength, durability, and precision for complex metal parts, making it ideal for critical medical components. In contrast, PIM offers lower-cost solutions for disposable, lightweight, and flexible components. Understanding these differences is crucial for manufacturers when selecting the most appropriate method for producing high-quality medical device components.
FAQs about Metal Injection Molding Medical
Medical injection molding is a specialized manufacturing process used to produce high-precision, high-quality components for the medical industry. This technique involves injecting molten plastic or metal material into a mold to form the desired shape of medical parts. The molds are designed with extreme precision to meet the stringent requirements of medical devices, such as surgical instruments, implants, and diagnostic tools. This process ensures that the final product adheres to strict medical standards for safety, reliability, and performance. Medical injection molding can be used for producing both small and large quantities of medical components, making it a versatile solution for medical manufacturers. The key advantage of this method is the ability to create complex and intricate parts with high consistency, making it ideal for applications where precision is crucial.
Metal injection molding (MIM) is a process that combines the precision of plastic injection molding with the strength of metal materials. In MIM, finely powdered metal is mixed with a binder material to form a feedstock that is injected into a mold cavity at high pressure. Once the part is molded, the binder is removed, and the metal part is sintered at a high temperature, resulting in a dense and durable metal component. MIM is used to create complex metal parts with high precision and tight tolerances, making it an excellent choice for medical, automotive, and electronics applications. Some of the most common metals used in MIM include stainless steel, titanium alloys, and cobalt-chromium, which are chosen for their strength, corrosion resistance, and biocompatibility—properties that are especially important in medical device manufacturing. MIM is an ideal method for producing small to medium-sized parts that require fine details and high-performance characteristics.
Yes, injection molding can be used for metals, but it is typically done in the form of metal injection molding (MIM). Unlike traditional plastic injection molding, MIM uses a metal powder mixed with a binder to form the feedstock, which is then injected into molds under high pressure. After molding, the binder is removed, and the metal part is sintered in a furnace to create a solid metal component. This process allows manufacturers to create intricate and complex metal parts that would be difficult to produce with traditional machining or casting methods. MIM is particularly beneficial for producing small metal components with high precision and tight tolerances. It is widely used in industries such as medical device manufacturing, automotive, aerospace, and electronics, where metal parts need to meet rigorous performance, durability, and safety standards.
Yes, injection molding over metal is possible and is often used in a process called overmolding. Overmolding involves injecting a material (typically plastic or elastomer) over a pre-existing metal part to form a composite component with unique properties. This technique is commonly used to enhance the functionality, ergonomics, or durability of metal parts. For example, a metal tool handle might be overmolded with a plastic or rubber coating to improve grip and comfort. The overmolding process can also improve the corrosion resistance or insulation properties of the metal. However, for injection molding to adhere properly to metal, certain conditions must be met, such as ensuring proper surface preparation of the metal, which may include cleaning, priming, or applying a bonding agent. Overmolding is particularly useful in medical device manufacturing, where the combination of metal strength and plastic flexibility is often required.
Metal injection molding (MIM) medical can be highly profitable, particularly for manufacturers producing high volumes of complex parts. The efficiency and scalability of the process allow for large batches of parts to be produced with minimal manual labor, which significantly reduces production costs in the long term. The ability to produce intricate parts with minimal post-processing further enhances profitability. MIM is especially cost-effective for medical device manufacturers when creating components like implants, surgical instruments, and other small, high-precision parts. However, the initial investment in equipment and setup can be substantial, making it more profitable for businesses that produce parts in large quantities. When optimized for high-volume production, MIM ensures that unit costs decrease, making it an economically viable option for mass-producing medical components. Thus, MIM medical processes offer high profitability once the scale is achieved and production stabilizes.
In general, Metal Injection Molding (MIM) is more cost-effective than CNC machining for the production of complex, small metal parts. CNC machining is a subtractive process, which involves cutting away material from a solid block of metal, leading to higher material costs and longer production times. On the other hand, MIM involves injecting metal powder into molds, resulting in minimal waste and faster cycle times. While CNC is more suited for low-volume, highly detailed parts, MIM is more economical for high-volume production, particularly in industries like medical devices. MIM’s ability to produce intricate shapes without the need for extensive machining makes it a more affordable option for mass production of medical parts, such as implants, surgical instruments, and connectors. Therefore, for high-volume manufacturing, MIM is typically cheaper than CNC machining.
