Prototype medical equipment molds are specialized tools used to create initial, functional models of medical devices before mass production. These molds allow manufacturers to test the design, functionality, and safety of a device, ensuring it meets regulatory standards. Prototypes medical molded plastic play a crucial role in this process, enabling precise testing and refinement of the device’s features. Prototyping is a critical step in medical device plastic manufacturing because it enables companies to detect and address potential issues early in the development process. Using prototype medical equipment molds offers key benefits, including cost efficiency by avoiding large-scale production errors, risk reduction by identifying design flaws, and faster iteration cycles for improving device functionality. These molds play a vital role in producing high-quality, compliant medical devices that can be safely used in healthcare settings. Prototype medical equipment molds create functional medical device models, using rapid prototyping and injection molding to streamline production and maximize profits.
Low-Volume to High-Volume Production Capabilities
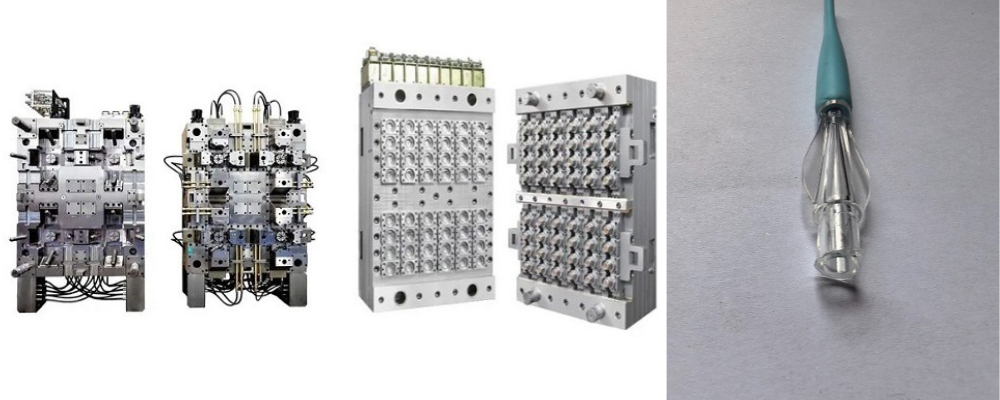
Attributes | Details |
---|---|
Place of Origin | Dongguan, Guangdong, China |
Brand Name | LY Medical Injection Mold |
Product Name | Medical Injection Mold |
Plastic Processing | Polypropylene, ABS, Polyvinyl Chloride, Polyethylene |
Process | Injection Molding |
Size | Customized Size |
Color | Customized Color |
Mold | Customizable |
Shape | Customized Shapes |
Certification | ISO9001 |
Tolerance | 0.02mm-0.05mm |
Drawing Format | STEP/STP/IGS/XT/STL/CAD/PDF/DWG and Others |
Mold Life | 500000 shots |
Service | OEM |
Workshop | ISO13485 cleanroom |
Operation Language | English/Chinese or Others |
Sales Unit | Single Item |
Why Are Prototype Medical Equipment Molds Crucial in Medical Device Manufacturing?
Prototype medical equipment molds are essential in medical device manufacturing for several reasons, playing a critical role in ensuring devices are safe, effective, and compliant with industry standards.
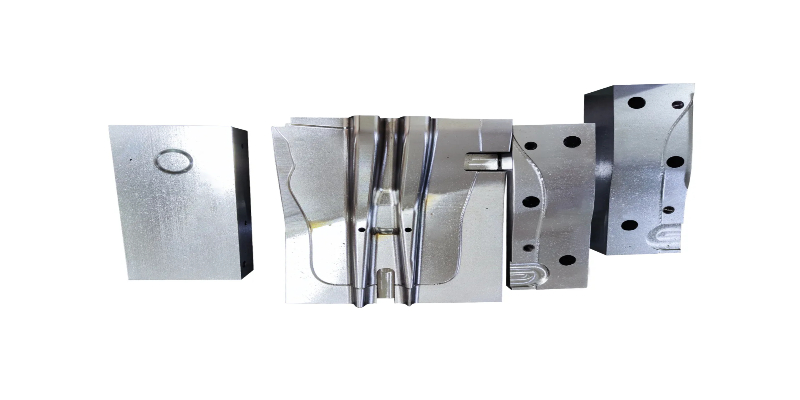
Risk Mitigation
Prototype medical equipment molds allow manufacturers to identify design flaws early in development. By creating a physical prototype, companies can evaluate the functionality and usability of a device before committing to large-scale production. Early testing helps pinpoint issues such as material weaknesses, ergonomic flaws, or mechanical failures, reducing the risk of costly recalls or regulatory setbacks later on. This proactive approach is vital for minimizing the risk of introducing faulty or unsafe devices to the market.
Cost Efficiency
Using prototype medical equipment molds is more cost-effective compared to full-scale production. By creating prototypes, manufacturers can test different materials and designs without the financial burden of producing thousands of units. This allows companies to refine their products while keeping costs manageable. Furthermore, prototyping reduces the likelihood of expensive design revisions during the production phase, saving both time and money in the long run.
Regulatory Compliance
Adhering to stringent medical standards is a critical aspect of developing medical devices. Prototype medical equipment molds help ensure that a device meets all necessary regulatory requirements by allowing for thorough testing and evaluation before the final product is mass-produced. This process ensures that the device complies with safety, performance, and quality standards, minimizing the risk of regulatory non-compliance that could delay product approval.
Enhanced Iteration
Prototype medical equipment molds facilitate quick testing and refinement of designs. This iterative process enables manufacturers to assess and adjust the device’s design based on real-world testing and feedback. Whether it’s adjusting the size, improving functionality, or ensuring compatibility with other medical systems, prototype molds allow for rapid changes to optimize the device before it enters full-scale production. This enhanced iteration process is critical for developing high-quality, market-ready medical equipment.
Steps in the Prototype Medical Equipment Molds Prototyping Process
The process of creating prototype medical equipment molds involves several key steps that ensure the device is functional, safe, and ready for mass production. These steps guide the development of medical devices from concept to pre-production, addressing both design and regulatory requirements along the way.
Requirement Analysis: Defining Device Specifications and Clinical Needs
The first step in the prototyping process is conducting a thorough requirement analysis. This involves defining the device’s specifications, including its size, function, and the clinical needs it must address. During this phase, medical professionals, engineers, and designers work together to understand the intended use of the device, the medical conditions it aims to treat, and the target patients. Identifying clinical needs and device functionality helps create a clear framework for the prototype medical equipment molds. This ensures that the prototype is designed with the necessary features to meet both medical standards and user requirements, forming the foundation for the subsequent design process.
Conceptual Design: Initial Sketches and CAD Modeling
Once the device requirements are clear, the next step is conceptual design. During this phase, initial sketches and 3D computer-aided design (CAD) models are created. These designs represent the first detailed visualizations of the medical device, providing a foundation for more precise development. CAD modeling is particularly useful as it allows designers to experiment with different forms, functions, and materials before moving to the prototyping stage. For prototype medical equipment molds, these designs are essential for ensuring that the device will fit together, function correctly, and meet the clinical needs defined earlier. The conceptual design stage is crucial for visualizing how the device will interact with patients and medical professionals.
Prototype Creation: Material Selection and Fabrication
The next step in the process is prototype creation, where the conceptual designs are turned into physical models. This involves selecting appropriate materials that are biocompatible, durable, and capable of withstanding the medical environment. For medical devices, materials must also comply with stringent regulatory standards to ensure patient safety. Common materials include medical-grade plastics, metals, and ceramics, each chosen based on their suitability for the device’s function.
Once the material is selected, prototype medical equipment molds are fabricated using various methods, such as CNC machining, 3D printing, or injection medical molding. CNC machining allows for precise shaping of materials, while 3D printing enables rapid prototyping with complex geometries. Injection molding is often used for larger production runs to create high-quality, consistent parts. Medical molding products, created through these fabrication methods, ensure that the prototype medical equipment molds accurately represent the intended device. These processes help achieve the precision and reliability required for medical devices, ensuring they meet industry standards.
