Precision machining plays a critical role in the medical industry, ensuring the creation of components with the accuracy and reliability required for healthcare applications. Medical devices demand exceptional quality and adherence to strict regulatory standards, making high-quality precision medical CNC machining indispensable. This advanced manufacturing process allows for the production of intricate parts with tight tolerances, supporting the development of cutting-edge medical technologies. From surgical instruments to implantable devices, CNC machining delivers unmatched precision and consistency. In parallel, medical injection molding contributes to the efficient production of high-volume, complex components, further supporting the medical industry’s need for both precision and scalability.
Additionally, precision mold medical is essential in producing highly detailed, precise molds for medical devices, ensuring the high standards necessary for the healthcare sector. Its role in advancing healthcare technologies is transformative, enabling innovations that improve patient outcomes and operational efficiency. As the medical industry continues to evolve, high-quality precision medical CNC machining, medical injection molding, and precision mold medical remain cornerstones of progress, driving breakthroughs that shape the future of healthcare. High-quality precision medical CNC machining enables cost-effective, precise production of complex surgical instruments, implants, and diagnostic devices.
Low-Volume to High-Volume Production Capabilities
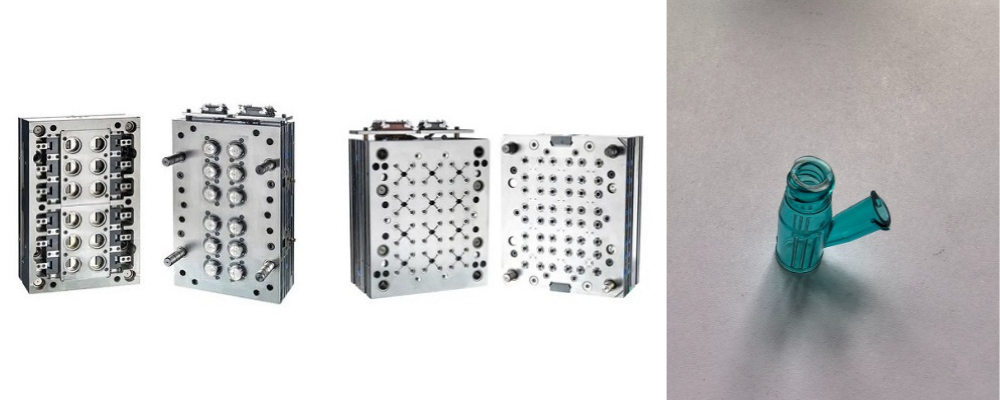
Attributes | Details |
---|---|
Place of Origin | Dongguan, Guangdong, China |
Brand Name | LY Medical Injection Mold |
Product Name | High Quality Precision Medical CNC Machining |
Type | Broaching, Drilling, Etching/Chemical Processing, Laser Processing, Milling, Other Processing Services, Turning, Wire Cutting, Rapid Prototyping |
Is Micro-machining | Micro-machining |
Process | CNC Machining + Deburring |
Tolerance | 0.005mm to 0.01mm |
Finish | Powder Coating, Anodizing, Plating, Polish |
Certificate | ISO9001:2008/ROSH |
Color | All kinds of Color Can be Made |
Drawing Format | PDF / STP / STEP /CAD and so on |
Item | OEM Precision Machining |
Quality control | 100% Inspection |
Service | OEM ODM |
Packing Details | Wooden boxes, pallets, cartons, PVC pallets, PP bags are available according to customer requirements |
Sales Unit | Single item |
Supply Capacity | 180,000 pieces per month |
What Are High Quality Precision Medical Cnc Machining?
CNC medical parts are components manufactured through computer numerical control (CNC) machining processes to meet the rigorous demands of the healthcare industry. These parts include:
- Surgical instruments: Precision-engineered tools like scalpels, forceps, and clamps.
- Implants: Devices such as orthopedic plates, screws, and joint replacements.
- Diagnostic tools: Components used in medical imaging equipment and lab diagnostics.
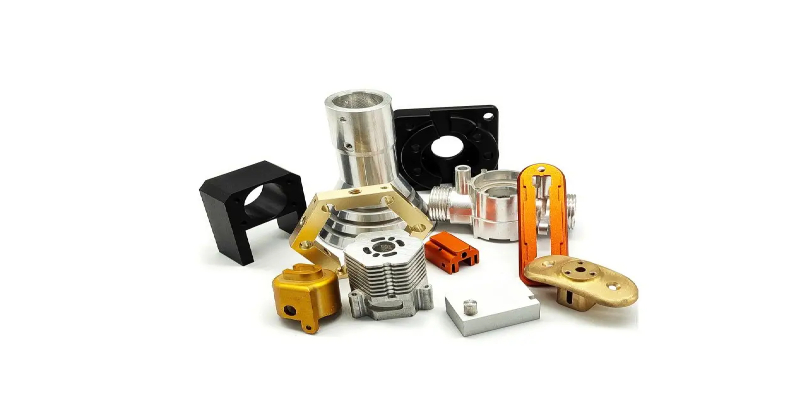
Importance of High Quality Precision Medical CNC Machining
The healthcare industry relies on high quality precision medical CNC machining to ensure:
- Precision: CNC machining achieves extremely tight tolerances, vital for medical devices to function accurately.
- Consistency: Repeatability in production guarantees uniformity across large batches of medical precision parts.
- Reliability: High-quality materials and precise machining methods ensure that parts perform reliably under critical conditions.
Applications of CNC Medical Parts
- Surgical applications: Creating tools for minimally invasive procedures.
- Prosthetics and implants: Custom-designed parts tailored to patient needs.
- Diagnostic equipment: Medical precision components for CT scanners, MRI machines, and laboratory instruments.
By leveraging high quality precision medical CNC machining, manufacturers produce components that meet stringent medical standards, driving innovation and enhancing patient care.
Key Features of High Quality Precision Medical Cnc Machining
Medical machining is built upon specific features that ensure components meet the exacting standards of the healthcare industry. These features highlight why high quality precision medical CNC machining is indispensable for manufacturing critical medical devices.
Key Features of High Quality Precision Medical CNC Machining
Precision
- CNC machining delivers exceptional accuracy, often within microns, which is vital for medical components.
- Precision ensures that implants fit perfectly and instruments perform reliably, reducing risks in medical procedures.
- High accuracy also supports the development of advanced diagnostic tools, enhancing their functionality.
Safety
- Smooth and burr-free surfaces are crucial to avoid tissue damage and ensure patient safety.
- CNC machining achieves sterilizable surfaces that comply with hygiene requirements for surgical instruments and implants.
- Materials processed through high quality precision medical CNC machining can withstand rigorous cleaning and sterilization processes.
Customization
- CNC technology allows for the production of bespoke medical components tailored to individual patient needs.
- This feature is essential for prosthetics, implants, and unique surgical tools, providing better outcomes and comfort.
- Customization is easily scalable with CNC machining, balancing individual requirements and mass production.
Regulatory Compliance
- Medical machining must adhere to strict standards such as FDA guidelines and ISO certifications, including ISO 9001:2015 and ISO 13485.
- These regulations ensure the quality, safety, and consistency of medical devices.
- The precision and repeatability offered by high quality precision medical CNC machining help manufacturers meet and maintain these standards.
Versatility
- Medical machining can process a wide range of biocompatible materials, including stainless steel, titanium, and advanced polymers.
- This versatility supports the creation of components for diverse applications, from implants to diagnostic equipment.
Reliability
- CNC machining guarantees consistent quality in every batch, ensuring devices perform reliably under critical conditions.
- This reliability builds trust in medical devices, benefiting both manufacturers and healthcare providers.
Through high quality precision medical CNC machining, these six key features combine to advance the development of safe, effective, and innovative healthcare solutions.
CNC Machining Technologies for High Quality Precision Medical Cnc Machining
Medical machining employs a variety of CNC technologies to manufacture components with unmatched accuracy and reliability. These techniques ensure that medical parts meet stringent industry standards for precision and safety.
Techniques Used in High Quality Precision Medical CNC Machining
CNC Milling
- CNC milling removes material from a workpiece to create complex shapes and contours.
- Used for manufacturing surgical tools, prosthetic components, and intricate implant structures.
- Capable of achieving tight tolerances essential for medical applications.
CNC Turning
- This process involves rotating the workpiece while a cutting tool shapes it.
- Ideal for cylindrical parts such as screws, pins, and bone plates.
- Ensures consistent results, critical in producing high-quality parts.
Swiss Precision Machining
- Swiss machining specializes in small, precise components for medical devices.
- Commonly used for producing stents, dental screws, and miniature surgical tools.
- Offers superior accuracy and repeatability, hallmarks of high quality precision medical CNC machining.
Wire EDM
- Wire Electrical Discharge Machining (EDM) uses electrical discharges to cut intricate shapes.
- Best suited for hard-to-machine materials and delicate geometries, such as those found in implantable devices.
- Ensures precise and burr-free edges, improving device safety.
Multi-Axis Machining
- Utilizes machines with 4, 5, or even 6 axes to handle complex geometries in a single setup.
- Reduces production time while maintaining exceptional precision, essential for medical implants and diagnostic equipment.
Comparison: Traditional Methods vs. CNC Machining
Aspect | Traditional Methods | High Quality Precision Medical CNC Machining |
---|---|---|
Precision | Limited, manual errors likely | Micron-level accuracy and consistency |
Complexity | Difficult for intricate designs | Capable of handling complex geometries efficiently |
Material Options | Restricted to basic materials | Works with advanced biocompatible materials |
Production Speed | Slower, more manual intervention | Faster with automated processes |
Repeatability | Inconsistent, prone to variation | High repeatability across all components |
Cost Efficiency | Higher labor costs, slower output | Optimized for precision and bulk production |
Why CNC Technologies Lead the Way
Through techniques like CNC milling, turning of medical parts, Swiss machining, and multi-axis setups, high quality precision medical CNC machining ensures optimal production outcomes. These technologies surpass traditional methods in accuracy, efficiency, and scalability, making them essential for advancing healthcare manufacturing.
