Medical plastic molding refers to the process of using injection molding techniques to create precise and durable plastic components for medical devices. This manufacturing process is critical for producing items like surgical instruments, diagnostic tools, and implants. Precision and biocompatibility are paramount in medical devices to ensure safety and effectiveness for patients. Medical plastic parts exporter play a vital role in the medical device supply chain by sourcing high-quality materials, FDA-approved plastics, and collaborating with manufacturers to produce components that meet stringent regulatory standards. These traders ensure timely delivery and consistent quality, facilitating the development of safe, reliable medical products that adhere to industry-specific requirements, ultimately supporting patient care and medical advancements. FUJIU Medical Injection Mold, a trusted medical plastic molding trader, offers expert material selection, cleanroom manufacturing, and precision molding.
Low-Volume to High-Volume Production Capabilities
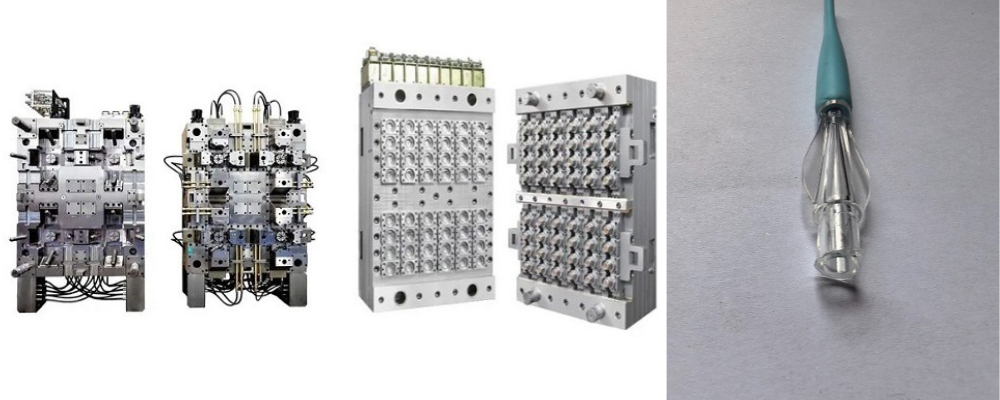
Attributes | Details |
---|---|
Place of Origin | Dongguan, Guangdong, China |
Brand Name | LY Medical Injection Mold |
Product Name | Medical Injection Mold |
Plastic Processing | Polypropylene, ABS, Polyvinyl Chloride, Polyethylene |
Process | Injection Molding |
Size | Customized Size |
Color | Customized Color |
Mold | Customizable |
Shape | Customized Shapes |
Certification | ISO9001 |
Tolerance | 0.02mm-0.05mm |
Mold Life | 500000 shots |
Service | OEM |
Workshop | ISO13485 cleanroom |
Sales Unit | Single Item |
Why Medical Plastic Molding Trader is Critical for Healthcare
Accuracy and Consistency in Medical Devices
Medical plastic molding plays an essential role in the healthcare industry, where accuracy and consistency are vital. Medical devices, like surgical tools, diagnostic instruments, and implants, require extremely precise manufacturing to ensure they function correctly and safely. A medical plastic molding trader ensures that all parts are molded to the exact specifications and meet the tight tolerances necessary for high-quality medical products, particularly when it comes to precision mold medical applications. Whether producing components with intricate designs or maintaining uniformity across high-volume production runs, the trader ensures the finished products meet rigorous standards for performance and reliability, guaranteeing that each part serves its critical function in the medical field.
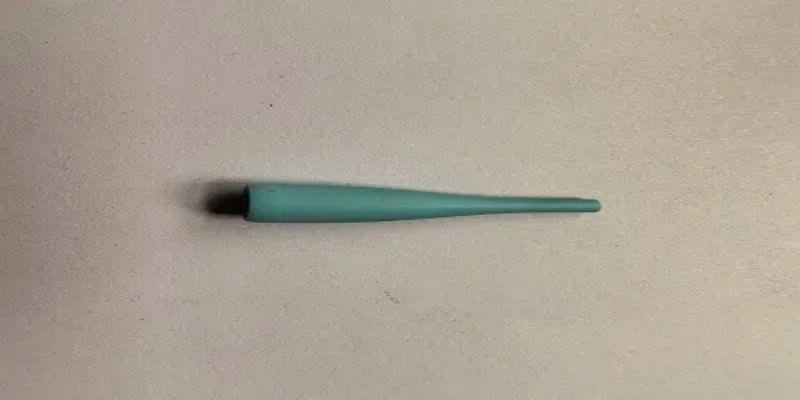
High Standards for Regulatory Compliance
Medical devices are subject to stringent regulations, including FDA approvals and ISO certifications, to guarantee their safety and efficacy. A medical plastic molding trader helps ensure that the medical components they supply comply with these regulatory requirements. By selecting FDA-approved materials and partnering with manufacturers that adhere to ISO certifications, traders ensure that the molded parts are both safe for use and legally compliant. This attention to regulatory detail is crucial to avoid potential product recalls or legal issues that could jeopardize patient health and the credibility of the manufacturer.
Ensuring Patient Safety Through Biocompatible Materials
Patient safety is a primary concern when manufacturing medical devices. The choice of materials used in molding directly impacts the safety and effectiveness of these products. A medical plastic molding trader plays a pivotal role by sourcing biocompatible materials that are non-toxic and safe for prolonged contact with the human body. These materials are critical for devices like implants, drug delivery systems, and surgical instruments, ensuring that they do not cause adverse reactions or harm to patients. By ensuring the use of the highest-quality, biocompatible plastics, traders help maintain the integrity of healthcare products and support better patient outcomes.
Key Roles of Medical Plastic Molding Trader & Supplier
Sourcing Medical-Grade Plastics and Resins
A medical plastic molding trader & supplier plays a crucial role in sourcing high-quality, medical-grade plastics and resins that meet the stringent requirements of the healthcare industry. These materials must comply with FDA regulations and be biocompatible to ensure patient safety. Traders collaborate with reliable suppliers to offer a wide variety of materials, including polypropylene, polycarbonate, and polyurethane, that are suitable for a range of medical applications. By carefully selecting the right materials, medical plastic molding traders ensure that every component produced is durable, safe, and capable of withstanding the demands of medical environments, such as sterilization or exposure to chemicals.
Providing a Network of Trusted Manufacturers
A medical plastic molding trader & supplier is also responsible for establishing and maintaining a network of trusted manufacturers. This network includes experienced molding facilities equipped with advanced technology and cleanroom environments that are essential for producing medical components. By working with these specialized manufacturers, traders ensure that each production run meets exacting standards for precision, consistency, and regulatory compliance. The trader’s ability to source trusted manufacturers enables smooth and reliable production workflows, ensuring timely delivery of medical devices and components.