Testing and Validation: Functional, Usability, and Safety Testing
Once the prototype is created, it must undergo rigorous testing to ensure that it functions as expected and meets all safety requirements. This phase involves functional testing, where the prototype is tested under real-world conditions to assess its performance. Usability testing is conducted to ensure that the device is user-friendly and intuitive for medical professionals or patients. Additionally, safety testing is essential to confirm that the prototype does not pose any risks to health, such as causing infections or malfunctions during use. Testing is a critical step in validating the prototype medical equipment molds, ensuring that any potential issues are identified and addressed before moving forward with mass production.
Iteration: Refining the Mold and Prototype for Optimal Performance
The final step in the process is iteration, where the mold and prototype undergo continuous refinement to optimize performance. Based on feedback from testing, design flaws or areas for improvement are addressed, and adjustments are made to enhance the device’s functionality, safety, and ease of use. This iterative process allows for fine-tuning the prototype medical equipment molds, ensuring that the final product is as effective and efficient as possible. During this stage, minor design changes may be implemented, and prototypes are retested until the device meets all required standards. Iteration helps ensure that the final medical device is ready for production, with all performance and safety concerns resolved.
Each of these steps plays a vital role in creating high-quality prototype medical equipment molds that are safe, functional, and compliant with industry standards. By following a structured prototyping process, manufacturers can reduce risks, improve device performance, and expedite the time to market for new medical devices.
Challenges in Prototype Medical Equipment Molds
Prototyping medical equipment, particularly when developing prototype medical equipment molds, presents several challenges that can complicate the process. These challenges stem from the complexity of medical device design, regulatory requirements, and the need for high precision. Below are some of the key difficulties encountered during the prototyping phase.
High Costs: Prototyping Can Be Expensive Due to Material and Precision Requirements
One of the most significant challenges in medical equipment prototyping is the high cost associated with the development of prototype medical equipment molds. The materials required for medical devices must meet rigorous standards for biocompatibility, durability, and safety, all of which come with a higher price tag. Additionally, the fabrication processes involved, such as CNC machining, injection molding, and 3D printing, require specialized equipment and highly skilled labor, further driving up costs. The need for precision medical molds, especially when working with complex medical devices, adds to the financial burden, as fine-tuning the prototype molds for accuracy can take considerable time and resources. In some cases, multiple iterations are necessary before the mold achieves the desired specifications, making prototyping an expensive and resource-intensive process.
Complexity: Difficulties in Achieving Accuracy for Intricate Medical Devices
Another major challenge in prototyping medical equipment is the complexity involved in achieving the required level of accuracy, especially for intricate devices. Many medical devices, such as surgical instruments, implants, or diagnostic tools, must be precisely engineered to ensure proper functionality and patient safety. Prototype medical equipment molds must reflect the exact design specifications, including fine details and tolerances that can be difficult to achieve with the available manufacturing processes. Small errors or inconsistencies in the mold can lead to defects in the final product, which could compromise its effectiveness and safety. Achieving the necessary level of detail often requires advanced technology and expertise, making it more challenging to create flawless prototype molds that meet the exact standards.
Time Constraints: Balancing Quick Iterations with Thorough Testing
Time constraints represent another challenge in the prototyping process for medical equipment. Medical device development often operates under tight deadlines, particularly when a new device is needed urgently to address healthcare needs or regulatory requirements. While rapid prototyping methods such as 3D printing can expedite the creation of prototype medical equipment molds, there is a delicate balance between moving quickly and ensuring thorough testing. Medical devices must undergo rigorous testing to meet safety and regulatory standards, which takes time. However, designers and manufacturers often face pressure to shorten the prototyping phase to accelerate the product’s time to market. This rush can compromise the depth of testing, leading to potential issues being overlooked and affecting the quality of the final product. Iterative testing and validation cycles are necessary to ensure that the prototype medical molds work effectively, but time constraints can limit how thoroughly this process is executed.
Best Practices for Medical Device Prototype Molds
Creating high-quality prototype medical equipment molds is a critical step in ensuring that medical devices are functional, safe, and ready for production. Following best practices can significantly improve the efficiency and success of the prototyping process, helping to meet regulatory requirements, reduce costs, and streamline the production process. Below are some key practices that manufacturers should consider when developing prototype medical equipment molds.
Early Integration of DFM (Design for Manufacturability): Simplify Designs to Ensure Production Efficiency
One of the most effective strategies for producing high-quality prototype medical equipment molds is the early integration of DFM (Design for Manufacturability). DFM is a design approach focused on simplifying and optimizing the design to ensure that the device can be manufactured efficiently and at a lower cost. By considering manufacturability early in the design phase, engineers can identify potential challenges and refine the design to eliminate unnecessary complexities. This includes minimizing part count, choosing materials that are easier to work with, and ensuring that the design can be efficiently scaled for mass production. Implementing DFM principles in the early stages of prototype creation can not only reduce the cost of producing prototype medical equipment molds but also lead to faster and smoother transitions from prototyping to full-scale manufacturing.
Collaboration with Experts: Engage Engineers and Healthcare Professionals for Insights
Another best practice when developing prototype medical equipment molds is to collaborate closely with experts, including engineers, healthcare professionals, and regulatory specialists. Engaging these professionals early in the process can provide valuable insights into the device’s performance, usability, and regulatory requirements. Engineers can offer advice on material selection, mold design, and manufacturing processes to ensure that the prototype is both functional and cost-effective. Healthcare professionals can provide real-world feedback on the usability of the design, ensuring that the device will meet the practical needs of patients and healthcare providers. Additionally, regulatory specialists can help align the prototype design with the stringent medical device regulations that must be followed to gain approval for market entry. By involving these experts throughout the prototyping process, manufacturers can create better, more reliable prototype medical equipment molds that are ready for clinical trials and production.
Leverage Advanced Tools: Use Cutting-Edge Technologies like Simulation Software and Precision Machining
To improve the accuracy and efficiency of prototype medical equipment molds, it is essential to leverage advanced tools and technologies. Modern simulation software can be used to model the behavior of the mold under different conditions, allowing manufacturers to predict potential issues before the mold is physically created. This software can help optimize the design by identifying weak points, thermal effects, or stresses that could affect the mold’s performance. Additionally, precision machining and 3D printing technologies enable the creation of highly detailed, accurate molds with tight tolerances. By utilizing these advanced technologies, manufacturers can reduce the number of iterations needed, improve the overall quality of the prototype, and shorten the time required for testing and validation. These tools not only streamline the prototyping process but also ensure that the final prototype medical equipment molds are of the highest possible quality.
Focus on Regulatory Standards: Align Prototype Designs with Medical Device Compliance Requirements
Medical device prototyping involves stringent regulatory requirements to ensure that the devices are safe and effective for patient use. As such, it is essential to focus on regulatory standards when designing prototype medical equipment molds. This involves ensuring that the design, materials, and manufacturing processes comply with international medical device regulations, such as those set by the FDA, ISO, or CE. Manufacturers must ensure that the materials used are biocompatible, durable, and able to withstand sterilization processes required for medical devices. The prototype molds should also be designed to meet functional performance requirements, ensuring that the final device performs reliably in clinical settings. Focusing on compliance early in the design phase can help avoid costly redesigns and delays later in the process. It also accelerates the approval process, allowing the device to reach the market faster while maintaining patient safety.
Prototype Mold Tool Design for Medical Devices
Prototype medical equipment molds plays a crucial role in the development of medical devices, as it directly impacts the accuracy, functionality, and manufacturability of the final product. The mold tool is the foundation upon which a prototype is created, ensuring that the medical device is formed with precise specifications and quality. When designing prototype molds for medical devices, several factors need to be considered to ensure the success of the prototyping process.
