Molding plays a crucial role in the medical device manufacturing industry, serving as a key process for producing high-quality, reliable medical products. With the growing demand for precise and durable medical devices, advanced molding techniques, such as injection molding, blow molding, and eco-friendly molding processes, are essential for meeting industry standards. These processes ensure that medical components, from syringes to surgical instruments, are both safe and functional. Medical molding products are precision devices made from medical-grade plastics through injection molding, ensuring quality and reliability for healthcare use.
Low-Volume to High-Volume Production Capabilities
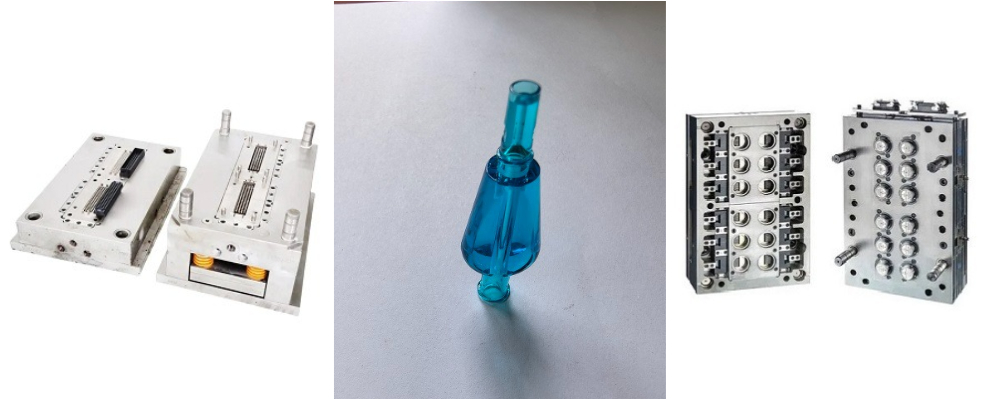
Attributes | Details |
---|---|
Place of Origin | Dongguan, Guangdong, China |
Brand Name | LY Medical Injection Mold |
Product Name | Medical Molding Products |
Molding Mode | Plastic Injection |
Product Material | Plastic |
Color | Customized |
Size | Customized |
Length | Customized |
Service | OEM ODM |
Processing Service | Molding, Cutting |
Surface Treatment | Anodizing, Polishing, Powder Coating, Screen Printing, Painting, etc. |
Tolerance | 0.01-0.05mm |
Features | High Precision |
Logo | Customized Logo Acceptable |
Certification | ISO9001/ISO13485 |
Packing Details | Outer Carton Inner Packing According to Customer Requirements |
Sales Unit | Single Item |
Medical Molding Products: Types of Molding Techniques in the Medical Industry
Medical molding products are produced using a variety of molding techniques, each tailored to specific requirements of the medical device plastic manufacturing industry. These techniques ensure the production of high-quality, precise, and durable products necessary for healthcare applications.

Injection Molding
Injection molding is one of the most widely used techniques in the medical industry. The process involves melting plastic or other materials and injecting them into a mold under high pressure to form the desired shape. This technique is particularly important for producing precise and durable medical products, including syringes, petri dishes, and implants. Common materials used in medical injection molding include Polypropylene (PP), which is biocompatible and durable; Polycarbonate (PC), known for its transparency and toughness; and Silicone, which offers flexibility and biocompatibility. These materials ensure that medical molding products are safe, reliable, and perform well in critical healthcare environments.
Eco Molding Techniques
As sustainability becomes more important in the manufacturing industry, eco-friendly molding techniques are gaining traction in the production of medical molding products. These processes use sustainable materials and energy-efficient methods, minimizing the environmental impact of production. By integrating recyclable polymers and reducing waste, eco molding techniques help companies meet their environmental responsibilities while maintaining the high standards required for medical products. The use of biodegradable or recyclable materials is particularly important in medical packaging, where sustainability is critical.
Blow Molding and Compression Molding
Blow molding and compression molding are specialized techniques used in the production of hollow medical parts such as bottles, tubes, and containers. Blow molding involves inflating a tube of molten plastic inside a mold to create hollow shapes, making it ideal for items like medical containers and bottles. Compression molding, on the other hand, involves applying heat and pressure to a material inside a mold to create the final product. Both methods offer distinct advantages, including the ability to create lightweight yet durable medical components and packaging.
