Plastic injection molding medical parts companies play a crucial role in the healthcare industry, providing essential components for medical devices. The precision offered by this manufacturing process ensures that even the most intricate designs meet stringent medical standards, which are critical for safety and efficacy. By utilizing medical molded plastics solutions, these companies can produce high-quality, durable parts efficiently, reducing waste and minimizing production costs.
Cost-effectiveness is another significant advantage, as plastic injection molding medical parts companies can produce large volumes of parts efficiently, reducing waste and minimizing production costs. This efficiency makes the technology ideal for both small and large-scale medical device production.
The versatility of plastic injection molding enables these companies to manufacture a wide range of components, from surgical instruments to diagnostic tools, meeting the diverse needs of modern healthcare. As medical technology advances, the demand for high-quality molded components continues to rise, underscoring the importance of these specialized manufacturers. Plastic injection molding medical parts companies ensure cost-effective, high-quality components, with FUJIU Medical excelling in precision and custom solutions.
Low-Volume to High-Volume Production Capabilities
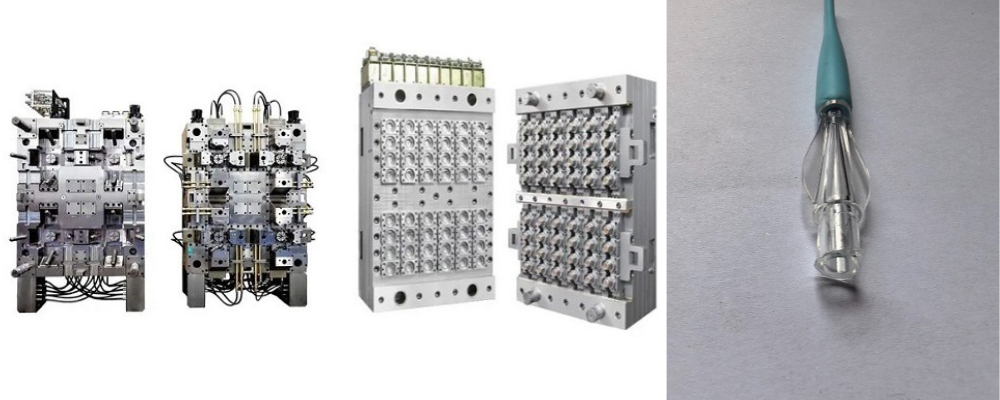
Attributes | Details |
---|---|
Place of Origin | Dongguan, Guangdong, China |
Brand Name | LY Medical Injection Mold |
Product Name | Medical Injection Mold |
Model Number | Custom |
Colors | Custom |
Size | Custom |
Weight | Custom |
Surface Finish | Texture/Sandy/MT/YS/SPI/EDM finish/smooth/glossy |
Tolerance | 0.02mm -0.05mm |
Drawing Format | STEP/STP/IGS/X-T/STL/CAD/PDF/DWG and Other |
Material Experience | ABS/PC/PP/Acetal/Acetron NS/Acrylic/Celcon/CPVC/Cycolca/Fluorosint |
Mold Life | 500000 shots |
Selling Units | Single item |
Supply Ability | 200 Piece/Pieces per Month |
What Are Plastic Injection Molding Medical Parts Companies?
Plastic injection molding medical parts companies specialize in manufacturing critical components for the medical industry using the process of plastic injection molding. These companies, including medical parts mold companies, combine advanced technology and precise techniques to meet the strict standards required for medical devices, ensuring safety, durability, and functionality. Plastic injection molding medical parts companies operate in one of the most demanding sectors, requiring extreme precision, compliance with strict regulations, and continuous innovation. To produce high-quality medical-grade plastic components, these companies must establish specialized manufacturing facilities, obtain essential certifications, and build a strong research and development (R&D) team.
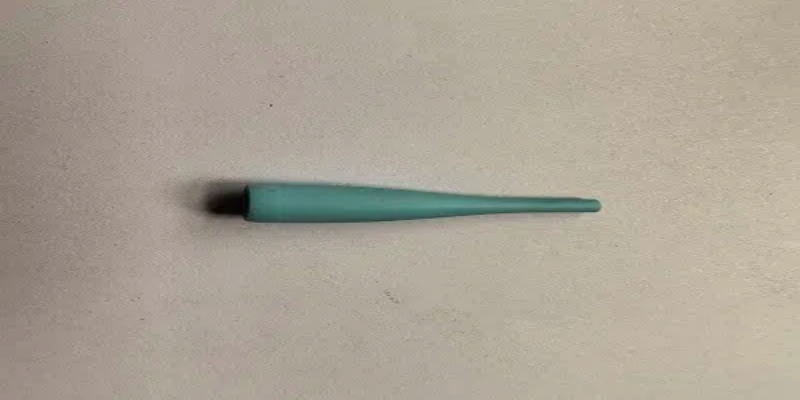
Advanced Manufacturing Facilities
Medical plastic injection molding requires highly controlled environments to produce defect-free, sterile, and biocompatible components. The facilities must be equipped with cutting-edge technology to meet the stringent requirements of the medical and pharmaceutical industries.
Cleanroom Manufacturing: Ensuring Sterility and Contamination Control
One of the most critical aspects of medical injection molding is maintaining a contamination-free environment. Many medical components, such as syringes, surgical instruments, and implantable devices, require production in a cleanroom setting to prevent bacterial contamination, dust particles, and other pollutants.
- ISO Class 7 and Class 8 Cleanrooms:
- Class 7 cleanrooms maintain fewer than 10,000 particles per cubic foot of air, ensuring a highly controlled production environment.
- Class 8 cleanrooms allow a slightly higher particle count but are still suitable for many medical applications.
- Air Filtration and Environmental Control:
- High-efficiency particulate air (HEPA) filters continuously remove airborne contaminants.
- Temperature and humidity control help maintain the integrity of sensitive plastic materials.
- Personnel and Hygiene Regulations:
- Employees wear sterilized gowns, gloves, and face masks to minimize contamination risks.
- Strict cleaning protocols ensure all equipment remains free from bacteria and foreign particles.
High-Precision Injection Molding Machines for Medical Applications
Unlike conventional plastic molding, medical injection molding demands extreme precision, as even microscopic defects can compromise patient safety. The latest injection molding machines integrate advanced features to meet these stringent requirements.
- Micro-Molding and Multi-Shot Injection:
- Enables the production of intricate medical components with tight tolerances (as small as ±0.001 inches).
- Multi-shot injection molding allows multiple materials to be combined into a single component, reducing assembly needs.
- Real-Time Process Monitoring:
- Sensors continuously measure variables like pressure, temperature, and cycle time.
- AI-driven automation ensures every part meets exact specifications, reducing waste and improving efficiency.
Post-Processing and Sterilization Capabilities
After molding, medical components often require sterilization and additional processing to ensure safety and compliance.
- Common Sterilization Methods:
- Gamma Radiation: Destroys bacteria and microorganisms without compromising plastic integrity.
- Ethylene Oxide (EtO) Sterilization: Used for heat-sensitive plastics like polypropylene (PP).
- Autoclave Steam Sterilization: Ideal for high-heat-resistant materials like polyetheretherketone (PEEK).
- Precision Machining and Finishing:
- CNC machining ensures final products meet dimensional accuracy.
- Surface treatments enhance durability, biocompatibility, and chemical resistance.
Industry Certifications and Regulatory Compliance
To manufacture safe and effective medical plastic components, companies must comply with global industry regulations. These certifications validate a company’s ability to meet stringent quality control and patient safety requirements.
ISO 13485: Medical Device Quality Management System
This internationally recognized certification ensures a company follows rigorous quality management practices tailored to the medical industry.
- Requirements Include:
- Risk management and traceability of all materials used in production.
- Strict documentation of manufacturing processes for auditing purposes.
- Regular internal audits and process validation to prevent defects.
FDA Registration and GMP Compliance
The U.S. Food and Drug Administration (FDA) regulates all medical devices and components to ensure patient safety.
- Key FDA Requirements:
- Registration under 21 CFR Part 820, which mandates compliance with Good Manufacturing Practices (GMP).
- Demonstration of product safety, effectiveness, and biocompatibility.
- Adherence to strict record-keeping and lot traceability requirements.
ISO 9001: Quality Management System
While not exclusive to the medical industry, ISO 9001 certification enhances a company’s operational efficiency and ensures products meet consistent quality standards.
- Benefits Include:
- Improved process control and reduced manufacturing defects.
- Standardized production methods for increased efficiency.
- Enhanced customer satisfaction and regulatory credibility.
ISO 10993: Biocompatibility Testing for Medical Plastics
Medical plastics must not cause adverse biological reactions when in contact with human tissue. ISO 10993 establishes guidelines for testing plastic materials for safety.