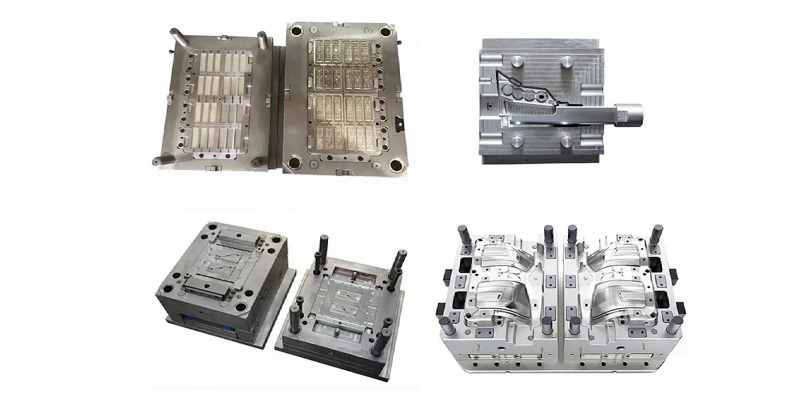
Key Considerations for Prototype Mold Tool Design
- Material Selection: The choice of material for the mold tool is one of the most critical aspects. For medical device prototypes, biocompatible materials that meet the required safety standards are essential. Mold tools are typically made from steel, aluminum, or softer tool steels depending on the complexity and volume of the prototype. Materials must also withstand the pressure and temperature requirements during the medical injection molding process without compromising the integrity of the device.
- Mold Design Complexity: Prototype mold design for medical devices must carefully balance complexity with functionality. The design should incorporate features that allow easy flow of materials, such as runners and gates, while minimizing any potential for defects. Molds for medical devices may have intricate features such as thin walls or microstructures that require high precision in design and manufacturing to ensure the prototype’s functionality.
- Tooling Lifecycle: Prototype molds often undergo multiple iterations as designs are refined and tested. Therefore, the design of the tool should allow for ease of modification and reusability. This flexibility helps manufacturers adjust the mold quickly without excessive retooling costs, enabling them to perform iterative testing and refinement efficiently.
- Tolerance and Accuracy: Medical devices require extremely tight tolerances, and the mold tool design must accommodate this requirement. Small deviations in mold accuracy can lead to defects in the prototype, which could impact the device’s performance, functionality, and safety. Advanced precision machining and quality control practices are necessary to achieve the required accuracy in the medical mold design.
- Regulatory Compliance: Mold tool design must adhere to the strict guidelines and regulations set forth by health authorities, such as the FDA or ISO standards. The mold must be designed with sterilization in mind, as many medical devices require sterilization before use. Ensuring that the tool can handle sterilization processes without degradation or contamination is crucial.
How to Choose a Prototype Medical Equipment Molds Supplier
Selecting the right prototype medical equipment molds supplier is crucial for ensuring high-quality, precise, and regulatory-compliant medical device components. A good supplier should offer expertise in mold manufacturing, advanced technology, and reliable customer support. This guide explores key factors to consider when choosing a supplier, helping you make an informed decision that aligns with your production needs.
Industry Experience and Expertise
A supplier’s experience in medical device prototyping directly impacts mold quality and performance.
- Look for suppliers with a proven track record in medical mold manufacturing.
- Ensure they understand regulatory standards like FDA, ISO 13485, and USP Class VI.
- Check their previous projects to assess their expertise in handling complex designs.
Manufacturing Capabilities and Technology
The right supplier should have cutting-edge technology to create accurate and high-quality prototypes.
- Ensure they use advanced CNC machining, 3D printing, and rapid tooling for precision.
- Verify their ability to handle multi-cavity, overmolding, and insert molding processes.
- Evaluate their material selection, especially for biocompatible and sterilizable plastics.
Customization and Design Support
A good supplier should offer design flexibility and engineering support to refine your prototype.
- Look for custom mold design services tailored to your medical device.
- Choose a supplier who provides DFM (Design for Manufacturability) analysis to optimize production.
- Confirm their ability to modify and improve prototype designs based on testing results.
Production Speed and Lead Times
Rapid prototyping is essential for accelerating medical device development and market launch.
- Check if they offer quick turnaround times for prototype mold creation.
- Ask about their capacity for low-volume production before full-scale manufacturing.
- Ensure they have efficient logistics to meet your deadlines without compromising quality.
Quality Control and Compliance
Medical device molds require strict quality control to ensure product safety and reliability.
- Verify if they follow ISO 9001 and ISO 13485 quality management systems.
- Ask about their testing procedures, including dimensional inspection and material verification.
- Ensure they provide detailed reports and certifications for compliance with medical standards.
Cost Efficiency and Scalability
A supplier should provide cost-effective solutions while supporting long-term scalability.
- Compare pricing models and choose a supplier offering transparent cost breakdowns.
- Ensure they balance affordability with high-quality mold materials and production efficiency.
- Check if they can scale production from prototypes to high-volume manufacturing.
By considering these factors, you can select a prototype medical equipment molds supplier that meets your technical requirements, regulatory needs, and production goals.
Applications of Prototype Medical Equipment Molds in Various Medical Devices
Prototype medical equipment molds play a critical role in the development of a wide range of medical devices, enabling manufacturers to test, refine, and validate designs before mass production. These molds are used to create functional prototypes of components that must meet stringent safety, performance, and regulatory standards. From diagnostic tools to surgical instruments, prototype molds help ensure that medical products are both functional and compliant. The following sections will explore the different types of medical equipment components where prototype medical equipment molds can be applied, offering insight into their versatility and importance across the healthcare industry.
Surgical Instruments and Tools
Prototype medical equipment molds are extensively used in the development of surgical instruments and tools, where precision and ergonomics are essential for performance and safety.
- Surgical tools, including scalpels, forceps, and clamps, require precise manufacturing to ensure safe and efficient usage. Prototype molds help simulate the feel and functionality of these instruments before full-scale production.
- These molds allow designers to test the ergonomics and durability of handles, cutting edges, and tips under simulated conditions.
- Medical-grade materials used in these molds ensure that the final product is suitable for sterilization and repeated use in clinical environments.
By utilizing prototype molds, manufacturers can refine designs for surgical tools, reducing the risk of defects and ensuring a smooth transition to production.
Diagnostic Equipment Components
Prototype molds are also essential for the development of components used in diagnostic equipment, such as sensors, housings, and interfaces.
- Diagnostic devices, including ultrasound machines, MRI scanners, and blood analyzers, require highly precise components that interface with both human operators and the patients.
- Prototypes for sensor housings and control panels are often created using prototype molds to test ease of use, compatibility, and function before mass manufacturing.
- These molds help create components that are biocompatible, ensuring that any part that comes into contact with patients or bodily fluids meets stringent medical standards.
In the case of diagnostic equipment, prototype medical molds are key to ensuring reliability and accuracy in critical health diagnostics.
Implantable Medical Devices
For implantable devices, prototype molds allow manufacturers to produce highly specialized components that meet strict regulatory standards.
- Implantable devices such as pacemakers, stents, and orthopedic implants require prototypes to validate their form, fit, and biocompatibility before full-scale production.
- Prototype molds for implantable devices are typically used to create models of intricate parts that may involve complex geometries and need to ensure the highest levels of safety and precision.
- These molds can simulate real-life conditions, allowing for testing in terms of durability, functionality, and patient comfort.
Prototype molds are crucial in the development of implantable devices, helping to minimize the risks associated with device failure once implants are inserted into patients.
Disposable Medical Devices
Prototype medical equipment molds are commonly used for disposable medical devices such as syringes, catheters, and IV connectors, which must be produced in large quantities while maintaining high quality.
- Disposable devices require fast prototyping to ensure they meet both manufacturing efficiency and stringent safety standards.
- Prototype molds for these devices help test the assembly, ergonomics, and sterilization requirements before full-scale injection molding begins.
- Testing for fluid flow and biocompatibility ensures that these devices perform as expected during medical procedures.
By using prototype molds, manufacturers can ensure that these high-demand medical devices are safe, functional, and cost-effective for mass production.
Drug Delivery Systems
For drug delivery systems, including insulin pens, inhalers, and auto-injectors, prototype molds enable manufacturers to test and refine the components involved in delivering medications effectively.
- Drug delivery systems require precision engineering to ensure accurate dosing and ease of use by patients or healthcare providers.
- Prototype molds for these devices are critical in creating functional models of complex components like needles, reservoirs, and nozzles.
- Testing prototypes allows for validation of mechanical functionality and patient interaction, ensuring that each device delivers the medication safely and efficiently.
Prototype molds help optimize the design and manufacturing processes for drug delivery systems, ensuring both patient safety and product reliability.
Medical Packaging
Prototype molds are also essential for creating packaging for medical devices, ensuring both protection and ease of use.
