Medical plastic parts play a pivotal role in modern healthcare, supporting the production of essential items like syringes, infusion sets, and diagnostic tools. As the demand for reliable and affordable solutions grows, China medical plastic parts have become a preferred choice for businesses worldwide. Renowned for their cost-effectiveness and capacity for high-volume production, Chinese manufacturers deliver exceptional quality while adhering to strict international standards such as ISO 13485 and GMP certifications. With advanced facilities, including cleanroom injection molding and precision machining, China stands out as a global leader in this industry. By leveraging innovative technologies and maintaining competitive pricing, China precision medical components continue to drive advancements in medical devices and healthcare solutions on a global scale. FUJIU Medical Injection Mold delivers affordable, high-quality china medical plastic parts for healthcare, offering custom solutions and competitive pricing.
Low-Volume to High-Volume Production Capabilities

Attributes | Details |
---|---|
Place of Origin | Dongguan, Guangdong, China |
Brand Name | LY Medical Injection Mold |
Product Name | China Medical Plastic Parts |
Molding Mode | Plastic Injection |
Product Material | Plastic |
Color | Customized |
Size | Customized |
Length | Customized |
Style | Customized |
Service | OEM ODM |
Processing Services | Broaching, Drilling, Milling, Other Processing Services, Turning, Rapid Prototyping |
Features | High Precision |
Logo | Customized Logo Acceptable |
Supplier | Manufacturer |
Design Software | 2D/3D/CAD/DWG//STEP/PDF/UG |
Surface Treatment | Customer Requirement |
Quality Control | 100% Inspection |
Minimum Order Quantity | Small Order Accepted |
Packing Details | Outer Packaging Carton Inner Packaging According to Customer Requirement |
Port | According to Your Requirement |
Key Characteristics of China Medical Plastic Parts
China’s medical plastic parts industry is a cornerstone of global healthcare, offering high-quality, cost-effective, and customizable solutions. Leveraging advanced manufacturing techniques and strict compliance with international standards, Chinese manufacturers deliver medical components that cater to diverse needs in the healthcare sector. From disposable syringes to complex surgical instruments, these products are characterized by their durability, precision, and adaptability. Below is a detailed exploration of the key characteristics that define China’s medical plastic parts, categorized into quality standards, customization, manufacturing techniques, compliance, and affordability.
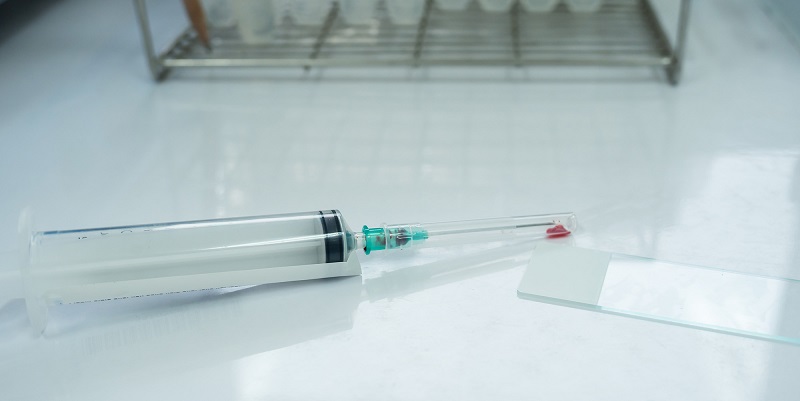
High-Quality Standards
China’s medical plastic parts are renowned for their adherence to international quality certifications, ensuring reliability and safety. The use of durable materials and rigorous quality checks further solidify their reputation for excellence.
- China medical plastic parts consistently meet international certifications such as ISO 13485, GMP, and ISO 9001, ensuring their safety and reliability for healthcare applications.
- Manufacturers prioritize the use of durable, medical-grade materials like polypropylene, PVC, and ABS, making these components suitable for demanding medical environments.
- Many providers of china plastic medical parts also perform rigorous quality testing to guarantee performance and longevity.
Customization Options
Chinese manufacturers provide extensive customization capabilities, enabling the development of medical parts tailored to specific client needs, from disposable items to complex instruments.
- The availability of OEM and ODM services ensures that china plastic injection molding medical parts can be tailored to meet diverse client requirements.
- Manufacturers offer adaptability for producing disposable medical items like syringes and more complex equipment such as surgical instruments and diagnostic devices.
- Custom designs allow china plastic medical parts to align with specific industry needs, including size, functionality, and material preferences.
Advanced Manufacturing Techniques
Chinese manufacturers employ state-of-the-art technologies to ensure precision, hygiene, and efficiency in the production of medical plastic parts.
- Leading manufacturers of china medical plastic parts utilize cutting-edge methods such as cleanroom injection molding, which ensures precision and hygiene for critical medical components.
- Techniques like precision CNC machining and 3D printing enhance production efficiency and accuracy, reducing waste while maintaining high standards.
- The integration of rapid prototyping allows for quick adjustments during product development, making china plastic injection molding medical parts an ideal choice for fast-paced healthcare markets.
Compliance with International Standards
Chinese medical plastic part manufacturers strictly adhere to international regulations and sustainability practices, guaranteeing safety and eco-friendliness.
- Beyond certification, manufacturers implement strict production protocols to ensure that china medical plastic parts align with global regulatory requirements.