Materials Used in Precision Medical Machining
Selecting the right materials is critical for producing medical components that meet the stringent requirements of the healthcare industry. Below are the most commonly used materials in high quality precision medical CNC machining, along with their unique properties and significance.
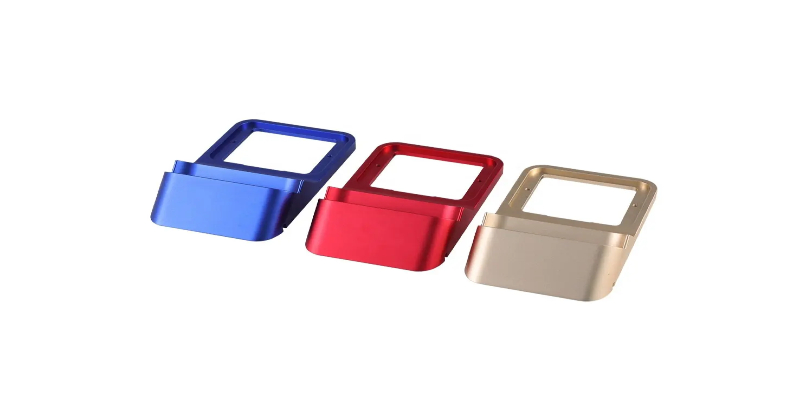
Key Materials in High Quality Precision Medical CNC Machining
Stainless Steel
- Properties: Highly durable, corrosion-resistant, and compatible with sterilization processes.
- Applications: Used in surgical instruments, medical implants, and hospital-grade equipment.
- Advantages: Its strength and resistance to wear ensure long-lasting performance under rigorous conditions.
Titanium
- Properties: Exceptional biocompatibility, lightweight, and high strength-to-weight ratio.
- Applications: Ideal for implants like joint replacements, bone plates, and dental fixtures.
- Advantages: Reduces patient discomfort due to its low weight while maintaining structural integrity in the body.
Medical-Grade Plastics
- Examples: PEEK (Polyetheretherketone), Polycarbonate, and UHMWPE (Ultra-High-Molecular-Weight Polyethylene).
- Properties: Lightweight, corrosion-resistant, and biocompatible.
- Applications: Used in prosthetics, diagnostic equipment, and non-metallic surgical instruments.
- Advantages: Medical-grade plastics provide design flexibility and reduce manufacturing costs without compromising quality.
Aluminum and Other Alloys
- Properties: Lightweight, corrosion-resistant, and easy to machine.
- Applications: Often used in diagnostic tools and equipment housings.
- Advantages: Aluminum’s excellent machinability makes it cost-effective for producing intricate designs.
Why Material Selection Matters
- The healthcare sector demands materials that can withstand harsh sterilization methods and function effectively in sensitive environments.
- Materials processed using high quality precision medical CNC machining meet these requirements, offering superior precision, safety, and reliability.
By leveraging advanced machining techniques and carefully chosen materials, manufacturers ensure that medical components achieve optimal performance and compliance with industry standards.
Applications of Precision Medical Machining
Precision machining is integral to the healthcare industry, enabling the production of critical components with exceptional accuracy and reliability. High quality precision medical CNC machining supports a wide range of applications that drive innovation and improve patient care.
Surgical Instruments
- Examples: Scalpels, forceps, clamps, and retractors.
- Significance: These tools require exacting precision and smooth surfaces to ensure safe and effective use during surgical procedures.
- Role of CNC Machining: High accuracy and repeatability ensure that instruments meet the stringent requirements of the operating room.
Medical Implants
- Examples: Joint replacements, dental implants, spinal implants, and bone plates.
- Significance: Implants must fit seamlessly into the body, requiring exceptional biocompatibility and durability.
- Role of CNC Machining: High quality precision medical CNC machining allows for the creation of implants with tight tolerances, ensuring proper function and patient comfort.
Diagnostic Equipment Components
- Examples: Parts for MRI machines, CT scanners, and laboratory analysis equipment.
- Significance: Accurate and reliable diagnostic tools are essential for early detection and effective treatment.
- Role of CNC Machining: The precise fabrication of intricate components ensures the optimal performance of these high-tech devices.
Robotic Surgery Tools
- Examples: Miniature tools and attachments for robotic-assisted surgical systems.
- Significance: These tools require unparalleled precision to perform delicate procedures with minimal invasiveness.
- Role of CNC Machining: Multi-axis CNC machining techniques enable the creation of complex, miniature parts with exceptional accuracy.
Why CNC Machining is Essential in Medical Applications
By leveraging high quality precision medical CNC machining, manufacturers produce components that are:
- Accurate: Supporting the safe and effective use of medical devices.
- Consistent: Ensuring uniformity across batches for reliable performance.
- Innovative: Enabling advancements in healthcare technologies, such as robotic surgery and personalized implants.
From surgical tools to state-of-the-art diagnostic equipment, CNC machining drives excellence in the medical field, improving patient outcomes and advancing modern medicine.
Advantages of Techniques Used in High Quality Precision Medical CNC Machining
The medical industry’s demand for reliability, precision, and scalability makes CNC machining a cornerstone of modern healthcare manufacturing. Below are six key advantages of high quality precision medical CNC machining that set it apart.
High Tolerance and Accuracy for Intricate Designs
- Significance: Medical devices and components often involve complex geometries and extremely tight tolerances.
- Benefit: CNC machining can achieve micron-level precision, ensuring parts meet exacting specifications.
- Examples: Surgical tools, robotic surgery components, and intricate implant designs are all produced with superior accuracy.
Flexibility in Material Usage
- Significance: The medical field requires a variety of materials, including biocompatible metals and medical-grade plastics.
- Benefit: CNC machining handles diverse materials, such as stainless steel, titanium, PEEK, and polycarbonate, with ease.
- Applications: From durable surgical instruments to lightweight diagnostic components, material versatility ensures the right fit for every application.
Cost-Effectiveness Through Repeatable Processes
- Significance: Precision machining for medical minimizes material waste and reduces labor costs.
- Benefit: Once a program is set, CNC machines produce consistent, high-quality parts in bulk, cutting overall costs.
- Examples: Manufacturing batches of implants or disposable medical tools becomes more economical without compromising quality.
Scalability from Prototyping to Mass Production
- Significance: The development of medical devices requires both rapid prototyping and efficient large-scale production.
- Benefit: CNC machining seamlessly transitions from creating initial prototypes to mass-producing finished parts.
- Applications: New surgical tool designs can be tested quickly, and once approved, produced in high volumes.
Enhanced Quality Control
- Significance: Medical components must adhere to strict industry standards, such as ISO 13485 and FDA regulations.
- Benefit: CNC machines deliver consistent quality, and integrated quality checks ensure compliance.
- Examples: Highly precise components for life-saving devices like pacemakers or ventilators meet rigorous inspection criteria.
Shorter Lead Times for Critical Products
- Significance: The medical industry often requires rapid production to meet urgent healthcare demands.
- Benefit: CNC machining reduces manufacturing time without sacrificing precision or quality.
- Applications: During emergencies, such as pandemics, CNC machining facilitates the swift production of diagnostic equipment components.
High quality precision medical CNC machining provides unmatched precision, material versatility, and efficiency, making it indispensable for the medical industry’s evolving needs. From prototyping cutting-edge designs to mass-producing life-saving tools, CNC machining drives innovation and excellence in healthcare manufacturing.
How to Choose a Suitable Supplier for High-Quality Precision Medical CNC Machining
When selecting a supplier for high-quality precision medical CNC machining, it’s essential to consider a variety of factors to ensure that the supplier can meet the stringent requirements of the medical industry. The medical field demands absolute precision, safety, and regulatory compliance, so your supplier must possess not only the right technology but also the necessary certifications, experience, and expertise. In this guide, we’ll explore key considerations that can help you choose the most suitable supplier. We will cover aspects like technical capabilities, experience, quality control systems, certifications, and customer service, each contributing to a comprehensive evaluation of potential partners for your CNC machining needs.
Technical Capabilities and Equipment
A supplier’s technical capabilities and the quality of their equipment are among the most important factors to consider when choosing a provider for high-precision medical CNC machining. Medical components often require multi-axis machining, advanced cutting tools, and specialized features such as precision spindles and high-end cooling systems. It is critical to ensure that the supplier has the latest CNC equipment designed for precision, such as 5-axis CNC machines, laser-assisted CNC, or ultra-precision grinders.
You should inquire about the specific machines they use and their capability to work with various materials like medical-grade titanium, stainless steel, PEEK, or coated alloys. High-precision work, such as producing surgical implants or micro-medical devices, demands the use of machines that offer tolerances as tight as ±0.0001 inches. A supplier with advanced technology will also be able to handle complex geometries and multi-step machining processes, making them better suited for intricate medical applications.
Experience and Expertise in Medical CNC Machining
The experience and specialized knowledge of a supplier play a crucial role in the success of your medical CNC machining project. You need a supplier who not only understands CNC machining but also has direct experience in the medical field, where the stakes are high. Medical machining requires a deep understanding of biocompatibility, tolerances, and regulatory compliance.
Look for suppliers with a proven track record in manufacturing medical components such as implants, surgical instruments, or diagnostic devices. Inquiring about their experience with specific types of medical products or complex geometries can give you a better understanding of their capabilities. Ask for case studies or examples of their previous work that demonstrate their ability to meet high standards. Suppliers who are experienced in handling demanding medical machining projects are more likely to meet your requirements efficiently and without costly errors.
Quality Control and Assurance Systems
In high-quality precision medical CNC machining, quality control is paramount. Even the slightest deviation from specifications can lead to serious consequences in medical applications. It is essential that your supplier has rigorous quality control measures in place, from the initial design and prototyping stages through to the final product.
A reliable supplier will typically follow a quality management system (QMS) such as ISO 13485, which specifically applies to medical device manufacturing. They should employ CMMs (Coordinate Measuring Machines), optical measuring systems, and other advanced tools to verify the accuracy of every part produced. Ensure that the supplier has clearly defined inspection protocols, including regular calibration of machines, statistical process control (SPC), and traceability of each batch. Furthermore, ask about their approach to handling defective parts and ensuring corrective actions are taken promptly.