Injection molding and casting are distinct processes, though both are used to produce parts by shaping materials. In Metal Injection Molding (MIM) medical, powdered metal is mixed with binders, injected into a mold under high pressure, and then sintered to create a solid part. The process is precise and ideal for creating small, intricate parts with high accuracy. Casting, on the other hand, typically involves pouring liquid metal into a mold and allowing it to cool and solidify. Casting is more commonly used for larger parts and those requiring a simple design. While both methods are used in manufacturing, MIM offers superior accuracy, complex geometries, and consistency, making it ideal for high-precision medical components. MIM is better suited for mass production of small parts, whereas casting is generally more appropriate for larger, simpler designs.
The cost of Metal Injection Molding (MIM) medical can vary depending on the volume of parts produced and the complexity of the design. For high-volume production, MIM is often a more cost-effective solution compared to other manufacturing methods like CNC machining. However, the initial setup costs for MIM, including mold creation and equipment, can be significant. For small production runs, the cost per part can be higher, making MIM less economical. But as the production scale increases, the per-unit cost decreases, making MIM an attractive option for manufacturers looking to mass-produce small, complex medical components. MIM is generally cheaper than traditional machining methods for high-volume manufacturing, but it can be more expensive for low volumes or highly specialized designs. Thus, MIM is most economical for large-scale production of medical device parts.
Metal Injection Molding (MIM) is considered a relatively sustainable manufacturing process, particularly for medical device production. MIM reduces material waste by using metal powders that can be precisely injected into molds with minimal excess material. The process also has lower energy consumption compared to other methods like CNC machining, which requires substantial energy for cutting and shaping metal blocks. Additionally, MIM allows for the use of biocompatible metals, such as titanium and stainless steel, that are recyclable and suitable for medical applications. While there is still some waste generated during binder removal and sintering, the overall efficiency and lower environmental impact of MIM make it a more sustainable option for producing high-precision medical parts compared to other manufacturing methods. Therefore, MIM is a sustainable choice for creating complex, durable, and biocompatible parts in the medical industry.
Pros of Metal Injection Molding (MIM) in medical applications:
Precision and Complexity: MIM allows for the production of small, intricate parts with high accuracy and complex geometries, ideal for medical devices such as implants and surgical tools.
Scalability: The process is highly scalable, making it ideal for mass production, resulting in lower per-unit costs as production volume increases.
Reduced Waste: Unlike machining, MIM generates minimal waste, making it a more sustainable manufacturing method.
Material Flexibility: MIM allows for a variety of metal materials that can be tailored to meet the specific performance and biocompatibility requirements of medical devices.
Cons of Metal Injection Molding:
High Initial Setup Cost: MIM requires significant investment in molds, equipment, and setup, making it less cost-effective for small production runs.
Complexity in Binder Removal: The process of removing the binder can be time-consuming and may require additional equipment.
The two common types of injection molding processes used in manufacturing are Metal Injection Molding (MIM) and Plastic Injection Molding (PIM). MIM is typically used for producing complex metal parts, such as those needed in medical devices, while PIM is used for producing plastic components. Both methods involve injecting material into a mold under high pressure to form parts, but MIM involves powdered metals mixed with binders, which are later sintered to create solid metal parts. In contrast, PIM uses molten plastic materials, which are cooled and solidified to form the desired part. MIM is ideal for producing small, high-precision medical components, while PIM is used for less complex plastic parts such as housings, connectors, or disposable medical devices.
In dentistry, injection molding is used to produce dental components such as crowns, bridges, and dental implants. Metal Injection Molding (MIM) is used for creating dental implants from biocompatible metals, such as titanium, which are used for long-term implantation in the jaw. The process allows for precise shaping of the parts with fine details, ensuring a perfect fit for patients. For crowns and bridges, Plastic Injection Molding (PIM) can be used to produce components made of dental resins or polymers. Injection molding is particularly useful in dental applications for its ability to create highly accurate, reproducible parts at a lower cost compared to traditional methods. It also allows for mass production of dental components, which helps reduce costs and improve accessibility to dental treatments.
The key difference between CNC machining and Metal Injection Molding (MIM) lies in the process and material efficiency. CNC (Computer Numerical Control) machining is a subtractive process that cuts and shapes a solid metal block into the desired shape, using precise cutting tools. CNC is ideal for low-volume, high-precision parts where intricate detailing is needed, but it can be slow and expensive due to the material waste and the labor-intensive process.
Metal Injection Molding (MIM), on the other hand, is a formative process where metal powder is injected into molds and then sintered to form solid parts. MIM is more suitable for high-volume production, where large quantities of small, complex metal components are needed. While CNC is more expensive for mass production, MIM is more cost-effective for producing high-precision parts at scale. MIM is also better suited for parts that have intricate shapes, reducing the need for post-production machining.