- Key Biocompatibility Tests:
- Cytotoxicity Testing: Ensures materials do not harm living cells.
- Sensitization & Irritation Tests: Verifies plastics do not cause allergic reactions or skin irritation.
- Extractables and Leachables Analysis: Examines whether any harmful chemicals migrate from the plastic into the body.
Research and Development Team: Driving Innovation and Compliance
A dedicated R&D team is essential for medical injection molding companies to stay competitive and meet evolving industry demands. These experts focus on material development, process optimization, and regulatory compliance.
Material Scientists and Biocompatibility Experts
Medical devices require specialized plastics with unique properties such as chemical resistance, heat stability, and biocompatibility.
- Common Medical Plastics Researched:
- Polyetheretherketone (PEEK) – Used in implants for its durability and biocompatibility.
- Polycarbonate (PC) – Transparent, impact-resistant material for surgical instruments.
- Liquid Silicone Rubber (LSR) – Flexible and ideal for medical tubing and prosthetics.
- Testing and Validation:
- Continuous research on new materials that improve patient safety and device performance.
- Development of antimicrobial plastics to reduce hospital-acquired infections.
Biomedical Engineers for Product Design and Development
A team of biomedical engineers collaborates with medical professionals to create cutting-edge device designs.
- Design Considerations Include:
- Minimizing material waste through optimized mold design.
- Enhancing ergonomics and functionality of medical devices.
- Ensuring compliance with FDA and ISO standards from the early design phase.
Process Optimization and Automation Experts
To enhance production efficiency and maintain cost-effectiveness, medical injection molding companies invest in process optimization.
- Key Responsibilities:
- Implementing AI-driven monitoring systems for real-time quality control.
- Reducing cycle times while maintaining precision through automation.
- Improving energy efficiency in manufacturing processes.
Regulatory Compliance Specialists
A dedicated team ensures that all products meet international safety and regulatory requirements.
- Responsibilities:
- Keeping up to date with changes in FDA, ISO, and EU MDR regulations.
- Preparing detailed documentation for audits and product approvals.
- Managing risk assessment strategies to prevent defects and recalls.
Plastic injection molding medical parts companies must integrate advanced manufacturing facilities, industry-recognized certifications, and an expert research team to maintain high standards. Cleanroom environments, high-precision molding machines, and sterilization capabilities ensure product safety. Certifications like ISO 13485, FDA compliance, and ISO 10993 validate quality assurance. Meanwhile, a strong R&D team, including material scientists, biomedical engineers, and regulatory specialists, drives innovation and ensures compliance. By excelling in these areas, companies can deliver cutting-edge medical devices while maintaining cost efficiency and regulatory adherence.
Medical Molding Definition and Basic Process
Plastic injection molding involves heating plastic material until it melts and then injecting it into precision-engineered molds. Once cooled, the material solidifies into a desired shape, forming components such as syringes, diagnostic tools, or surgical implants. Plastic injection molding medical parts companies use this process to create high-quality medical molding products with consistent accuracy, even for intricate designs.
Definition of Medical Injection Molding
Medical injection molding is a high-precision manufacturing technique used to produce medical-grade plastic parts through the injection of molten polymer into a mold cavity. The process is highly automated, repeatable, and capable of producing intricate designs with tight tolerances.
Key characteristics of medical injection molding include:
- Use of Biocompatible Materials – Complies with FDA, ISO 10993, and USP Class VI standards.
- Strict Quality and Regulatory Standards – Ensures products meet cleanroom manufacturing requirements and sterility guidelines.
- High-Volume Production Efficiency – Reduces unit costs while maintaining precision.
- Micro-Molding Capability – Allows for the production of miniature medical components with complex geometries.
Medical injection molding is used to manufacture a wide range of critical healthcare components, including syringes, IV connectors, prosthetic parts, surgical tools, and drug delivery devices.
Basic Process of Medical Injection Molding
Step 1: Product Design and Engineering
The first step in medical injection molding is designing the product, ensuring it meets functional, regulatory, and manufacturability requirements.
Key Aspects of Medical Part Design
- Material Selection – Engineers choose materials like PEEK, polycarbonate, polypropylene, and silicone based on biocompatibility, sterilization resistance, and mechanical strength.
- Dimensional Tolerances – Medical parts require extreme precision, often within microns, to function correctly in diagnostic and surgical applications.
- Regulatory Compliance – Designs must adhere to FDA guidelines, ISO 13485, and Good Manufacturing Practices (GMP) to ensure safety.
- Prototyping & Testing – Rapid prototyping (3D printing or CNC machining) is used to validate designs before full-scale production.
Medical injection molding companies collaborate with medical device manufacturers to optimize designs for both functionality and efficient molding.
Step 2: Mold Design and Manufacturing
Once the product design is finalized, the mold (tooling) is designed and fabricated. The mold is the most critical component in ensuring precision, repeatability, and efficiency in medical part production.
Mold Design Considerations
- Multi-Cavity Molds – Used for high-volume production to reduce cycle times.
- Micro-Molds – Designed for miniature medical components such as catheter tips, stents, and implantable devices.
- Cooling Systems – Ensures uniform temperature control to prevent defects and improve cycle efficiency.
- High-Quality Materials – Molds are typically made from hardened stainless steel for durability and precision.
After the mold is manufactured, rigorous testing is conducted, including mold flow analysis and trial runs to detect any potential defects before full-scale production begins.
Step 3: Injection Molding Process
With the mold ready, the actual injection molding process begins. This involves melting medical-grade plastic, injecting it into the mold, cooling, and ejecting the finished part.
Detailed Steps in the Injection Molding Process
- Material Preparation – The selected medical-grade polymer is fed into the injection molding machine’s hopper.
- Melting & Injection – The material is heated to a specific temperature and injected into the mold cavity under high pressure.
- Cooling & Solidification – The molten plastic rapidly cools and solidifies into the exact shape of the mold.
- Ejection – The mold opens, and the finished part is removed using ejector pins.
- Inspection & Trimming – The part is examined for defects, and any excess material (flash) is trimmed.
The entire cycle can take seconds to minutes, depending on the complexity and material properties. Advanced cleanroom injection molding ensures that parts are produced in a sterile environment, meeting the highest medical standards.
Step 4: Post-Molding Processing and Sterilization
After molding, medical plastic parts undergo post-processing and sterilization to ensure they meet strict medical safety standards.
Common Post-Molding Steps
- Surface Finishing – Includes polishing, coating, or texturing to enhance performance and aesthetics.
- Assembly & Bonding – Some parts require welding, gluing, or mechanical assembly.
- Quality Inspection – Uses automated vision systems, dimensional measurement, and functional testing to ensure compliance.
- Sterilization – Medical components undergo autoclaving, gamma radiation, ethylene oxide (EtO) gas, or UV sterilization to eliminate contamination.
At this stage, defective or non-conforming parts are removed, ensuring that only flawless medical components are delivered to customers.
Step 5: Packaging and Distribution
Once the medical plastic parts pass quality control, they are packaged and prepared for shipment.
Packaging Considerations for Medical Parts
- Sterile Packaging – Parts that require sterility are sealed in medical-grade pouches or blister packs.
- Labeling & Compliance – Packaging includes lot numbers, expiration dates, and regulatory compliance details.
- Temperature & Contamination Control – Some components need temperature-controlled storage to maintain integrity.
The final products are shipped to hospitals, laboratories, medical device manufacturers, and distributors worldwide, ready for use in life-saving applications.
Plastic injection molding medical parts companies play a crucial role in the healthcare industry, producing high-precision, biocompatible, and cost-effective medical components. The end-to-end process, from design to molding and packaging, follows strict regulatory and quality control measures to ensure safety, durability, and sterility.
With advancements in automation, micro-molding, and sustainable materials, the future of medical injection molding continues to evolve, meeting the ever-growing demands of modern healthcare.
Common Materials Used in Medical Molding
Plastic injection molding medical parts companies rely on specific materials known for their biocompatibility and durability:
Polycarbonate: Strength and Optical Clarity
Polycarbonate is a versatile, transparent thermoplastic that is widely used in medical molding due to its excellent strength and optical clarity. This material is ideal for medical components that require visibility and durability, such as diagnostic devices, optical lenses, and protective housings for electronic medical equipment. Polycarbonate is not only known for its strength but also its impact resistance, making it suitable for applications that demand both transparency and the ability to withstand mechanical stress. In addition to its durability, polycarbonate can be sterilized using common medical sterilization techniques, making it a reliable choice for critical medical applications.