Certifications and Regulatory Compliance
Medical device manufacturing is highly regulated, and choosing a supplier with the necessary certifications and a deep understanding of regulatory standards is critical. The supplier should comply with FDA guidelines for medical devices and meet ISO 13485 standards for medical device quality management systems. These certifications confirm that the supplier’s processes and products meet international standards for quality and safety.
In addition to certification, the supplier should be familiar with regulatory bodies specific to your market, whether that’s CE marking for the European market or FDA approval for the United States. Make sure they have experience working with materials that meet medical-grade standards and can ensure that their products comply with relevant biocompatibility and sterilization requirements. Regulatory compliance ensures that your products will meet the necessary safety standards before they reach patients or healthcare providers.
Customer Service and Support
The quality of customer service provided by the supplier is an important factor in determining whether they are the right fit for your needs. A supplier that communicates well, provides technical support, and works closely with you to troubleshoot issues can be invaluable, especially when working on complex medical CNC machining projects.
Ensure that your potential supplier offers excellent pre- and post-production support, including rapid response times, transparent communication, and a willingness to make necessary adjustments during production. A good supplier will also be able to guide you through the prototyping process, helping you make design decisions that optimize manufacturability without sacrificing performance or safety. Additionally, consider the turnaround time for sample production and the flexibility of the supplier to meet your timeline, particularly if you need rapid prototyping or fast production for critical medical devices.
Cost-Effectiveness and Value
While cost is always a consideration, it should not come at the expense of quality, especially in the medical field, where precision and safety are critical. When evaluating potential suppliers, consider the total cost of ownership rather than just the per-unit price. Look for a supplier who offers a balance of competitive pricing and high-quality results.
Additionally, a supplier who uses advanced technology and efficient manufacturing processes may be able to offer better value over the long term by minimizing waste, reducing production time, and lowering material costs. Ensure that the supplier provides transparent pricing models and does not include hidden costs, especially for services like prototyping or expedited shipping. Quality and reliability are key in medical CNC machining, so aim for a supplier that delivers long-term value rather than simply choosing the lowest-cost option.
Scalability and Flexibility
As your business grows or as new medical applications emerge, you’ll need a CNC machining supplier that can scale with your needs. Whether you need to produce a small batch of prototypes or a large volume of parts for mass production, the supplier must have the flexibility and capacity to handle both.
A supplier with a diverse set of manufacturing capabilities, including the ability to handle low-volume and high-volume production, will be more adaptable to your changing needs. This scalability is particularly important in the medical field, where the demand for certain devices may vary based on new treatments, technological advances, or market changes. Discuss the supplier’s capacity for handling future expansions and their ability to accommodate fluctuating order sizes without compromising quality.
Choosing the right supplier for high-quality precision medical CNC machining is crucial to ensuring that your medical devices are produced with the utmost precision, safety, and reliability. By carefully considering factors such as technical capabilities, experience in the medical field, quality control systems, certifications, customer service, cost-effectiveness, and scalability, you can find a supplier that meets your unique needs. This comprehensive evaluation will help ensure that your parts meet the highest standards of performance, safety, and regulatory compliance, contributing to the success of your medical applications.
Innovations in High-Quality Precision Medical CNC Machining
High-quality precision medical CNC machining has transformed the way medical devices and components are designed, manufactured, and delivered. By utilizing cutting-edge technologies and advanced materials, CNC machining enables the creation of highly complex and precise parts, driving innovation in areas such as surgical instruments, implants, and diagnostic devices. This process has allowed for the production of smaller, more efficient, and more reliable components, meeting the ever-growing demands of the medical industry. In this section, we’ll explore various innovations brought about by high-quality precision medical CNC machining, covering advancements in machining techniques, material use, manufacturing efficiency, and customization.
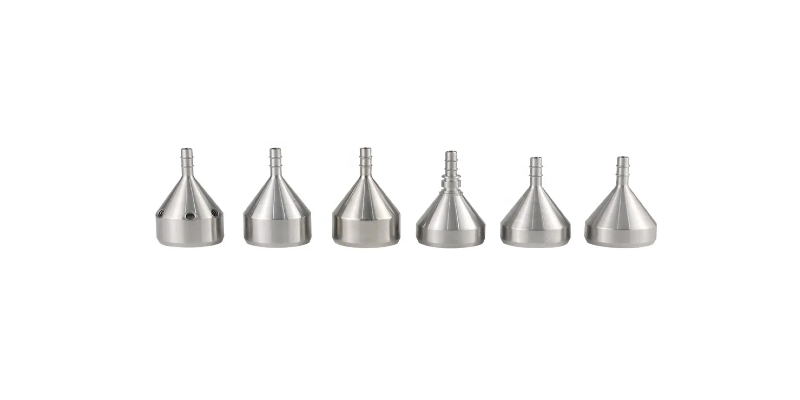
Advanced Machining Techniques and Capabilities
High-quality precision medical CNC machining has led to the development of more advanced machining techniques, which are capable of producing highly intricate and precise medical components. The use of multi-axis CNC machines, such as 5-axis CNC machines, allows manufacturers to machine complex geometries in a single setup, reducing time and improving the accuracy of parts. These machines are particularly beneficial for producing components with intricate features like surgical implants, orthopedic devices, and micro-medical instruments.
Furthermore, innovations such as laser-assisted machining and electrical discharge machining (EDM) are enhancing the precision and efficiency of medical part production. These methods enable the machining of delicate materials with minimal thermal impact, ensuring the integrity of parts used in sensitive medical applications. The ability to produce highly detailed, complex parts with tight tolerances allows for more functional, safer, and effective medical devices.
Material Advancements for Medical Components
One of the most significant innovations driven by high-quality precision medical CNC machining is the ability to work with advanced materials tailored for medical applications. CNC machining enables the use of biocompatible materials such as titanium, stainless steel, cobalt-chromium, and PEEK, which are ideal for implants, surgical instruments, and diagnostic tools. These materials offer superior strength, durability, and resistance to corrosion, which are essential for medical devices that come into contact with the human body.
Additionally, CNC machining allows manufacturers to experiment with new alloys and composites that combine the properties of traditional materials with the benefits of newer innovations, such as improved flexibility, lighter weight, or enhanced resistance to wear. These innovations have expanded the range of possible applications in the medical field, improving patient outcomes and enhancing the performance of medical devices.
Enhanced Precision and Tolerances
The precision and tight tolerances achievable with high-quality precision medical CNC machining are another area where significant innovation has occurred. Medical devices, particularly implants and diagnostic components, require tolerances as fine as ±0.0001 inches to ensure they function correctly and safely within the human body. CNC machines can meet these stringent specifications consistently, reducing the risk of human error and producing parts that fit perfectly in complex medical assemblies.
These capabilities have led to advances in miniaturization, allowing for the production of extremely small, intricate parts with high accuracy. This has paved the way for the development of micro-medical devices such as implantable sensors, micro-surgical tools, and diagnostic instruments that offer improved functionality in minimally invasive procedures.
Faster Prototyping and Production
With high-quality precision medical CNC machining, the development cycle for new medical devices has accelerated. The ability to rapidly prototype and test designs has made it easier for companies to refine their concepts before mass production. CNC machining enables the creation of prototypes with the same level of precision as final products, allowing engineers to identify design flaws early and make adjustments quickly.
Additionally, CNC machining allows for rapid production of medical components in both low-volume and high-volume runs. This flexibility helps meet the demand for both customized, patient-specific implants and mass-produced medical devices. Innovations in automation, such as the integration of robotic arms and computer-aided design (CAD) systems, further enhance production speed and consistency, ensuring that parts are produced on time without sacrificing quality.
Customization and Patient-Specific Solutions
One of the more recent innovations in precision medical CNC machining is the ability to produce customized medical devices tailored to individual patients. Using 3D scanning and patient data, CNC machines can create highly personalized implants, prosthetics, and surgical tools that fit a patient’s specific anatomy. This level of customization improves the effectiveness of treatments and surgical outcomes.
For example, patient-specific implants for joint replacements, spinal surgeries, and cranial reconstructions can be produced with a perfect fit, reducing the risk of complications and improving recovery times. This ability to personalize medical devices has opened up new possibilities in areas such as orthopedics, dentistry, and plastic surgery, where one-size-fits-all solutions are no longer adequate.
Cost-Effectiveness and Efficiency
While the demand for higher precision and customization increases, high-quality precision medical CNC machining also remains a cost-effective solution for manufacturers. CNC machining requires fewer special tools and fixtures compared to traditional manufacturing methods, reducing overall production costs. The automation of CNC machines further improves efficiency, enabling the production of high-quality medical components at a lower cost.
Moreover, by reducing material waste, minimizing human error, and improving production speed, CNC machining offers manufacturers a way to reduce operational costs while maintaining the highest standards of quality. These factors make it an ideal solution for producing medical devices, where performance and cost are both critical factors in bringing products to market.
High-quality precision medical CNC machining continues to drive significant innovations across the medical industry by enabling the production of highly precise, complex, and customizable medical devices. From advanced machining techniques and material developments to enhanced precision, faster prototyping, and patient-specific solutions, CNC machining has become a cornerstone of modern medical manufacturing. The ability to create intricate components with tight tolerances, cost-effectively and efficiently, ensures that precision medical machining will continue to shape the future of surgical instruments, implants, diagnostic devices, and other critical medical applications.
Comparison Between High-Quality Precision Medical CNC Machining and Medical Injection Molding
In the medical manufacturing industry, high-quality precision medical CNC machining and medical injection molding are two essential manufacturing techniques used to create critical medical components such as implants, surgical instruments, and diagnostic equipment. While both processes contribute to the production of high-precision medical devices, they differ significantly in terms of manufacturing method, material compatibility, cost efficiency, precision levels, and application suitability. Understanding these differences is crucial for selecting the right production method based on specific medical requirements. Below, we explore the key distinctions between these two manufacturing processes from multiple perspectives.
Manufacturing Process Differences
The core difference between high-quality precision medical CNC machining and medical injection molding lies in how each process creates medical components. CNC machining is a subtractive process, while injection molding is an additive forming process.