- Packaging components, such as sterile packaging, blister packs, and trays, need to be molded to fit specific medical devices while maintaining sterility.
- Prototypes for packaging can test ease of opening, compatibility with sterilization methods, and integration with medical products.
- These molds ensure that the final packaging design maintains the safety and integrity of the medical device during transport and storage.
The ability to prototype packaging components ensures that medical devices reach the end-user in optimal condition, without compromising sterility or usability.
Prototype medical equipment molds are indispensable in the development of various types of medical device components. Whether used in creating surgical instruments, implantable devices, or disposable tools, prototype molds allow for functional testing, design refinement, and regulatory compliance before mass production. These molds are critical to ensuring the final product meets the high safety, quality, and performance standards required in the medical industry.
Different Types of Prototype Medical Equipment Molds
Prototype medical equipment molds play a crucial role in the development of medical devices, allowing manufacturers to test, refine, and validate their designs before mass production. These molds vary in material, manufacturing process, and intended use, depending on factors such as production volume, required precision, and regulatory requirements. By categorizing them based on their structure, material, and functionality, we can better understand how different mold types contribute to the medical device prototyping process. The following sections break down the key types of prototype medical equipment molds, each serving a distinct purpose in medical manufacturing.
Classification by Material
The material used in a prototype medical equipment mold significantly affects its durability, precision, and cost. Different materials cater to different stages of development, from early concept testing to pre-production validation.
- Aluminum Molds: These are widely used for low-volume prototype production due to their affordability and ease of modification. Aluminum molds cool quickly, reducing cycle times, but they have a shorter lifespan compared to steel molds.
- Steel Molds: Used for high-precision medical prototypes requiring extended use, steel molds provide excellent durability and fine detail replication. However, they are costly and time-consuming to manufacture.
- Silicone Molds: Typically used for soft tooling, silicone molds are flexible and ideal for creating medical prototypes requiring intricate details or bio-compatible properties, such as prosthetics and wearables.
- 3D-Printed Molds: With advancements in additive manufacturing, 3D-printed molds (made from resins, polymers, or metal composites) allow rapid iterations and cost savings for complex geometries.
Classification by Manufacturing Process
Prototype medical equipment molds are also categorized based on the method used to create them. Each process has unique advantages in terms of speed, cost, and part complexity.
- CNC-Machined Molds: These molds are milled from solid blocks of metal or plastic, offering high precision and strength. They are ideal for prototyping intricate medical components that require tight tolerances.
- Injection Molding Prototypes: For devices that will eventually be mass-produced using injection molding, prototype molds made from aluminum or soft steel allow manufacturers to test designs with near-final production conditions.
- Silicone Molding (Soft Tooling): This process is used for low-volume medical device prototypes where flexibility and cost efficiency are priorities. It is commonly used for producing small batches of medical-grade components for testing.
- Additive Manufacturing-Based Molds: In some cases, molds themselves are 3D printed, enabling rapid design iterations with reduced lead times and tooling costs.
Classification by Functionality
Prototype medical equipment molds serve different purposes depending on their role in the development process. Some are designed strictly for testing and validation, while others are closer to production-ready designs.
- Concept Validation Molds: These early-stage molds help manufacturers assess basic shape, size, and ergonomics. They are often made from low-cost materials like resin or soft plastic.
- Regulatory Testing Molds: Used to create prototypes that undergo biocompatibility and sterilization testing, these molds must meet strict medical-grade material requirements.
- Pre-Production Molds: Designed to simulate full-scale manufacturing conditions, these molds allow manufacturers to fine-tune the production process before mass production begins.
Classification by Application in Medical Equipment
Depending on the type of medical device being developed, different prototype molds are required to accommodate specific functional needs.
- Implantable Device Molds: Used for producing prototype components for orthopedic implants, dental implants, and other bio-compatible medical parts.
- Surgical Instrument Molds: Designed for prototyping precision tools such as scalpels, forceps, and endoscopic instruments.
- Diagnostic Equipment Molds: Used for creating casings and functional components for medical devices such as blood analyzers and imaging systems.
- Wearable Medical Device Molds: Specialized molds designed for producing prototypes of patient-monitoring wearables, such as smart patches or biosensors.
Prototype medical equipment molds come in many forms, each serving a unique role in the medical device development process. Whether classified by material, manufacturing process, functionality, or application, these molds help manufacturers create high-quality, regulatory-compliant medical devices with precision and efficiency. By selecting the right type of mold based on the intended use, medical companies can accelerate their product development cycles while ensuring safety and reliability in healthcare applications.
Medical Grade Plastics Used in Prototype Medical Equipment Molds
When creating prototype medical equipment molds, selecting the right plastic materials is essential to ensure the safety, durability, and regulatory compliance of the medical devices. Medical-grade plastics must meet strict standards for biocompatibility, sterility, strength, and chemical resistance. The choice of material influences the prototype’s performance during testing and evaluation, ultimately determining the device’s success in production. This section will explore some of the most commonly used medical grade plastics in prototype molding, highlighting their unique properties and applications.
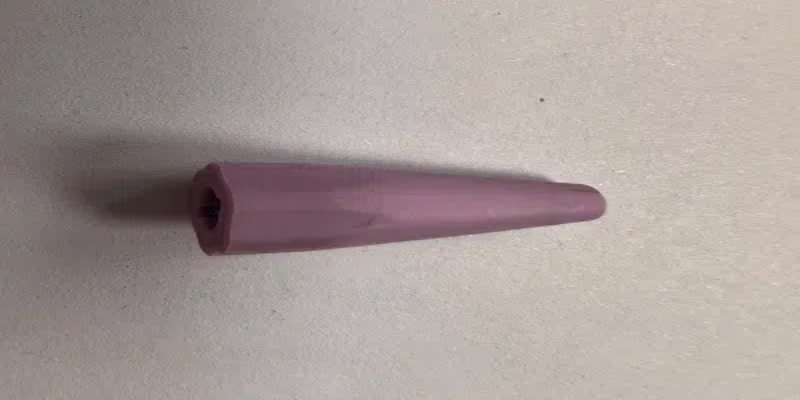
Polycarbonate (PC)
Polycarbonate is one of the most widely used plastics in the medical industry, particularly for prototype medical equipment molds due to its durability, transparency, and high impact resistance.
- Polycarbonate is known for its high tensile strength, which makes it suitable for parts that need to withstand mechanical stress, such as housings for diagnostic equipment or surgical tools.
- It is optically clear, making it ideal for applications where visibility is crucial, such as in medical device viewing windows.
- Polycarbonate is biocompatible, allowing it to come into contact with bodily fluids without causing adverse reactions, making it suitable for medical device components.
- It can be sterilized and is often used for medical equipment housings, blood filters, and infusion devices.
Its versatility and strength make polycarbonate an excellent choice for a variety of medical device prototypes.
Polypropylene (PP)
Polypropylene is another popular choice for prototype medical equipment molds, especially when cost-effectiveness, chemical resistance, and flexibility are key considerations.
- Polypropylene is resistant to a wide range of chemicals, including acids and bases, making it a great material for disposable medical devices like syringes, catheters, and diagnostic components.
- It is also highly flexible, offering resistance to fatigue, which makes it useful for products requiring bending or movement, such as tubing and valves.
- Polypropylene is biocompatible and can be sterilized by autoclaving, ensuring it meets the necessary safety standards for medical use.
- The material is often used for plastic medical containers, sterile packaging, and medical device components.
The combination of durability and chemical resistance makes polypropylene ideal for many types of medical device prototypes.
Polyethylene (PE)
Polyethylene is one of the most commonly used plastics for medical applications, particularly for components that require low friction, high strength, and flexibility.
- Polyethylene is typically used for medical tubing, catheters, and protective covers due to its smooth surface that reduces friction, which is essential for devices that interact with the human body.
- It is biocompatible, making it safe for medical use, and is resistant to moisture and chemicals, ensuring the longevity of devices exposed to fluids.
- Polyethylene’s low cost and ease of processing make it a popular choice for mass-produced medical products like disposable gloves, wound dressings, and surgical drapes.
Its combination of flexibility, chemical resistance, and low cost make polyethylene an ideal material for medical prototype molds that require performance under various conditions.