Silicone: Flexibility and Temperature Resistance
Silicone is a highly flexible material often used in medical molding for components requiring resilience, elasticity, and resistance to temperature changes. Medical grade silicone for molding is specifically designed to meet the rigorous standards of the healthcare industry, ensuring both safety and durability in critical medical applications. It is commonly used in items such as catheters, seals, and gaskets, where flexibility and biocompatibility are essential. Silicone maintains its performance across a broad temperature range—from extreme cold to high heat—making it ideal for medical devices that undergo frequent sterilization or need to endure fluctuating environmental conditions. Additionally, its hypoallergenic properties make it a safe choice for implants and devices in direct contact with sensitive tissues.
Polypropylene: Lightweight and Durable
Polypropylene is a lightweight, impact-resistant material often used for disposable medical supplies. It is highly resistant to chemicals and fatigue, making it suitable for a wide range of applications, including syringes, medical trays, and packaging for sterile products. One of the key benefits of polypropylene is its ability to withstand multiple sterilization cycles without degrading, which is essential for maintaining the integrity of disposable devices. Its lightweight nature also contributes to the ease of handling and cost-effectiveness in large-scale production, making it an attractive choice for manufacturers of single-use medical devices. Additionally, polypropylene is a commonly used material for medical devices class 2 injection molding parts due to its durability and biocompatibility.
Medical-Grade Plastics: Sterility and Biocompatibility
Medical-grade plastics are specifically engineered to meet the rigorous requirements of medical device manufacturing. These plastics are designed to be biocompatible, meaning they can safely interact with human tissues without causing adverse reactions. Materials such as medical-grade polyethylene, polycarbonate, and polyvinyl chloride (PVC) are commonly used in implants, surgical tools, and other devices that require direct contact with the body. These materials are also capable of maintaining sterility and can be safely sterilized using methods such as autoclaving or chemical sterilization. The biocompatibility and sterility of medical-grade plastics make them essential in ensuring the safety and functionality of critical medical devices.
Polysulfone: High Thermal Stability and Chemical Resistance
Polysulfone is a high-performance thermoplastic known for its exceptional thermal stability and resistance to chemicals, making it ideal for medical devices that need to withstand harsh sterilization procedures. This material is commonly used for components such as diagnostic equipment, filters, and fluid-handling devices, often produced through thermoplastic injection molding medical. Polysulfone can endure high temperatures and exposure to corrosive chemicals without losing its structural integrity, making it a reliable choice for medical applications that require prolonged durability. Additionally, polysulfone is transparent, allowing for visual monitoring of medical fluids, which is essential in devices such as IV sets or dialysis equipment.
Polyvinyl Chloride (PVC): Versatile and Cost-Effective
Polyvinyl chloride (PVC) is a widely used plastic in the medical molding industry, primarily due to its versatility and cost-effectiveness. It can be formulated in both rigid and flexible forms, allowing for a broad range of medical applications, including blood bags, tubing, and medical packaging. Flexible PVC is particularly useful for devices that require a high degree of elasticity and flexibility, such as IV tubing or oxygen masks. In addition, medical atomization mask injection molding processing often utilizes flexible PVC to create masks that are both durable and adaptable, providing high functionality for respiratory treatments. The material is also resistant to chemicals and can be easily sterilized, ensuring safety and reliability in clinical environments. PVC’s affordability and ease of processing make it a popular choice for a variety of disposable medical products.
Acrylonitrile Butadiene Styrene (ABS): Tough and Impact-Resistant
Acrylonitrile Butadiene Styrene (ABS) is a tough, impact-resistant thermoplastic often used in medical molding for products that require high strength and durability. ABS is commonly used in the production of components such as surgical instrument handles, diagnostic equipment housings, and dental devices. This material is prized for its ability to withstand mechanical stress and its ease of processing, allowing for the production of complex shapes and intricate designs. In addition to its mechanical properties, ABS can also be sterilized through various methods, making it suitable for a range of medical applications that require both toughness and sterility.
Polyetheretherketone (PEEK): High-Performance and Biocompatible
Polyetheretherketone (PEEK) is a high-performance polymer known for its outstanding mechanical properties, including strength, stiffness, and resistance to wear. PEEK is commonly used in high-end medical devices such as spinal implants, orthopedic devices, and dental applications. One of its key advantages is its biocompatibility, which makes it suitable for long-term implantation in the human body. PEEK is also resistant to high temperatures, chemicals, and radiation, ensuring its reliability even in demanding medical environments. Due to its durability and ability to mimic the mechanical properties of bone, PEEK is becoming increasingly popular in surgical and implant applications.
Nylon: Strength and Resistance to Wear
Nylon, a strong and durable material, is often used in medical molding for applications that require resistance to wear and tear. It is commonly found in medical components like sutures, filters, and surgical instruments. Nylon’s resistance to abrasion and fatigue makes it ideal for parts that need to withstand repeated use or exposure to mechanical stress. Additionally, nylon is biocompatible, ensuring its safe use in medical devices that come into contact with human tissues. The material is also lightweight and can be easily molded into complex shapes, offering flexibility in design.
Polyethylene: Low-Friction and Wear-Resistant
Polyethylene is one of the most commonly used plastics in the medical industry, known for its low friction, high wear resistance, and biocompatibility. This material is often used in applications such as joint replacements, medical tubing, and surgical gloves. Polyethylene’s ability to withstand wear and tear makes it especially useful in implantable devices that are exposed to mechanical stress over time, such as hip and knee replacements. Additionally, its low friction properties contribute to the comfort and functionality of medical devices that require smooth interaction with the body. Polyethylene is also highly resistant to moisture, chemicals, and fatigue, further enhancing its suitability for medical applications.
Overview of Injection Molding Types
Plastic injection molding medical parts companies employ various techniques to meet diverse manufacturing requirements:
Standard Injection Molding: Precision and High Volume Production
Standard injection molding is one of the most widely used techniques in plastic medical injection molding for parts, especially when producing high volumes of components with tight tolerances. In this process, plastic material is heated until it reaches a molten state and then injected under high pressure into a precisely engineered mold. This method is highly effective for manufacturing medical components that require consistency and exacting precision, with precision mold medical ensuring the intricate details and functionality needed for devices like syringes, IV components, and diagnostic equipment. Due to its scalability, standard injection molding is often the preferred choice for mass production of disposable medical devices, where efficiency, accuracy, and cost-effectiveness are essential. The ability to produce large quantities quickly and cost-effectively while maintaining stringent quality standards makes it ideal for meeting the demands of the healthcare industry.
Insert Molding: Combining Materials for Hybrid Components
Insert molding is a specialized technique that involves placing an existing part, typically made of metal, into the medical parts injection molds before the plastic is injected. The plastic is then molded around the insert, creating a hybrid component that combines the durability and strength of metal with the versatility and cost-effectiveness of plastic. This method is commonly used for manufacturing medical devices that require the integration of multiple materials, such as surgical instruments, medical connectors, and probes. By combining materials in a single molding process, insert molding reduces the need for additional assembly steps, which can lower production costs and improve the overall strength and reliability of the final component. It also ensures better material bonding between plastic and metal, increasing the durability and functionality of the device.
Overmolding: Enhancing Functionality and Durability
Overmolding is a technique where one or more layers of plastic are molded over an existing substrate, such as a metal or plastic part, to enhance its durability, functionality, or ergonomics. In medical device manufacturing, overmolding is frequently used to improve the performance of components like ergonomic handles, medical grips, and multi-material parts that require specific tactile properties. For example, overmolding allows for the addition of soft-touch, non-slip materials over hard plastic substrates, which is particularly important in devices that need to be handled frequently, such as surgical tools or diagnostic devices. Overmolding also enables the integration of additional features such as seals or protective coatings that can improve the safety and usability of the medical device. This technique is valuable for producing medical parts that need to be both functional and comfortable for long-term use.
Liquid Silicone Rubber (LSR) Molding: Flexibility and Biocompatibility
Liquid Silicone Rubber (LSR) molding is a specialized injection molding technique that uses liquid silicone rubber (LSR) to create flexible, biocompatible parts. LSR is ideal for medical applications where high flexibility, durability, and biocompatibility are essential. It is commonly used for components like seals, gaskets, medical tubing, and implants, where the material needs to conform to the shape of surrounding tissues and provide a barrier against contamination. LSR molding offers the advantage of creating parts with complex shapes and smooth surfaces that are resistant to temperature extremes, chemicals, and environmental stress. This makes it especially suitable for applications that require long-term use, such as in implants or in products that undergo frequent sterilization. Additionally, LSR’s inherent biocompatibility makes it an excellent choice for devices that come into direct contact with the human body.