CNC Machining
- CNC (Computer Numerical Control) machining starts with a solid block of material, which is gradually cut away using precision tools to achieve the desired shape.
- The process allows for highly complex and custom designs with extremely tight tolerances, often within ±0.0001 inches.
- Multi-axis CNC machines (e.g., 5-axis CNC) enable the production of intricate geometries without requiring additional assembly.
- Ideal for low- to medium-volume production and prototypes requiring flexibility and high precision.
Injection Molding
- Involves melting plastic or specialized medical-grade polymers and injecting them into a mold cavity, where they cool and solidify into the final shape.
- Best suited for high-volume production, as the cost per unit decreases significantly after mold fabrication.
- Complex internal structures can be achieved, but with less design flexibility compared to CNC machining.
- Requires expensive tooling, making it less practical for low-volume or highly customized medical parts.
Material Selection and Biocompatibility
Medical devices require biocompatible materials to ensure patient safety and regulatory compliance. The choice of materials is influenced by whether CNC machining or injection molding is used.
CNC Machining Materials
- Can process metals (e.g., titanium, stainless steel, cobalt-chrome, aluminum) and high-performance plastics (e.g., PEEK, PTFE, UHMW-PE).
- Titanium and stainless steel are essential for implants and surgical tools due to their strength, durability, and corrosion resistance.
- More suitable for high-temperature, high-stress applications such as orthopedic implants and precision surgical instruments.
Injection Molding Materials
- Primarily used for medical-grade plastics such as PEEK, PC, ABS, and silicone.
- Ideal for disposable medical components like syringes, tubing, and casings for diagnostic devices.
- Biocompatible polymers can be used, but lack the mechanical strength of metals used in CNC machining.
Precision and Tolerance Levels
When manufacturing medical devices, precision is a critical factor that directly impacts the performance, safety, and regulatory approval of the final product.
CNC Machining Precision
- Offers exceptionally high precision, often achieving tolerances as tight as ±0.0001 inches.
- Ensures smooth, burr-free surfaces, essential for implants and surgical tools that interact with human tissue.
- Guarantees consistency across complex geometries without warping or deformation.
Injection Molding Precision
- Tolerances are generally within ±0.005 inches, which is sufficient for most medical plastic components but not ideal for ultra-precise applications.
- Material shrinkage and warping can occur, requiring mold adjustments and additional finishing steps.
- While post-processing (e.g., trimming and polishing) can improve precision, it cannot match the ultra-tight tolerances of CNC machining.
Cost and Production Efficiency
The choice between high-quality precision CNC machining and injection molding also depends on cost-effectiveness and production volume.
CNC Machining Cost Considerations
- Higher cost per unit, especially for high-precision, low-volume production.
- No expensive mold tooling required, making it ideal for prototyping and custom, small-batch medical devices.
- More cost-efficient for low- to medium-production runs where extreme precision is necessary.
Injection Molding Cost Considerations
- High initial cost due to mold design and fabrication, but lower cost per unit for high-volume production.
- Ideal for mass production of disposable or standardized medical components.
- Not cost-effective for small runs or frequently changing designs due to mold modification expenses.
Application Suitability in the Medical Industry
Both CNC machining and injection molding play crucial roles in the medical industry, but their suitability depends on the type of medical device being manufactured.
Best Applications for CNC Machining
- Implants (e.g., orthopedic screws, dental implants, hip replacements) that require biocompatible metals and extreme precision.
- Surgical tools (e.g., scalpels, forceps, endoscopic instruments) where durability, sharpness, and corrosion resistance are essential.
- High-precision diagnostic equipment requiring tight tolerances and superior surface finishes.
- Prototyping and custom medical device production for new product development.
Best Applications for Injection Molding
- High-volume disposable medical components (e.g., syringes, IV connectors, catheters) where cost-efficiency is key.
- Medical device housings and enclosures, such as for ECG machines, ventilators, and infusion pumps.
- Wearable medical devices (e.g., hearing aids, insulin pump casings) that require lightweight, durable plastic materials.
- Medical packaging and tubing, which benefit from mass production efficiency.
When deciding between high-quality precision medical CNC machining and medical injection molding, manufacturers must consider material selection, precision requirements, cost constraints, and production volume. CNC machining is the preferred choice for high-precision, custom, and metal-based medical devices, while injection molding is ideal for mass-produced, disposable, or plastic medical components.
Ultimately, many medical device manufacturers use a combination of both processes—CNC machining for high-precision functional components and injection molding for casing, tubing, and mass-produced plastic parts. By understanding the strengths and limitations of each technique, companies can ensure they select the most efficient and cost-effective method for producing high-quality, safe, and regulatory-compliant medical devices.
Requirements for Typical Characteristics of High-Quality Precision Medical CNC Machining
High-quality precision medical CNC machining is essential for producing medical devices and components that meet the stringent standards of safety, reliability, and performance in the medical field. The nature of medical applications demands that CNC machining processes achieve exceptionally high standards across multiple aspects of the manufacturing process. In this section, we will explore the typical characteristics and requirements of high-quality precision medical CNC machining, covering key factors such as precision, material selection, surface finish, quality control, regulatory compliance, and technological innovation. Each of these elements plays a critical role in ensuring that the parts produced are not only functional but also safe and effective in medical environments.
High Precision and Tight Tolerances
Precision and tolerance are the cornerstones of high-quality precision medical CNC machining. Medical components, particularly implants, surgical instruments, and diagnostic devices, require extremely tight tolerances to ensure proper function and fit. Even the smallest deviation can compromise the safety and effectiveness of a medical device, making high precision essential.
Typically, medical components require tolerances in the range of ±0.0001 inches, though this may vary depending on the specific application. 5-axis CNC machines and other advanced machinery allow for the creation of complex geometries with high accuracy, ensuring that parts fit together perfectly and function optimally. Achieving tight tolerances is critical in areas such as joint replacements, neurosurgery, and cardiovascular devices, where even the slightest misalignment could lead to device failure or complications during surgery.
Biocompatible and Specialized Materials
The materials used in high-quality precision medical CNC machining must meet rigorous requirements for biocompatibility and durability. Medical devices that interact with the human body, whether externally or internally, must be made from materials that are safe, non-toxic, and able to withstand physiological conditions. CNC machining enables manufacturers to work with a variety of medical-grade materials such as titanium, stainless steel, PEEK (Polyetheretherketone), and cobalt-chromium alloys, all of which offer excellent mechanical properties and are well-suited for medical applications.
In addition to material strength and durability, materials must be resistant to corrosion, wear, and fatigue, particularly for devices that are implanted in the body for extended periods. CNC machining allows for precise control over material processing, ensuring that components are manufactured to the highest standards of quality and reliability.
Surface Finish Quality
In high-quality precision medical CNC machining, the surface finish of the component is critical to both its performance and safety. Medical devices often require smooth surfaces to avoid irritation or damage to surrounding tissue, and to ensure that the device functions properly within the body or medical environment. CNC machining allows for the creation of highly polished surfaces, which are particularly important for implants that will be in contact with biological tissues.
Surface finish requirements vary depending on the device type, but for medical components, Ra values (roughness average) typically need to be less than 1.6 micrometers for implantable devices. In addition, specific coatings such as biocompatible coatings or anti-corrosive layers are often applied post-machining to enhance the device’s performance and longevity. Precision finishing technologies such as grinding, lapping, or electropolishing are often integrated with CNC machining to achieve these high-quality surface standards.
Regulatory Compliance and Certification
Medical devices are subject to strict regulatory oversight due to their critical role in patient safety. Therefore, high-quality precision medical CNC machining must adhere to a variety of regulatory standards and certifications to ensure compliance with industry requirements. One of the most important certifications is ISO 13485, which sets out the requirements for a quality management system in the medical device industry. This certification ensures that the supplier follows rigorous standards for product quality, documentation, and traceability.
Additionally, medical devices must comply with FDA regulations in the United States or CE marking requirements in Europe. These certifications ensure that the parts produced through CNC machining meet all safety, performance, and biocompatibility standards necessary for medical applications. The ability to work with a supplier who understands and adheres to these regulations is essential to mitigate risks and ensure the success of the product in the marketplace.
Consistency and Reproducibility
In high-quality precision medical CNC machining, consistency is paramount. Since medical devices often require large production runs, it is essential that each part is produced to the exact same specifications. CNC machining offers high repeatability, meaning that once a machine has been set up and calibrated, it can produce parts that meet the same high standards across multiple production cycles.
This reproducibility is crucial for components like surgical tools and implants, where each part must have the same dimensions, features, and finish to ensure they work properly within medical procedures. Manufacturers use advanced statistical process control (SPC) and quality monitoring systems to track each stage of production and ensure that every part meets the required specifications.
Advanced Technological Integration
The integration of advanced technologies into high-quality precision medical CNC machining has revolutionized the medical device manufacturing process. Technologies like computer-aided design (CAD) and computer-aided manufacturing (CAM) allow for the optimization of designs and the creation of complex medical components with ease. 3D scanning and reverse engineering can also be used to create digital models of existing parts, enabling more precise replication or modification for specific medical applications.
In addition, robotic automation and AI-driven process optimization are increasingly used to improve production efficiency and reduce human error. These technologies not only enhance the precision and quality of the finished product but also enable faster turnaround times for prototypes and production runs, making it easier to meet the demanding timelines of the medical industry.
Cost-Effectiveness and Efficiency
Despite the high precision required, high-quality precision medical CNC machining is a cost-effective solution for producing medical components. CNC machining eliminates the need for expensive tooling and molds, which are often required for traditional manufacturing methods. This makes it easier to produce small runs of high-precision components at a lower cost compared to other processes.
The efficiency of CNC machining is also improved through the use of automated systems that reduce production time, minimize human error, and decrease material waste. This results in lower overall manufacturing costs while maintaining high-quality standards. Additionally, the ability to produce both low-volume prototypes and high-volume production runs means manufacturers can scale up production quickly without sacrificing quality or increasing costs.