Offering a Range of Services: Prototyping, Molding, Assembly, and Packaging
One of the key benefits of partnering with a medical plastic molding trader is the wide range of services they provide. Traders not only assist with prototyping and molding but also offer additional services such as assembly and packaging. Prototyping allows for early-stage testing of medical components to ensure functionality and design integrity before mass production begins. After molding, the trader & supplier may offer value-added services like part assembly, laser marking, or pad printing. In addition, packaging services ensure that medical components are securely packed and meet regulatory standards for distribution. This full-service approach streamlines the production process and reduces the need for multiple vendors.
Ensuring Timely Delivery and Cost-Efficiency
A medical plastic molding trader & supplier is instrumental in ensuring that medical device components are delivered on time and within budget. By managing the entire supply chain, from sourcing raw materials to overseeing production, traders streamline the manufacturing process. They collaborate with logistics providers to ensure timely delivery and minimize delays that could affect product launch schedules. Additionally, by optimizing production processes and sourcing materials efficiently, medical plastic molding traders can reduce costs for their clients, making it more cost-effective for medical device companies to produce high-quality components at scale. This efficiency allows healthcare manufacturers to meet market demands and maintain competitive pricing for their products.
Benefits of Partnering with a Medical Plastic Molding Trader
Expertise in Material Selection
One of the primary benefits of partnering with a medical plastic molding trader is their deep expertise in material selection. Medical devices require materials that are not only durable but also safe for patient use. A medical plastic molding trader understands the complexities of choosing FDA-approved and biocompatible plastics, ensuring that all materials used in production are suitable for medical applications. Common plastics used include Polypropylene, Polycarbonate, and Polyurethane, all of which offer various advantages, such as resistance to chemicals, heat, and sterilization methods. By leveraging their extensive knowledge, traders help manufacturers select the most appropriate materials for their specific device needs, enhancing both performance and safety.
Streamlined Supply Chain
A medical plastic molding trader plays an essential role in streamlining the supply chain for medical device components. With their broad network of trusted suppliers and manufacturers, traders help facilitate the efficient sourcing of raw materials and manage the production process from start to finish. They ensure timely delivery of components, reducing delays in the manufacturing and assembly stages. By optimizing logistics and managing inventory levels, medical plastic molding traders minimize the risk of supply chain disruptions, ensuring that plastic medical device manufacturers can meet production deadlines and maintain continuous product availability. This streamlined approach is particularly important in the fast-paced medical industry, where speed to market is critical.
Customization and Scalability
A medical plastic molding trader provides significant value in terms of customization and scalability, playing a crucial role in medical device plastic manufacturing. Medical device manufacturers often face the challenge of designing components that meet specific functional, aesthetic, or regulatory requirements. By collaborating closely with manufacturers, traders ensure that components are molded to precise specifications, aligning seamlessly with the demands of Medical Device Plastic Manufacturing. Whether addressing low-volume runs of prototype devices or managing high-volume production, traders offer the flexibility to scale operations efficiently. This adaptability ensures each medical device is tailored to the unique needs of healthcare providers, while the scalability supports efficient mass production as market demand grows.
Compliance with Industry Standards
Partnering with a medical plastic molding trader ensures that the products meet critical industry standards. Medical plastic molding traders are well-versed in the regulatory requirements for medical devices, including FDA and ISO standards. They ensure that all molded components undergo rigorous quality control processes and meet the necessary certifications for medical use. Compliance with these industry standards is crucial for avoiding costly recalls or legal challenges. By adhering to these regulations, medical plastic molding traders help ensure that medical devices are safe, reliable, and approved for use, ultimately improving patient outcomes and protecting manufacturers from legal or financial liabilities.
Key Features and Capabilities of a Medical Plastic Molding Trader
Injection Molding Services
One of the key features of a medical plastic molding trader is their ability to provide high-precision injection molding services, which is central to injection molding medical devices. This process is essential for producing intricate and complex medical device components that demand tight tolerances and consistency. By leveraging advanced injection molding technology, traders ensure that every part is manufactured to the exact specifications required for medical applications. Whether it involves creating surgical instruments, diagnostic tools, or prosthetics, the focus remains on meeting stringent standards for quality, performance, and safety. The integration of state-of-the-art equipment and technical expertise allows medical plastic molding traders to excel in injection molding medical devices, consistently delivering high-quality parts while maintaining cost-efficiency across both low and high-volume production runs.
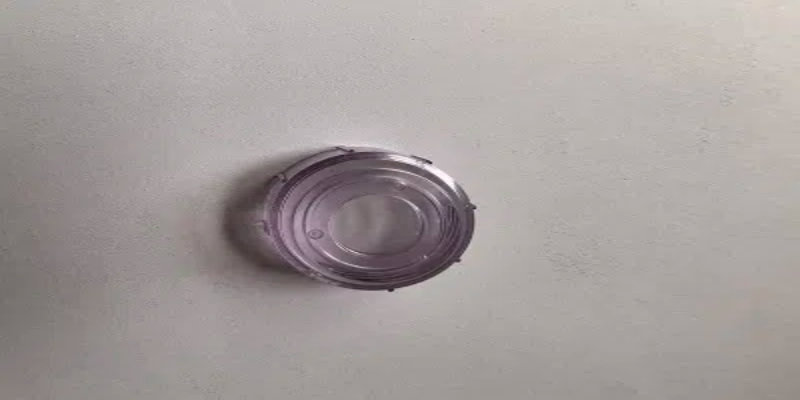
Cleanroom Manufacturing
For medical devices, maintaining a sterile environment during the manufacturing process is crucial to ensuring patient safety and compliance with regulatory standards. A medical plastic molding trader often provides cleanroom manufacturing services, where components are molded in ISO-certified cleanroom environments. These cleanrooms adhere to strict standards for air quality, particulate control, and contamination prevention, ensuring that no harmful particles or contaminants come into contact with the medical device components during production. Whether producing components for implants, drug delivery systems, or diagnostic devices, medical plastic molding traders use these controlled environments to prevent contamination and ensure that every part is safe and sterile for medical use.
Design for Manufacturability
A medical plastic molding trader also offers design for manufacturability (DFM) services, which is an essential part of the product development process and closely tied to medical device automation. By collaborating with medical device manufacturers during the early stages of design, the trader helps optimize designs for both cost-effectiveness and scalability, ensuring seamless integration with automated production systems. This involves considering the limitations of the molding process, material properties, and production capabilities, while also aligning with the requirements of medical device automation to streamline manufacturing efficiency. DFM not only reduces production costs and improves part performance but also supports the precise, automated processes essential in modern medical device manufacturing, minimizing the risk of design errors that could lead to delays or recalls. The trader ensures that designs are functional, manufacturable, and compatible with automated production, meeting the evolving needs of the medical industry.