PET Preform Molding
PET preform molding is a critical technique used in the production of medical packaging. The process involves shaping PET (Polyethylene Terephthalate) into preforms, which are then blown into their final shapes, such as vials or bottles. This technique is widely used for creating medical packaging products that require high strength and durability, including medical vials, bottles, and other healthcare-related packaging products. PET’s inherent properties, such as being lightweight and resistant to chemicals, make it an ideal material for medical molding products, ensuring product integrity and safety for healthcare applications.
These diverse molding techniques are essential in the medical industry, enabling the production of high-quality medical devices and packaging that meet both regulatory standards and patient needs.
Key Players in Medical Molding Products
The medical molding products industry is driven by several key players, each contributing to the innovation, precision, and quality of medical devices and packaging. These companies specialize in advanced molding technologies that ensure the reliability and safety of medical components, such as syringes, surgical instruments, and pharmaceutical packaging.
FUJIU Medical Injection Mold
FUJIU Medical Injection Mold is a global leader in the medical molding products industry, particularly known for its expertise in medical injection molding and pharmaceutical packaging. Our company’s advanced hot runner systems and precision molding technologies have set the standard for high-quality, efficient production of medical devices. FUJIU Medical Injection Mold’s hot runner systems are designed to minimize waste, improve cycle times, and ensure uniformity, which is critical in manufacturing medical components with high precision. FUJIU Medical Injection Mold also plays a pivotal role in producing a range of medical devices, including auto-injectors, pre-filled syringes, and diagnostic devices, all of which require the highest levels of accuracy and reliability. Our company’s commitment to customer success is evident in its ability to offer customized solutions that meet specific regulatory requirements and exceed industry standards.
National Molding Duraflex
National Molding Duraflex is another significant player in the medical molding products market, renowned for its ability to produce high-precision, durable components for the medical industry. National Molding specializes in manufacturing complex medical components, including implants, surgical tools, and drug delivery devices. Their expertise in injection molding and their focus on quality assurance make them a preferred partner for plastic medical device manufacturers seeking precision and dependability. National Molding’s products are designed to meet stringent regulatory standards, ensuring the safety and effectiveness of medical devices in critical healthcare applications. With a focus on material efficiency and production scalability, National Molding has earned a strong reputation for delivering innovative medical molding solutions.
Magor Mold
Magor Mold is a key contributor to the medical molding products industry, particularly in the development of complex, high-performance medical molds used in critical medical applications. Magor Mold’s ability to produce precision medical molds that meet the specific requirements of the medical field has made them a trusted partner for companies in the healthcare industry. The company excels in providing tailored molding solutions for the production of intricate medical devices and components, such as surgical instruments, diagnostic equipment, and drug delivery systems. Magor Mold’s commitment to quality and precision ensures that their medical molding products consistently meet regulatory standards while delivering the durability and performance needed in life-saving applications. Their expertise in high-performance molding processes makes them an essential player in the global medical manufacturing market.
Medical Molding Products: Materials and Their Importance
Selecting the right materials for medical molding products is crucial for ensuring the safety, durability, and performance of medical devices and components. The materials used in medical molding must meet stringent regulatory standards, including biocompatibility and resistance to wear and chemical exposure. The choice of material can impact the functionality, sterilization, and overall lifespan of the product, making it a critical factor in the manufacturing process. By choosing the appropriate materials, manufacturers can create medical devices that are safe for patient use, reliable in performance, and able to withstand the harsh conditions often encountered in medical environments.
Overview of Material Choices
Medical molding materials are carefully selected based on specific criteria such as biocompatibility, strength, and flexibility. Biocompatibility ensures that the material will not cause an adverse reaction when in contact with human tissues or fluids, making it essential for implantable devices and medical components that are exposed to the body. Durability is another key consideration, particularly for devices that must withstand wear and tear or repeated use, such as surgical tools or diagnostic equipment. Furthermore, manufacturers must also consider factors like ease of sterilization, stability under different environmental conditions, and the material’s resistance to chemicals, heat, and UV exposure.
Common Materials in Medical Molding
- Polyetheretherketone (PEEK): PEEK is a high-performance thermoplastic known for its exceptional strength and resistance to harsh conditions, making it ideal for implants and surgical tools. Its biocompatibility and ability to withstand high temperatures and chemicals make it a top choice for applications requiring both durability and safety. PEEK is often used in spinal and orthopedic implants, where long-term reliability is essential.