High-quality precision medical CNC machining is defined by its ability to meet the highest standards across various aspects of medical device production. From precision and material selection to regulatory compliance, surface finish quality, and cost-effectiveness, CNC machining provides the flexibility and innovation needed to create the next generation of medical devices. Meeting the exacting requirements of the medical industry, CNC machining is a vital process for ensuring that medical components are reliable, functional, and safe for use in healthcare applications.
Limitations of High-Quality Precision Medical CNC Machining in the Medical Field
High-quality precision medical CNC machining is widely used in the medical field for manufacturing implants, surgical instruments, and diagnostic equipment. This process offers exceptional accuracy, biocompatibility, and customization, making it indispensable for medical device production. However, despite its many advantages, CNC machining also has several limitations that impact its applicability and efficiency in the medical industry. These challenges stem from factors such as cost, material constraints, production speed, and complexity of regulatory compliance. Below, we explore the limitations of high-quality precision medical CNC machining from multiple perspectives.
High Production Costs
While CNC machining provides unparalleled precision, its cost structure makes it less suitable for large-scale, cost-sensitive medical applications. The expenses associated with machine operation, materials, and skilled labor contribute to its high cost per unit.
Specific Cost Challenges
- Expensive Equipment – High-precision medical CNC machines require advanced multi-axis systems, specialized tooling, and real-time monitoring, leading to substantial capital investment.
- Material Waste – Since CNC machining is a subtractive manufacturing process, a significant portion of raw material is cut away and discarded, increasing material costs. This is particularly expensive when machining high-value medical materials like titanium and cobalt-chrome.
- Skilled Labor Costs – Operating CNC machines for medical applications requires highly trained machinists and engineers who understand ISO 13485 compliance, FDA regulations, and precision machining techniques, which increases labor costs.
Due to these factors, CNC machining is less cost-effective for high-volume medical device production compared to alternative methods like medical injection molding.
Limited Suitability for Mass Production
CNC machining is excellent for low- to medium-volume production and prototyping, but it struggles with mass manufacturing demands in the medical field.
Challenges in Large-Scale Production
- Slow Production Speeds – CNC machining removes material layer by layer, making it a time-consuming process compared to injection molding, where thousands of components can be produced in a single run.
- Higher Cost Per Unit – While CNC machining excels at making custom parts, its cost per unit does not decrease significantly with higher production volumes, making it less competitive for disposable medical components like syringes, IV connectors, and catheters.
- Machine Wear and Maintenance – Continuous operation of high-precision CNC machines leads to tool wear, requiring frequent maintenance and recalibration to maintain accuracy, further increasing downtime and operational costs.
For large-scale medical device production, other manufacturing methods such as injection molding or metal stamping are often more efficient and cost-effective.
Material Limitations and Challenges
Although CNC machining can handle a wide range of materials, it has some limitations in terms of material selection, machinability, and efficiency for certain medical applications.
Material Constraints in CNC Machining
- Not Ideal for Soft or Elastic Materials – While CNC machining is excellent for metals and rigid plastics, it is less effective for soft, flexible, or highly elastic materials like silicone, which are commonly used in medical tubing and wearable devices.
- Difficult Machining of Certain Biocompatible Materials – Some biocompatible materials, such as ceramics (e.g., zirconia) and composite materials, are challenging to machine due to their hardness and brittleness, leading to tool breakage and increased machining time.
- Material Waste and Recycling Challenges – Unlike additive manufacturing (e.g., 3D printing), which uses only the required material, CNC machining results in high material wastage, making it less sustainable for certain medical applications.
These material-related limitations make alternative manufacturing methods like 3D printing, injection molding, and laser sintering more suitable for certain medical devices.
Complexity of Regulatory Compliance
Medical device manufacturing requires strict adherence to regulatory standards, and CNC machining must meet stringent compliance requirements to be used in the medical field.
Regulatory Challenges in CNC Machining
- Stringent Quality Control – High-quality precision CNC machining requires continuous monitoring, first-article inspection (FAI), and coordinate measuring machine (CMM) verification to ensure that all medical components meet ISO 13485, FDA, and EU MDR (Medical Device Regulation) standards.
- Process Validation Requirements – Unlike standardized manufacturing methods such as injection molding, CNC machining often involves customized processes that require extensive validation, documentation, and repeatability testing before medical device approval.
- Traceability and Documentation – Medical CNC machining requires full traceability of materials, production processes, and quality inspections, adding complexity to manufacturing workflows and increasing operational overhead.
These regulatory hurdles add time and cost to CNC machining, making it less favorable for mass production of medical devices that require rapid market entry.
Design and Geometric Limitations
Although CNC machining can create complex medical components, it has design limitations compared to other advanced manufacturing methods like 3D printing and injection molding.
Geometric Constraints in CNC Machining
- Internal Cavities and Hollow Structures – CNC machining struggles with intricate internal geometries, such as small hollow chambers or microfluidic channels, which are easier to produce using injection molding or additive manufacturing.
- Size Limitations – Large medical components may require multiple machining setups or assembly of multiple parts, which increases production complexity.
- Tool Access Restrictions – Some intricate medical device designs, especially those with deep undercuts or sharp internal corners, may not be machinable using standard CNC tools.
For highly complex, organic, or lattice-structured medical devices, 3D printing (additive manufacturing) provides greater design flexibility compared to CNC machining.
High-quality precision medical CNC machining remains an essential manufacturing process in the medical industry due to its superior accuracy, material versatility, and ability to produce customized implants and surgical instruments. However, it also has limitations, including high production costs, slow scalability for mass production, material constraints, regulatory complexity, and geometric restrictions.
For low-volume, high-precision, and metal-based medical devices, CNC machining is unmatched in quality and precision. However, for high-volume production, flexible material applications, and highly intricate internal geometries, alternative manufacturing methods like injection molding, 3D printing, and laser sintering may be more suitable.
Ultimately, medical manufacturers must carefully evaluate their specific needs, regulatory requirements, and cost constraints when choosing between CNC machining and other production technologies. Often, a combination of CNC machining for critical precision parts and other methods for mass-produced components provides the most efficient and cost-effective solution for medical device manufacturing.
The Future of High-Quality Precision Medical CNC Machining in the Medical Field
High-quality precision medical CNC machining is poised to continue transforming the medical field by enabling the development of more sophisticated, personalized, and effective medical devices. As technology advances, the scope of CNC machining is expanding, offering exciting possibilities for the production of medical components with higher precision, greater complexity, and enhanced functionality. This section explores the future of precision medical CNC machining, focusing on emerging trends, technological advancements, evolving material use, and the potential for new applications in the medical field. These developments will shape how medical devices are designed, manufactured, and used, ultimately improving patient outcomes and enhancing the overall healthcare experience.
Advancements in Machine Capabilities
The future of high-quality precision medical CNC machining is closely tied to the continual evolution of CNC machines. As manufacturers push for ever greater accuracy and speed, new innovations in machine technology are allowing for even more precise and complex medical components to be produced. The rise of multi-axis CNC machines, including 7-axis and 9-axis configurations, allows for greater flexibility and precision when machining intricate, complex shapes.
These advancements will make it possible to create even more intricate surgical instruments, implants, and diagnostic devices. These machines will also be faster, allowing for higher-volume production while maintaining tight tolerances and reducing lead times. Furthermore, the integration of robotic automation and artificial intelligence (AI) into CNC machines will optimize machining processes, reduce human error, and enhance production efficiency, allowing manufacturers to produce high-quality medical components at scale.
Increased Customization and Patient-Specific Devices
A major trend shaping the future of high-quality precision medical CNC machining is the growing demand for customized and patient-specific devices. With the rise of personalized medicine, there is an increasing need for medical devices, implants, and prosthetics that are tailored to the unique anatomical requirements of individual patients. CNC machining is already playing a pivotal role in this shift, allowing manufacturers to produce patient-specific implants based on 3D scans or imaging data.
In the future, innovations in 3D scanning and computer-aided design (CAD) will further enhance the ability to create customized medical devices with a higher level of precision. The ability to manufacture highly personalized surgical instruments or prosthetic limbs that precisely fit a patient’s body will improve surgical outcomes, speed up recovery times, and provide a better overall patient experience. As the demand for such customized devices grows, CNC machining will become an even more integral part of medical manufacturing.
Use of Advanced Materials
The future of high-quality precision medical CNC machining will also be marked by the expanded use of advanced materials that offer improved performance and biocompatibility. As the need for more durable, flexible, and lightweight medical components grows, CNC machining will allow for the production of components made from new materials like bioresorbable polymers, graphene, and advanced metal alloys.
For example, PEEK (Polyetheretherketone) and titanium alloys are already commonly used in medical applications, but research into new materials continues to expand possibilities. CNC machining allows for the precise processing of these materials, ensuring they meet the necessary standards for biocompatibility and durability. With the continued development of materials that offer enhanced properties, precision medical CNC machining will be able to meet even more demanding medical requirements, enabling the creation of safer, longer-lasting, and more efficient medical devices.
Integration of Additive Manufacturing
As additive manufacturing (3D printing) technology advances, there will likely be an increasing integration of 3D printing and CNC machining to create highly complex medical components. While CNC machining is ideal for producing precise and accurate parts with tight tolerances, 3D printing allows for the rapid prototyping of intricate geometries that would be difficult to achieve with traditional methods.
By combining these technologies, manufacturers can create medical devices that are both highly complex and highly precise. For example, 3D-printed scaffolds for tissue engineering, when combined with CNC-machined components, can result in custom implants that perfectly fit a patient’s body. This hybrid approach will open new doors for manufacturing innovative medical components that were previously difficult or impossible to produce, particularly in the fields of orthopedics, dentistry, and tissue engineering.
Faster Production and Shorter Lead Times
As demand for medical devices continues to rise, there is increasing pressure to reduce lead times and speed up the manufacturing process. The future of high-quality precision medical CNC machining will focus on achieving faster production times without compromising on quality. The implementation of automated CNC machines and smart manufacturing processes will enable continuous, high-efficiency production while ensuring that each part meets the required specifications.
In addition, cloud-based software will be used to improve collaboration and design optimization, allowing manufacturers to streamline the entire product lifecycle from concept to production. As a result, shorter lead times will allow medical device manufacturers to respond more quickly to market needs, especially in the case of urgent or emergency medical requirements, such as in trauma surgery or life-saving implants.