Secondary Services
In addition to primary molding services, a medical plastic molding trader often provides a wide range of secondary services to add value to the final product. These secondary services include assembly, laser marking, pad printing, and other post-processing techniques that enhance the functionality and appearance of the medical device components. For example, laser marking can be used to add serial numbers, barcodes, or branding to components, while pad printing can apply intricate patterns or labels to surfaces. These services are essential for creating finished products that are ready for use in the medical field, and a medical plastic molding trader ensures that all secondary operations are performed to the highest quality standards. This comprehensive approach to manufacturing allows traders to meet the complex and varied needs of the medical industry while offering added convenience for their clients.
Medical Plastic Molding Trader:Applications of Medical Plastic Molding
Medical Devices
A medical plastic molding trader plays a critical role in the production of a wide variety of medical devices. These include high-precision components used in implants, prosthetics, and diagnostic tools. Medical plastic molding traders utilize advanced molding techniques to create durable, biocompatible plastic parts that meet stringent safety and performance standards. For example, implants like joint replacements and dental devices require precise molding to ensure they fit perfectly and function optimally within the human body. Prosthetics also demand the use of high-quality plastics to ensure comfort, strength, and flexibility, while diagnostic tools require components that can handle complex functions while remaining sterile and safe for medical use. Medical plastic molding traders are essential to ensuring that these devices are manufactured to the highest standards, ensuring both patient safety and effective medical outcomes.
Drug Delivery Systems, Surgical Instruments, and Patient Monitoring Devices
The medical plastic molding trader is also integral to the production of drug delivery systems, surgical instruments, and patient monitoring devices. These devices often require components that are not only durable but also highly accurate and safe. Drug delivery systems, such as inhalers and infusion pumps, require precisely molded parts that can withstand various pressures and temperatures while maintaining the integrity of the medication being delivered. Surgical instruments need components that are lightweight yet strong, often requiring advanced polymers that are biocompatible and resistant to wear and tear. Patient monitoring devices such as heart rate monitors, glucose meters, and thermometers rely on molded plastic components for their housings, buttons, and sensors, all of which need to be highly accurate to ensure patient safety. A medical plastic molding trader ensures that these components meet the functional and regulatory requirements of the medical industry.
Components for Orthopedic, Cardiovascular, Neurological, and Oncology Applications
In addition to general medical devices, medical plastic molding traders supply specialized components used across various medical fields. These include:
Orthopedic Applications
- Molded plastic components play a critical role in orthopedic devices, such as casts, splints, and braces.
- Precision and comfort are essential in orthopedic devices to ensure proper healing and support for patients.
- These components need to be durable, lightweight, and able to withstand the mechanical stresses common in orthopedic applications.
Cardiovascular Applications
- Stents, pacemakers, and catheters are some of the critical cardiovascular devices that rely on molded plastic parts.
- These components must be biocompatible to prevent adverse reactions within the body.
- The materials must also be reliable under high pressure, varying temperatures, and long-term use.
Neurological Applications
- In the neurological field, neural implants, electrode arrays, and diagnostic equipment depend on molded plastic components.
- The precision and biocompatibility of these materials are essential for sensitive applications in brain and nerve treatment.
- Molded plastic parts need to meet strict performance standards, ensuring they integrate well with neural tissue.
Oncology Applications
- Medical plastic molding traders supply essential components for radiation therapy devices, cancer diagnostic tools, and drug delivery systems used in chemotherapy.
- Components must meet stringent requirements for both safety and performance in cancer treatments.
- Molded plastics are tailored to provide optimal functionality while ensuring that these devices are safe for prolonged use in sensitive oncology treatments.
These specialized components for orthopedic, cardiovascular, neurological, and oncology applications all require high-performance, biocompatible materials. A medical plastic molding trader ensures that manufacturers receive the precise components they need to meet the complex demands of each specialized medical field.
Choosing the Best Medical Plastic Molding Trader
When selecting the best medical plastic molding trader, consider the following key factors:
Experience and Expertise
- A reputable medical plastic molding trader should have extensive experience in the medical device industry.
- They should have a proven track record of providing high-quality, FDA-compliant, and biocompatible materials.
Sourcing Medical-Grade Plastics
- The best medical plastic molding trader must have access to top-quality, medical-grade plastics such as Polypropylene, Polycarbonate, or Polyurethane.
- Ensuring that the materials are safe and functional for medical devices is critical.
Comprehensive Service Offerings
- Look for a medical plastic molding trader that offers a full range of services, including injection medical molding, cleanroom manufacturing, and post-processing options like laser marking and pad printing.
- These services help ensure that your products are manufactured to the highest standards.
Advanced Technology and Equipment
- The best medical plastic molding trader should use state-of-the-art equipment capable of handling complex, intricate designs.
- This ensures precision and reliability in every medical device component.
Quality Control and Compliance
- The trader should emphasize stringent quality control processes to meet ISO and FDA regulations.
- Compliance with industry standards is crucial for patient safety and device efficacy.
Timely Delivery and Cost-Efficiency
- A reliable medical plastic molding trader ensures that your components are delivered on time and within budget.
- Look for a partner who can handle both low- and high-volume production runs with efficiency.
Customer Service and Support
- A leading medical plastic molding trader will provide excellent customer service, offering ongoing support and expert advice throughout the project.
- Strong communication and responsiveness are key for the success of your medical device production.
By carefully evaluating these factors, you can partner with the best medical plastic molding trader, ensuring the production of high-quality, compliant, and reliable medical devices.
Medical Plastic Molding Trader: Key Techniques in Research and Production
Medical plastic molding traders play a crucial role in the research and production of plastic components used in the healthcare industry. Their work involves a variety of advanced molding techniques to ensure the safety, precision, and biocompatibility of medical devices and equipment. These traders utilize multiple plastic molding processes to meet industry standards, optimize production efficiency, and develop high-quality medical products. Below, we explore the key medical plastic molding techniques employed by these traders, categorized by their research and manufacturing applications.
Injection Molding: The Backbone of Medical Plastic Molding
Injection molding is one of the most widely used techniques in medical plastic molding due to its precision, scalability, and ability to produce complex parts with high consistency. This process involves melting plastic pellets and injecting the molten material into a mold cavity under high pressure.
- High Precision and Repeatability: Injection molding enables the production of intricate medical components, such as syringes, IV connectors, and surgical instrument handles, with extreme accuracy.
- Material Versatility: A wide range of biocompatible plastics, such as polycarbonate, polyethylene, and PEEK, can be used to meet specific medical requirements.
- Cleanroom Manufacturing: Many medical plastic molding traders conduct injection molding in cleanroom environments to ensure sterile production for applications in the medical and pharmaceutical industries.
Blow Molding: Producing Hollow Medical Components
For medical devices requiring hollow structures, such as fluid containers and IV bottles, blow molding is a preferred method. This technique involves inflating a heated plastic tube inside a mold to form the desired shape.