Two-Shot Molding: Multi-Material Integration for Complex Components
Two-shot molding, also known as multi-shot molding, is a process that involves injecting two different materials into a mold in two separate phases, using the same mold and equipment. The first material is injected into the mold, and then the mold is rotated or repositioned to inject a second material. This method allows manufacturers to create complex, multi-material parts in a single step, eliminating the need for additional assembly processes. In medical molding, two-shot molding is often used to produce components that require both hard and soft materials in a single piece, such as a device handle that combines a rigid core with a soft, ergonomic outer layer. Mold core pins for medical industry play a crucial role in ensuring the precise positioning and molding of these components, especially when working with multiple materials. This process enables the production of components that are more durable, offer better performance, and have enhanced functionality, while also reducing labor costs and time-to-market. It is commonly used in producing medical devices that need a combination of structural strength and comfort, such as surgical instruments, grips, and connectors. The versatility of multi component injection molding medical also allows for more complex designs, facilitating the integration of multiple functions and materials into a single component, which is essential for modern medical devices.
Gas-Assisted Injection Molding: Reducing Weight While Maintaining Strength
Gas-assisted injection molding is an advanced technique used to reduce the weight of medical components without compromising their structural integrity. In this process, gas (usually nitrogen) is injected into the mold after the plastic has been injected, creating hollow channels within the part. This technique is particularly useful for manufacturing large, complex parts such as medical device housings, where a reduction in material usage can lead to lighter components that are easier to handle. Gas-assisted injection molding helps to improve cycle times and reduce material costs, as less plastic is needed to produce the part. It also enables the creation of parts with improved strength-to-weight ratios, which is critical for medical devices that need to be both lightweight and durable, such as portable medical equipment or assistive devices.
Hot Runner Systems: Improving Efficiency and Reducing Waste
Hot runner systems are an advanced injection molding technique designed to keep the plastic in the runner system heated and in a molten state throughout the injection process. This eliminates the need for cooling and reheating the material between cycles, leading to faster cycle times and more consistent parts. Hot runner systems are often used in medical molding to improve efficiency and reduce waste, especially when producing small, complex components in high volumes. This method is ideal for medical parts that require tight tolerances and high-quality finishes, such as connectors, housings, and other small devices. Hot runner systems can also help reduce material waste, as the plastic in the runner is not discarded after each cycle, making it a more sustainable and cost-effective molding technique.
Compression Molding: Precision and Quality in Large-Scale Production
Compression molding is a technique used for forming plastic parts by placing a preheated material into an open mold cavity, which is then closed to shape the material. This method is particularly effective for producing large, durable parts that require a high degree of precision and consistency, such as prosthetics, orthopedic devices, and custom surgical implants. The compression molding process allows for better control over the material flow, leading to parts with superior mechanical properties and surface finishes. Although this technique is generally used for less intricate designs than injection molding, it remains an important option for producing high-performance medical parts that need to withstand significant stress or wear.
By mastering these materials and techniques, plastic injection molding medical parts companies provide the medical industry with reliable, efficient, and innovative medical molding solutions for creating essential healthcare products.
Top Plastic Injection Molding Medical Parts Companies & Factory Worldwide
The medical industry relies on precision, safety, and innovation, which is why plastic injection molding medical parts companies & factories are indispensable. These companies manufacture components that are critical for medical devices, using advanced molding techniques and medical-grade materials to meet stringent industry standards.
FUJIU Medical Injection Mold:A Leading Global Company & Factory
At FUJIU Medical Injection Mold, we specialize in plastic injection molding for medical parts, providing comprehensive solutions that include custom medical mold design, production, and testing. We are known for our ability to produce high-precision medical components, ensuring tight tolerances and exceptional quality in every part. Our expertise in handling complex medical part designs is critical for ensuring the safety and performance of medical devices.
With our advanced molding technologies, we can produce intricate medical components that meet the stringent requirements of the healthcare industry. We prioritize precision in every step of the process to guarantee that each part is manufactured with the utmost accuracy. By continuously integrating the latest technologies, we improve efficiency while maintaining consistent, high-quality production standards.
Customer satisfaction is a core value for us, and we work closely with our clients to meet specific design and regulatory needs. Our rigorous quality control processes, coupled with thorough testing and inspection, ensure that every medical part we produce is safe, effective, and compliant with international standards. Our commitment to quality and reliability positions FUJIU as a top choice for healthcare manufacturers seeking high-performance plastic injection molded parts, driving growth in the medical injection molding market.
By partnering with industry leaders, healthcare organizations benefit from the unparalleled expertise, advanced technologies, and commitment to quality offered by plastic injection molding medical parts company & factory.
Best Plastic Injection Molding Medical Parts Companies to Consider
Selecting the right plastic injection molding medical parts companies is critical for ensuring the success of medical device manufacturing projects. The “best” companies distinguish themselves by their expertise, technological advancements, and ability to meet rigorous industry standards. Below, we delve into what makes a company stand out and highlight leading examples in the field.
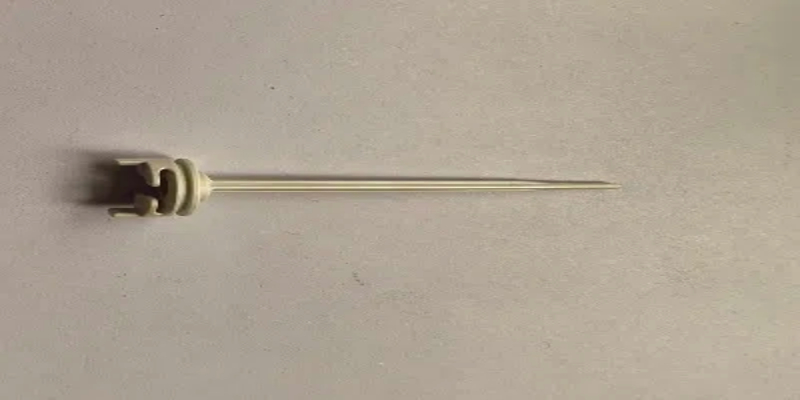
What Makes a Company “The Best”?
- Experience and Reputation in Medical Device Manufacturing
The best plastic injection molding medical parts companies have extensive experience in crafting components for medical devices. Their established reputation ensures trust, as they consistently deliver high-quality products to healthcare clients worldwide. - Use of Advanced Technology
Leading companies invest in state-of-the-art technology, such as ISO-certified cleanroom environments and advanced injection molding machines. These tools guarantee sterile, contaminant-free production and meet the stringent requirements of the medical industry. - Precision, Scalability, and Compliance
Precision is non-negotiable in medical device manufacturing, as even minor deviations can compromise safety. The best plastic injection molding medical parts companies excel in producing high-precision parts that meet FDA and ISO standards while also offering scalability for high-volume production. - Commitment to Cost-Effectiveness and Efficiency
Top companies focus on reducing product development time through efficient processes and cost-effective manufacturing. Their ability to streamline operations benefits clients by delivering quicker time-to-market without sacrificing quality.
Examples of the Best Companies
- FUJIU Medical Injection Mold
We are renowned for our comprehensive engineering services, spanning parts analysis, mold design, and final delivery. Our team of medical molding engineers specializes in producing complex medical components with precise tolerances, ensuring reliability for critical applications.With a focus on innovation, we stand out as a leader among plastic injection molding medical parts companies.
The best plastic injection molding medical parts companies excel in combining cutting-edge technology with deep industry knowledge, ensuring we can meet the evolving demands of the healthcare sector. Whether for prototyping or mass production, our companies provide the expertise needed to manufacture safe, reliable, and high-quality medical components.
Plastic Injection Molding Medical Parts Companies: Key Considerations for Medical Devices
The role of plastic injection molding medical parts companies in the production of medical devices is vital, as these manufacturers ensure that components meet the highest standards of precision, safety, and functionality. Below are some key considerations these companies must address when manufacturing medical devices.
Types of Medical Devices Manufactured via Injection Molding
Plastic injection molding medical parts companies produce a wide range of critical components for the healthcare sector. These include:
- Surgical Instruments: Handles, grips, and other ergonomic components used in operating rooms. Injection molding ensures these parts meet strict hygiene and durability requirements.
- Implants: Components like screws, plates, and artificial joints made with biocompatible materials to integrate seamlessly with the human body.
- Syringes and IV Connectors: Disposable items that require sterile, high-volume production. Rapid injection molding medical enables the rapid and cost-effective manufacturing of these essential components, ensuring precision and compliance with stringent medical standards.
- Diagnostic Tools: Enclosures, housings, and small parts for medical equipment like glucose meters and blood analyzers. Molding offers precise tolerances to ensure accuracy in diagnostic results.