Enhanced Quality Control and Monitoring
With the future of high-quality precision medical CNC machining focusing on improved consistency and accuracy, the integration of advanced quality control systems will become increasingly important. Technologies such as in-process monitoring, machine vision systems, and AI-powered quality assurance tools will provide real-time feedback on machining operations, ensuring that any deviations from the desired tolerances are quickly identified and corrected.
In addition, digital twins—virtual replicas of physical devices—could be used to simulate machining processes, providing manufacturers with the ability to predict and prevent defects before they occur. This enhanced level of monitoring will ensure that medical devices meet the strict regulatory and safety requirements expected of them, reducing the risk of recalls and improving overall product reliability.
The future of high-quality precision medical CNC machining holds tremendous potential to drive innovation in the medical field. With advancements in machine capabilities, material use, customization, and production speed, CNC machining will continue to play a central role in the creation of complex, high-precision medical devices and components. By embracing new technologies such as additive manufacturing, AI, and automation, the industry will be able to meet the growing demand for customized, cost-effective, and high-quality medical devices. As the medical field evolves, so too will the role of CNC machining in shaping the future of healthcare.
FAQs about High Quality Precision Medical Cnc Machining
CNC (Computer Numerical Control) machines are known for their high precision and accuracy. The precision of a CNC machine can vary based on various factors, such as the type of machine, the tooling used, and the material being worked on. Generally, high-quality CNC machines can achieve precision levels as fine as 0.001 inches (25 microns) or better. Some advanced CNC machines, particularly those used in aerospace and medical industries, can achieve tolerances as tight as 0.0001 inches (2.5 microns). This exceptional level of precision ensures that parts are produced consistently with minimal deviation, allowing for complex designs and tight tolerances to be met. Regular maintenance and calibration are critical in maintaining the precision of CNC machines over time.
Absolutely, there is a promising future in CNC machining. As industries continue to evolve with advancements in automation, the demand for CNC machining is only expected to grow. One key area driving this growth is the increase in demand for highly specialized and complex components, especially in sectors such as aerospace, automotive, defense, and healthcare. Moreover, advancements in technology are continuing to enhance the capabilities of CNC machines, enabling even greater precision, efficiency, and versatility. This includes developments in multi-axis machining, additive manufacturing integration, and intelligent automation systems. The rise of Industry 4.0 and the Internet of Things (IoT) are also influencing the future of CNC machining, introducing smarter, more connected manufacturing processes.
CNC machining can be expensive due to several key factors. First, the initial cost of purchasing and setting up CNC machines is significant. High-quality CNC machines are sophisticated pieces of equipment that come with a hefty price tag. Secondly, the materials used in CNC machining, especially specialized metals and composites, can be costly. Additionally, the tooling and consumables required for CNC machining, such as cutting tools and coolant, add to the overall expense. Skilled labor is another crucial component; CNC machinists and programmers require specialized training and expertise, which commands higher wages. Finally, maintaining and servicing CNC machines to ensure optimal performance involves ongoing costs. Although CNC machining may have higher upfront costs, the trade-off is the ability to produce high-quality, precise components efficiently, often resulting in cost savings in the long run due to reduced waste and faster production times.
CNC precision machining refers to the use of CNC machines to produce components with very tight tolerances and high levels of detail. This process involves the highly controlled and automated removal of material from a workpiece to achieve the desired geometric shape and specifications. Precision machining is critical in industries where even the smallest deviation can lead to significant issues, such as aerospace, healthcare, automotive, and electronics. The process utilizes various cutting tools, which are programmed to follow exact paths and sequences to shape the material. Precision machining allows for the production of complex parts with consistent accuracy and repeatability. The integration of advanced CNC technology, such as multi-axis machining and real-time feedback systems, further enhances the precision capabilities, enabling manufacturers to meet the stringent requirements of high-tech applications.
CNC machining for medical applications can be stressful due to the extreme precision and quality standards required. Medical components, such as implants and surgical tools, must meet strict tolerances, often within microns, as even the slightest deviation can affect performance or patient safety. Additionally, CNC machinists in the medical industry must work with challenging materials like titanium and stainless steel, which require specialized tooling and techniques. The pressure to avoid errors, coupled with tight production deadlines and regulatory compliance (such as ISO 13485), can make this field demanding. However, advancements in automation, high-speed machining, and real-time quality control have helped reduce stress by improving consistency and minimizing human errors. Skilled machinists who are well-trained in precision CNC processes, programming, and machine maintenance can better manage stress and ensure high-quality output, making medical CNC machining both challenging and rewarding.
CNC machining and forging serve different purposes, and their strength depends on the application. Forging compresses metal under extreme pressure, aligning the grain structure for enhanced toughness and durability, making it ideal for heavy-duty applications. However, CNC machining excels in high-precision applications, such as medical devices, where tight tolerances, smooth finishes, and complex geometries are required. CNC-machined medical implants, like orthopedic screws or dental prosthetics, need to be biocompatible and dimensionally accurate, which forging alone cannot achieve. While forging may create stronger bulk material, CNC machining allows for precise customization, superior surface finishes, and the ability to manufacture intricate medical components that meet regulatory standards. In some cases, a combination of both processes is used—forge the material for strength and CNC machine it for accuracy and detailed finishing.
High precision is critical in medical CNC machining and is overwhelmingly good, but it comes with challenges. In the medical industry, implants, prosthetics, and surgical instruments require extreme accuracy to ensure compatibility with the human body. Tolerances as tight as ±0.0001 inches ensure that components fit seamlessly, reducing the risk of complications. High precision also minimizes material waste and enhances product reliability, making medical devices safer and more effective. However, achieving this level of accuracy can be costly and time-consuming. Specialized high-precision CNC machines, advanced metrology tools, and skilled operators are required to maintain consistency. Additionally, tighter tolerances may increase machining time and tool wear. While precision is beneficial, the key is balancing accuracy with efficiency, ensuring that medical components meet stringent standards without unnecessary costs or delays.
Machining precision is categorized into different levels, depending on the application and industry standards. In medical CNC machining, the following precision levels are commonly used:
Standard Precision (±0.01 inches or more) – Suitable for general manufacturing but rarely used in medical applications.
High Precision (±0.001 inches) – Common in aerospace and medical industries for components requiring tighter tolerances.
Ultra-Precision (±0.0001 inches) – Necessary for implants, micro-surgical instruments, and high-performance medical devices.
Nano Precision (±0.00001 inches or below) – Used in cutting-edge medical and scientific research, such as microfluidic devices or nano-implants.
In medical CNC machining, ultra-precision is the most critical level, ensuring that parts integrate seamlessly with human anatomy. Achieving this requires advanced CNC equipment, real-time monitoring, and precision tooling.
Patient Safety and Biocompatibility – In medical CNC machining, precision is crucial to ensure that implants and devices fit correctly and function reliably. A minor deviation in an orthopedic screw or a prosthetic joint can lead to discomfort, rejection, or even surgical failure. Precision machining ensures smooth, contamination-free surfaces that reduce infection risks and enhance biocompatibility.
Regulatory Compliance and Performance Standards – Medical components must adhere to strict industry standards, such as ISO 13485 and FDA regulations. High-precision machining guarantees that parts meet these quality requirements, ensuring functionality, durability, and reliability. Any deviation can result in recalls, legal issues, or patient harm. Precision also contributes to repeatability, allowing manufacturers to produce identical, high-quality medical components in large volumes.
CNC precision technology refers to advanced machining techniques that allow manufacturers to produce highly accurate and intricate components. In medical applications, precision CNC machines use multi-axis control, ultra-fine tooling, and real-time feedback systems to achieve tolerances as tight as ±0.0001 inches.
Key features include:
Computer-Aided Manufacturing (CAM) for precise programming
Automated tool changers for efficiency and consistency
High-speed spindles for smooth surface finishes
Real-time quality monitoring to detect defects early
This technology is vital for medical devices such as implants, prosthetics, and surgical instruments, where accuracy directly impacts patient health. By integrating CNC precision technology with high-performance materials like titanium and stainless steel, medical manufacturers can ensure reliability, longevity, and safety in their products.
High-performance machining (HPM) in medical CNC machining refers to the use of advanced cutting techniques, high-speed spindles, and optimized tool paths to increase efficiency and accuracy while maintaining superior quality. Medical components, such as implants and surgical tools, require precision within microns, and HPM ensures that parts are produced faster without compromising precision.
Key features of HPM include:
High-speed cutting (HSC) to minimize cycle times
Advanced tooling materials, such as diamond-coated or carbide tools, for durability
Real-time monitoring to maintain tight tolerances
Optimized coolant systems to prevent material deformation
HPM is crucial in medical CNC machining because it enables manufacturers to produce high volumes of intricate parts while reducing tool wear, improving surface finishes, and maintaining regulatory compliance. This process ensures that medical devices meet industry standards such as ISO 13485 and FDA requirements, making them safe for patient use.
High-precision machining in medical CNC applications refers to the ability to produce parts with extreme accuracy, often within ±0.0001 inches. This level of precision is essential for components such as orthopedic implants, dental prosthetics, and micro-surgical instruments, where even the smallest deviation can impact functionality and patient safety.
To achieve high precision, manufacturers utilize:
Multi-axis CNC machines (e.g., 5-axis machining) for complex geometries
Laser measurement and quality control systems for real-time adjustments
Advanced software integration (CAD/CAM) to optimize machining strategies
Ultra-fine tooling and vibration control to ensure smooth, defect-free surfaces
High-precision machining ensures that medical components are biocompatible, durable, and free from defects. This process is critical in the medical field, as poor precision can lead to surgical failures, discomfort, or regulatory non-compliance. As a result, high-precision machining plays a crucial role in producing life-saving medical devices.
High-precision manufacturing in medical CNC machining refers to the end-to-end process of designing, fabricating, and inspecting medical components with ultra-tight tolerances. Unlike standard manufacturing, which allows for slight deviations, high-precision manufacturing ensures that every part is identical, flawless, and meets strict industry regulations.