Polytetrafluoroethylene (PTFE)
Polytetrafluoroethylene, commonly known as PTFE, is a high-performance plastic used in prototype medical equipment molds for its exceptional non-stick properties and chemical resistance.
- PTFE is often used in the development of components that need to resist extreme conditions, such as chemical exposure and high temperatures, making it suitable for devices like surgical instruments, vascular grafts, and implantable devices.
- It is biocompatible and provides excellent resistance to bacteria, ensuring that it is safe for long-term use in the body.
- The material’s non-reactive nature makes it ideal for drug delivery systems or devices that require direct interaction with sensitive biological tissues.
Although more expensive than other materials, PTFE is critical in prototype medical molds that require advanced performance characteristics under harsh conditions.
Medical-Grade Silicone
Medical-grade silicone is a flexible and durable material frequently used for prototype medical equipment molds due to its unique properties that make it suitable for implants, gaskets, and soft-touch applications.
- Medical-grade silicone is biocompatible, hypoallergenic, and non-toxic, making it ideal for devices that come into direct contact with skin or internal tissues, such as wound dressings, catheters, and breathing tubes.
- Silicone is known for its high elasticity, allowing it to be used in parts that need to stretch or bend, such as seals or gaskets.
- It is resistant to extreme temperatures, making it suitable for products exposed to heat, such as in sterilization processes.
Medical-grade silicone’s softness, flexibility, and safety make it a key material in developing medical device prototypes for applications requiring high comfort and performance.
Acrylonitrile Butadiene Styrene (ABS)
Acrylonitrile Butadiene Styrene (ABS) is a versatile plastic that combines strength and impact resistance, making it suitable for medical prototypes that require both durability and ease of molding.
- ABS is often used for the housing of medical devices such as dialysis machines or patient monitoring equipment due to its sturdiness and impact resistance.
- It has good chemical resistance and can be easily molded into complex shapes, allowing for high-quality prototypes with intricate designs.
- ABS is also FDA-approved for certain medical applications and can be sterilized to meet regulatory standards.
ABS is often chosen for prototype molds in devices where durability and versatility are necessary.
Choosing the right medical-grade plastic for prototype medical equipment molds is critical for ensuring the functionality, safety, and performance of medical devices. Each of the materials discussed—polycarbonate, polypropylene, polyethylene, PTFE, silicone, and ABS—offers unique characteristics that make them suitable for different applications in medical device development. Understanding the specific requirements of the medical device and the material properties will guide manufacturers in selecting the ideal plastic for their prototype medical molds, helping them create effective and compliant medical devices.
Surface Treatment Processes Used in Prototype Medical Equipment Molds
Surface treatment processes play a critical role in prototype medical equipment molds, influencing the mold’s durability, precision, and compatibility with medical-grade materials. These treatments enhance mold performance by improving wear resistance, surface smoothness, corrosion resistance, and sterilization compatibility. Since medical devices often require high precision and strict hygiene standards, selecting the right surface treatment ensures that the molds can produce components that meet regulatory and functional requirements. The following sections categorize surface treatment processes based on their primary functions, including enhancing durability, improving surface finish, and ensuring biocompatibility.
Surface Treatments for Durability Enhancement
Durability is a key factor in prototype medical equipment molds, as they need to withstand repeated use while maintaining precision. Various coatings and hardening treatments improve the strength and lifespan of molds, making them more suitable for high-precision applications.
- Nitriding: A process that diffuses nitrogen into the mold’s surface, increasing its hardness and wear resistance. It is ideal for steel molds that require extended usage in medical prototyping.
- Hard Chrome Plating: Adds a thin, corrosion-resistant layer to the mold surface, reducing friction and extending the mold’s service life. This is particularly useful for molds used in producing disposable medical components.
- Titanium Nitride (TiN) Coating: A biocompatible coating that enhances hardness and oxidation resistance, making it ideal for molds used in surgical instruments and implantable device prototypes.
Surface Treatments for Improving Mold Finish
For medical equipment prototypes, surface smoothness directly affects the accuracy, functionality, and hygiene of molded components. Various finishing techniques ensure that the mold surfaces meet the high standards required for medical applications.
- Polishing & Mirror Finishing: Achieves an ultra-smooth surface, reducing the risk of material adhesion or bacterial growth in medical devices. This treatment is widely used for molds producing transparent medical components, such as syringes and optical lenses.
- Electropolishing: A chemical process that removes surface roughness at a microscopic level, improving corrosion resistance and sterilization compatibility. It is commonly used for stainless steel molds.
- Vapor Honing (Wet Blasting): Uses a fine abrasive mixed with water to smooth the surface without altering the mold’s precision. This technique is ideal for delicate medical prototypes that require soft yet clean finishes.
Surface Treatments for Biocompatibility & Hygiene Compliance
Since medical device components must meet strict biocompatibility and sterilization standards, molds require surface treatments that prevent contamination and ensure material safety.
- Teflon (PTFE) Coating: Provides a non-stick surface, reducing the risk of material residue buildup and making the mold easier to clean. It is particularly useful for molds producing bio-compatible polymers.
- Passivation: A chemical treatment that removes free iron from stainless steel molds, improving corrosion resistance and ensuring compatibility with sterilization processes. It is widely used for medical molds exposed to harsh disinfectants and steam sterilization.
- Plasma Surface Treatment: Modifies the mold’s surface properties to enhance adhesion and cleanliness, making it ideal for precision medical devices requiring high-purity material processing.
Surface Texturing for Functional Prototypes
Some medical equipment prototypes require specialized surface textures for better grip, aesthetic appeal, or functional integration.
- Laser Texturing: Uses a high-precision laser to engrave micro-patterns on the mold surface, improving grip and functionality for medical tools such as surgical handles and prosthetic components.
- Etching & Sandblasting: Creates controlled roughness on the mold surface, which is useful for medical prototypes requiring matte finishes or controlled friction.
- Chemical Texturing: Alters surface properties at a microscopic level, helping with fluid dynamics in diagnostic equipment molds.
The choice of surface treatment for prototype medical equipment molds depends on the required durability, precision, hygiene compliance, and functionality of the final medical device. Hardening processes like nitriding enhance durability, polishing techniques improve mold finish, and biocompatible coatings ensure safety and sterilization compatibility. Additionally, texturing methods enhance usability for certain medical applications. By selecting the right surface treatment, manufacturers can ensure that their prototype medical molds meet the high standards necessary for healthcare and medical technology innovation.
Medical Equipment Molding Technologies Used in Prototype Medical Equipment Molds
The development of prototype medical equipment molds involves various molding technologies that ensure precision, compliance, and optimal performance. These technologies are essential for creating high-quality, functional prototypes that meet regulatory standards before moving to full-scale production. Each molding technology offers unique advantages based on the complexity, material, and intended use of the medical device. This section explores the different molding technologies used in the production of prototype medical equipment molds, providing an understanding of their benefits and applications in the medical field.
Injection Molding
Injection molding is one of the most common and versatile molding technologies used for prototype medical equipment molds due to its high efficiency, precision, and ability to handle complex designs.
- Injection molding involves injecting molten material into a pre-designed mold under high pressure, where it cools and solidifies into the desired shape.
- This technology is ideal for creating highly detailed components such as housings, connectors, and functional parts like catheters, syringes, and diagnostic tools.
- It offers the advantage of fast production cycles, allowing for the creation of several prototypes quickly, which is crucial for design iteration and testing.
- Injection molding is compatible with a variety of medical-grade plastics, ensuring the produced components are both durable and compliant with medical standards.
The ability to handle intricate geometries and produce prototypes at a fast pace makes injection molding a go-to choice for many medical equipment prototypes.
3D Printing (Additive Manufacturing)
3D printing is gaining significant popularity in the creation of prototype medical equipment molds, as it offers unmatched flexibility, speed, and precision during the prototyping phase.
- 3D printing (or additive manufacturing) involves building up a prototype layer by layer based on a digital model. This method is particularly useful for creating prototypes with complex geometries or internal features that are difficult to mold using traditional methods.
- It allows for rapid iterations and modifications, making it ideal for early-stage prototyping where design changes are frequent.