- Polycarbonate (PC): Polycarbonate is a versatile material used for transparent, tough, and flexible medical devices. It is commonly used for components such as blood collection tubes, syringe barrels, and medical eyewear. Polycarbonate is known for its clarity, allowing for easy visualization of fluids, and its durability, making it a reliable choice for devices that need to be both lightweight and resistant to impact.
- Polypropylene (PP): Polypropylene is a widely used material in medical packaging and devices like syringes and medical containers. Its durability and biocompatibility make it suitable for both single-use items and products that come in contact with bodily fluids. Polypropylene is often chosen for its resistance to chemicals and its ability to maintain structural integrity even after repeated sterilization processes, such as autoclaving.
- Silicone: Silicone is a flexible, inert material that is ideal for soft-touch devices and implants. It is often used for applications such as catheters, surgical gloves, and wound care products. Silicone’s flexibility allows it to conform to the body, making it an excellent choice for products that require both comfort and precision. Its resistance to extreme temperatures and biocompatibility make it suitable for long-term medical applications, including implants and prosthetics.
Each of these materials plays a vital role in the creation of medical molding products. By selecting the most appropriate material for each application, manufacturers can produce medical devices that not only meet stringent safety and performance standards but also ensure patient comfort and device longevity. With the continuous development of new materials and molding technologies, the future of medical molding products looks promising, offering even more innovative solutions for the healthcare industry.
The Role of Technology in Medical Molding Products
Technology plays a vital role in the production of medical molding products, as it directly influences the precision, efficiency, and quality of medical devices and components. With advancements in molding technology, manufacturers can produce complex, high-quality medical products that meet stringent regulatory standards while reducing costs and increasing sustainability. Key technological innovations have significantly enhanced the manufacturing process, ensuring that medical molding products are both reliable and cost-effective.
Precision Molding and Automation
Another key technological advancement in the production of medical molding products is precision molding, which is essential for producing complex medical components with tight tolerances and intricate designs. Precision molding techniques ensure that the final product meets exact specifications, reducing defects and enhancing the reliability of medical devices. This is particularly important in the medical field, where even the smallest defect can lead to product failure and pose significant risks to patient safety.
The integration of automation in the medical injection molding industry has also played a crucial role in maintaining consistency and scalability. Automated molding processes ensure that each medical molding product is manufactured with the same level of precision and quality, regardless of the production volume. Automation also enables manufacturers to meet the high demand for medical products, ensuring that production is both efficient and scalable. With automation, the risk of human error is minimized, and the time required for manufacturing can be reduced, enabling faster time-to-market for medical molding products.
Benefits of Medical Molding Products
The manufacturing of medical molding products offers numerous benefits, which not only improve the quality and functionality of medical devices but also enhance the efficiency of production processes. These benefits encompass regulatory compliance, cost-effectiveness, and sustainability—each playing a vital role in ensuring that medical products meet the highest standards of safety, affordability, and environmental responsibility.
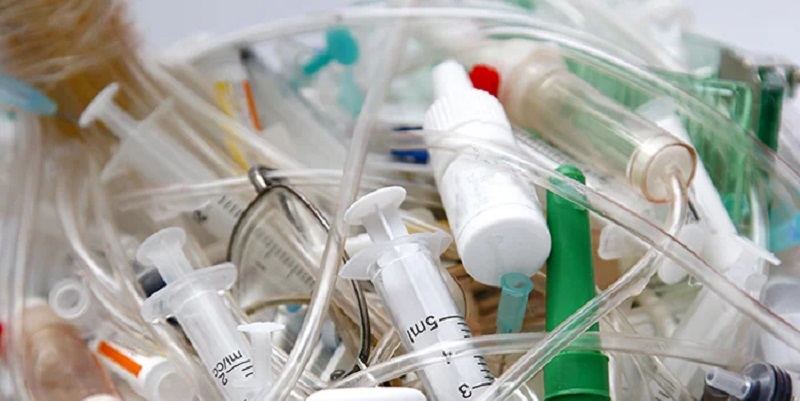
Regulatory Compliance
One of the primary advantages of using medical molding products in the healthcare sector is the ability to meet rigorous regulatory compliance standards. In the medical industry, products must adhere to strict health and safety regulations, such as those set forth by the FDA and other global regulatory bodies. These regulations ensure that medical molding products are safe for patient use and are manufactured in accordance with the highest quality standards.