- Many suppliers of china plastic medical parts also emphasize sustainability, adopting eco-friendly practices while maintaining product integrity.
Cost-Effective Solutions
The competitive pricing of Chinese medical plastic parts makes them accessible without compromising on quality, offering a valuable balance for healthcare providers worldwide.
- The competitive pricing of china plastic injection molding medical parts makes them accessible to both startups and established healthcare companies.
- Bulk production capabilities, coupled with advanced technologies, allow manufacturers to offer high-quality products without compromising affordability.
Top Manufacturers for China Medical Plastic Parts
China has emerged as a leading provider of high-quality and cost-effective medical plastic parts, supported by a range of top-tier manufacturers. These companies specialize in producing components for disposable syringes, wound care items, diagnostic tools, and sterile packaging. By integrating advanced manufacturing techniques, customization options, and compliance with global standards, Chinese manufacturers cater to the diverse needs of the healthcare industry.
FUJIU Medical Injection Mold
FUJIU Medical Injection Mold is a trusted manufacturer specializing in precision manufacturing for products like syringes, wound care items, and sterile packaging. Our company stands out for its fast delivery, competitive pricing, and adherence to international standards.
- We are a trusted provider of china medical plastic parts, excelling in high-precision manufacturing for products like syringes, wound care items, and sterile packaging.
- Known for fast delivery (within 15 workdays) and competitive pricing, we offers solutions tailored for both large-scale healthcare providers and small distributors.
- Our company’s expertise in china plastic injection molding medical parts ensures compliance with ISO and GMP standards, catering to international market needs.
Dongguan Yixun Industrial Co., Ltd.
Dongguan Yixun Industrial Co., Ltd. specializes in manufacturing durable and precise medical plastic components and molds. The company is known for its flexibility, quick response times, and customized production capabilities.
- This manufacturer stands out for producing china plastic medical parts, focusing on plastic components and precision medical molds with high durability.
- Dongguan Yixun offers flexible MOQs and quick response times (≤3 hours), making it a reliable partner for customized production.
- Their services also include OEM and ODM capabilities, ensuring china plastic injection molding medical parts are crafted to client specifications.
Leading China Medical Plastic Parts Manufacturer: Features and Benefits
China’s medical plastic parts manufacturers emphasize high-quality production and cost efficiency, combining advanced technology and expertise to support global healthcare needs.
- As a china medical plastic parts manufacturer, companies in this industry emphasize high-quality production and cost efficiency.
- These manufacturers integrate state-of-the-art technology, including cleanroom injection molding and precision plastic medical parts machining, ensuring that their products meet stringent industry standards.
- The ability to handle bulk orders while maintaining precision makes them a preferred choice for china plastic medical parts and china plastic injection molding medical parts worldwide.
Why Choose a China Medical Plastic Parts Manufacturer?
Choosing a China-based medical plastic parts manufacturer ensures access to diverse expertise, advanced customization, global certifications, and cost-effective production solutions.
- Expertise in Diverse Medical Components
- Includes disposable syringes, infusion sets, and diagnostic tools.
- Advanced Customization Options
- Offers tailored solutions for unique healthcare needs, from design to prototyping.
- Global Certifications
- Compliance with ISO 13485, GMP, and other international regulations ensures product safety and reliability.
- Affordable Production
- Competitive pricing for china plastic injection molding medical parts, making it ideal for businesses aiming to minimize costs without sacrificing quality.
These manufacturers provide dependable and high-quality china medical plastic parts, leveraging advanced technology and cost-effective methods to support the global healthcare industry.
Benefits of Choosing Chinese Manufacturers for China Medical Plastic Parts
China Medical Micro Plastic Injection Parts
Cost Efficiency
- Chinese manufacturers offer highly competitive pricing for china medical plastic parts, making them an ideal choice for businesses looking to minimize production costs.
- By requesting medical plastic parts quotes, companies can gain a better understanding of the price ranges and evaluate cost-saving opportunities for bulk production.
- With the ability to scale production for bulk orders, costs are reduced significantly while maintaining consistent quality.
Global Standards Compliance
- Manufacturers of china medical plastic parts adhere to strict international standards, including ISO 13485, GMP, and ISO 9001, ensuring their products are safe and reliable.
- This compliance makes their products suitable for export to markets across the globe, meeting diverse regulatory requirements.
Rapid Prototyping and Production
- Chinese suppliers excel in providing fast turnaround times for both prototyping and mass production of china medical plastic parts.
- Advanced technologies like 3D printing and CNC machining streamline the development process, ensuring quick delivery without compromising on quality.
Versatility in Applications
- China medical plastic parts are used in a wide range of healthcare applications, including disposable items like syringes and precision components for surgical tools.
- This versatility enables manufacturers to cater to varied client requirements, from large hospitals to small clinics.
Advanced Manufacturing Capabilities
- Technologies such as cleanroom medical injection molding, automated assembly lines, and precision engineering are standard in the production of china medical plastic parts.
- These advanced methods ensure consistent quality and hygiene, crucial for medical applications.
Customization and Flexibility
- OEM and ODM services allow for customized solutions tailored to specific healthcare needs, whether it’s disposable syringes or diagnostic equipment.
- Many manufacturers of china medical plastic parts offer personalized designs to meet client specifications efficiently.