- Efficient Production of Thin-Walled Containers: Blow molding is ideal for producing lightweight yet durable medical bottles, inhalers, and specimen containers.
- Cost-Effective for Large Volumes: This process is well-suited for mass production, ensuring a lower cost per unit while maintaining consistent quality.
- Material Compatibility: Commonly used medical-grade plastics include PET, PP, and HDPE, which provide excellent chemical resistance and durability.
Thermoforming: Customization for Medical Trays and Packaging
Thermoforming is a process where a plastic sheet is heated to a pliable temperature, then shaped over a mold and trimmed to create the final product. Medical plastic molding traders use this technique for custom packaging solutions and disposable medical trays.
- Rapid Prototyping and Customization: Thermoforming allows for quick adjustments in design, making it ideal for custom medical packaging and prototypes.
- Sterile Packaging Solutions: This method is commonly used to manufacture blister packs, sterile barrier packaging, and surgical trays to ensure product safety.
- Material Efficiency: Thermoforming minimizes material waste while providing strong yet lightweight protective enclosures for medical devices.
Compression Molding: High-Strength Medical Components
Compression molding is used when producing high-strength and heat-resistant medical components. This process involves placing a plastic material in a heated mold, which is then compressed to take the desired shape.
- Durability for High-Performance Applications: Compression molding is commonly used for orthopedic implants, prosthetics, and surgical instrument components.
- Superior Mechanical Properties: The process ensures high strength, rigidity, and resistance to wear and tear, making it suitable for long-term medical applications.
- Ideal for Advanced Polymers: High-performance medical plastics like PEEK and UHMWPE (ultra-high-molecular-weight polyethylene) are frequently used in compression molding.
Micro Molding: Precision for Miniature Medical Devices
Micro molding is an advanced technique designed for the production of extremely small and intricate medical components, often required in minimally invasive medical devices and surgical instruments.
- Ultra-Precise Manufacturing: Micro molding enables the creation of tiny features with tolerances in the micron range, essential for catheters, stents, and microfluidic devices.
- High-Performance Medical Polymers: Materials such as bioresorbable plastics and liquid silicone rubber (LSR) are commonly used for micro molding applications.
- Integration with Automation: Many medical plastic molding traders incorporate automation in micro molding to enhance precision and efficiency.
Medical plastic molding traders employ a range of specialized techniques to research and produce high-quality medical plastic components. From the precision of injection molding to the durability of compression molding, each method serves a unique purpose in meeting the stringent requirements of the healthcare industry. As technology advances, these traders continue to refine their processes, integrating automation, cleanroom manufacturing, and innovative materials to enhance product safety, reliability, and efficiency.
Challenges Faced by Medical Plastic Molding Traders
Medical plastic molding traders play a critical role in connecting manufacturers with healthcare providers, hospitals, and medical device companies. However, they face numerous challenges that stem from regulatory compliance, material selection, technological advancements, and market competition. Successfully navigating these challenges requires deep industry knowledge, strong supplier networks, and continuous innovation. Below, we explore the key challenges faced by medical plastic molding traders in detail.
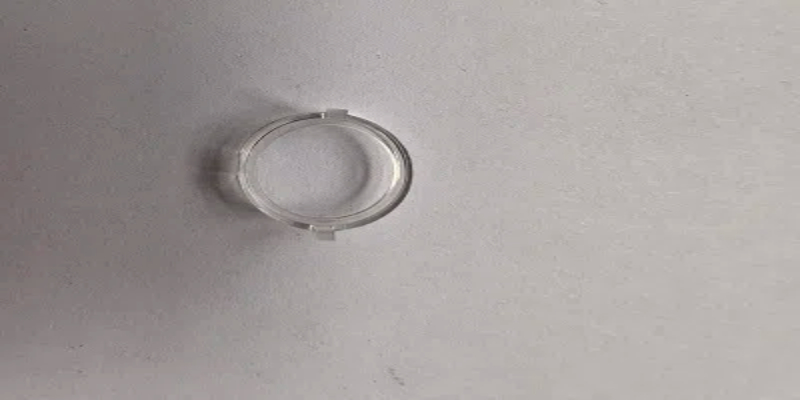
Stringent Regulatory Compliance
The medical industry is one of the most heavily regulated sectors, requiring traders to source and distribute only certified, high-quality medical plastic components.
FDA & ISO 13485 Compliance – Medical plastic products must meet FDA, ISO 13485, and USP Class VI standards to ensure biocompatibility, sterility, and safety. Traders must ensure their manufacturers adhere to these regulations, which adds complexity and costs.
Material Certification – Every medical plastic component must have proper documentation, material traceability, and validation. Traders must verify that medical-grade polymers (e.g., PEEK, polycarbonate, and TPEs) are approved for healthcare use.
Regional Regulations – Different regions have varying compliance standards (e.g., EU MDR in Europe, FDA in the U.S., NMPA in China), making it challenging for traders to handle global distribution.
High Cost of Medical-Grade Materials & Molding Processes
Unlike general plastic molding, medical plastic molding requires specialized materials that increase production costs and limit supplier options.
Expensive Biocompatible Plastics – Medical-grade plastics like PEEK, PSU, and PPSU cost 5–10 times more than standard plastics due to their sterilization resistance, chemical stability, and strength. Traders must balance cost-efficiency and quality when sourcing materials.
Strict Production Requirements – Medical injection molding often requires ISO Class 7 or 8 cleanroom facilities, increasing manufacturing costs. Traders must find suppliers who can meet these standards while maintaining competitive pricing.
Long Validation & Approval Processes – Medical plastic components require extensive testing and approval before market release, delaying time-to-market and increasing investment risks for traders.
Supply Chain Disruptions & Logistics Challenges
Efficient supply chain management is crucial for medical plastic molding traders, but disruptions can severely impact product availability and cost.
Raw Material Shortages – Global shortages of medical-grade plastics can delay production and increase prices, making it difficult for traders to fulfill orders on time.
Supply Chain Bottlenecks – Delays in shipping, customs clearance, and global distribution networks can affect product availability, especially when trading internationally.
Inventory Management – Medical plastic traders must balance stock levels to prevent shortages while avoiding overstocking of perishable or regulatory-sensitive materials.
Rising Competition & Market Saturation
The medical plastic molding industry is highly competitive, with numerous traders, manufacturers, and distributors vying for market share.
Price Pressure from Manufacturers – Large manufacturers often work directly with hospitals and medical device companies, bypassing traders. This forces traders to compete on pricing, value-added services, and supply chain reliability.
Emerging Players & Low-Cost Regions – Countries like China and India offer lower-cost medical molding solutions, making it difficult for traders in high-cost regions to compete.
Customization Demands – Many medical device companies now require custom plastic components, which may not be readily available. Traders must partner with manufacturers offering custom injection molding to stay competitive.