Medical molding companies implement precise and robust quality control processes to ensure that their products consistently meet these regulatory requirements. For example, during the production of medical molding products, manufacturers conduct thorough testing to verify the biocompatibility and sterilization of components, ensuring that they are safe for use in medical applications. This not only helps in avoiding costly recalls but also promotes patient safety and trust in the products being used in healthcare settings.
Cost-Effectiveness
Another significant benefit of medical molding products is the cost-effectiveness it provides. Medical molding techniques, such as injection molding, allow for high-volume production with minimal labor costs, reduced material waste, and shortened production cycles. As a result, manufacturers can achieve significant cost savings, which is particularly crucial in the competitive healthcare market.
Efficient molding processes also minimize the waste of raw materials, which can otherwise drive up production costs. Moreover, advanced automation and precision molding technologies help reduce human error, leading to fewer defects and rework. This efficiency ultimately contributes to lower production costs, making medical molding products more affordable and accessible to healthcare providers, thereby benefiting patients and the healthcare industry as a whole.
Sustainability
The increasing focus on sustainability in manufacturing has also become a key benefit of medical molding products. Many medical molding companies are incorporating eco-friendly materials and adopting recycling practices to reduce their environmental footprint. For example, using biodegradable polymers or materials that can be recycled reduces waste and the consumption of non-renewable resources.
Additionally, advancements in eco-molding techniques have led to the development of energy-efficient processes that lower energy consumption during production. By reducing carbon emissions and minimizing waste, companies not only contribute to environmental preservation but also align with global efforts to create more sustainable manufacturing practices. This commitment to sustainability ensures that medical molding products are not only effective in their intended medical applications but also support a greener, more sustainable future.
Medical Molding Products: Injection Molding of Medical Products
Precision and Complexity
Injection molding is highly valued for its ability to produce high-precision and complex medical components. Medical devices often require tight tolerances and intricate designs to function properly. Injection molding ensures that each product, whether it’s a syringe, catheter, or surgical tool, is manufactured to the highest standards of accuracy.
Wide Range of Medical Products
The injection molding process is ideal for producing a variety of medical molding products, including syringes, catheters, diagnostic devices, and surgical instruments. This method is particularly effective for injection molding for Class I medical products, as it can produce reliable and cost-effective components that meet the basic requirements for safety and functionality in healthcare settings.
Material Versatility
Injection molding can accommodate a range of medical-grade materials, such as Polypropylene (PP), Polycarbonate (PC), Polyetheretherketone (PEEK), and Silicone. These materials are chosen based on their specific properties such as biocompatibility, flexibility, strength, and resistance to sterilization, ensuring the safety and durability of the final product.
High-Volume Production
One of the key advantages of injection molding is its ability to produce large quantities of medical products quickly and cost-effectively. Once the mold is created, it can be used to produce thousands, or even millions, of identical parts with minimal human intervention. This reduces labor costs and increases production efficiency.
Automation and Reduced Defects
Injection molding of medical products is often highly automated, which reduces the potential for human error and contamination. This automation ensures consistent quality across each product, maintaining high standards of safety and reliability in medical applications.
Regulatory Compliance and Safety
The injection molding process in medical product manufacturing complies with stringent health and safety regulations, including FDA guidelines. The ability to meet these regulations is essential for producing medical molding products that are safe for use in critical medical environments, ensuring patient safety and product efficacy.
Applications of Medical Molding Products in Healthcare
Medical molding products play a vital role in the manufacturing of precision and high-quality medical devices. Using medical-grade plastics, injection molding ensures durability, biocompatibility, and accuracy, meeting the strict standards of healthcare applications.