This approach involves:
High-speed CNC machining for accuracy and repeatability
Cleanroom environments to prevent contamination of medical parts
Automated inspection systems, such as CMM (Coordinate Measuring Machines), for quality control
Material traceability and compliance with medical standards like ISO 13485 and FDA regulations
Examples of high-precision medical components include pacemaker housings, spinal implants, and robotic-assisted surgical instruments. By integrating cutting-edge machining technology with strict quality control, high-precision manufacturing ensures that medical devices function reliably in critical healthcare applications, ultimately improving patient outcomes.
High-Speed Machining (HSM) CNC is a specialized machining technique that enhances cutting speeds, reduces tool wear, and improves surface finishes—critical factors in medical CNC machining. HSM is particularly useful for machining titanium, stainless steel, and cobalt-chrome, which are commonly used in implants and medical instruments.
Key benefits of HSM CNC in medical applications include:
Reduced cycle times, increasing production efficiency
Minimized heat generation, preventing material distortion
Smoother surface finishes, ideal for biocompatibility and reducing bacterial adhesion
Enhanced tool life, reducing overall manufacturing costs
In medical machining, HSM allows for intricate, micro-level detailing required for parts like stents, bone plates, and surgical robotics. By combining HSM with multi-axis CNC machines, real-time monitoring, and ultra-fine cutting tools, manufacturers can achieve the highest precision and efficiency needed for medical-grade components.
CNC machines, especially those used in high-precision fields like medical machining, can consume a significant amount of electricity, but the actual usage depends on the size and type of machine. For medical applications, where precision and reliability are crucial, CNC machines are typically designed to operate efficiently while maintaining high accuracy. Larger machines or machines with multiple axes tend to consume more energy, as they require more motors and sophisticated control systems. Additionally, advanced features like cooling systems or laser integration can increase power consumption. However, in many cases, the energy efficiency of modern CNC equipment has improved due to advancements in technology and automation. For medical CNC machining, it’s essential to balance energy consumption with the need for accuracy and speed, ensuring that power use doesn’t negatively impact production costs or machine longevity.
Precision machining, particularly in the medical field, offers an extraordinary level of accuracy, often within microns (1/1000th of a millimeter). Medical components, such as implants, surgical instruments, or prosthetics, require tight tolerances to ensure they function correctly and safely. CNC machines are capable of achieving tolerances as low as 0.0001 inches, which is essential for producing high-quality medical parts that meet regulatory standards. The accuracy of the process depends on several factors, including the type of CNC machine used, the material being machined, and the skill of the operator. Advanced equipment with high-end controllers and sensors plays a key role in ensuring precise cuts and finishes, which are critical when manufacturing medical components that must perform under strict conditions.
Improving CNC accuracy, especially in precision medical machining, requires a combination of machine maintenance, operator skill, and process optimization. First, regularly calibrating and maintaining the CNC machine is crucial. This ensures that all axes, tools, and spindles operate within their specified tolerances. Second, using high-quality cutting tools that are specifically designed for medical-grade materials can reduce tool wear and improve precision. Third, machine operators should be well-trained in using the software and equipment, ensuring they can troubleshoot issues and make adjustments as needed. Additionally, investing in high-precision machines, like those with linear scales or high-precision encoders, will help further improve accuracy. Lastly, controlling environmental factors—like temperature and humidity—can prevent material expansion or contraction, which could affect precision.
The time required for CNC machining varies widely based on several factors, including the complexity of the part, material type, machine capabilities, and desired finish. For medical components, which often have intricate designs and need tight tolerances, CNC machining can take anywhere from a few hours to several days. Simpler parts might be completed in a few hours, while highly detailed, complex implants or surgical instruments could take longer. Factors like setup time, tool changes, and post-processing (e.g., polishing or coating) can also extend machining time. Generally, though, CNC machining for medical parts is faster than traditional manufacturing processes, especially for producing small, precise batches. Speed is also affected by the automation level of the process, with more advanced CNC machines offering faster cycle times.
The cost of CNC machining per hour can vary widely depending on the machine’s capabilities, material, and the specific requirements of the job. For high-precision medical CNC machining, rates generally range from $75 to $200 per hour, although more specialized or advanced machines may cost more. Factors like the complexity of the part, the precision needed, and post-processing requirements (e.g., cleaning, inspection, or coating) all affect the hourly rate. Medical-grade CNC machining requires additional considerations such as adherence to FDA standards and specific certification processes, which can also contribute to higher costs. Additionally, the experience level of the operator and any custom programming required will add to the hourly rate.
Precision machining costs in the medical field can range significantly, typically between $50 and $250 per hour, depending on the part’s complexity, material, and the precision required. Components that demand very tight tolerances, such as implants, surgical tools, or diagnostic devices, tend to be on the higher end of the price spectrum due to the sophisticated machinery and technical expertise involved. Additionally, material costs—such as medical-grade titanium, stainless steel, or polymers—can further influence the price. Labor costs, tooling, setup times, and post-machining operations (like finishing or sterilization) also contribute to the overall cost. Since precision medical machining often involves smaller production runs, the cost per part can be relatively high, but this is justified by the need for reliability and accuracy in life-saving applications.
Renting a CNC machine for medical machining is not as common as purchasing or leasing, but some companies may offer rental options, particularly for short-term projects or prototyping. Rates can vary depending on the machine type, size, and capabilities, but for high-precision machines used in medical CNC machining, rental costs typically range from $500 to $2,000 per day, or around $10,000 to $30,000 per month for long-term rentals. Specialized machines capable of ultra-precise work, like 5-axis CNC machines or those with laser engraving systems, can be on the higher end of the spectrum. Additionally, the cost may include technical support, maintenance, or even operator training. Renting can be a cost-effective solution for short-term projects or when specialized machinery is required without the commitment of a full purchase.
To reduce the cost of CNC machining, especially in the precision medical sector, several strategies can be implemented. First, optimizing part design is key—simplifying geometry or reducing the number of operations required can lower both machining time and tool wear, resulting in cost savings. Second, using less expensive materials (while still meeting medical standards) can significantly reduce costs. Third, improving machine efficiency through regular maintenance and calibration helps avoid downtime, reducing the overall cost per part. Fourth, outsourcing the job to contract manufacturers with high-capacity, automated machines can help reduce labor costs. Lastly, consolidating multiple machining operations into a single setup or optimizing the production process can minimize handling and machine setup time, making the process more cost-effective overall.
Whether CNC machining is cheaper than 3D printing depends on the specific application, material, and volume of production. For high-precision medical parts that require tight tolerances and a smooth finish, CNC machining is typically the more cost-effective option, especially for small to medium production runs. CNC machining is faster for these applications and produces parts with better mechanical properties compared to 3D printing. However, for more complex geometries or rapid prototyping, 3D printing can be cheaper, particularly in terms of initial setup costs. While 3D printing offers flexibility and reduced material waste, it may struggle to meet the precision and strength requirements of medical parts in comparison to CNC machining. Therefore, CNC machining remains the go-to for high-quality, precision-driven medical parts.
CNC machining can be cost-effective, particularly for high-precision, small- to medium-scale production runs in industries like medical manufacturing. While the initial investment in machinery and tooling can be significant, the ability to produce parts with high accuracy, repeatability, and minimal waste often results in long-term savings. For medical applications, where safety and precision are paramount, the cost of CNC machining is often justified by the need for reliability and compliance with strict regulatory standards. Additionally, advancements in automation, multi-axis machining, and tool management have made CNC machining more efficient, helping reduce costs over time. Though the process may be more expensive for low-volume production compared to traditional methods, its cost-effectiveness increases as part complexity and volume grow.
A Coordinate Measuring Machine (CMM) is crucial for high-quality precision medical CNC machining, as it is used to measure the physical geometrical characteristics of a part with high accuracy. CMM machines can achieve accuracies of up to 0.0001 inches (0.0025 mm) or better, depending on the type and configuration. For medical components, such as implants or surgical instruments, even the slightest deviation can affect performance, so high-precision measurements are essential. CMMs typically use probes (either contact or laser) to capture data and are highly effective for inspecting parts against CAD models. The accuracy of a CMM depends on factors such as the machine’s resolution, probe type, the environment in which it operates, and the skill of the operator. With proper calibration and environmental controls, CMMs offer an essential tool for ensuring that medical CNC-machined components meet stringent tolerance requirements.
One of the biggest disadvantages of using CNC for high-quality precision medical machining is the high upfront cost of equipment and tooling. CNC machines, especially those capable of high precision, can be quite expensive, and medical-grade machines with multi-axis capabilities or specialized features for materials like titanium or PEEK can be particularly costly. Additionally, maintaining CNC machines requires ongoing expenses, such as tooling replacement, software updates, and regular calibration to maintain accuracy. There is also a learning curve for operators to become proficient in handling advanced CNC machines. For small-run or custom parts, the cost of setup and programming time can make CNC machining less cost-effective compared to other methods. Moreover, CNC machining often involves material waste, especially when working with high-cost medical materials, which can be another disadvantage in terms of cost efficiency.
In machining, accuracy refers to how closely a part’s dimensions match the desired or target dimensions, whereas precision refers to the consistency or repeatability of the machining process over time. In the context of high-quality medical CNC machining, accuracy is critical to ensuring that parts—such as implants or surgical tools—fit within tight tolerances and perform correctly. Precision, on the other hand, is necessary to ensure that each part produced is consistent, with minimal variation from one piece to another, ensuring reliability in mass production. A machine can be precise without being accurate if it consistently produces parts that are slightly off the target dimension. Conversely, a machine can be accurate but not precise if it occasionally produces parts that meet the target but varies significantly between parts. Both high accuracy and high precision are crucial for medical machining, where both reliability and safety are paramount.
CNC machining and precision machining both aim to create high-quality parts, but the terms differ in scope. CNC machining refers to the use of computer-controlled machines to automate the machining process, often involving milling, turning, or drilling. This technology allows for complex geometries and high repeatability. Precision machining, however, specifically refers to processes that achieve very tight tolerances, typically in the micron or sub-micron range. In high-quality medical CNC machining, precision machining ensures that parts meet stringent quality standards, such as those required for implants or medical instruments. While CNC machining can be precise, the term “precision machining” emphasizes the meticulousness of the process, particularly when working with high-end materials and demanding applications like medical device manufacturing. Thus, precision machining is a subset of CNC machining that focuses on achieving extremely tight tolerances and high-quality finishes.