Rapid Technological Advancements
The medical plastic industry is constantly evolving, and traders must stay updated with the latest material innovations and production techniques.
New Biocompatible Polymers – Advanced plastics with antimicrobial properties, enhanced biocompatibility, and improved sterilization resistance are in demand. Traders must adapt to these new materials.
Micro-Injection Molding – The rise of microfluidic devices, microneedles, and miniature surgical tools requires precision molding techniques. Traders must find suppliers with the necessary micro-molding capabilities.
Hybrid Manufacturing Methods – 3D printing, CNC machining, and injection molding are being combined to produce complex medical parts. Traders must understand these hybrid techniques to meet client demands.
Sustainability & Environmental Regulations
Sustainability is becoming a major concern in medical plastic molding, creating new challenges for traders.
Eco-Friendly Medical Plastics – The demand for biodegradable and recyclable medical plastics is growing, but cost-effective, FDA-approved sustainable materials remain limited.
Regulatory Pressure on Single-Use Plastics – Many medical devices (e.g., syringes, IV components) rely on single-use plastics, but environmental regulations are pushing for more sustainable alternatives. Traders must stay ahead of these changes.
Recycling & Waste Management – The medical industry generates significant plastic waste. Traders must work with manufacturers that offer recyclable or reusable plastic solutions to comply with sustainability initiatives.
Medical plastic molding traders play a vital role in the healthcare industry, but they must navigate strict regulations, supply chain complexities, cost pressures, and technological advancements.
Key Data to Provide When Cooperating with a Medical Plastic Molding Trader for Business Customization
When engaging with a medical plastic molding trader for customized solutions, there are several essential data points that need to be shared to ensure a smooth and successful collaboration. These data points help the trader understand the specific requirements for your medical products and allow them to offer tailored solutions, from material selection to manufacturing processes. This comprehensive approach ensures that the customized products meet both regulatory standards and performance expectations. Below, we break down the key data you will need to provide in order to achieve a successful partnership with a medical plastic molding trader.
Product Design and Specifications
The product design and its associated specifications are fundamental pieces of information for any customization project. Providing the medical plastic molding trader with detailed blueprints or CAD (Computer-Aided Design) files helps clarify your vision and ensures that the trader can manufacture the product accurately and to your desired dimensions.
- Detailed Drawings or CAD Files: These are crucial for communicating the exact design, dimensions, and features of the medical device or component you wish to produce.
- Tolerance and Precision Requirements: Medical devices often require high precision. Clearly outlining tolerance levels and specific geometric features is essential to ensure the product meets performance and safety standards.
- Functional Requirements: Describe the intended function of the product, such as fluid handling, sterilization compatibility, or mechanical strength. This will help in selecting the best molding technique and material.
Material Selection and Performance Criteria
Choosing the right material is critical in the medical plastic molding process. Providing detailed information about the material requirements ensures that the final product is both functional and biocompatible. The material needs to meet various performance criteria, such as resistance to chemical corrosion, temperature stability, and compliance with regulatory standards.
- Material Specifications: Share the specific plastic materials you are interested in or ask for recommendations based on your product’s intended use. Common medical plastics include polycarbonate, polypropylene, polyethylene, and medical-grade silicone.
- Biocompatibility and Safety Standards: For medical devices that will have direct contact with patients, ensuring the material meets biocompatibility standards like ISO 10993 or USP Class VI is essential.
- Mechanical and Thermal Properties: Outline any particular mechanical properties such as tensile strength, impact resistance, or flexibility, and thermal stability requirements (e.g., resistance to high temperatures or sterilization processes).
Production Volume and Lead Time
Providing information about the expected production volume and timelines helps the medical plastic molding trader optimize the manufacturing process, select appropriate molding techniques, and determine the scalability of the project.
- Expected Volume: Specify whether the product will be produced in small batches, medium quantities, or large-scale mass production. This will influence the molding technique and equipment used (e.g., injection molding for large volumes or thermoforming for smaller batches).
- Lead Time Expectations: Clearly state the desired timelines for the project, including prototyping, tooling, and final production. This will help the trader set realistic expectations and ensure timely delivery.
- Order Flexibility: Indicate if there is a need for flexibility in terms of production schedules and order quantities, especially in cases of unexpected demand changes.
Regulatory and Compliance Requirements
Medical products are heavily regulated to ensure patient safety, and it is crucial to provide the trader with the relevant standards and certifications your products need to comply with. Sharing this information upfront will guide the design, material selection, and manufacturing processes to ensure compliance with local and international medical regulations.
- Regulatory Standards: Inform the medical plastic molding trader about any necessary certifications, such as FDA 21 CFR Part 820 (Quality System Regulations), ISO 13485 (Medical Devices), or European Union MDR (Medical Device Regulation).
- Sterilization and Packaging Standards: Provide details on sterilization methods (e.g., gamma radiation, ethylene oxide, autoclaving) and packaging requirements that meet regulatory guidelines.
- Product Labeling and Traceability: Outline the labeling requirements, including product identification, traceability information, and any other necessary regulatory markings for compliance.
Prototyping and Testing Needs
Prototyping and product testing are vital steps in the product development lifecycle. By providing clear expectations about your prototyping and testing needs, you help the medical plastic molding trader ensure that the product performs optimally before mass production.
- Prototype Requirements: Indicate if you require prototypes for design validation, user feedback, or testing purposes. This helps the trader understand the level of detail and accuracy needed in the prototype phase.
- Performance and Quality Testing: Specify any testing protocols, such as mechanical stress tests, biocompatibility assessments, or environmental durability tests, that the prototypes need to undergo before full-scale production.
- Approval Process: Establish a clear process for reviewing and approving prototypes and samples, outlining how feedback will be integrated into the final design and production process.
Packaging and Shipping Specifications
Once your product is molded, packaging and shipping play a critical role in ensuring its safety and integrity during transportation. Provide clear packaging and shipping requirements to ensure that the final product reaches its destination in optimal condition.
- Packaging Requirements: Indicate if the products need specific packaging for sterility, such as sterile barrier systems or blister packs. Consider any protective packaging needs to prevent damage during shipping.
- Shipping Considerations: Share any necessary shipping or logistics requirements, such as temperature control, expedited delivery, or specific distribution channels.
- Labeling and Documentation: Ensure that the trader understands any special labeling or documentation required for shipping, especially for medical products that may need to comply with international export regulations.
When working with a medical plastic molding trader for business customization, the data provided will form the foundation for a successful collaboration. From detailed product designs to regulatory compliance requirements, each piece of information ensures that the customized medical products meet the necessary safety standards and functional requirements. By clearly communicating your expectations on material selection, production volume, prototyping, and packaging, you help the trader produce high-quality products tailored to your specifications.