Injection molding is a specific type of molding process where material (plastic, metal, or other materials) is injected into a mold under high pressure to create a part. Molding, more broadly, refers to any process where material is shaped into a desired form by placing it in a mold and applying heat or pressure. Molding can include techniques such as compression molding, blow molding, and rotational molding, which are used for different materials and applications. In the case of Metal Injection Molding (MIM), the process involves powdered metal, which is injected into molds and then sintered, creating parts for industries such as medical devices. The main difference is that injection molding specifically involves injecting material under pressure, while molding can refer to a broader range of shaping processes.
Metal casting and metal molding are both processes used to shape metal parts, but they differ in their methods and materials. Metal casting involves pouring molten metal into a mold to create parts. This process is typically used for larger parts and can handle metals with high melting points. Casting is suitable for parts that don’t require intricate shapes or fine precision. In contrast, metal injection molding (MIM) uses metal powders mixed with binders, which are injected into molds under high pressure to create intricate, small, and precise components. MIM is ideal for producing high-precision medical devices such as implants and surgical tools, while casting is often used for bulkier parts like engine blocks. MIM generally produces more complex parts and has finer tolerances compared to casting.
Metal Injection Molding (MIM) and forging are both used to manufacture metal parts, but they operate on different principles. MIM is a process that involves mixing metal powders with binders, injecting the mixture into molds, and then sintering to form solid parts. MIM is ideal for producing complex, small parts with high precision, such as those used in medical devices. It allows for intricate geometries and minimal waste. Forging, on the other hand, involves shaping metal by applying compressive forces, usually at high temperatures, to a metal billet. This results in strong, durable parts but is best suited for simpler shapes and larger components. Forging is commonly used for parts subjected to high stress and where strength is critical. In medical device manufacturing, MIM is often chosen for its ability to produce intricate, high-precision parts, while forging is used for larger, robust components.
Powder injection molding (PIM) is a broader category that includes both metal injection molding (MIM) and ceramic injection molding (CIM). MIM specifically refers to the use of metal powders mixed with binders, injected into molds, and then sintered to create parts. It is commonly used in the medical industry for producing complex, small, high-precision components like implants and surgical instruments. Powder injection molding, in general, involves using fine powders of various materials (metals, ceramics, etc.) and is used for creating parts in a variety of industries. While MIM focuses on metals, CIM uses ceramic powders for applications requiring heat resistance and hardness. Both processes share similar principles but differ in material usage and applications. MIM is primarily used in medical devices, whereas powder injection molding can be applied to a wider range of industries.
The future of injection molding, including Metal Injection Molding (MIM), looks promising with advances in materials, technology, and automation. As industries demand higher precision, smaller components, and complex geometries, injection molding techniques will evolve to meet these needs. Innovations in 3D printing and smart manufacturing will likely enhance the molding process, allowing for greater design flexibility and faster production cycles. Sustainability will also play a major role, as manufacturers focus on reducing waste and energy consumption, and adopting environmentally friendly materials. In the medical field, the demand for more biocompatible, reliable, and durable components will drive further growth in MIM. Furthermore, automation and improved quality control will make injection molding more cost-effective, even for low-volume production runs. Overall, injection molding will continue to be an essential manufacturing method, with ongoing improvements in efficiency, precision, and sustainability.
The future of Metal Injection Molding (MIM) is bright, especially in the medical device sector. With the increasing demand for complex, small, high-precision components, MIM is poised for continued growth. The process offers distinct advantages, such as the ability to create parts with intricate geometries and high tolerance without requiring expensive post-machining. As the technology evolves, improvements in binder systems, sintering techniques, and material quality will increase the overall efficiency and scalability of MIM. Additionally, the rise of biocompatible materials and innovations in 3D printing will allow MIM to be used for even more advanced medical applications. The growing emphasis on miniaturization in medical devices, such as implants and surgical tools, will drive MIM’s adoption. The future will also likely see enhanced automation and sustainability, further improving MIM’s economic and environmental viability in the medical industry.
The most common raw materials for Metal Injection Molding (MIM) in the medical industry are metal powders combined with binders. These metal powders are typically stainless steel, titanium alloys, cobalt-chromium, and nickel alloys, depending on the application and required properties. Stainless steel, for example, is commonly used for implants, surgical instruments, and dental devices due to its strength, durability, and biocompatibility. Titanium alloys are favored for their lightweight and excellent corrosion resistance, making them ideal for orthopedic implants. Cobalt-chromium is used in parts requiring high wear resistance, such as dental implants. The binder system in MIM plays a critical role in holding the metal powder together during injection and molding before the part undergoes sintering to remove the binder and solidify the metal. These raw materials offer a range of mechanical properties tailored to medical applications.