In machining, high accuracy means that a part’s dimensions closely match the target dimensions, while high precision refers to the ability of a machine or process to consistently reproduce parts with minimal variation. In high-quality medical CNC machining, both are crucial, but they serve different purposes. High accuracy ensures that individual medical components—such as implants, surgical tools, or diagnostic devices—fit precisely into their intended applications and meet safety requirements. High precision, on the other hand, is necessary to ensure that these components are consistently manufactured to the same specifications, especially when producing large volumes of identical parts. While both accuracy and precision are necessary, achieving high accuracy ensures that each part is correct, while high precision ensures that the process will consistently produce parts within those exact specifications, minimizing variability and improving the overall quality of medical devices.
The hardest material to CNC, particularly in the context of high-quality medical machining, is typically a material like cobalt-chromium or certain types of titanium alloys, such as Ti-6Al-4V. These materials are commonly used in medical implants and surgical instruments due to their strength, corrosion resistance, and biocompatibility. However, their hardness makes them challenging to machine. Titanium alloys, for example, have high strength and low thermal conductivity, which can cause tools to wear out quickly and generate heat during the machining process. Cobalt-chromium alloys, while excellent for wear resistance, also present challenges due to their hardness and brittleness. To effectively machine these materials, advanced tooling, higher spindle speeds, and precise cooling methods are necessary. For medical CNC machining, the ability to accurately machine these tough materials while preserving their properties is critical for ensuring the quality and functionality of the final product.
The highest accuracy in machining, especially in the field of high-quality medical CNC machining, can reach tolerances as tight as ±0.0001 inches (±0.0025 mm) or even finer. This level of precision is required for the production of medical devices like implants, prosthetics, and surgical instruments, where even the slightest deviation could affect the safety and functionality of the product. Achieving such accuracy requires a combination of advanced CNC equipment, skilled operators, and carefully controlled environmental conditions. Machines with multi-axis capabilities, precision spindles, and high-end sensors play a key role in reaching these tolerances. Additionally, advanced measuring tools such as CMMs (Coordinate Measuring Machines) are used to verify the accuracy of the machined parts, ensuring that they meet the required specifications. In high-precision medical machining, accuracy is critical to meet regulatory requirements and ensure the safety and performance of the end product.
The highest tolerance CNC machining typically achieves tolerances of ±0.0001 inches (±0.0025 mm) or better, particularly for precision medical machining applications. Tighter tolerances are often required for medical devices such as orthopedic implants, pacemaker components, and surgical instruments, where even a small deviation could result in failure or complications. Achieving these tolerances demands a combination of advanced CNC equipment, specialized tooling, and meticulous control over the machining environment. Multi-axis CNC machines with high-end spindles and feedback systems, as well as advanced measuring tools like CMMs, are necessary for such precise work. In addition, the use of premium materials and precise programming ensures that parts are machined within the specified tolerances. While CNC machines are capable of high tolerance levels, the specific tolerance achievable depends on the machine’s capabilities, tooling, and the complexity of the part being produced.
The most accurate CNC machines used in high-quality precision medical machining are typically optical CNC machines and ultra-precision CNC grinders. These machines can achieve tolerances as tight as ±0.0001 inches (±0.0025 mm) or even better, which is essential for medical components like implants and surgical instruments. One example is the Jena ultra-precision CNC machine, which is designed specifically for high-accuracy applications. These machines incorporate advanced feedback systems, such as laser interferometers, and can operate under tightly controlled environmental conditions to minimize errors caused by vibration, temperature fluctuations, and mechanical wear. Advanced features like air bearings, linear encoders, and multi-axis control contribute to these machines’ ability to achieve unparalleled accuracy, which is critical in the production of medical devices that must meet strict regulatory standards and ensure patient safety.
The most advanced CNC machines in the field of high-quality precision medical machining are 5-axis CNC machines. These machines can machine complex geometries with extreme precision and are ideal for creating intricate medical components such as implants, prosthetics, and surgical tools. A leading example of advanced CNC technology is the DMG MORI LASERTEC 65 3D, which combines additive manufacturing (laser deposition) with CNC machining. This hybrid system allows for ultra-precise, customized production of complex medical parts, reducing material waste and production time. Advanced CNC machines also incorporate multi-axis capabilities, integrated automation, and real-time monitoring systems, all of which help improve both the speed and quality of the machining process. With the ability to handle multiple materials, these machines are crucial in medical machining for achieving highly accurate results in a cost-effective manner.
The most expensive CNC machines are typically those designed for ultra-precision or aerospace applications, where tolerances are exceptionally tight. For high-quality medical CNC machining, some of the most expensive machines are ultra-precision CNC machines with capabilities to achieve tolerances in the sub-micron range. One such machine is the Nakamura-Tome NTY3-200, which can cost upwards of $1 million. These machines are equipped with features like high-speed spindles, advanced cooling systems, and precision encoders that make them capable of producing the highly detailed and intricate medical components required in surgeries or implants. Another expensive machine is the Mikron HPM 800U, a 5-axis machining center used for complex parts that demand extreme precision. The high cost of these machines reflects the combination of advanced technology, precision engineering, and the capability to produce medical components to the most stringent standards.
In high-quality precision medical CNC machining, the tightest machining tolerances achievable are typically ±0.00005 inches (±0.00127 mm), which is often referred to as ultra-precision machining. These tight tolerances are essential when manufacturing critical medical components like artificial joints, surgical instruments, or micro-medical devices, where even the smallest error could have significant implications for patient safety and device functionality. Achieving such tight tolerances requires a combination of high-end CNC machines, specialized tooling, advanced software, and a controlled manufacturing environment. Moreover, techniques like laser interferometry and CMM (Coordinate Measuring Machines) are frequently employed to ensure that the dimensions of the parts meet the specified tolerances. These processes are standard in the medical field to guarantee that every part, whether it’s a prosthetic or an implant, meets the rigorous standards demanded for patient care.
For precision machining in the medical field, tolerances typically range from ±0.0001 inches (±0.0025 mm) to ±0.001 inches (±0.025 mm), depending on the complexity and application of the part. In high-quality medical CNC machining, such as the manufacturing of prosthetic components or surgical instruments, tighter tolerances are often required to ensure the proper function and fit of the device. These tight tolerances are critical for minimizing the risk of complications during surgeries and ensuring the long-term effectiveness of medical devices. Precision machining is defined by the ability to produce parts with minimal deviation from the design specifications, ensuring reliability and performance in the final product. The higher the tolerance, the more specialized the machining equipment and tooling need to be, which is why precision machining in medical applications often involves the use of high-precision CNC machines.
The tolerance standard for machining is typically governed by international standards like ISO 2768, which outlines general tolerances for linear dimensions, angular dimensions, and geometrical tolerances. For high-quality precision medical CNC machining, a tolerance standard of ±0.0001 inches (±0.0025 mm) is often required for components that must meet strict medical and regulatory requirements. These parts, such as implants or surgical tools, must be manufactured to very tight tolerances to ensure proper fit, function, and safety. Standards set by organizations like the FDA and ISO also influence the tolerances applied in the medical device industry, where high accuracy and reliability are critical. In practice, these tolerances are determined by the complexity of the part and its intended function in the human body. Tighter tolerances are typically achieved using CNC machines with multi-axis capabilities and advanced measuring tools, such as CMMs.
The top 5 accuracy metrics in high-quality precision medical CNC machining typically include:
Positional Accuracy: This refers to the ability of a CNC machine to position the tool at the desired location with high precision. For medical components, this is critical for ensuring proper fit and function.
Geometric Tolerances: Geometric accuracy involves ensuring that the shape and form of the machined part match the design specifications. This is especially important for medical implants and surgical tools.
Surface Finish: High-quality surface finishes (such as Ra or Rz values) are important for ensuring that parts are smooth and free of defects, particularly in medical devices that must avoid contamination or irritation.
Repeatability: The ability of a CNC machine to repeatedly produce the same part to the same specifications, which is essential for high-volume production of medical parts.
Dimensional Tolerance: The tolerance for the dimensions of parts, often expressed in microns or sub-microns for high-precision medical machining, ensuring that each part meets the design specifications without deviation.
Ultra-precision machining is a highly specialized form of machining that can achieve tolerances as tight as ±0.000001 inches (±0.000025 mm), making it essential for the production of medical components that require extreme accuracy, such as microsurgical instruments, implantable devices, and precision diagnostics equipment. This process utilizes advanced equipment such as air-bearing spindles, diamond tools, and laser interferometry to create parts with extremely smooth surfaces and minimal dimensional variation. Ultra-precision machining is performed in environmentally controlled rooms to avoid errors caused by vibrations, temperature fluctuations, or airborne contaminants. The process is typically used for highly detailed parts that require not only dimensional precision but also surface integrity. By combining multi-axis CNC technology with specialized cutting techniques, ultra-precision machining ensures that the manufactured parts meet strict regulatory requirements and high-performance standards, crucial in medical applications.
To make high-precision measurements in high-quality medical CNC machining, several tools are employed, with the most common being Coordinate Measuring Machines (CMMs). These machines use a probe (either contact or non-contact) to measure the part’s geometry against its CAD model. Laser interferometers are also used for ultra-precise measurements, particularly in ultra-precision machining, to detect even the smallest deviations in position. Other tools include optical microscopes and scanning electron microscopes (SEMs) for measuring surface roughness or fine features on the micrometer or nanometer scale. Additionally, micrometers, calipers, and height gauges are commonly used for routine measurements on less complex parts. In the context of high-quality medical CNC machining, these tools are essential to ensure that parts meet strict tolerances and safety standards, as even the smallest measurement discrepancy can have a significant impact on device performance and patient safety.
Contact our professional team now for a same-day quote and risk-free project evaluation. Benefit from ISO 8 cleanrooms, advanced machines, and 12-hour fast response in medical injection molding.