Medical Injection Molding Surface Treatment Services Provided by Medical Plastic Molding Traders
As medical plastic molding traders, the quality of the surface finish of medical components is crucial. Surface treatment plays a vital role in ensuring the biocompatibility, sterilization effectiveness, and aesthetic quality of plastic medical devices. Traders in the medical plastic molding industry offer a variety of surface treatment services that cater to the stringent standards of the medical sector. These treatments not only enhance the functional properties of medical plastics but also ensure that the final product meets regulatory compliance and performance expectations. Below, we explore the most common surface treatment services offered by medical plastic molding traders from different angles.
Polishing for Aesthetic and Functional Quality
Polishing is an essential surface treatment for medical plastic components, particularly when the final product needs to meet specific aesthetic or tactile standards. The process involves improving the smoothness and glossiness of the plastic surface.
Mechanical Polishing – Often used for larger components, mechanical polishing uses abrasive pads or brushes to refine the surface, eliminating imperfections and providing a shiny, smooth finish. It’s commonly used for surgical instruments, casings, and diagnostic devices that require a clean and sleek appearance.
Electrostatic Polishing – In some cases, electrostatic polishing is employed to remove microscopic imperfections and create an ultra-smooth surface, improving the biocompatibility and sterilization properties of the product. This process ensures that parts are suitable for use in sensitive medical environments.
This treatment is particularly important when cosmetic appearance is vital for medical devices, such as patient-facing components or visible parts of devices like monitors or injectors.
Plasma Treatment for Enhanced Surface Energy
Plasma treatment is an advanced surface treatment that involves exposing medical plastics to ionized gas (plasma) to increase surface energy and improve adhesion properties. This service is particularly beneficial for medical devices that require coatings, bonding, or printing.
Plasma Etching – Plasma etching is used to roughen the surface of plastics without affecting the material integrity. It makes surfaces more adhesive, improving the bonding of coatings, paints, or adhesives. This is crucial for implantable devices, drug delivery systems, and surgical tools that require sterile coatings or ink marking for identification.
Plasma Activation – This process activates the surface to improve compatibility with biocompatible materials, such as hydrophilic coatings. It’s often used for catheters, pacemakers, and IV sets, which require surfaces that interact well with bodily fluids and tissues.
The increased surface energy is essential for ensuring long-term performance and reliable functionality in the demanding medical field.
Coating and Layering Services for Functional Enhancement
Medical plastic molding traders offer several coating services to improve the functionality and protection of plastic parts used in medical devices. Coatings can provide antimicrobial properties, improve wear resistance, or enhance biocompatibility.
Antimicrobial Coatings – Antimicrobial surface coatings are widely used in medical plastic molding to prevent infection and enhance safety. Silver-ion coatings, for example, can be applied to devices like surgical tools, stents, and wound dressings, reducing microbial growth.
Hydrophobic or Hydrophilic Coatings – Hydrophilic coatings improve the lubricity of devices like catheters and needles, ensuring smooth insertion into the body. In contrast, hydrophobic coatings are often used for devices that require water resistance.
Protective Coatings – Durable coatings like UV-cured coatings can be applied to plastic casings for medical equipment that are regularly exposed to harsh environments, helping to protect devices from abrasion, moisture, and UV degradation.
This ensures that devices are long-lasting, safe, and able to perform optimally over extended use periods.
Laser Marking and Etching for Permanent Identification
In the medical industry, permanent identification of devices is required for tracking, traceability, and regulatory compliance. Laser marking and etching are services offered by medical plastic molding traders to etch precise information onto plastic parts without compromising their integrity.
Laser Marking – This technique uses laser beams to create high-contrast marks on the surface of medical plastic components, such as barcodes, serial numbers, or product details. This ensures that critical information remains legible for the lifetime of the product, even after sterilization processes.
Laser Etching – Laser etching allows for deeper engraving of medical parts, making it ideal for devices such as implants or surgical tools, where visible markings are necessary for identification but must remain sterile and intact over time.
Laser marking and etching ensure that devices can be traced and identified throughout their life cycle, which is essential for patient safety, regulatory reporting, and recall management.
Sterilization and Surface Treatment for Biocompatibility
Surface treatments for sterilization are vital for ensuring that medical plastic components can be safely used in sterile environments, preventing contamination and infections. Traders provide sterilization services that make medical devices suitable for implantation or use in healthcare settings.
Autoclaving Resistance – For devices that need to withstand high-temperature sterilization methods, such as autoclaving, special surface treatments are applied to ensure that the medical plastic retains its strength, shape, and biocompatibility after each sterilization cycle.
Gamma Radiation Resistance – For gamma radiation sterilization, surface treatments that enhance the resilience of plastic parts are often necessary. Devices such as single-use syringes, infusion pumps, and catheters are frequently subjected to this process, ensuring they remain safe for medical use.
These treatments ensure that medical plastics can endure repeated sterilization cycles while maintaining their biocompatibility, which is crucial for implantable devices and single-use medical components.
The surface treatment services offered by medical plastic molding traders are essential for ensuring the functional performance, safety, and aesthetic quality of medical devices. Whether it’s polishing for aesthetic appeal, plasma activation for improved bonding, or sterilization for biocompatibility, these treatments are crucial for meeting the rigorous demands of the medical industry. By offering these advanced services, traders ensure that medical plastic components are ready for safe use in healthcare environments and compliance with international standards, contributing to the overall success and longevity of medical devices.
FAQs about Medical Plastic Molding Trader
The market for medical plastic injection molding is growing rapidly due to the increasing demand for high-quality, precision-molded medical components. Medical plastic molding traders serve industries like diagnostics, drug delivery, surgical instruments, and implantable devices. The rise of minimally invasive procedures, personalized medicine, and disposable medical products further drives demand. Regulatory compliance and the need for biocompatible materials shape this industry. Advanced technologies such as micro-molding and cleanroom manufacturing enhance product quality and safety. With the global healthcare sector expanding, medical plastic molding remains essential for producing cost-effective, reliable medical components at scale.
Injection mold costs vary based on complexity, size, and material. For medical plastic molding traders, precision and regulatory compliance increase mold costs. Simple molds start at $5,000, while complex multi-cavity medical molds range from $50,000 to $250,000. Factors like high-precision tolerances, specialized medical-grade materials, and cleanroom production drive up costs. However, for high-volume medical device manufacturing, injection molding remains cost-efficient due to lower per-unit costs over time. Advanced automation and durable mold materials help traders achieve long-term profitability despite high initial investments.
The hourly cost of running a plastic injection molding machine varies based on machine size, energy consumption, and operational efficiency. For medical plastic molding, costs can range from $30 to $150 per hour, depending on precision requirements, material selection, and regulatory compliance. Medical-grade plastic molding requires cleanroom environments, specialized equipment, and FDA-compliant materials, which further increase operational costs.