The best country for Metal Injection Molding (MIM) largely depends on factors such as manufacturing capabilities, labor costs, and access to high-quality raw materials. Countries with advanced manufacturing infrastructure and access to a highly skilled workforce, such as Germany, Japan, and the United States, are leading in injection molding, especially for the medical device industry. Germany, for example, is known for its precision manufacturing and engineering expertise, making it a prime location for producing high-precision medical components. China and India have also become strong players in injection molding, primarily due to their cost-effective manufacturing and large-scale production capabilities. For MIM specifically, the United States and Europe are at the forefront of technological advancements, material development, and production for medical devices, where stringent quality control and regulatory standards are crucial.
The injection molding of metal powders, specifically Metal Injection Molding (MIM), has become an important process due to its ability to produce high-precision, complex parts at a lower cost than traditional methods like CNC machining and casting. The process is ideal for creating intricate, small components made from durable materials, such as those used in the medical device industry. MIM allows for high material utilization and reduces waste, making it more sustainable compared to other metalworking techniques. It also enables the mass production of parts with complex shapes that would be challenging or impossible to achieve with traditional forging or casting. With its ability to handle a wide range of metals, MIM offers flexibility in material choices, such as stainless steel, titanium, and cobalt-chromium alloys, which are commonly used in medical devices. The ability to produce parts quickly and cost-effectively has made MIM a critical process in the manufacture of medical components.
Metal injection molding (MIM) is widely used in the medical industry to manufacture complex, high-precision components that require superior mechanical properties and biocompatibility. MIM is ideal for producing surgical instruments, orthopedic implants, dental devices, and minimally invasive surgical tools. It enables the creation of intricate geometries that would be difficult or costly to achieve with traditional machining. The process allows for mass production of small, lightweight parts while maintaining strict tolerances. Medical-grade materials such as stainless steel, titanium, and cobalt-chrome alloys are commonly used due to their corrosion resistance and durability. Additionally, MIM is used for implantable components that require high strength and compatibility with human tissue. The ability to manufacture near-net-shape components reduces material waste and post-processing requirements, making it a cost-effective solution for medical device manufacturers. As a result, MIM plays a crucial role in advancing medical technology and improving patient outcomes.
For metal injection molding (MIM) in the medical industry, manufacturers must meet stringent qualifications to ensure quality, safety, and regulatory compliance. Companies involved in MIM medical manufacturing should have ISO 13485 certification, which guarantees adherence to medical device quality management standards. Compliance with U.S. Food and Drug Administration (FDA) regulations is essential, as MIM components may be used in critical medical applications. Engineers and technicians working in MIM production require expertise in metallurgy, mold design, and process control to maintain precision and consistency. Experience in validation protocols, such as IQ, OQ, and PQ (Installation Qualification, Operational Qualification, and Performance Qualification), is necessary to meet regulatory standards. Manufacturers also need cleanroom facilities for medical-grade component production to prevent contamination. In addition, rigorous quality control measures, including X-ray inspection, metallographic analysis, and functional testing, are essential to ensure that each part meets the required medical industry standards.
Aluminum is not commonly used in metal injection molding (MIM) for medical applications due to its low sintering temperature and difficulty in maintaining high-density, high-strength properties through the MIM process. Unlike stainless steel, titanium, and cobalt-chrome alloys, aluminum has a lower melting point, which makes it challenging to sinter effectively without significant porosity. The medical industry requires materials with excellent biocompatibility, corrosion resistance, and mechanical strength, qualities that aluminum often lacks in comparison to other MIM-compatible metals. While aluminum can be processed using other manufacturing techniques, such as die casting or CNC machining, it is not an ideal candidate for MIM. For medical applications, stronger and more durable metals like titanium and stainless steel are preferred due to their ability to withstand sterilization, wear, and long-term use in surgical and implantable devices. Therefore, MIM is not a practical choice for manufacturing aluminum medical components.
Copper can be processed through metal injection molding (MIM), but its applications in the medical industry are limited. Copper’s high thermal and electrical conductivity makes it useful in specialized medical applications, such as electromagnetic shielding for medical devices or antimicrobial components. However, pure copper is difficult to sinter effectively due to its oxidation properties, which require controlled environments and special sintering techniques. In the medical field, copper alloys, such as copper-nickel or copper-titanium blends, may be used when biocompatibility and corrosion resistance are necessary. Additionally, antimicrobial properties of copper can be beneficial in medical equipment that requires high levels of hygiene. Despite these advantages, stainless steel and titanium remain the preferred materials for MIM medical applications due to their superior strength, durability, and compliance with medical regulations. When copper is required, alternative manufacturing methods, such as machining or casting, may be more effective than MIM.