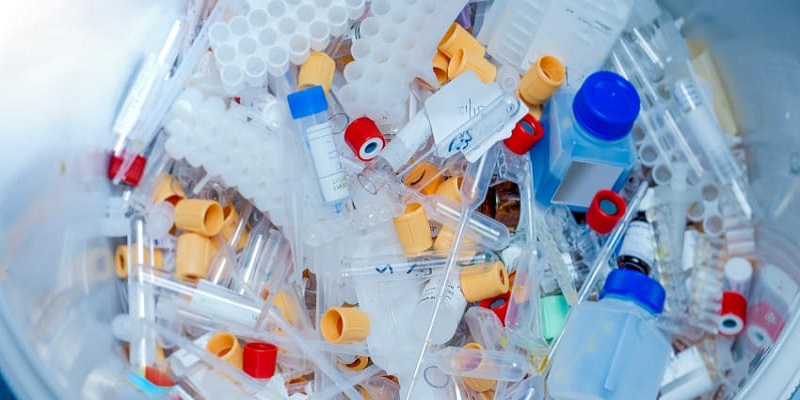
Below are detailed applications:
Infusion/Blood Transfusion Equipment
Medical injection molding is used to produce components for infusion and blood transfusion devices, such as connectors, tubing clamps, and housings. These parts require precision to ensure seamless fluid flow and avoid contamination during medical procedures.
Pipette Tips
Pipette tips are essential for laboratory work, particularly in diagnostic and pharmaceutical research. Injection molding enables the production of precise, uniform tips that ensure accurate liquid handling and compatibility with automated systems.
Blood Collection Tubes
Injection molding is critical for producing durable and airtight blood collection tubes. The process ensures consistent dimensions and high-quality surfaces, which are necessary for accurate sample preservation and analysis.
Swab Tubes
Swab tubes, used for storing diagnostic samples, are made with injection molding to guarantee sterility and structural integrity. The process ensures the tubes are clean, durable, and suitable for sensitive healthcare applications.
Reaction Tubes
Reaction tubes are integral to diagnostic processes and laboratory testing. Injection molding provides the precision required for creating uniform tubes that ensure accurate chemical reactions and reliable results.
Petri Dishes
Petri dishes, commonly used in microbial cultures, require high transparency and smooth surfaces. Injection molding ensures these dishes are manufactured with consistent quality to facilitate clear observations during laboratory tests.
Standard IVD Disposable Supplies
Injection molding is widely applied in producing in-vitro diagnostic (IVD) disposables like trays, casings, and testing components. These products require precision, cleanliness, and high-volume production capabilities to meet clinical demands.
Medical molding products are indispensable in modern healthcare, providing cost-efficient, reliable, and high-precision solutions for both diagnostic and treatment applications.
Essential Capabilities for Producing Medical Molding Products
To produce high-quality medical molding products, manufacturers must possess comprehensive capabilities that ensure precision, safety, and regulatory compliance. Below are the critical capabilities a manufacturer should have:
Class 8 Cleanroom (Class 100,000):
A clean, climate-controlled environment is essential for manufacturing medical devices to prevent contamination and maintain product sterility, meeting industry standards for Class I and Class II devices.
Advanced Molding Services:
Manufacturers should offer specialized molding processes, including precision injection molding, to create durable, biocompatible, and high-quality components for patient use.
Value-Added Services:
These include secondary processes like rotary pad printing (e.g., syringe markings), corona treatment for enhanced adhesion, and automation for consistency and efficiency.
Thermoforming Packaging and Sealing:
Proper packaging ensures medical devices are sterile, protected, and compliant with regulatory guidelines during transportation and use.
Full-Service Tool Room:
A dedicated tool room with advanced capabilities allows for mold maintenance, repair, and optimization, ensuring consistent production quality.
Process Monitoring System:
Real-time monitoring systems guarantee precise control over production, identifying and minimizing defects for reliable medical molding products.
Lean Initiatives and Automation:
Efficiency-driven lean initiatives and automated systems reduce production costs and errors while enhancing product output and consistency.
Level 3 Mold Master Expertise:
Expert mold masters ensure molds are designed and maintained for high performance, critical for producing accurate and consistent medical components.
With these capabilities, manufacturers can produce medical molding products that meet the strictest industry standards, ensuring safety, quality, and reliability for patient care.
Ensuring Quality in the Production of Medical Molding Products
To guarantee the quality of medical molding products, manufacturers must implement rigorous processes and possess advanced capabilities to ensure compliance at every stage of production.
Class 8 Cleanroom Environment:
Manufacturers should operate in a Class 8 cleanroom (Class 100,000) to prevent contamination, ensuring that medical products meet stringent hygiene standards required for patient safety.
Comprehensive Process Monitoring Systems:
Real-time process monitoring systems ensure precise control over temperature, pressure, and molding cycles, reducing errors and maintaining consistency in product quality.