- 3D printing supports a wide range of materials, including medical-grade resins and thermoplastics, suitable for biocompatibility testing.
- This technology is also advantageous when creating small-scale runs or low-volume prototypes, as it eliminates the need for expensive tooling and mold creation.
While it may not yet be suitable for mass production, 3D printing is invaluable in the prototype medical equipment mold phase, particularly for complex and detailed parts.
Compression Molding
Compression molding is a commonly used process in the development of prototype medical equipment molds, especially for creating parts made from rubber or silicone materials.
- In compression molding, a pre-measured amount of material is placed into a mold cavity, and pressure is applied to form the desired shape.
- This technology is particularly suited for producing rubber seals, gaskets, and soft-touch components used in implantable devices, catheters, and other medical equipment requiring flexibility.
- It is commonly used with medical-grade silicone, a material widely chosen for its biocompatibility, hypoallergenic properties, and ability to withstand sterilization processes.
- Compression molding offers a cost-effective solution for producing prototypes that require soft, flexible materials that are difficult to work with in other molding processes.
With its suitability for silicone and rubber materials, compression molding is crucial for prototype molds used in medical devices that demand flexibility and high durability.
Overmolding
Overmolding is a technology that is often employed in the production of prototype medical equipment molds, particularly for parts that require multiple materials with different properties, such as soft-touch components.
- Overmolding involves the process of molding one material over an already molded part, allowing for the creation of components with multiple layers of different materials.
- This technology is ideal for producing ergonomic handles, buttons, or multi-material parts found in surgical tools, diagnostic devices, and drug delivery systems.
- It allows manufacturers to combine the rigidity of a base material with the softness or tactile feel of a second material, resulting in more user-friendly, comfortable, and functional designs.
- Overmolding also provides an excellent way to create components that are biocompatible and resistant to sterilization processes.
For prototypes requiring multiple materials in one component, overmolding is an effective technology to enhance the performance and usability of medical devices.
Blow Molding
Blow molding is commonly used for creating hollow components in medical devices, such as containers or flexible parts that need to hold liquids or air.
- In blow molding, a heated plastic tube is inflated inside a mold to form a hollow part, such as medical bags, breathing tubes, or IV containers.
- This process is particularly useful for creating thin-walled, lightweight components with complex shapes, making it ideal for disposable medical products like drip bags or fluid reservoirs.
- Blow molding offers cost-efficient low-volume production and the ability to use medical-grade plastics that ensure the final product’s safety and reliability.
- This process can also support the integration of barrier layers to ensure the protection of fluids or medications inside medical devices.
Blow molding is a key technology for creating prototype medical equipment molds for medical devices that require hollow, flexible, and lightweight components.
Injection Compression Molding
Injection compression molding combines the benefits of both injection molding and compression molding, providing a versatile solution for certain complex medical device components.
- Injection compression molding involves injecting molten material into a mold and then compressing the material to form the part, which is ideal for parts that require both precision and high structural integrity.
- This process is often used for producing large, thin-walled parts, such as medical trays and dental devices that need to meet strict size and shape tolerances.
- It allows for the use of a variety of thermoplastics and biocompatible materials suitable for medical applications.
- It also helps reduce the internal stresses in parts, leading to improved part quality and consistency in prototypes.
Injection compression molding is an advanced technology used for prototype medical equipment molds that need high precision, strength, and reduced warping.
The molding technologies used in prototype medical equipment molds play an essential role in shaping the functionality, safety, and compliance of medical devices. Each molding technology—injection molding, 3D printing, compression molding, overmolding, blow molding, and injection compression molding—offers unique advantages depending on the material requirements, complexity, and intended function of the medical device. By choosing the appropriate molding method, manufacturers can create high-quality prototypes that support medical device development, ensuring the final product meets regulatory and performance standards.
FAQs about Prototype Medical Equipment Molds
A prototype mold is a specialized tool used to create initial samples or models of a product, especially in industries like medical device manufacturing. It is an essential part of the prototyping process, as it helps to test and validate the design, functionality, and overall feasibility of a product before mass production begins. These molds are typically made from materials such as aluminum or steel and are used to create prototypes of medical devices such as surgical tools, implants, or diagnostic equipment. The prototypes produced from these molds undergo various tests, including functional and safety evaluations, to identify potential flaws or improvements. This early stage testing is crucial in ensuring that the final product will meet regulatory requirements and perform as intended. Prototype molds also offer the advantage of cost efficiency, allowing manufacturers to test different designs and refine them before committing to full-scale production. In medical device manufacturing, these molds are vital for mitigating risks, ensuring product safety, and accelerating the time-to-market for new products.
Building a medical device prototype is a multi-step process that involves detailed planning and collaboration among engineers, designers, and medical professionals. The first step in the process is requirement analysis, where the device’s specifications, clinical needs, and regulatory requirements are clearly defined. This sets the foundation for the next step, which is conceptual design, where initial sketches and CAD models are created to visualize the device’s form and function. Once the design is established, material selection becomes crucial, as the materials must be biocompatible and durable to meet medical safety standards. The actual prototype creation follows, using methods such as 3D printing, CNC machining, or injection molding to bring the design to life. Once the prototype is created, it undergoes rigorous testing to evaluate its functionality, usability, and safety. The feedback gathered from this testing leads to iteration and design refinements, ensuring that the prototype meets all necessary requirements. Once the prototype is fully validated, it moves into regulatory approval processes before being considered for mass production. Each of these steps ensures that the final product will be both safe and effective for medical use.
In medical terms, a prototype is an early version or model of a medical device that is created for the purpose of testing and evaluating its design, functionality, and safety. Prototypes are essential in the development of medical devices because they allow manufacturers to identify and address any design issues early on, ensuring that the final product will be both effective and safe for use. These prototypes are created during the early stages of product development and are subjected to rigorous testing to evaluate how they perform in real-world conditions. This testing includes functional testing to assess how well the device works, usability testing to determine how easy it is to use, and safety testing to ensure that the device does not pose any harm to patients. A medical prototype may go through several iterations based on feedback from engineers, medical professionals, and regulatory bodies. Ultimately, the goal of the prototype is to refine the design before it moves into the mass production phase and undergoes regulatory approval.
Prototype equipment refers to the specialized tools, machines, or devices used to create early models of products during the prototyping phase of development. In manufacturing, prototype equipment is often used to test a product’s design, functionality, and performance before committing to large-scale production. For instance, in medical device development, prototype equipment can include specialized molds, 3D printing machines, CNC machines, or other tools used to create initial samples of medical devices like implants, surgical tools, or diagnostic devices. The prototype equipment used is intended to replicate the final product as closely as possible, allowing manufacturers to assess its performance, safety, and usability in real-world conditions. By using prototype equipment, manufacturers can test different materials, designs, and features to ensure that the final product meets regulatory standards and performs as expected. This early stage testing with prototype equipment helps identify any potential issues, enabling improvements to be made before production begins. Ultimately, prototype equipment plays a critical role in the development process by allowing manufacturers to refine designs, reduce production risks, and improve the overall quality of the final product.
A prototype mold is a temporary, lower-cost mold used for creating test parts before full production. These molds are typically made from aluminum or soft steel, allowing for quick adjustments and design validation in the early stages of medical device development. They help manufacturers refine a design before investing in a full-scale mold.
A production mold, on the other hand, is a durable, high-precision mold designed for mass manufacturing. Made from hardened steel, it can withstand high-volume production cycles while maintaining tight tolerances. These molds require a greater upfront investment but are essential for long-term, cost-effective manufacturing of medical devices.
For medical equipment, prototype molds help test performance, biocompatibility, and regulatory compliance before committing to a production mold, reducing risk and ensuring the final product meets stringent healthcare standards.
Medical device prototyping is the process of creating preliminary versions of medical equipment to test functionality, ergonomics, and compliance before full-scale production. This process often involves 3D printing, CNC machining, or injection molding to produce prototype parts that mimic the final product.
In medical injection molding, prototyping ensures that devices like surgical tools, diagnostic equipment, or implantable components meet strict FDA and ISO standards. Prototypes help in user testing, regulatory approvals, and identifying design flaws early in development.