Reliable Supply Chains
- Chinese manufacturers maintain robust supply chains, ensuring the timely delivery of china medical plastic parts even for large-scale orders.
- This reliability minimizes the risk of disruptions, which is critical in the healthcare sector.
China Medical Plastic Parts Wholesale Injection Molding of Atomization Mask
Key Features of China Wholesale Injection Molding of Medical Atomization Mask
- Chinese manufacturers excel in china wholesale injection molding of medical atomization mask, producing high-quality masks for respiratory care.
- Advanced injection molding techniques ensure that each mask meets stringent hygiene and safety standards required for medical use.
- The ability to produce in bulk makes china wholesale injection molding of medical atomization mask an economical choice for global healthcare markets.
Benefits of Choosing China Wholesale Injection Molding of Medical Atomization Mask
- High Production Efficiency
- Manufacturers can handle large-scale orders with quick turnaround times.
- Compliance with Global Standards
- Masks produced adhere to ISO and GMP regulations, ensuring reliability.
- Cost-Effective Solutions
- Affordable pricing for china wholesale injection molding of medical atomization mask without compromising quality.
- Customization Options
- OEM and ODM services allow clients to design masks tailored to specific requirements.
By choosing Chinese manufacturers, businesses can access high-quality, affordable china medical plastic parts and specialized products like atomization masks to meet the growing demands of the healthcare industry.
Applications of China Medical Plastic Parts
Disposable Medical Devices
- China medical plastic parts are widely used in disposable medical devices such as syringes, IV catheters, and infusion sets.
- These components are manufactured with precision using medical-grade materials like polypropylene and PVC to ensure patient safety and single-use hygiene standards.
- Bulk production capabilities enable manufacturers to supply high-demand items at competitive prices for global healthcare markets.
Surgical Instruments and Tools
- Manufacturers of china medical plastic parts play a vital role in producing advanced surgical tools, including ligating clips, blood transfusion kits, and endoscopic instruments.
- These tools require meticulous design and precision, which is achieved through cutting-edge techniques like injection molding and CNC machining.
- Plastic parts used in surgical applications are lightweight, durable, and resistant to sterilization processes, making them essential for modern operating rooms.
Diagnostic and Lab Equipment
- Diagnostic tools such as test tubes, pipette tips, and cryo vials depend on the durability and accuracy of china medical plastic parts.
- Plastic components ensure reliability in laboratory environments where precision is critical for accurate results.
- The adaptability of plastic molding processes allows manufacturers to produce parts in various sizes and specifications, meeting the diverse needs of diagnostic labs and research facilities.
Hospital Furniture Components
- China medical plastic parts are integral to hospital furniture, including fittings for hospital beds, IV stands, and medical carts.
- These plastic components offer lightweight durability, corrosion resistance, and easy sterilization, ensuring long-term usability in healthcare settings.
- Manufacturers focus on ergonomic designs and high-quality materials to enhance functionality and comfort for both patients and healthcare providers.
Additional Applications of China Medical Plastic Parts
- Drug Delivery Systems
- Components for inhalers, auto-injectors, and insulin pens.
- Packaging for Sterile Products
- Blister packs and vials made from specialized plastics to preserve sterility.
- Rehabilitation Equipment
- Lightweight plastic parts used in wheelchairs, braces, and crutches.
By addressing a wide range of applications, china medical plastic parts continue to advance the efficiency and accessibility of healthcare solutions worldwide.
Tips for Importing China Medical Plastic Parts
Research Reliable Suppliers
- Look for reputable manufacturers of china medical plastic parts by exploring online platforms, trade directories, and industry exhibitions.
- Prioritize suppliers with certifications like ISO 13485 and GMP to ensure compliance with international medical standards.
- Consider third-party reviews or referrals from industry professionals to validate the credibility and performance history of the supplier.
Request Samples
- Before placing bulk orders for china medical plastic parts, request product samples to evaluate their quality, durability, and compliance with your specifications.
- Conduct thorough testing of the samples, focusing on factors like material strength, functionality, and finish to ensure they meet your expectations.
- Samples can also help identify potential issues early, reducing risks in large-scale production.
Import Regulations
- Familiarize yourself with your country’s import regulations regarding china medical plastic parts, including customs duties, documentation, and medical device registration requirements.
- Ensure that the products meet local standards for medical devices, such as FDA approval for the U.S. or CE marking for the European market.
- Work with a reliable freight forwarder or customs broker to streamline the import process and avoid unnecessary delays.