Regulatory Compliance
To operate successfully, plastic injection molding medical parts companies must adhere to strict regulatory standards, which guarantee the safety and effectiveness of medical devices.
- FDA Certification: Compliance with FDA regulations ensures that materials and manufacturing processes meet the criteria for medical device safety. This includes sterility, biocompatibility, and durability.
- ISO Standards: Many companies maintain ISO 13485 certification, which outlines requirements for a quality management system specifically for medical device production.
- Impact on Quality and Safety: Regulatory compliance minimizes risks by ensuring every component is free of defects and meets the functional requirements essential for patient care.
Material Selection and Biocompatibility
Plastic injection molding medical parts companies must carefully select materials to meet the specific demands of medical devices. Material selection directly impacts the device’s performance, safety, and compliance.
- Polyetheretherketone (PEEK): Used in implants for its exceptional resistance to wear and harsh environments.
- Polycarbonate: Transparent, durable, and lightweight, making it ideal for diagnostic tools and enclosures.
- Silicone: Highly flexible and chemically inert, used for catheters and seals.
- Medical-Grade Plastics: Engineered for sterilization compatibility and biocompatibility, ensuring they can safely interact with human tissues.
Material biocompatibility is essential for devices like implants or syringes, where direct contact with the body occurs. Companies must rigorously test materials to confirm their safety and effectiveness in medical applications.
Plastic injection molding medical parts companies are integral to the development of reliable, high-quality medical devices. By addressing these key considerations—device type, regulatory compliance, and material selection—they deliver safe, durable, and precise components critical to the healthcare industry.
Factors to Consider When Choosing Plastic Injection Molding Medical Parts Companies
Choosing the right plastic injection molding medical parts companies is critical to ensuring your medical device manufacturing project meets its quality, compliance, and delivery requirements. Below are key factors to evaluate when selecting a company for your needs.
Location
The location of plastic injection molding medical parts companies plays an essential role in ensuring seamless collaboration and efficient shipping.
- Proximity for Convenience and Cost Savings: Working with a company located nearby can reduce logistical challenges and shipping costs. A local manufacturer enables easier communication, quicker project adjustments, and faster turnaround times.
- Plastic Injection Molding Medical Parts Companies Near Me: To find local manufacturers, research companies with facilities in your region. Look for reviews, certifications, and capabilities that align with your project needs. Leveraging regional expertise ensures quicker access to prototypes and finished parts, which is crucial in meeting time-sensitive medical device production schedules. Many of these companies also specialize in the fabrication of prototype medical equipment molds, providing the necessary expertise and precision to create accurate and functional molds for your medical device designs.
Industry Specialization
Not all injection molding companies focus on the medical industry, and specialization matters significantly when choosing a partner.
- Expertise in Medical Parts: Select plastic injection molding medical parts companies with a strong focus on medical device manufacturing. These companies understand the critical need for precision, biocompatibility, and compliance with regulations like FDA and ISO 13485. Their experience ensures they can meet the specific challenges of medical part production, such as creating sterilizable and safe components.
- Medical Device Injection Molding Companies vs. Automotive Injection Molding Companies: Medical device molding demands higher precision, tighter tolerances, and rigorous testing compared to automotive or consumer goods industries. Medical-grade materials, cleanroom environments, and regulatory adherence are essential in the healthcare field, making specialized companies better suited for such projects.
Other Key Considerations
- Reputation and Track Record: Evaluate the company’s history of delivering high-quality medical components. Client testimonials and case studies can provide insights into their reliability and expertise.
- Capabilities and Technology: Ensure the company uses advanced technology, such as cleanrooms for sterile production and modern machinery for precision molding.
- Scalability and Flexibility: Consider whether the company can accommodate your production volume, from prototyping to mass production, without compromising on quality or timelines.
By prioritizing these factors, you can confidently select the best plastic injection molding medical parts companies for your project. Their specialization, proximity, and expertise will ensure your medical components meet the industry’s highest standards.
How to Choose the Best Plastic Injection Molding Medical Parts Companies for Medical Devices
Selecting the best plastic injection molding medical parts companies for your medical device project is essential to ensure quality, precision, and compliance. A thorough evaluation of the following criteria can help you make an informed decision.
Evaluation Criteria
- Technological Capabilities
The use of advanced machinery and technology is a hallmark of top plastic injection molding medical parts companies. Look for manufacturers that operate in ISO-certified cleanroom environments to guarantee sterile production. Cutting-edge machines ensure high precision, enabling tight tolerances and consistent quality, which are essential for medical devices like surgical instruments and implants. - Company Experience and Client Portfolio
A company’s experience in the medical industry speaks volumes about its ability to handle the complexities of medical component manufacturing. Review their client portfolio and past projects to assess their expertise in producing parts that meet stringent medical standards. Reputable plastic injection molding medical parts companies often highlight their success in partnering with leading healthcare organizations. - Customization Options and Flexibility in Production
The best plastic injection molding medical parts companies offer extensive customization options to cater to unique project requirements. Whether you need small, intricate parts or larger components, the company should demonstrate flexibility in material selection, mold design, and production volumes. They should also be able to adjust to changes in project scope or specifications without compromising quality or timelines. - Support with Prototyping and Design
Companies that provide robust support for prototyping and design add significant value to your project. Prototyping ensures that designs meet functional requirements before full-scale production, reducing costly errors. The best plastic injection molding medical parts companies offer design assistance to refine complex medical parts, optimizing them for manufacturability and performance.
Choosing the best plastic injection molding medical parts companies for medical devices requires a balance of technological expertise, industry experience, and a commitment to quality. By prioritizing the evaluation criteria outlined above, you can find a reliable partner from the leading medical plastic parts companies to produce safe, precise, and compliant medical components, ensuring the success of your project and the well-being of end users.
Key Measures Plastic Injection Molding Medical Parts Companies Take to Ensure Product Consistency
Plastic injection molding medical parts companies must achieve high precision, repeatability, and compliance to ensure product consistency. Since medical devices directly impact patient health and safety, even minor deviations in dimensions, material properties, or quality can lead to product failures or regulatory non-compliance. To maintain strict standards, these companies implement a combination of advanced process control, rigorous quality assurance, standardized material selection, and data-driven manufacturing optimization.
This article explores the key measures plastic injection molding medical parts companies take to maintain product consistency, covering aspects such as precision molding techniques, quality control systems, material verification, process automation, and regulatory compliance. Each of these elements ensures that every medical component produced meets exact specifications, regardless of batch size or production volume.
Precision Molding Techniques to Maintain Dimensional Accuracy
Consistent product quality begins with precise molding processes that minimize variation and ensure that each medical part is manufactured to exact specifications. Plastic injection molding medical parts companies use specialized techniques to maintain tight tolerances, reduce defects, and improve repeatability.
High-Precision Injection Molding Machines
- Use of micro-molding technology enables the production of extremely small, complex medical parts with tolerances as low as ±0.001 inches.
- Machines equipped with servo-driven controls offer better accuracy in pressure, speed, and temperature regulation, reducing inconsistencies in the final product.
Multi-Cavity Molding for Batch Uniformity
- Companies use multi-cavity molds to produce identical medical parts in large quantities.
- To ensure uniformity, molds undergo flow balance analysis, which ensures that plastic fills each cavity evenly, preventing weight and dimension variations.
Scientific Molding for Process Optimization
- Scientific molding principles involve testing and optimizing parameters such as melt temperature, cooling rate, and injection pressure before full-scale production.
- Data from real-time sensors helps adjust the process in case of variations, ensuring consistent results.
Rigorous Quality Control Systems for Defect Prevention
Medical plastic components must meet strict quality standards to ensure reliability. Companies use advanced inspection and testing at multiple production stages to identify and eliminate defects before products reach the market.
Automated In-Process Quality Inspection
- High-speed vision inspection systems detect surface defects, dimensional variations, and contamination in real-time.
- Inline laser measurement tools ensure consistent part dimensions during production.
First Article Inspection (FAI) and Statistical Process Control (SPC)
- FAI is performed before mass production to confirm that the first batch meets design specifications.
- SPC techniques, such as real-time data collection and trend analysis, help monitor variations and detect inconsistencies early.
Non-Destructive Testing (NDT) for Material Integrity
- X-ray and ultrasonic testing ensure internal structural consistency without damaging components.
- Tensile and impact testing verifies mechanical strength, ensuring that the plastic part can withstand medical applications.
Standardized Material Selection and Verification
The properties of medical-grade plastics significantly impact product consistency. Companies must ensure that all materials meet biocompatibility, durability, and sterilization requirements.
Use of FDA and ISO-Approved Medical-Grade Plastics
- Materials like PEEK, polycarbonate (PC), polypropylene (PP), and liquid silicone rubber (LSR) are selected for their chemical resistance, durability, and biocompatibility.