Rapid prototyping techniques allow manufacturers to iterate designs quickly, minimizing time-to-market and reducing costly mistakes. Materials used in medical device prototyping must be biocompatible and sterilizable, ensuring safety for patients and healthcare professionals.
By leveraging prototype molds, manufacturers can create small batches of test components before transitioning to production molds for mass manufacturing, ensuring a seamless transition from concept to commercialization.
The market for medical injection molding is growing due to the increasing demand for high-quality, cost-effective medical devices. This sector includes disposable syringes, diagnostic components, surgical instruments, drug delivery systems, and implantable devices.
North America, Europe, and Asia-Pacific are key regions driving demand, with stringent regulatory requirements influencing material selection and production processes. The global medical injection molding market was valued at several billion dollars and is expected to grow due to aging populations, advancements in biocompatible materials, and the rise of minimally invasive surgical tools.
Medical-grade plastics like PEEK, polycarbonate, and silicone are widely used due to their durability, sterilizability, and chemical resistance. Additionally, automation and Industry 4.0 technologies are enhancing precision and efficiency in medical injection molding, making it a crucial manufacturing method for medical device companies worldwide.
Prototype casting is a manufacturing technique used to create prototype parts from various materials, including metal, plastic, and resin. It helps test a product’s form, fit, and function before mass production.
For medical devices, prototype casting is used to develop surgical instruments, prosthetic components, and diagnostic equipment. Common casting methods include:
Investment casting (for high-precision metal parts)
Sand casting (for low-cost, early-stage testing)
Silicone mold casting (for flexible, biocompatible prototypes)
Unlike injection molding, which requires expensive molds, prototype casting offers a faster and more affordable way to create medical equipment samples for evaluation. It allows for quick modifications, ensuring that the final design meets regulatory and functional requirements before committing to large-scale injection molding production.
Prototype examples in medical device manufacturing include:
Surgical Tool Prototypes – Early versions of scalpels, forceps, and laparoscopic instruments.
Prosthetic Limb Models – 3D-printed or casted designs tested for fit and movement.
Syringe and Catheter Prototypes – Disposable medical tools requiring FDA approval.
Implantable Devices – Early-stage heart valves, stents, and orthopedic implants.
Diagnostic Equipment Parts – Prototypes of housings for MRI, ultrasound, or blood analysis machines.
Prototyping allows for testing and design refinement, ensuring that the final product meets functional and safety standards before investing in full-scale injection molding.
A molded product is a component or item created by shaping material inside a mold, typically through injection molding, compression molding, or blow molding.
In medical device manufacturing, molded products include syringes, IV connectors, dental trays, and surgical instrument handles. These products must meet strict medical-grade requirements, such as biocompatibility, sterilizability, and durability.
Medical molding uses high-precision techniques to produce complex geometries with consistent quality. The process is ideal for manufacturing disposable medical devices and implantable components, ensuring repeatability in mass production.
Molded medical products offer advantages like cost-efficiency, lightweight properties, and design flexibility. By using prototype molds before full-scale production, manufacturers can refine their designs to meet industry regulations and performance requirements.
Injection molding can be highly profitable, especially in the medical sector, where precision and regulatory compliance drive demand for high-quality, repeatable components. The profitability depends on factors like mold cost, production volume, and material selection.
Once a production mold is developed, per-unit costs decrease significantly, making high-volume manufacturing highly cost-effective. Medical injection molding businesses benefit from long-term contracts with hospitals, pharmaceutical companies, and device manufacturers.
Profit margins are strong due to the high demand for sterile, disposable medical products. Automation further enhances profitability by reducing labor costs and improving efficiency. However, upfront mold and regulatory compliance costs can be significant, requiring careful investment planning.
Overall, companies specializing in medical injection molding can achieve substantial profits by optimizing processes, reducing material waste, and ensuring compliance with industry standards.
Injection mold costs vary widely depending on complexity, material, and production requirements. For prototype molds, prices range from $5,000 to $50,000, while production molds can cost $20,000 to $500,000 or more.
Medical device molds are more expensive due to the need for ultra-precise machining, specialized materials (such as stainless steel for high-sterility environments), and compliance with FDA and ISO standards.
Factors affecting mold cost include:
Number of cavities (multi-cavity molds cost more but improve efficiency)
Material choice (hardened steel molds last longer but are pricier)
Complexity (intricate designs require precision machining)
Although initial mold costs are high, the long-term savings per unit in mass production make injection molding cost-effective for medical devices. Using prototype molds first helps refine the design before investing in expensive production molds.
The hourly cost of running a plastic injection molding machine varies based on machine size, automation level, and energy consumption. Generally, costs range from $30 to $150 per hour.
For medical-grade injection molding, costs may be higher due to:
Specialized cleanroom requirements (Class 7 or 8 environments increase operational expenses)
High-precision equipment for medical device manufacturing
Material costs (biocompatible plastics like PEEK and medical-grade silicone are expensive)
Larger machines with higher clamping force (measured in tons) have higher hourly costs, but they can produce more parts per cycle, making production more efficient. Manufacturers optimize costs by automating processes, reducing cycle times, and minimizing material waste.
Injection molding is cheaper than CNC machining for high-volume production, but CNC is more cost-effective for low-volume prototyping and complex geometries.
For medical device manufacturing:
Injection molding is ideal for mass production of disposable devices, reducing per-unit costs significantly after the mold investment.
CNC machining is better for prototyping, custom implants, or small production runs, as it eliminates the need for expensive molds.
Medical injection molding becomes cost-effective when producing thousands to millions of parts, while CNC machining is best for high-precision, low-volume applications like orthopedic implants or surgical tool prototypes.
Using prototype molds before full production helps balance cost-effectiveness and precision, ensuring the best manufacturing method is chosen based on volume and complexity.
Yes, in the context of prototype medical equipment molds, a good mold ensures high-quality, precise, and reliable components, while a bad mold leads to defects, inconsistencies, and potential product failures.
A good prototype mold is designed with high precision, using durable materials like aluminum or soft steel to create test samples that accurately mimic production parts. It allows for design adjustments and functional testing before investing in a production mold.
A bad mold, on the other hand, may be poorly designed or manufactured, leading to defects such as warping, flashing, or incomplete part formation. In medical applications, bad molds can compromise sterility, safety, and regulatory compliance.
To ensure a good mold, manufacturers must work with experienced mold designers, use high-quality materials, and conduct rigorous mold testing. This guarantees that the final production mold will create medical components that meet stringent industry standards.
A prototype and a product are different stages in the development of a medical device.
A prototype is an early version of a product used for testing, validation, and regulatory approvals. It helps refine design, material selection, and functionality before mass production. Prototype medical molds create small batches of test components to evaluate performance and compliance with medical standards.
A product is the final, fully developed version that has passed all testing, certifications, and approvals. It is mass-produced using production molds and is ready for commercial use in hospitals, clinics, or patient care.
The key difference is that prototypes help identify and resolve design flaws, while the final product is the perfected version manufactured at scale. Medical prototypes are crucial for ensuring that the product meets safety, biocompatibility, and regulatory requirements before large-scale injection molding begins.
Yes, the type of mold plays a crucial role in medical device manufacturing, affecting cost, quality, and production efficiency.
Prototype molds – Used for early-stage product development, typically made from aluminum or soft steel for quick modifications and low-volume production.
Production molds – Made from hardened steel for high-volume manufacturing, designed to last millions of cycles with consistent quality.
Single-cavity vs. multi-cavity molds – Single-cavity molds produce one part per cycle (good for prototypes), while multi-cavity molds produce multiple parts at once (ideal for mass production).
Overmolding and insert molding – Used in medical devices to combine multiple materials or embed components like sensors into plastic housings.
Choosing the right mold is essential for balancing cost and performance. Prototype molds allow for testing and refinement before committing to expensive production molds, ensuring efficiency and compliance in medical manufacturing.
A prototype is an early-stage model used to test design, function, and manufacturability, while pre-production refers to the final stage before full-scale manufacturing.
Prototype Stage:
Used for initial concept testing and design validation.
Manufactured using prototype molds for small batches.
Allows for quick modifications before regulatory approval.
Pre-Production Stage:
Uses near-final versions of molds (soft production molds) to test scalability.