Advanced Molding Capabilities:
Precision injection molding, combined with expert mold maintenance through a Level 3 mold master, guarantees that medical devices meet tight tolerances and exact specifications.
Value-Added Services and Automation:
Automation minimizes human error, ensuring production efficiency and consistency. Additional processes like rotary pad printing and corona treatment enhance product functionality while maintaining compliance.
Lean Initiatives and Full-Service Tool Room:
Lean initiatives streamline operations to eliminate waste and optimize productivity. A full-service tool room ensures molds are regularly maintained and repaired, reducing defects during production.
Thermoforming Packaging and Sealing:
Proper packaging processes ensure that medical molding products remain sterile and protected, complying with Class I and Class II medical device standards.
Climate-Controlled Environment:
A controlled production environment stabilizes critical parameters like humidity and temperature, essential for maintaining material integrity and product precision.
By integrating these capabilities, manufacturers can ensure that each step in the production of medical molding products adheres to strict quality control standards, resulting in safe, reliable, and compliant medical devices for patient use.
Risks of Medical Molding Products and How to Avoid Them
Medical molding products play a critical role in healthcare, but both manufacturers and buyers face risks such as material contamination, precision errors, and regulatory non-compliance. This section outlines these risks, their impact, and practical solutions to mitigate them, ensuring product safety, quality, and reliability.
Risks Faced by Manufacturers
Material Contamination: Using non-compliant or contaminated medical-grade plastics can compromise product safety and biocompatibility.
Solution: Manufacturers must strictly use certified medical-grade materials and implement stringent quality control during production.
Precision Errors: Inaccuracies in molding can lead to defective components, impacting device performance.
Solution: Regular maintenance of molds, automated quality inspection systems, and skilled operators ensure high precision and minimal errors.
Regulatory Non-Compliance: Failure to meet ISO and medical standards can result in product recalls or legal issues.
Solution: Manufacturers must follow ISO standards (e.g., ISO 13485) and operate in cleanroom environments to meet regulatory requirements.
Risks Faced by Buyers
Inferior Quality Products: Buyers may receive poorly manufactured or non-compliant medical molding products, leading to device failures.
Solution: Buyers should source from certified and reputable manufacturers with proven quality assurance processes. Requesting documentation of material and production standards minimizes this risk.
Supply Chain Delays: Unreliable suppliers can disrupt production schedules, delaying critical medical operations.
Solution: Buyers should establish partnerships with manufacturers offering consistent delivery timelines and transparent communication.
By proactively identifying and addressing these risks, manufacturers and buyers can ensure the reliability, safety, and performance of medical molding products.
FAQs about Medical Molding Products
Medical molding refers to the process of manufacturing medical devices, components, or packaging through molding techniques. This involves shaping materials like plastics, metals, and polymers into precise forms that are required for various medical applications. Medical molding is crucial for producing high-quality, durable, and biocompatible products that meet the rigorous standards of the healthcare industry. It is most commonly used to create items such as syringes, surgical instruments, diagnostic devices, and implantable components. The molding process ensures consistency and precision, which are essential for the functionality and safety of medical products. Techniques like injection molding, compression molding, and blow molding are often employed to manufacture medical devices in large volumes with minimal human intervention. These processes are tightly controlled to ensure compliance with regulatory standards such as FDA guidelines to ensure the safety and efficacy of medical devices.
Molding products refer to items that are created through various molding techniques, where materials are shaped into specific forms to produce the final product. These products can range from everyday items like plastic containers and automotive parts to specialized medical devices and pharmaceutical packaging. The molding process involves heating a material until it becomes pliable and then shaping it inside a mold under pressure. Once the material cools, it solidifies into the shape of the mold, ready for use. Common materials used in molding include plastics, metals, silicone, and rubber. The molding technique chosen depends on the type of product being manufactured and the required precision, strength, and durability. Molding products are used across various industries, including automotive, healthcare, electronics, and packaging. For example, medical molding products like syringes, implants, and diagnostic tools are often manufactured using injection molding for their precision and reliability.