- Only suppliers with FDA, ISO 10993, and USP Class VI certifications are chosen to ensure material reliability.
Raw Material Lot Testing and Certification
- Incoming material inspection includes moisture analysis, melt flow index testing, and chemical composition verification.
- Lot traceability ensures that each batch of raw material can be tracked back to its source, preventing contamination risks.
Consistency in Material Processing Parameters
- Pre-drying plastics with controlled moisture content ensures optimal viscosity and mold filling behavior.
- Strict control of melt temperature and injection pressure prevents material degradation and inconsistencies.
Process Automation and Smart Manufacturing for Repeatability
Automation enhances repeatability and efficiency, reducing the risk of human error while ensuring consistent product output. Leading companies integrate AI-driven manufacturing, robotics, and IoT monitoring to maintain tight process control.
AI-Driven Process Monitoring and Feedback Loops
- Real-time AI analysis detects minor deviations in injection parameters and automatically adjusts machine settings.
- Closed-loop feedback systems correct pressure, temperature, and cooling variations in real time.
Robotic Handling and Assembly
- Automated robotic arms remove molded parts with consistent handling force, preventing deformation.
- Automated assembly and packaging lines ensure sterility and prevent contamination during post-processing.
Digital Twin Technology for Predictive Maintenance
- Digital twin simulations create a real-time virtual replica of the manufacturing process.
- Predictive analytics help identify potential failures before they affect production, reducing downtime and ensuring consistency.
Regulatory Compliance and Validation for Consistent Performance
Medical plastic parts must comply with global regulatory requirements to ensure they meet safety and performance standards. Companies follow strict validation procedures to confirm consistent product quality across multiple production runs.
ISO 13485 and FDA 21 CFR Part 820 Compliance
- ISO 13485-certified companies implement a medical device quality management system (QMS) that includes risk management, traceability, and process validation.
- FDA 21 CFR Part 820 mandates that manufacturers follow Good Manufacturing Practices (GMP) to ensure uniformity and quality.
Process Validation and Qualification (IQ, OQ, PQ)
- Installation Qualification (IQ) verifies that equipment is installed and operates correctly.
- Operational Qualification (OQ) ensures that molding processes meet defined specifications under standard conditions.
- Performance Qualification (PQ) confirms that repeated production cycles produce consistent and defect-free medical parts.
Lot Traceability and Documentation for Audits
- Comprehensive documentation ensures that every batch is traceable from raw material procurement to final delivery.
- Regular internal audits and regulatory inspections help maintain compliance with industry standards.
Plastic injection molding medical parts companies take comprehensive measures to ensure product consistency across all production stages. Precision molding techniques, including scientific molding and multi-cavity molds, help maintain dimensional accuracy. Rigorous quality control systems, such as real-time monitoring, statistical process control, and non-destructive testing, prevent defects. Standardized material selection ensures the use of biocompatible and FDA-approved plastics, while process automation enhances repeatability and reduces human error. Lastly, regulatory compliance and validation through ISO 13485, FDA, and GMP requirements guarantee safe and reliable medical components. By implementing these strategies, medical injection molding companies achieve high-quality, consistent, and regulatory-compliant production that meets the demands of the healthcare industry.
Do Plastic Injection Molding Medical Parts Companies Need to Comply with MedAccred Certification?
Plastic injection molding medical parts companies play a crucial role in the healthcare industry, manufacturing critical components for medical devices, surgical tools, and implantable parts. Given the high regulatory and quality standards in the medical sector, manufacturers must comply with various certifications and quality assurance programs. One of the most recognized certifications is MedAccred, a specialized accreditation for critical manufacturing processes in the medical industry.
This article explores whether plastic injection molding medical parts companies need to comply with MedAccred certification by analyzing its importance, industry requirements, benefits, and challenges.
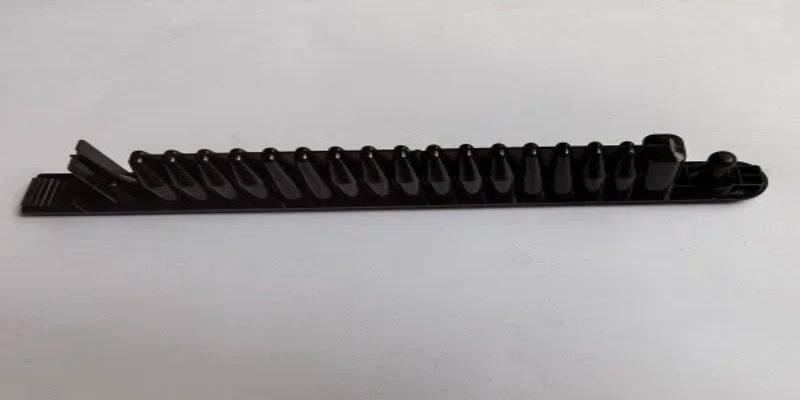
What Is MedAccred Certification and Why Does It Matter?
Before determining whether compliance is necessary, it is essential to understand what MedAccred certification is and why it holds significance in the medical industry.
Definition and Purpose of MedAccred
MedAccred is a rigorous quality assurance program managed by the Performance Review Institute (PRI). It is designed to ensure that critical manufacturing processes meet industry-specific quality and safety requirements. Unlike general certifications like ISO 13485, which focus on overall quality management systems, MedAccred specifically evaluates manufacturing processes such as:
- Plastic injection molding
- Extrusion and blow molding
- Sterilization and heat treating
- Welding and brazing
MedAccred certification is not legally required but is often demanded by medical device OEMs (Original Equipment Manufacturers) as part of their supplier qualification process.
Are Plastic Injection Molding Medical Parts Companies Required to Have MedAccred Certification?
While MedAccred certification is not a legal requirement, many medical device companies prefer or require their suppliers to have this accreditation.
Industry Regulations vs. MedAccred Compliance
- Regulatory bodies like the FDA (U.S.), EMA (Europe), and ISO 13485 set general quality standards, but they do not mandate MedAccred certification.
- However, major medical device manufacturers and OEMs often require their suppliers to obtain MedAccred as a way to demonstrate superior process control and risk mitigation.
- Hospitals, surgical centers, and regulatory agencies increasingly prefer suppliers with MedAccred accreditation, as it ensures compliance with best-in-class manufacturing practices.
Thus, while not mandatory by law, MedAccred can be a business requirement for plastic injection molding companies working with top-tier medical device brands.
Benefits of MedAccred Certification for Medical Injection Molding Companies
Even though compliance is not legally required, obtaining MedAccred certification provides several competitive advantages for medical injection molding companies.
Key Benefits of MedAccred Accreditation
- Improved Market Access – Many large medical OEMs prioritize suppliers with MedAccred certification, leading to better business opportunities.
- Enhanced Quality Control – The accreditation ensures superior process validation, defect prevention, and risk management in plastic injection molding.
- Regulatory Compliance Support – MedAccred aligns with FDA, ISO 13485, and GMP standards, helping manufacturers meet broader industry regulations.
- Increased Customer Confidence – Healthcare providers and device manufacturers trust MedAccred-certified suppliers to deliver safe and high-quality medical components.
- Process Optimization & Cost Savings – The rigorous audit process helps companies identify inefficiencies, reducing scrap rates, rework, and compliance risks.
For plastic injection molding medical parts companies, MedAccred certification enhances credibility, improves process consistency, and secures long-term partnerships with medical OEMs.
Challenges of Obtaining MedAccred Certification
While the benefits are significant, achieving MedAccred certification comes with challenges that companies must consider.
Common Challenges in MedAccred Compliance
- High Costs – The certification process involves comprehensive audits, documentation, and training, which can be expensive.
- Strict Audit Requirements – MedAccred audits are extremely detailed, requiring companies to prove process consistency, traceability, and risk management.
- Time-Consuming Process – The accreditation process can take months to years, depending on the company’s readiness and compliance levels.
- Continuous Compliance Requirements – MedAccred requires ongoing monitoring, including regular audits and process validations.
Despite these challenges, many leading medical injection molding companies invest in MedAccred certification to stay ahead in the competitive medical manufacturing market.
While not legally mandatory, MedAccred certification is increasingly becoming a standard requirement for plastic injection molding medical parts companies working with top-tier medical device manufacturers. The certification offers quality assurance, regulatory alignment, and competitive advantages, making it a valuable investment for companies seeking long-term success in the medical manufacturing sector.
For companies aiming to expand market access, improve quality control, and build stronger relationships with OEMs, obtaining MedAccred accreditation is a strategic move that ensures compliance with industry best practices and superior manufacturing standards.