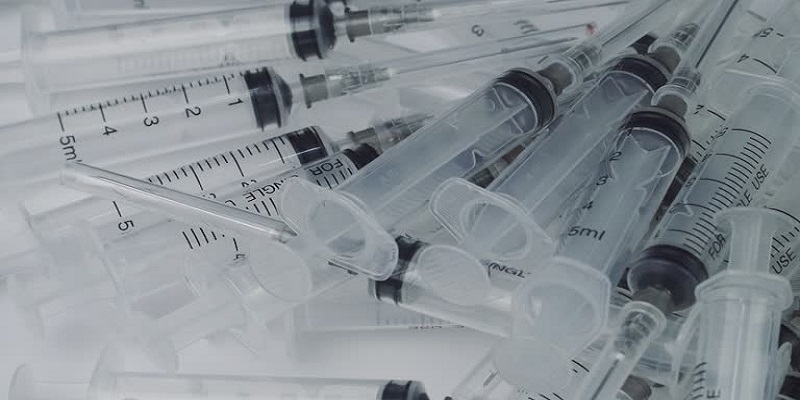
Importance of Medical Injection Molding Technology in the Production of China Medical Plastic Parts
Medical injection molding technology plays a pivotal role in the production of China medical plastic parts, enabling manufacturers to meet the high standards of precision, durability, and scalability demanded by the healthcare industry. By utilizing this advanced manufacturing process, Chinese companies can produce a wide range of reliable and cost-effective medical devices and components. Below, we explore the key benefits and applications of medical injection molding in this sector, categorized into control and reliability, high-volume production, housing solutions, and the versatility of medical devices.
Provides Control and Reliability
Medical injection molding is a highly controlled and reliable process, ensuring the consistent production of high-quality plastic medical parts. Its advanced capabilities streamline production and optimize performance.
Medical injection molding utilizes advanced modeling software that eliminates guesswork in mold design. This precision allows moldmakers to adjust parameters efficiently, ensuring optimal performance for each batch. The process’s stability is ideal for manufacturing critical medical components that require uniformity and accuracy. Furthermore, the technology reduces production lead times, enabling manufacturers to meet tight deadlines while maintaining quality. In China, where manufacturers often operate on a large scale, this combination of control and efficiency is crucial to staying competitive in global markets.
High-Volume Production
Medical injection molding is particularly well-suited for high-volume production, making it an economical choice for manufacturing large quantities of medical plastic parts.
Creating complex medical products through injection molding requires significant upfront investment in mold design and development. However, once the mold is finalized, manufacturers can produce thousands of identical parts quickly and efficiently. This scalability allows Chinese companies to amortize tooling costs over large production runs, reducing the price per piece. As a result, high-volume production becomes cost-effective, making it possible for Chinese manufacturers to deliver affordable yet high-quality medical plastic parts to global clients.
Ideal Housing Solution
Medical injection molding is the preferred method for creating housings and enclosures for medical devices due to its speed, efficiency, and cost-effectiveness.
Unlike other manufacturing methods, injection molding uses less raw material and operates at a lower cost per part, especially for large production runs. This makes it the ideal choice for creating housings, shells, and enclosures for medical devices. The process supports the use of medical-grade plastics that offer durability, chemical resistance, and biocompatibility. Furthermore, the ability to produce parts with faster cycle times ensures that manufacturers can meet high demand without compromising quality. In China, where medical device production is a major industry, injection molding enables the efficient production of housings for devices ranging from diagnostic tools to surgical instruments.
Versatility of Medical Devices
Medical injection molding allows for the use of diverse resins, enabling the production of versatile and specialized medical devices tailored to various needs.
A key advantage of injection molding is its compatibility with a wide range of plastic resins. These resins can be selected based on their specific properties, such as thermal stability, biocompatibility, chemical resistance, biodegradability, strength, and lightweight characteristics. This versatility allows manufacturers to customize medical parts for specific end-user requirements and environmental conditions. In China, the availability of cost-effective, high-quality resins enables the production of a broad spectrum of medical components, from disposable syringes to complex implants, catering to both domestic and international markets.
Medical injection molding technology is indispensable in the production of China medical plastic parts, offering unparalleled precision, scalability, and versatility. Its ability to produce high-quality components efficiently and affordably positions Chinese manufacturers as leaders in the global medical device industry. By leveraging advanced molding techniques, these manufacturers can meet the evolving demands of the healthcare sector while maintaining strict compliance with international quality standards.
Factors to Consider When Selecting China Medical Plastic Parts Manufacturers
Choosing the right China medical plastic parts manufacturer is a critical decision that can significantly impact the success of your project. From ensuring production capacity to guaranteeing quality and design expertise, several key factors must be evaluated to find the best fit for your needs. Below, we delve into the essential considerations for selecting a reliable medical plastic parts supplier, categorized into production capacity, range of services, design expertise, applications, technology, and quality assurance.
Production Volume and Capacity
The production capacity of a manufacturer determines their ability to meet your project’s volume requirements while maintaining quality and efficiency.
When evaluating manufacturers, consider their expertise in medical plastic injection molding and the quality of raw materials used. High-quality plastic materials ensure the durability and reliability of medical devices and consumables. Manufacturers with scalable production capacity can handle varying project sizes, making them ideal partners for both small-batch prototypes and large-scale production runs. Assessing their ability to manage your specific volume needs helps avoid delays and ensures consistent supply.
Provide a Range of Services
A manufacturer offering comprehensive services simplifies the production process by handling everything from initial design to final production.
Choosing a supplier that provides one-stop solutions can streamline your project. Look for companies that assist with part design, prototyping, and mold flow analysis. These services help optimize designs for manufacturability and cost efficiency. Such manufacturers can guide you through every stage of production, ensuring that your medical plastic parts meet your expectations and budget constraints.
Experienced Design Team
An experienced design team is crucial for creating high-quality medical plastic parts and maximizing the efficiency of the manufacturing process.