Focuses on refining manufacturing processes, tooling, and regulatory compliance.
Ensures the product is ready for mass production with minimal defects.
In medical injection molding, prototyping helps perfect a design, while pre-production ensures the manufacturing process is optimized before committing to high-volume production.
For prototype medical equipment molds, the best mold testing methods ensure precision, consistency, and compliance with industry regulations.
Dimensional Inspection – Uses CMM (Coordinate Measuring Machines) and laser scanning to check part accuracy.
Material Testing – Ensures biocompatibility and durability of medical-grade plastics like PEEK and polycarbonate.
Injection Mold Flow Analysis – Simulates plastic flow inside the mold to detect defects like warping, sink marks, or incomplete filling.
Functional Testing – Verifies that the molded prototype meets design and operational requirements.
Regulatory Compliance Testing – Ensures that the prototype meets FDA, ISO 13485, and USP Class VI medical standards.
A combination of these tests ensures that the prototype mold produces high-quality medical components before investing in full-scale production molds.
A manufacturing mold is a specialized tool used in injection molding, compression molding, or blow molding to create plastic or metal parts for medical devices.
For medical applications, these molds must be high-precision to produce sterile, biocompatible, and durable components. There are two main types:
Prototype Molds – Temporary, lower-cost molds for testing and early-stage development.
Production Molds – Durable, high-quality molds made from hardened steel, designed for mass manufacturing.
Medical manufacturing molds are used to produce syringes, surgical tools, implantable devices, and diagnostic components. High-end medical molds incorporate multi-cavity designs to optimize efficiency while maintaining strict tolerances and regulatory compliance.
Building a medical device prototype involves several key steps to ensure safety, functionality, and manufacturability.
Concept Design – Develop initial sketches, CAD models, and technical specifications.
Material Selection – Choose biocompatible plastics or metals suited for medical use.
Prototyping Method – Use 3D printing, CNC machining, or prototype injection molding to create test components.
Testing and Validation – Conduct functional, mechanical, and regulatory tests to ensure compliance.
Iterate and Improve – Refine design based on testing results before moving to pre-production.
Using prototype molds allows for cost-effective testing and adjustments before investing in high-volume production molds. This approach ensures that the medical device meets industry standards and is manufacturable at scale.
OEM (Original Equipment Manufacturer) medical devices are products made by one company and sold under another company’s brand. These devices include components or full medical systems that are manufactured under strict ISO 13485 and FDA regulations.
Examples of OEM medical devices include:
Surgical instruments – Scalpels, forceps, and endoscopic tools.
Implantable components – Hip implants, pacemaker parts, and stents.
Diagnostic equipment parts – Sensors, housings, and cartridge systems.
Drug delivery devices – Insulin pens, inhalers, and infusion pumps.
OEM manufacturers provide high-quality, customizable components to medical device companies, reducing production costs while ensuring compliance with healthcare industry standards. Many medical injection molding companies act as OEM suppliers, producing specialized parts for leading medical brands.
A prototype refers to an initial or early-stage model of a medical device mold, used for testing and refining design before large-scale production. It is created to identify flaws, optimize functionality, and ensure regulatory compliance in medical applications. Prototypes are often made using 3D printing, CNC machining, or soft molds to allow for easy modifications.
A category, on the other hand, refers to a classification of molds based on function, material, or application. For example, in medical equipment molds, common categories include:
Injection Molds: Used for mass production of medical device casings and components.
Compression Molds: Used for producing rubber-based medical parts.
Prototype Molds: Designed for rapid design validation before committing to production.
Essentially, a prototype is a specific, functional test unit, whereas a category defines the broader classification of different mold types used in medical manufacturing.
Differentiating between molds involves evaluating material, manufacturing process, and intended use.
Material Composition: Steel molds are heavy, durable, and used for large-scale production, while aluminum molds are lighter and more suited for prototyping. Silicone and epoxy molds are flexible and used for small-batch medical prototyping.
Surface Finish: Medical-grade steel molds are highly polished to meet strict hygiene standards, whereas prototyping molds may have a rougher finish.
Manufacturing Purpose: Soft molds (aluminum, silicone) are used for short-run prototypes, while hard molds (steel) are built for mass production in regulated environments.
Thermal Conductivity & Lifespan: Aluminum molds cool faster and wear out sooner, while steel molds provide longevity and consistent part quality over thousands of cycles.
In medical device prototyping, soft molds allow quick iteration, while hard molds ensure production consistency once designs are finalized.
For medical equipment prototyping, several mold materials are used depending on cost, durability, and flexibility:
Aluminum: Frequently used for soft tooling, it offers a balance between affordability and durability. It is ideal for producing a limited number of medical components before transitioning to steel molds.
Silicone: Used in soft molds for rapid prototyping and small-batch production, silicone is particularly useful when creating flexible or bio-compatible parts for medical applications.
3D-Printed Resin: Emerging technologies enable the use of 3D-printed molds made from specialized resins, reducing costs and increasing design flexibility.
Urethane and Epoxy-Based Composites: These materials allow for quick prototyping of plastic components, enabling medical manufacturers to test device functionality before investing in full-scale production.
Choosing the right mold material depends on budget, required part precision, and regulatory considerations in medical device manufacturing.
The two primary types of molds used in medical equipment prototyping and production are soft molds and hard molds:
Soft Molds: These are typically made from aluminum or silicone and are used for low-volume production or prototyping. They are cheaper to manufacture, have faster turnaround times, and allow for easy modifications, making them ideal for testing medical device designs before mass production.
Hard Molds: These are usually made from steel and are designed for high-volume manufacturing. They are more durable, withstand thousands of injection cycles, and ensure consistent part quality over time. Hard molds are used when a medical device moves from prototype to mass production, ensuring the final product meets stringent regulatory and material requirements.
For medical prototypes, soft molds are preferred to reduce costs, while hard molds are essential for long-term manufacturing.
Injection molding can be cost-effective for large-scale production, but it is expensive for prototyping medical equipment molds due to high initial tooling costs. A single steel mold can cost tens of thousands of dollars, making it impractical for rapid design iteration. However, for mass production of medical components like syringes, IV connectors, or casings for diagnostic devices, injection molding becomes one of the most affordable and efficient manufacturing processes, with low per-unit costs. Soft tooling options, such as aluminum molds, can reduce expenses for low-volume medical device prototypes, but they may not support the durability needed for extended runs. For small production batches or R&D, 3D printing and CNC machining are more economical choices. Companies developing new medical equipment typically use alternative methods before committing to injection molding to avoid costly design changes after mold fabrication.
Metal Injection Molding (MIM) has a strong future in the medical sector, particularly for manufacturing complex, small, and high-precision metal components such as surgical tools, orthopedic implants, and dental braces. The technology is evolving with advancements in biocompatible materials, automation, and hybrid manufacturing, making it a viable option for prototype medical equipment molds. Nano-MIM and additive manufacturing (AM) integration are pushing the boundaries of what can be achieved with MIM, enabling better material properties and design flexibility. The medical industry demands miniaturization, precision, and high-performance alloys, which MIM excels at producing. With advancements in feedstock formulations and post-processing techniques, the process is becoming more cost-effective and scalable. The future of MIM in medical applications will likely see increased use in customized implants and patient-specific medical devices, benefiting from digital design innovations and AI-driven manufacturing optimization.
For prototyping medical equipment molds, alternative methods like 3D printing, CNC machining, and silicone molding can be more advantageous than injection molding. These methods allow for faster iterations, lower upfront costs, and greater flexibility in design modifications. 3D printing is especially beneficial for rapid prototyping since it eliminates the need for expensive tooling. CNC machining offers superior precision and is ideal for metal or high-strength plastic components. Silicone molding, also known as soft tooling, is useful for small-batch production while maintaining detail accuracy. While injection molding is ideal for mass production due to its cost efficiency per unit, these alternatives enable faster development cycles for medical prototypes, allowing engineers to refine designs before committing to full-scale manufacturing. The best approach depends on factors like material requirements, production volume, and timeline constraints in medical device development.
Contact our professional team now for a same-day quote and risk-free project evaluation. Benefit from ISO 8 cleanrooms, advanced machines, and 12-hour fast response in medical injection molding.