Key Innovation Focus Areas for Plastic Injection Molding Medical Parts Companies to Drive Future Growth
The medical injection molding industry is highly competitive and heavily regulated, requiring companies to stay innovative to meet the evolving needs of healthcare. Plastic injection molding medical parts companies looking to maintain growth must focus on a variety of innovative strategies that enhance product quality, manufacturing efficiency, regulatory compliance, and customer satisfaction. This article explores the critical areas where these companies should focus their innovation efforts to stay ahead in the medical injection molding industry. Key aspects of innovation include material advancements, smart manufacturing technologies, sustainability initiatives, customization and miniaturization of medical parts, and enhanced regulatory compliance.
Each of these focus areas addresses challenges faced by medical manufacturers while also providing opportunities for differentiation, cost reduction, and better patient outcomes.
Advancements in Medical-Grade Materials
Innovation in medical-grade materials is essential to meet the increasing demand for biocompatibility, durability, and performance in medical devices. As medical technologies become more sophisticated, the need for advanced materials that can withstand more rigorous applications grows.
Biocompatible and High-Performance Plastics
- Polyetheretherketone (PEEK) and polycarbonate (PC) are high-performance plastics used in implants, surgical tools, and other medical devices. As the medical device sector moves toward more complex solutions, companies need to focus on researching and developing new biocompatible polymers that offer better strength, resistance to wear, and chemical compatibility with the human body.
- Companies should also explore bio-degradable polymers for applications where long-term implant solutions are not necessary. These materials can help in reducing long-term complications and environmental impact.
Customized Material Solutions
- To meet unique patient needs or specialized devices, companies can look into developing customized formulations of plastics that exhibit improved functionality, such as enhanced antimicrobial properties or higher flexibility for patient comfort.
- Collaborating with material scientists to create proprietary materials specifically designed for challenging medical applications can give companies a competitive edge.
Smart Manufacturing and Automation Technologies
To remain competitive, plastic injection molding medical parts companies must embrace smart manufacturing technologies that leverage automation, data analytics, and AI. These technologies can drive cost-efficiency, reduce human error, and improve product quality and traceability.
AI and Machine Learning for Predictive Maintenance
- AI-driven systems can monitor production machines and predict when maintenance is needed before a failure occurs. This reduces downtime and ensures that machines are operating at optimal efficiency, leading to consistent product quality.
- Implementing machine learning algorithms also helps optimize molding parameters such as temperature, pressure, and injection speed in real-time, reducing waste and improving the precision of each medical part.
Robotics and Automation for Efficient Production
- Automated handling of molded parts by robotic arms minimizes human error, reduces contamination risks, and speeds up production time.
- Automated post-processing of parts, such as packaging, assembly, and sterilization, can further reduce costs and ensure products meet sterile packaging standards.
- Companies should also invest in digital twin technology, which creates virtual replicas of manufacturing processes. These models allow for real-time simulations, improving decision-making and process control.
Sustainability and Eco-friendly Practices
Sustainability is becoming an increasingly important factor in both medical device production and regulatory compliance. Plastic injection molding medical parts companies should focus on greener manufacturing practices, recycling initiatives, and energy-efficient production systems to minimize their environmental impact.
Recyclable and Eco-friendly Materials
- Emphasizing the development and use of recyclable medical plastics (such as polypropylene (PP) and high-density polyethylene (HDPE)) can reduce waste and contribute to more sustainable practices. Companies can also work to introduce biodegradable polymers for certain applications.
- Collaboration with supply chain partners to recycle post-production scrap and reduce waste can create a closed-loop system, improving sustainability in the production process.
Energy-Efficient Manufacturing
- Advanced injection molding machines that use less energy by optimizing cooling cycles and heating temperatures can significantly reduce overall energy consumption.
- Companies should explore the integration of renewable energy sources (like solar or wind power) into their facilities to reduce their carbon footprint.
Miniaturization and Customization of Medical Parts
As medical technology continues to advance, there is an increasing demand for smaller, more complex components. This trend towards miniaturization and customization requires companies to innovate in both design and manufacturing processes.
Miniaturization for Surgical and Implant Devices
- With the increasing demand for minimally invasive procedures and precision medical devices, micro-molding technologies can enable the production of tiny, complex components used in surgeries and implants. These technologies make it possible to create intricate features and fine details that are required in modern medical applications.
- Sub-micron molding technologies enable production of smaller, lighter devices that improve patient comfort and recovery times. Companies should invest in specialized equipment to produce parts with higher precision and miniaturized features for use in implantable devices, drug delivery systems, and catheters.
Customization of Parts for Specific Applications
- Companies should explore the 3D printing of molds and customized injection molding solutions to meet the growing demand for patient-specific medical parts, such as customized implants, prosthetics, and orthodontics. This allows for creating unique shapes and sizes based on patient-specific anatomy, improving both the functionality and comfort of medical devices.
- Partnering with healthcare providers and biomedical engineers can help companies understand specific needs, leading to better-designed products that can cater to individualized treatment plans.
Enhanced Regulatory Compliance and Documentation Systems
As medical device regulations become stricter globally, companies must continuously innovate to stay ahead of regulatory challenges and ensure full compliance. Innovation in documentation systems, validation processes, and regulatory reporting can streamline compliance and reduce the risk of costly errors or product recalls.
Automated Documentation and Traceability Systems
- The introduction of digital documentation systems and blockchain technology can improve traceability and ensure that all steps of production are recorded and auditable, making it easier to comply with FDA 21 CFR Part 820 or ISO 13485 standards.
- Real-time validation of production processes through automated systems ensures continuous compliance, reducing the time and cost required for manual inspections.
Global Regulatory Adaptation and Compliance Tools
- Companies should invest in software tools that allow them to quickly adapt to changing regulations in different markets, such as EU MDR (Medical Device Regulation) or FDA standards.
- Leveraging machine learning algorithms to predict future regulatory changes and automatically update compliance systems will allow companies to stay ahead of new challenges and minimize the risk of non-compliance.
Plastic injection molding medical parts companies must focus on innovation across multiple fronts to remain competitive in the rapidly evolving medical device industry. Innovations in medical-grade materials, smart manufacturing technologies, sustainability, miniaturization, and regulatory compliance are all critical to meeting the increasing demand for high-performance, cost-effective, and patient-specific medical solutions. By staying ahead in these areas, companies can not only improve product consistency and manufacturing efficiency but also position themselves as leaders in the medical injection molding industry, helping shape the future of healthcare.
FAQs about Plastic Injection Molding Medical Parts Companies
Medical injection molding is used to manufacture a wide range of medical products essential to the healthcare industry. These include single-use items such as syringes, IV connectors, catheters, and blood bags, which are produced in large quantities to meet global demands for sterile and safe medical equipment.
More complex components like surgical instruments, diagnostic tools, and implants are also crafted using injection molding techniques. These products require high precision and are often made from biocompatible materials like polycarbonate, PEEK, and medical-grade silicone.
Other examples include enclosures for electronic medical devices, test tubes, and petri dishes, which are critical in laboratories and hospitals. Injection molding is favored for its ability to produce durable, high-quality parts at scale while maintaining tight tolerances, ensuring reliability in life-saving medical applications.
The largest injection molding company in the world is Haitian International Holdings Limited, headquartered in China. Haitian is recognized globally for its production of high-performance injection molding machines and its extensive manufacturing capabilities, serving industries such as automotive, consumer goods, and medical devices.
With a strong presence in over 100 countries, Haitian dominates the market by delivering cost-effective and technologically advanced solutions. Their machines, such as the Mars Series and Jupiter Series, are designed to handle a wide range of applications, including those required for precision medical molding.
Haitian’s innovation, scalability, and customer-focused approach make it a leader not only in injection molding machinery production but also in supporting various industries, including the growing medical device sector.
The market for medical injection molding is expanding rapidly due to increasing demand for affordable, high-quality, and precise medical components. In 2022, the global medical injection molding market was valued at USD 34.78 billion, with projections to reach USD 51.95 billion by 2029, growing at a compound annual growth rate (CAGR) of 6.7%.
Key drivers include the growing global population, advancements in healthcare technologies, and the rising prevalence of chronic diseases. Emerging markets in regions like Asia-Pacific are also contributing to this growth, as healthcare infrastructure improves and demand for medical devices rises.
The market encompasses a wide array of products, from disposable medical supplies to intricate surgical tools and implants. Companies investing in biocompatible materials, cleanroom facilities, and precision molding technologies are well-positioned to thrive in this lucrative and vital industry.