The design phase is critical in determining the functionality, aesthetics, and cost of medical plastic parts. Manufacturers with skilled design teams can collaborate with you during the early stages of production, ensuring your goals are met while minimizing waste. Their expertise contributes to better part performance, reduced material usage, and an improved return on investment (ROI). Selecting a manufacturer with a robust design team ensures smoother development and production workflows.
Applications for All Products
Manufacturers must have the expertise to recommend the right materials and processes for various medical applications, ensuring optimal performance and cost efficiency.
Medical device injection molding companies should help clients choose suitable plastic resins based on the product’s end use and budget. By understanding the unique requirements of your medical applications, they can guide you in selecting materials with properties like biocompatibility, chemical resistance, or durability. Their ability to support different stages of manufacturing ensures that each product meets its intended purpose effectively.
Specifications and Technology
Advanced technology and adherence to specifications are essential for producing precise medical plastic parts that meet industry standards.
The ideal manufacturer should have the experience and technical capabilities required to produce parts according to your exact specifications. They must provide guidance throughout the process and make recommendations for achieving optimal results. Companies equipped with state-of-the-art technology, such as cleanroom injection molding and precision machining, can ensure high-quality outputs. Their knowledge and technical infrastructure are critical for delivering reliable and accurate components.
Internal Quality Assurance
A mature internal quality assurance system ensures the consistency, safety, and compliance of medical plastic parts.
Quality assurance is vital for ensuring that medical plastic parts meet industry standards and perform reliably. Manufacturers with robust quality assurance processes can monitor production to prevent defects and ensure consistency. Companies with ISO certifications and a strong reputation for quality are preferable. Conducting a background check on the manufacturer’s track record and certifications helps verify their ability to deliver guaranteed results. Efficient quality control processes contribute to better outcomes and long-term partnerships.
Selecting a China medical plastic parts manufacturer requires careful evaluation of their production capacity, service offerings, design expertise, and quality assurance practices. By considering these factors, you can identify a partner capable of meeting your project’s needs with precision and reliability. A well-chosen manufacturer will contribute to the success of your medical plastic parts, ensuring high-quality, cost-effective, and timely production.
Commonly Used Medical Plastic Types in the Production of China Medical Plastic Parts
The production of China medical plastic parts relies on a variety of specialized plastics to meet the rigorous demands of the healthcare industry. These materials are selected for their biocompatibility, durability, and ability to withstand sterilization processes, among other properties. Below, we explore the most common types of medical plastics used in the production of China medical plastic parts, as well as additional materials that find widespread use in the medical field. This overview covers their unique properties, applications, and suitability for specific medical needs, providing a comprehensive guide to understanding medical plastic materials.
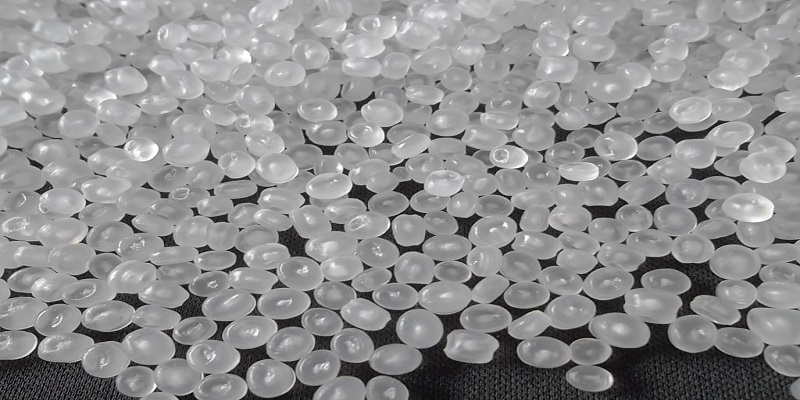
Common Types of Medical Plastics in China Medical Plastic Parts
The most frequently used medical plastics in China are selected for their ability to meet stringent international standards while providing cost-effective solutions for diverse medical applications.
Polypropylene (PP):
Polypropylene is widely used in disposable medical devices, such as syringes, specimen containers, and IV bottles. It offers excellent chemical resistance, lightweight properties, and high durability. Its ability to withstand autoclaving and other sterilization processes makes it indispensable in the healthcare industry.
Polyvinyl Chloride (PVC):
PVC is one of the most versatile plastics in the medical field, commonly used for tubing, blood bags, and catheters. Its flexibility and ability to be easily sterilized make it ideal for applications that require close patient contact. Medical-grade PVC is also phthalate-free, ensuring patient safety.
Acrylonitrile Butadiene Styrene (ABS):
Known for its toughness and impact resistance, ABS is used in medical device housings, surgical instruments, and enclosures. It is favored for its strength and ability to be molded into complex shapes while maintaining dimensional stability.
Polycarbonate (PC):
Polycarbonate is a transparent, impact-resistant plastic used in devices like oxygenators, blood reservoirs, and syringes. It combines optical clarity with high strength, making it ideal for precision medical applications.
High-Density Polyethylene (HDPE):
HDPE is a durable plastic used in containers, medical packaging, and tubing. It provides excellent resistance to chemicals and moisture, making it suitable for sterile environments.
Other Commonly Used Medical Plastic Types
Beyond the core materials used in China medical plastic parts, other plastics play a vital role in specialized medical applications, offering unique properties that address specific healthcare challenges.