Yes, steel can be processed through metal injection molding (MIM) and is one of the most commonly used materials for medical applications. Stainless steel, particularly 316L, is highly favored in the medical industry due to its excellent corrosion resistance, biocompatibility, and mechanical strength. MIM allows the production of complex, high-precision steel components that are used in surgical instruments, orthopedic implants, dental tools, and endoscopic devices. Unlike traditional machining or casting, MIM enables near-net-shape manufacturing, reducing material waste and allowing for intricate geometries that would be difficult to achieve otherwise. Stainless steel components produced through MIM can withstand sterilization methods such as autoclaving and chemical cleaning, making them ideal for repeated medical use. Additionally, MIM-produced steel parts can undergo secondary processes such as polishing, passivation, and coating to enhance their performance and longevity in medical environments. Therefore, steel is a highly viable and widely used material in MIM for medical applications.
The medical injection molding market is a rapidly growing sector, driven by advancements in healthcare technology, the increasing demand for minimally invasive procedures, and the rising need for high-precision medical components. In 2023, the global medical injection molding market was valued at approximately $20 billion, with projections indicating steady growth at a compound annual growth rate (CAGR) of around 6-8% over the next decade. Factors contributing to this growth include the rising adoption of plastic and metal injection molding for medical devices, the demand for cost-effective mass production, and stringent regulatory requirements for medical components. MIM, in particular, is gaining traction due to its ability to manufacture complex, high-strength metal parts for implants, surgical tools, and diagnostic equipment. The market is expected to expand further as new biocompatible materials and advanced manufacturing techniques emerge, solidifying MIM’s role in the future of medical device production.
The global metal injection molding (MIM) market was valued at approximately $3.5–4 billion in 2023 and is projected to grow at a CAGR of 7-10% over the next decade. The medical sector represents a significant portion of this market, driven by the need for precision-engineered, high-strength, and biocompatible metal components. The increasing demand for minimally invasive surgical instruments, orthopedic implants, and customized dental tools is fueling the adoption of MIM in medical manufacturing. Additionally, advancements in material science and process automation are making MIM a more attractive alternative to traditional manufacturing methods. While other industries, such as aerospace, automotive, and electronics, also contribute to the growth of MIM, the medical sector remains one of the most promising areas due to strict quality requirements and ongoing innovations in healthcare technology. As demand for personalized and high-performance medical devices rises, the MIM market is expected to expand further.
The entire metal injection molding (MIM) process, from design to final production, can take anywhere from four to twelve weeks, depending on complexity, material selection, and post-processing requirements. The MIM process consists of four key stages: feedstock preparation, injection molding, debinding, and sintering. The molding stage itself is quick, typically taking only a few seconds per part. However, debinding and sintering are time-intensive, often requiring 24 to 48 hours per batch to achieve full density and mechanical strength. Additional post-processing, such as polishing, coating, or sterilization, can extend the production timeline. For medical applications, regulatory validation and quality control inspections further add to lead times. Despite these steps, MIM remains one of the most efficient methods for mass-producing high-precision medical components. Manufacturers can optimize production schedules by implementing automated systems and parallel processing techniques to reduce overall turnaround time.
The cost of a steel injection mold for medical metal injection molding (MIM) varies significantly based on design complexity, part size, and tooling requirements. A high-precision MIM mold for medical components typically ranges from $10,000 to $100,000 or more. The initial tooling cost is high due to the need for precision engineering, durable mold materials, and fine-tuned cavity designs that ensure consistent part quality. Medical-grade MIM molds require specialized coatings, such as PVD or nitriding, to enhance durability and ensure compliance with industry standards. While the upfront cost is substantial, the per-unit production cost decreases significantly with higher volumes. Manufacturers often amortize mold costs over large production runs, making MIM cost-effective for mass-producing medical components. Factors like multi-cavity tooling and automation can further optimize costs, making MIM a viable solution for high-volume medical manufacturing.
The cost of injection molding for medical applications varies based on machine type, material, and production complexity. On average, metal injection molding (MIM) costs between $75 and $250 per hour, with larger, high-precision machines on the higher end of the spectrum. Additional factors, such as material selection, post-processing, and quality control, can influence overall costs. For medical-grade production, cleanroom environments and regulatory compliance further add to expenses. However, due to its efficiency and ability to produce complex medical components in bulk, MIM remains a cost-effective solution for high-volume medical manufacturing.
Contact our professional team now for a same-day quote and risk-free project evaluation. Benefit from ISO 8 cleanrooms, advanced machines, and 12-hour fast response in medical injection molding.