In pharmacy, molding is the process of manufacturing pharmaceutical products such as tablet molds, drug delivery devices, and packaging through shaping or molding techniques. This can involve molding solid dosage forms like tablets and capsules, which are created by compressing powdered substances into a mold to form uniform tablets. Molding in pharmacy is also used to create packaging for medications, such as blister packs and bottles, which protect the integrity of the medicine and ensure it is administered in a safe and convenient manner. The molding process in the pharmaceutical industry also extends to the production of medical molding products, like drug delivery devices such as inhalers, syringes, and auto-injectors. These products require precise and consistent molding to meet stringent quality and safety standards. Pharmaceutical molding techniques help reduce production time, ensure scalability, and meet regulatory compliance for safe and effective drug delivery.
An example of molding is the creation of a plastic bottle using injection molding. In this process, plastic resin is heated until it becomes molten and then injected into a mold shaped like a bottle. Once the plastic cools and solidifies, it takes the form of the bottle, ready for packaging and use. Molding is a versatile process that can be used with a wide range of materials, including plastics, metals, and silicone, depending on the intended application. Medical molding products, for instance, include syringes, diagnostic tools, and surgical instruments, which are often manufactured using similar molding processes for precision and reliability. Other examples of molding include the creation of rubber seals, plastic toys, automotive components, and even food packaging. The key benefit of molding is its ability to produce complex shapes with high accuracy, repeatability, and in large quantities, making it ideal for both consumer and industrial products.
Injection molding is a widely used manufacturing process to produce medical molding products due to its precision, efficiency, and scalability. Products include components like surgical instruments, syringe parts, implantable devices, catheters, and diagnostic tools. High-volume items such as blood caps, IV connectors, and housings for medical devices are also created through injection molding. This method allows for the production of complex shapes with consistent quality, ensuring compliance with medical-grade standards. Medical-grade polymers like polyethylene, polycarbonate, and PEEK are commonly used to meet sterility and safety requirements. The process is ideal for producing lightweight, durable, and biocompatible components, which are crucial for healthcare applications. Injection molding excels in meeting the rigorous demands of the medical industry, where precision and hygiene are critical. With its ability to produce intricate and reliable parts at scale, injection molding remains a preferred method for manufacturing high-quality medical products.
Yes, injection molding is highly profitable, particularly in industries like medical manufacturing, where demand for precision and high-volume products is continuous. Medical molding products benefit from the cost efficiency of injection molding, which allows for mass production of components with minimal material waste. While the initial cost of molds can be high, the per-unit cost decreases significantly as production volume increases. This makes injection molding ideal for large-scale production of medical components like syringes, implants, and connectors. Profitability is further enhanced by the process’s ability to maintain consistent quality and precision, reducing the need for rework or rejects. Additionally, medical-grade plastics, though specialized, are often less expensive than metals, increasing margins while maintaining regulatory compliance. For businesses investing in medical molding, injection molding offers a reliable return on investment through efficiency, quality, and scalability, solidifying its position as a profitable manufacturing method.
Molding products are components created through processes like injection molding, compression molding, or blow molding, where molten materials are shaped into specific forms using molds. In the medical industry, molding products include critical devices and components such as catheter tips, drug delivery systems, surgical handles, and implantable devices. These products are often made using medical-grade plastics that meet strict biocompatibility and sterilization standards. Injection molding specifically allows for the creation of complex, precise parts required for healthcare applications. Molding products offer high durability, accuracy, and uniformity, making them ideal for large-scale production. They play a vital role in ensuring the reliability of medical equipment, tools, and devices used in life-saving treatments. With technological advancements, molding techniques now produce intricate components that meet the stringent demands of the medical field, offering a versatile solution for creating functional, safe, and high-quality medical products.
While 3D printing offers advantages like rapid prototyping and customization, injection molding remains superior for producing medical molding products at scale. Injection molding is better suited for high-volume production due to its lower per-unit cost and ability to produce consistent, precise components. Medical devices like syringes, surgical tools, and connectors require high accuracy and biocompatibility, which injection molding delivers efficiently. In contrast, 3D printing is slower and less cost-effective for mass production, though it excels in creating prototypes, custom implants, or limited-run products.
Injection molding ensures the use of medical-grade materials that meet regulatory standards, making it more reliable for producing components in healthcare. While 3D printing is innovative and flexible, it cannot match the speed, scalability, and long-term cost-effectiveness of injection molding for mass-produced medical devices. Both methods have their place, but injection molding remains the gold standard for precision and high-volume medical products.
Contact our professional team now for a same-day quote and risk-free project evaluation. Benefit from ISO 8 cleanrooms, advanced machines, and 12-hour fast response in medical injection molding.