Polytetrafluoroethylene (PTFE):
Commonly known as Teflon, PTFE is highly resistant to chemicals and heat. It is used in medical tubing, surgical grafts, and implants due to its non-reactive and biocompatible nature.
Medical-Grade Silicone:
Silicone is a biocompatible material often used for implants, catheters, and sealants. It is flexible, hypoallergenic, and can withstand both extreme temperatures and sterilization methods, making it highly versatile.
Polyethylene Terephthalate (PET):
PET is a strong, lightweight material used in diagnostic equipment, packaging, and disposable medical products. It is also valued for its recyclability, contributing to sustainable medical manufacturing.
Polyetheretherketone (PEEK):
PEEK is a high-performance thermoplastic used in medical implants and devices requiring exceptional strength, heat resistance, and chemical stability. It is increasingly popular in orthopedic and dental implants.
Polyurethane (PU):
PU is used in medical tubing, wound dressings, and adhesives. Its flexibility and ability to mimic natural tissue properties make it suitable for wearable medical devices and prosthetics.
Factors Influencing Material Selection in Medical Plastics
The choice of medical plastic depends on various factors, including the application, required properties, and regulatory compliance.
Manufacturers of China medical plastic parts consider properties like biocompatibility, chemical resistance, sterilization compatibility, and mechanical strength when selecting materials. Cost efficiency, ease of processing, and adherence to international certifications like ISO 10993 also play critical roles in material selection. The availability of advanced materials allows for the development of safe, durable, and innovative medical products.
The production of China medical plastic parts involves a wide range of high-performance plastics, each tailored to meet the unique demands of the medical industry. From commonly used materials like polypropylene and PVC to specialized options like PEEK and medical-grade silicone, these plastics enable the creation of reliable, cost-effective, and safe medical devices. Understanding the properties and applications of these materials is essential for selecting the right plastic for specific healthcare needs, ensuring compliance and quality in medical manufacturing.
China Medical Plastic Parts Production Process Steps
The production of China medical plastic parts follows a meticulous, multi-step process designed to meet the strict demands of the healthcare industry. Each phase integrates advanced technologies, rigorous quality standards, and precision engineering to deliver reliable, biocompatible medical components. From initial product design to final surface treatment, every step plays a critical role in ensuring the production of high-quality medical parts. Below, we outline the key steps in the production process, highlighting their significance and methodologies.
Product Design
The product design phase involves working closely with customers to develop and refine technical drawings, ensuring compliance with medical standards and optimizing manufacturability. This foundational step sets the stage for all subsequent processes.
- Collaborate with clients to create 2D and 3D design files tailored to their specific requirements.
- Ensure designs align with stringent healthcare regulations, focusing on functionality, durability, and precision.
- Optimize technical drawings for manufacturability, reducing production challenges and costs.
- Typical projects include the design of surgical instruments, diagnostic devices, and disposable medical items.
Mold Design
Custom mold design is crucial for producing precise medical plastic parts. This step uses advanced modeling tools to optimize the mold structure for efficient and consistent manufacturing.
- Utilize 3D modeling software and simulation tools, including Moldflow analysis, to design molds.
- Focus on optimizing gating systems, cooling channels, and overall mold structure to ensure even material flow and quality.
- Provide tailored solutions for a range of medical products, such as syringes, implants, and diagnostic tools.
Mold Manufacturing
High-precision molds are manufactured using state-of-the-art machining techniques, ensuring dimensional accuracy and durability for the injection molding process.
- Use advanced machining technologies, including milling, turning, wire cutting, and EDM, to create molds.
- Ensure tight tolerances and smooth surface finishes to enhance the quality of molded medical parts.
- Molds are specifically designed to support large-scale production while maintaining consistent results.
Custom Injection Molding
Injection molding forms the core of the production process, producing medical-grade plastic parts with high precision and consistency in a cleanroom environment.
- Utilize biocompatible materials like PC, PEEK, and LCP to ensure safety and performance.
- Manufacture parts in a contamination-free cleanroom to meet the hygiene requirements of the medical industry.
- Applications include medical device housings, diagnostic equipment components, and disposable medical products.
Rapid Prototyping
Rapid prototyping accelerates the development process by enabling quick creation of concept models and functional prototypes, supporting innovation and iteration.
- Use technologies like 3D printing and CNC machining to produce prototypes with precision.
- Create prototypes in various materials to meet the needs of different medical projects.
- Support a wide range of CAD file formats to facilitate seamless integration with customer designs.
3D Printing
3D printing provides a flexible, cost-effective solution for low-volume production and prototyping of medical-grade plastic parts with complex geometries.
- Manufacture parts with intricate details, customized textures, and fine finishes.
- Process a variety of materials to meet the specific requirements of different medical applications.
- Ideal for producing specialized or unique medical components.
CNC Machining
CNC machining ensures the precise production of mold components and medical device parts, meeting the high standards of the healthcare industry.
- Perform advanced operations like shaft machining, wire cutting, and EDM to create mold cavities, cores, and inserts.
- Produce surgical tools, implants, and other medical device parts with exceptional accuracy.
- Comply with AS9100 and other industry certifications for quality and safety.
Surface Treatment
Surface treatment processes enhance the quality, durability, and functionality of medical devices, ensuring they meet specific requirements for their applications.