Factors such as machine tonnage (e.g., 50-ton vs. 500-ton machines), maintenance, and labor expenses also impact hourly rates. Advanced servo-electric machines are more energy-efficient but require higher initial investments. Additionally, regulatory compliance in medical molding adds validation and testing expenses to ensure biocompatibility and sterility, increasing overall costs.
To optimize costs, medical plastic molding traders often outsource production to specialized facilities or invest in automation to reduce labor expenses. Proper process monitoring and waste reduction can further enhance cost efficiency.
Plastic injection molding for medical applications is particularly challenging due to strict quality, safety, and regulatory standards. Unlike standard industrial molding, medical plastic molding requires:
Precision & Consistency – Medical components, such as syringes and implants, must meet micron-level accuracy to ensure patient safety.
Material Compliance – Medical plastics, including PEEK, polycarbonate, and medical-grade polypropylene, must be biocompatible and sterilizable.
Regulatory Approvals – Compliance with FDA, ISO 13485, and USP Class VI standards is essential, adding complexity to material selection and validation.
Controlled Manufacturing – Many medical parts require cleanroom injection molding (ISO Class 7 or 8) to prevent contamination.
Medical molding also involves scientific molding techniques, where process parameters (e.g., pressure, temperature, cooling rates) are optimized to ensure repeatability. This level of control makes medical injection molding more complex than standard plastic manufacturing.
Starting a medical plastic molding business requires technical expertise, regulatory knowledge, and capital investment. Key steps include:
Market Research & Niche Selection – Focus on high-demand products like surgical instruments, diagnostic equipment, or drug delivery devices.
Regulatory Compliance – Obtain necessary certifications (ISO 13485, FDA approval) and set up GMP-compliant manufacturing.
Facility & Equipment – Invest in cleanroom molding machines, precision tooling, and quality control systems.
Material Sourcing – Establish relationships with suppliers of biocompatible resins (PEEK, polycarbonate, TPEs).
Process Development & Prototyping – Validate molding processes using scientific molding principles before full-scale production.
Customer Acquisition – Target medical device OEMs, hospitals, and pharmaceutical companies for business contracts.
A successful medical molding business requires a high level of quality assurance, traceability, and continuous innovation to remain competitive.
While injection molding is efficient for medical plastics, there are challenges and downsides:
High Initial Costs – Tooling costs for medical-grade molds can range from $20,000 to $500,000, making it expensive for small-scale production.
Regulatory Barriers – Compliance with FDA, ISO 13485, and USP Class VI regulations increases production complexity and costs.
Material Constraints – Not all plastics are suitable for sterilization, biocompatibility, or long-term body contact, limiting material choices.
Environmental Concerns – Medical plastic waste, especially single-use disposables, raises sustainability issues.
Long Lead Times – Mold fabrication can take weeks to months, delaying product launches in a fast-moving healthcare market.
Despite these challenges, automation, advanced material selection, and sustainable molding practices are improving efficiency and reducing waste.
For mass production, injection molding is significantly cheaper than 3D printing, but for prototyping or low-volume runs, 3D printing can be more cost-effective.
Injection Molding: Best for large production runs (10,000+ units); costs are lower per unit but require expensive molds.
3D Printing: Ideal for prototyping and custom parts; no tooling costs but higher material expenses and slower production speeds.
For medical devices, injection molding is preferred due to:
Biocompatible materials availability (PEEK, PC, TPE)
Sterile, repeatable production in controlled environments
Regulatory compliance for FDA-approved parts
However, 3D printing is useful for rapid prototyping, surgical guides, and patient-specific implants before mass production.
One of the hardest plastics used in medical injection molding is PEEK (Polyether Ether Ketone) due to its:
High strength & durability – Comparable to metals, often used in implants, spinal cages, and orthopedic devices.
Heat & Chemical Resistance – Withstands autoclaving, radiation sterilization, and harsh chemicals.
Biocompatibility – FDA-approved for long-term implantable medical devices.
Other tough medical plastics include polycarbonate (PC), PPSU, and ULTEM (PEI), which are used for surgical tools and medical housings. However, their molding process requires high temperatures, specialized molds, and precision processing to avoid defects.
For medical plastic molding, key rules of thumb include:
Wall Thickness Uniformity – Maintain 0.5mm–3mm for consistent cooling and strength.
Draft Angles – Use 1-3° draft per side to ease part ejection.
Gate Placement – Position away from critical medical features to avoid defects.
Material Selection – Choose biocompatible, sterilizable plastics (e.g., PEEK, PC, TPE).
Process Validation – Follow IQ/OQ/PQ (Installation, Operational, Performance Qualification) to meet FDA standards.
Following these guidelines ensures high precision, minimal defects, and regulatory compliance in medical injection molding.
The hourly rate for medical injection molding depends on:
Machine size: Small (50-ton) vs. Large (500-ton+)
Cleanroom requirements: ISO 7 or 8 increases cost
Material type: PEEK and high-performance plastics raise expenses
Rates typically range from $50 to $200 per hour, with medical molding costing 20-50% more due to strict quality standards. Additional expenses include mold maintenance, regulatory validation, and specialized labor.
Injection molding cycle time for medical plastics varies based on part complexity and material:
Simple parts: 15–30 seconds
Complex medical components: 1–3 minutes
High-precision implants: 5–10 minutes
Including setup, validation, and quality checks, full production can take days to weeks, especially for FDA-regulated devices requiring extensive testing.
The future of medical injection molding is driven by automation, sustainability, and advanced materials. Smart manufacturing, including AI-driven quality control and IoT-enabled monitoring, will improve precision and efficiency.
Biodegradable and recyclable medical plastics, such as PLA-based biopolymers, are gaining traction to reduce plastic waste in healthcare. Additionally, micro-injection molding is expanding, enabling the production of ultra-small medical components like microneedles and drug delivery systems.
3D printing and hybrid molding are also transforming the field by allowing customized implants, rapid prototyping, and shorter development cycles. As regulatory requirements tighten, ISO 13485 and FDA-compliant automated systems will become standard to ensure zero-defect production.
The market is expected to grow as minimally invasive surgeries, wearables, and single-use medical devices become more widespread, making injection molding an essential part of modern healthcare manufacturing.
The global medical injection molding market is projected to exceed $30 billion by 2030, with a CAGR of 6-8%. The growth is driven by rising demand for single-use medical devices, drug delivery systems, and diagnostic equipment.
Key market segments include:
Syringes & IV components (high demand due to infection control protocols)
Surgical instruments (lightweight, durable plastics replacing metals)
Implants & prosthetics (biocompatible and sterilizable materials like PEEK)
Labware & diagnostic devices (rapid COVID-19 testing kits accelerated demand)
North America leads the market, followed by Europe and Asia-Pacific, where low-cost manufacturing hubs like China and India are expanding rapidly. Companies focusing on ISO 13485 certification, cleanroom production, and high-performance polymers will dominate this lucrative sector.