For plastic injection molding medical parts companies, the hourly rate varies based on machine size, complexity, and location. Generally, small machines (under 100 tons) cost around $30–$60 per hour, while larger machines (500+ tons) can exceed $150 per hour. Additional factors like cleanroom requirements for medical-grade production, material selection, and secondary operations (e.g., sterilization, assembly) can increase costs. Companies like FUJIU Medical Injection Mold optimize efficiency and automation to reduce hourly expenses while maintaining high precision for medical applications.
Medical-grade plastics must meet biocompatibility, sterilization, and durability requirements. Common choices include:
Polycarbonate (PC) – High impact resistance, transparent, used for surgical instruments.
Polyetheretherketone (PEEK) – Heat-resistant, ideal for implants.
Polypropylene (PP) – Lightweight, chemical-resistant, used for syringes.
Polyethylene (PE) – Flexible, used for tubing.
FUJIU Medical Injection Mold specializes in precision molding with these materials, ensuring compliance with FDA and ISO standards for medical devices.
Cost calculation includes tooling, material, machine time, labor, and post-processing. The formula:
Total Cost = (Material Cost + Machine Time Cost + Labor) × Production Volume + Mold Cost
For medical injection molding, factors like cleanroom compliance, high-precision tooling, and sterilization add to expenses. FUJIU Medical Injection Mold optimizes costs with automated production and durable molds for high-volume medical device manufacturing.
A well-maintained injection mold lasts between 100,000 and 1,000,000 cycles, depending on material, design, and usage. Medical-grade molds, requiring tight tolerances and FDA compliance, often use hardened steel, extending lifespan. FUJIU Medical Injection Mold ensures durability by using high-quality tooling and maintenance, allowing cost-effective production of medical parts over many years.
Medical injection molds vary in cost, from $5,000 for simple molds to $200,000+ for complex, multi-cavity, high-precision molds. Factors affecting cost include material, number of cavities, cleanroom requirements, and cycle life. FUJIU Medical Injection Mold specializes in high-precision tooling, offering cost-effective solutions for medical devices while ensuring long-lasting performance.
For medical-grade plastic injection molding, machine costs depend on tonnage and complexity. Small machines (~100 tons) cost $30–$60/hour, while larger machines (500+ tons) can exceed $150/hour. Cleanroom-certified machines for medical parts incur extra costs. FUJIU Medical Injection Mold optimizes efficiency to reduce per-hour expenses while maintaining medical-grade quality.
A typical draft angle for injection molding is 1–3 degrees per side, ensuring easy ejection from the mold. For medical components, tight tolerances may require lower draft angles. FUJIU Medical Injection Mold uses precision engineering to maintain accuracy while optimizing draft angles for smooth production and minimal defects.
Medical injection molding is highly profitable due to high demand, repeat orders, and regulatory compliance barriers. Profitability depends on automation, production volume, and material efficiency. FUJIU Medical Injection Mold maximizes profitability through high-precision, cost-effective manufacturing, ensuring compliance while reducing waste and cycle time.
The highest-quality plastics used in medical injection molding are those that combine strength, biocompatibility, and sterilization resistance:
PEEK – Gold standard for implants and high-performance medical devices.
Medical-Grade Polycarbonate – Used for ventilators, surgical tools, and durable medical enclosures.
Medical-Grade Silicone – Preferred for catheters and flexible prosthetics due to its soft, skin-friendly properties.
PTFE (Teflon) – Used in medical tubing and coatings due to its non-stick and chemical-resistant properties.
These materials are widely used in injection molding for medical parts due to their safety, durability, and compliance with medical standards.
The hardest plastics used in medical injection molding include:
PEEK (Polyether Ether Ketone) – Highly durable, used in implants, orthopedic devices, and surgical tools.
Ultem (Polyetherimide – PEI) – Known for high heat resistance and strength, used in sterilizable surgical equipment.
Polycarbonate (PC) – Impact-resistant, used in protective medical gear and equipment housings.
PEEK stands out as the hardest plastic, offering metal-like properties with superior biocompatibility and sterilization resistance.
The future of medical injection molding is driven by innovation in materials, automation, and sustainability:
Bioabsorbable Polymers – Future medical implants will use biodegradable plastics that dissolve in the body over time, reducing the need for surgical removal.
Automation & AI – Smart manufacturing, using AI and robotics, will improve quality control and production efficiency.
Micro-Molding – The demand for miniature, high-precision medical components will push advancements in micro-injection molding.
Sustainable Plastics – Eco-friendly, recyclable, and bio-based polymers will gain traction as medical industries strive for greener solutions.
Injection molding will continue to dominate mass production of medical devices, with enhanced precision, faster cycles, and advanced materials shaping its future.
Surgical-grade plastics are biocompatible, sterilizable, and high-performance polymers used in medical and surgical applications. These include:
PEEK – Used in implants and spinal fusion cages due to its strength and compatibility with the human body.
Polycarbonate (PC) – Used for surgical instrument handles, ventilators, and face shields due to its high impact resistance.
Polypropylene (PP) – Common in syringes and IV components due to its chemical resistance.
Medical-Grade Silicone – Used for catheters, prosthetics, and soft-tissue implants due to its flexibility and skin-friendliness.
These materials are used in injection molding for their precision, durability, and ability to meet FDA regulations.
Injection molding is cost-effective for high-volume production, but for low-volume runs, other processes may be cheaper:
Vacuum Forming – Used for medical trays and enclosures, this process requires simpler tooling, making it more cost-effective for small production batches.
CNC Machining – While machining is expensive per unit, it avoids costly mold development, making it suitable for custom, low-quantity medical parts.
3D Printing – Offers cost advantages for prototyping and limited production of medical devices without mold expenses.
Extrusion Molding – Cheaper for tubing and catheter production, extrusion is used widely in the medical industry.
If a medical company requires thousands to millions of identical parts, injection molding remains the best option. For smaller production runs, 3D printing or machining can be more cost-efficient.
While injection molding is the dominant manufacturing method for medical plastic parts, alternative technologies might be better depending on the application:
3D Printing (Additive Manufacturing) – Ideal for rapid prototyping, low-volume production, and custom medical implants, 3D printing allows for complex geometries that traditional molding cannot achieve.
Micro-Molding – A specialized injection molding process used for ultra-small, highly precise medical components.
Compression Molding – Preferred for larger medical parts that don’t require intricate detailing.
Thermoforming – Useful for medical trays, packaging, and enclosures where injection molding may be cost-prohibitive.
For large-scale production, injection molding remains superior in cost-efficiency and consistency. However, for custom and patient-specific medical devices, 3D printing is increasingly becoming a viable alternative.
Medical-grade plastics used in injection molding must meet four critical requirements:
Biocompatibility – The plastic must not cause toxic or allergic reactions in the human body. Compliance with ISO 10993 and USP Class VI is necessary.
Sterilizability – The material should withstand sterilization methods such as autoclaving, gamma irradiation, or EtO sterilization without degrading.
Chemical Resistance – It should resist bodily fluids, cleaning agents, and harsh chemicals commonly used in medical environments.
Mechanical Strength & Durability – The plastic must maintain structural integrity under stress, especially for implants, surgical tools, and drug delivery devices.
Materials like PEEK, polycarbonate, and medical-grade polyethylene are widely used in medical injection molding due to their compliance with these requirements.
Medical-grade polymers are specialized plastics designed to meet stringent healthcare industry standards for biocompatibility, sterilization, and durability. These polymers include polyether ether ketone (PEEK), polycarbonate (PC), polypropylene (PP), polyethylene (PE), and medical-grade silicone. They are widely used in injection molding for surgical instruments, implants, drug delivery devices, and diagnostic equipment. Medical-grade polymers must comply with FDA regulations, ISO 10993, and USP Class VI standards to ensure safety for direct or indirect human contact. Many of these materials are resistant to harsh sterilization methods, including autoclaving, gamma radiation, and ethylene oxide (EtO) sterilization. Their lightweight properties, chemical resistance, and strength make them preferable over traditional materials like metals and ceramics.
Yes, injection molding is generally cheaper than machining when producing large quantities of medical plastic parts. Machining is ideal for low-volume production and highly intricate designs because it doesn’t require expensive molds. However, for mass production, injection molding offers a lower per-unit cost due to its ability to rapidly produce thousands or millions of identical parts with minimal material waste. Medical companies prefer injection molding for components such as syringes, IV connectors, and surgical instrument casings because of its efficiency, precision, and repeatability. While initial mold costs are high, the long-term savings outweigh machining when scaling up production. Additionally, advanced micro-molding techniques allow for the creation of highly detailed medical parts that machining might struggle to achieve efficiently.
Contact our professional team now for a same-day quote and risk-free project evaluation. Benefit from ISO 8 cleanrooms, advanced machines, and 12-hour fast response in medical injection molding.