- Provide polishing, anodizing, and passivation services for a wide range of medical devices.
- Ensure surface finishes meet the standards for surgical instruments, implants, and diagnostic tools.
- Tailor treatments to improve aesthetics, corrosion resistance, and overall performance.
The production of China medical plastic parts involves a systematic approach, combining innovation, precision, and quality assurance at every step. From product design to surface treatment, each phase contributes to creating reliable and cost-effective medical components. By leveraging advanced technologies like rapid prototyping, 3D printing, and CNC machining, manufacturers in China deliver high-quality solutions tailored to meet the evolving needs of the global healthcare industry.
FAQs about China Medical Plastic Parts
Medical-grade plastic is made from high-purity polymers such as polypropylene (PP), polyethylene (PE), polycarbonate (PC), and polyetheretherketone (PEEK). These materials are chosen for their biocompatibility, sterilization compatibility, and mechanical strength. In China, manufacturers often use these materials to produce precise and high-quality medical parts, adhering to global standards like ISO 10993 and USP Class VI.
Polyetheretherketone (PEEK) and polycarbonate (PC) are highly regarded in medical applications due to their exceptional strength, chemical resistance, and biocompatibility. For disposable components, polypropylene (PP) and polyethylene (PE) are preferred. Chinese manufacturers frequently optimize material choice based on the application, ensuring compliance with regulatory standards.
Medical-grade plastics are designed to minimize degradation and particle release. However, under certain mechanical stress or prolonged use, microplastics may be released. Chinese manufacturers are addressing this concern through stringent testing and advanced material formulations to ensure safety.
Medical grade silicone is a non-toxic, biocompatible material commonly used in medical devices. Unlike conventional plastics, silicone is an elastomer with a stable molecular structure, making it highly resistant to degradation. When used properly, medical grade silicone does not release microplastics, as it does not break down into smaller fragments like traditional plastics.
For China’s medical plastic parts industry, silicone is widely utilized in products like catheters, seals, and implants due to its durability and stability. Manufacturers often adhere to stringent quality control measures to ensure the silicone used meets international medical standards. However, during manufacturing or improper disposal, there is potential for environmental contamination, so sustainable practices are encouraged. China’s advancements in medical-grade silicone production are focused on reducing waste and improving environmental safety, reflecting a growing global commitment to eco-friendly practices.
High-density polyethylene (HDPE) is indeed used in medical devices, particularly for its strength, lightweight nature, and chemical resistance. In the context of China’s medical plastic parts industry, HDPE is a material of choice for items like disposable syringes, tubing, and containers for storing medical samples.
HDPE’s non-toxic properties and ability to withstand sterilization make it suitable for medical applications. Manufacturers in China typically follow ISO and FDA regulations when producing HDPE medical components, ensuring their safety and reliability for healthcare settings. Additionally, HDPE’s recyclability contributes to reducing waste in the medical field. While HDPE is not as flexible as other plastics like silicone, its low cost and durability make it invaluable in disposable and reusable medical devices, underlining its importance in the global medical supply chain.
Medical grade plastics are recyclable, but their recyclability depends on the type of plastic and whether it is contaminated. Common materials such as polypropylene (PP), polyethylene (PE), and polycarbonate (PC) are used in medical devices and are recyclable under controlled conditions. In China’s medical plastic parts industry, efforts are being made to implement recycling programs for non-contaminated plastics.
The challenge lies in handling biohazardous waste. Medical plastics that come into contact with bodily fluids or hazardous substances require specialized disposal methods, limiting their recyclability. However, advancements in China’s waste management systems are opening opportunities to recycle non-contaminated medical-grade plastics, such as packaging and protective equipment. Innovative recycling technologies and strict regulatory frameworks ensure that recyclable materials are handled safely while minimizing environmental impact.
Medical grade plastics are designed to meet stringent safety standards for use in healthcare. These materials, such as polycarbonate, polyethylene, and medical-grade silicone, undergo rigorous testing for biocompatibility, sterilization resistance, and durability. In China, the production of medical plastic parts follows global standards such as ISO 10993 to ensure patient safety.
The safety of medical-grade plastics makes them ideal for applications ranging from surgical instruments to drug delivery systems. Manufacturers in China prioritize quality control, using cleanroom environments to minimize contamination during production. However, the safety of medical plastic parts also depends on proper usage, sterilization, and disposal. By adhering to regulatory guidelines, China’s medical plastics industry contributes to global healthcare solutions without compromising patient or environmental safety.
Medical grade resin is safe for use in healthcare applications, provided it complies with biocompatibility and regulatory standards. In China, manufacturers of medical plastic parts use resins such as polypropylene, polyethylene, and polycarbonate to create a wide range of products, including syringes, IV components, and diagnostic tools.
These resins are engineered to withstand sterilization methods like autoclaving and gamma radiation. Compliance with global safety standards such as ISO 13485 ensures that medical-grade resins do not leach harmful substances or cause adverse reactions. China’s medical plastics industry also emphasizes material traceability and quality assurance to maintain safety. However, improper handling or recycling of resin-based products can pose environmental risks, highlighting the need for sustainable practices in manufacturing and disposal.
Medical grade silicone is not classified as a plastic but as an elastomer—a flexible, rubber-like material made from silica. Unlike traditional plastics, silicone has a unique molecular structure that gives it superior durability, biocompatibility, and resistance to temperature extremes.