Injection molding for medical plastics is expensive due to high tooling costs, regulatory compliance, and cleanroom requirements.
Tooling & Mold Costs – Medical-grade molds cost between $20,000 to $500,000, requiring precision CNC machining and validation.
Regulatory Compliance – FDA, ISO 13485, and USP Class VI approvals demand extensive testing and documentation, increasing costs.
Cleanroom Manufacturing – Many medical parts require ISO Class 7 or 8 cleanrooms, adding to facility and operational expenses.
Material Selection – High-performance, biocompatible plastics (e.g., PEEK, PPSU, medical-grade TPEs) are expensive.
Process Control & Validation – Scientific molding techniques, in-line inspections, and strict quality control extend production cycles.
Despite high costs, injection molding remains the preferred choice for scalability, precision, and sterility in medical device manufacturing.
Yes, injection molding is cheaper than CNC machining for high-volume production, but CNC is more cost-effective for prototyping and low-volume runs.
Injection Molding – Best for 10,000+ parts; lower per-unit costs but high upfront mold investment.
CNC Machining – Ideal for prototyping and low-volume precision parts, but material waste and longer machining times increase costs.
For medical components, CNC machining is often used for custom implants, surgical tools, and prototype testing, while injection molding is preferred for mass production of syringes, tubing, and casings.
Advanced hybrid manufacturing—combining CNC-machined molds with injection molding—is an emerging trend, offering cost-effective precision for high-performance medical devices.
Medical injection molding is highly profitable, with gross margins ranging from 30% to 60%, depending on market niche, production volume, and regulatory approvals.
High-Volume Efficiency – Once molds are created, per-unit costs drop significantly, making long production runs very profitable.
Premium Pricing – Medical plastics, like PEEK and PC, command higher prices due to biocompatibility and sterilization capabilities.
Specialized Markets – Serving medical OEMs, hospitals, and pharmaceutical companies creates long-term contracts with repeat orders.
Automation & Cost Reduction – Robotics and AI-driven quality control improve efficiency and lower labor costs.
Despite high initial investment (cleanroom setup, tooling, compliance costs), businesses with ISO 13485 certification and FDA-approved processes enjoy steady revenue streams in the booming medical sector.
For medical applications, the best alternative depends on production needs, material requirements, and cost constraints:
3D Printing (Additive Manufacturing) – Ideal for custom implants, prototypes, and complex geometries; lacks mass-production efficiency.
CNC Machining – Preferred for high-precision surgical instruments and titanium implants, but costly for high-volume runs.
Micro-Molding – Best for ultra-small medical components (e.g., catheters, microneedles) with extreme precision.
Blow Molding – Used for hollow medical containers like IV bags and bottles, but unsuitable for solid parts.
While injection molding remains the dominant choice for mass-producing medical plastics, hybrid approaches (3D printing for prototyping, CNC for tooling, and molding for mass production) provide the best efficiency and cost savings.
The cost of an injection mold for medical plastic components varies based on complexity, size, and material requirements. On average:
Simple medical molds (e.g., disposable syringes, tubing connectors) cost $20,000–$50,000.
Complex, multi-cavity molds (e.g., implant casings, drug delivery systems) range from $50,000–$250,000.
Micro-injection molds (used for microneedles, surgical components) can exceed $500,000 due to high precision requirements.
Medical-grade molds require high-precision CNC machining, stainless steel tooling, and ISO 13485/FDA compliance, increasing costs. Multi-cavity molds reduce per-unit costs by enabling high-volume production.
Despite the high upfront cost, injection molds for medical devices last for hundreds of thousands to millions of cycles, making them cost-effective over time.
The cost of medical plastic injection molding is calculated using:
Mold Cost – Initial investment for tooling ($20,000–$500,000).
Material Cost – Medical-grade plastics (e.g., PEEK, polycarbonate) cost $5–$50 per kg, depending on biocompatibility and sterilization requirements.
Machine Time – Hourly machine rates range from $50–$200 per hour, influenced by cleanroom requirements and automation.
Cycle Time – Shorter cycles (10–60 seconds) reduce costs per unit.
Labor & Compliance – FDA/ISO 13485 validation, cleanroom operation, and quality control add costs.
Formula:
Total Cost=(Mold CostTotal Units)+(Material Cost per Unit)+(Machine Hourly Rate×Cycle Time)
Automation, multi-cavity molds, and high-volume production lower per-unit costs significantly.
For medical plastic molding, the recommended draft angle depends on the part’s geometry, material, and surface finish:
General Rule: 1°–3° per side for easy part ejection.
Highly Textured Surfaces: 3°–5° to prevent sticking.
Medical-Grade Plastics: Some materials (e.g., PEEK, PC) may require larger draft angles due to shrinkage.
Thin-Walled Parts: More draft is needed for flexible, thin components like catheter tips and microfluidic devices.
Using proper draft angles prevents defects like warping, stress marks, and ejection failures, ensuring smooth high-precision medical parts.
For medical applications, casting is NOT cheaper than injection molding for high-volume production.
Injection Molding – Best for mass production; high upfront mold cost but low per-unit cost after production begins.
Casting – Used for low-volume medical prototypes, but longer curing times, material waste, and manual labor increase costs.
When is casting used?
Custom prosthetics, dental implants, or orthopedic components.
Silicone molding for flexible, small-batch medical parts.
For scalable medical production, injection molding is the most cost-effective and precise method.
Injection molding for medical plastics is not inherently cheap, but it becomes cost-effective in high-volume production.
Expensive Initial Costs – Molds cost $20,000–$500,000, requiring precision CNC machining.
Low Per-Unit Cost – Once molds are made, per-unit costs drop significantly, often under $1 per part.
Regulatory & Cleanroom Expenses – FDA and ISO 13485 compliance add costs but ensure safety and consistency.
For mass production of medical devices (e.g., syringes, drug delivery systems), injection molding is the cheapest and most reliable method due to scalability, automation, and precision.
Injection molds for medical plastic components can last anywhere from 100,000 to 5,000,000 cycles, depending on:
Mold Material – Hardened stainless steel molds last 1M+ cycles, while aluminum molds last 100,000–200,000 cycles.
Medical Plastic Type – High-temperature plastics like PEEK and PPSU wear molds faster.
Maintenance & Cleaning – Regular cleanroom maintenance, lubrication, and precision CNC rework extend mold life.
Injection Pressure & Heat – High-pressure molding (e.g., for microfluidics) shortens mold lifespan.
For high-precision medical parts, manufacturers invest in hardened steel molds to ensure long-lasting, defect-free production.
Contact our professional team now for a same-day quote and risk-free project evaluation. Benefit from ISO 8 cleanrooms, advanced machines, and 12-hour fast response in medical injection molding.