In China’s medical plastic parts industry, medical-grade silicone is used extensively in products such as catheters, implants, and seals due to its non-toxic and hypoallergenic properties. Its stability under sterilization processes makes it indispensable for reusable and long-term medical applications. While it is distinct from conventional plastics, silicone’s role complements plastic components in creating safe and efficient medical devices. Manufacturers in China are leveraging silicone’s versatility to produce innovative solutions, contributing to the global healthcare market.
Medical grade plastics refer to a variety of specialized materials used in healthcare applications, commonly known by their individual names such as polycarbonate (PC), polypropylene (PP), polyethylene (PE), and polyvinyl chloride (PVC). These materials are engineered to meet stringent medical standards, including biocompatibility and sterilization resistance.
In China’s medical plastic parts industry, these materials are often tailored to specific applications, such as syringes, surgical instruments, or implantable devices. High standards like ISO 10993 and FDA certifications ensure these plastics are safe for patient use. By leveraging advancements in polymer technology, Chinese manufacturers are producing medical-grade plastics that meet global quality requirements, supporting healthcare innovations worldwide.
The “best” medical grade plastic depends on the application, but polycarbonate (PC) and polypropylene (PP) are widely regarded as versatile materials. Polycarbonate is valued for its high strength, clarity, and resistance to impact, making it ideal for surgical instruments and housings. Polypropylene, on the other hand, offers chemical resistance, lightweight properties, and affordability, making it a popular choice for disposable syringes and IV components.
In China’s medical plastic parts industry, manufacturers often choose materials based on compliance with international standards like ISO 10993 for biocompatibility. High-density polyethylene (HDPE) and polyvinyl chloride (PVC) are also commonly used for specific needs like fluid containers and tubing. China’s advancements in polymer science have positioned it as a leader in producing high-quality medical-grade plastics that are reliable, safe, and cost-effective for global healthcare markets.
Medicine containers are typically made from high-density polyethylene (HDPE) or polypropylene (PP), depending on the specific storage needs. HDPE is preferred for its chemical resistance, durability, and lightweight properties, making it ideal for liquid medicine bottles. Polypropylene, being highly resistant to heat and moisture, is often used for pill bottles and closures.
China’s medical plastic parts industry is a significant producer of these containers, adhering to global safety standards such as USP Class VI and ISO certifications. To ensure product safety, manufacturers focus on producing containers that are airtight, non-reactive, and capable of preserving the efficacy of the medication. Advanced manufacturing techniques in China enable the production of customizable medicine containers with features like child-resistant caps, tamper-proof seals, and dosage markings, catering to diverse pharmaceutical needs.
Medical device packaging commonly uses plastics such as polyethylene (PE), polyvinyl chloride (PVC), and polyethylene terephthalate glycol (PETG). These materials are selected for their durability, transparency, and ability to withstand sterilization processes like gamma radiation or ethylene oxide treatment.
In China’s medical plastic parts industry, manufacturers produce a wide range of packaging solutions, from blister packs and pouches to rigid trays. PETG is particularly popular for its clarity and impact resistance, ideal for showcasing and protecting sensitive medical devices. PE and PVC are widely used for flexible packaging, ensuring sterility and ease of transportation. Chinese manufacturers are also embracing eco-friendly practices by developing recyclable and biodegradable packaging materials, aligning with global sustainability trends. With advanced facilities and adherence to international standards, China plays a key role in supplying reliable medical packaging worldwide.
The pharmaceutical industry relies on several types of plastics, including polypropylene (PP), polyethylene (PE), polyvinyl chloride (PVC), and polystyrene (PS), for packaging, storage, and device manufacturing. PP and HDPE are commonly used for pill bottles, syringes, and IV fluid containers due to their chemical resistance and low reactivity. PVC is widely used for blood bags and tubing, while PS is preferred for lab equipment like petri dishes and pipettes.
In China, the medical plastic parts sector is a major supplier of these materials, producing cost-effective and high-quality components. Advanced manufacturing techniques allow for precise customization to meet the stringent requirements of pharmaceutical applications. Chinese manufacturers adhere to global standards such as ISO and GMP to ensure safety, biocompatibility, and compliance, solidifying their position as key contributors to the global pharmaceutical supply chain.
Polymers used for medical implants include ultra-high molecular weight polyethylene (UHMWPE), polyether ether ketone (PEEK), and medical-grade silicone. UHMWPE is widely used in orthopedic implants, such as hip and knee replacements, for its wear resistance and biocompatibility. PEEK is a high-performance polymer known for its strength, lightweight properties, and chemical resistance, making it suitable for spinal and dental implants. Medical-grade silicone is preferred for soft tissue implants due to its flexibility and hypoallergenic nature.
China’s medical plastic parts industry has made significant advancements in producing implantable-grade polymers that meet stringent international standards like ISO 13485. Manufacturers focus on precision molding, biocompatibility testing, and sterilization capabilities to ensure safety and effectiveness. With cutting-edge research and production facilities, China continues to expand its role in the global market for medical implants, delivering innovative and cost-effective solutions.
Contact our professional team now for a same-day quote and risk-free project evaluation. Benefit from ISO 8 cleanrooms, advanced machines, and 12-hour fast response in medical injection molding.