Medical silicone injection molding is a specialized manufacturing process used to create precise and reliable silicone components for medical devices. This method involves injecting liquid silicone rubber (LSR) into a mold to form intricate parts with high precision. The process is crucial in medical device manufacturing because it allows for the production of components that meet strict regulatory standards and provide consistent performance. The benefits of medical silicone injection molding include excellent biocompatibility, durability, flexibility, and resistance to temperature extremes, making it ideal for critical medical applications such as seals, gaskets, and tubing. Additionally, this molding process ensures tight tolerances and reproducibility, especially with precision mold medical components, enhancing the quality and safety of medical devices. Medical silicone injection molding is a precise process for creating high-quality, reliable silicone parts for medical devices with repeatability and precision.
Low-Volume to High-Volume Production Capabilities
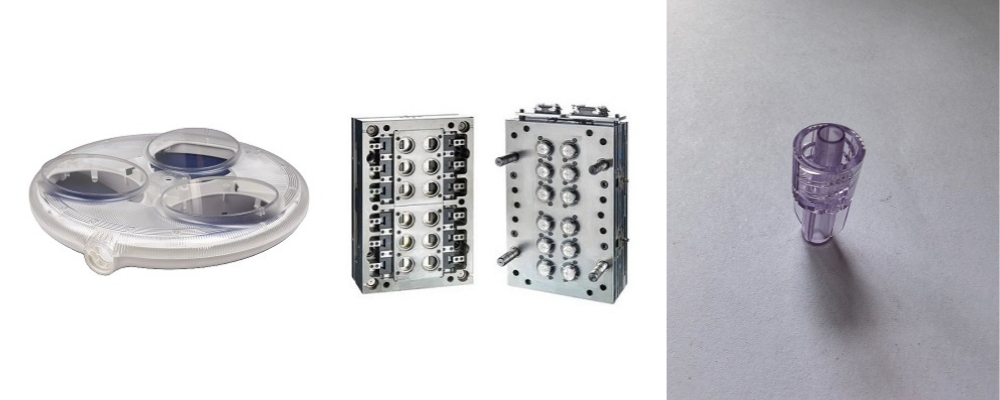
Attributes | Details |
---|---|
Place of Origin | Dongguan, Guangdong, China |
Brand Name | LY Medical Injection Mold |
Product Name | Medical Silicone Injection Molding |
Molding Mode | Plastic Injection Mold |
Product Material | Plastic; ABS/PC/PP/HDPE/POM/PA6/PA6+GF/PVC/NYLON/PMMA/PET, etc. |
Surface Treatment | Customized Surface Texture |
Tolerance | 0.01-----0.05mm |
Features | High Precision, Environmentally Friendly, Durable |
Color | Customized |
Size | Customized |
Length | Customized |
Style | Customized |
Service | OEM ODM |
Processing Service | Molding, Cutting |
Logo | Customized Logo Acceptable |
Quality Control | 100% Inspection |
Mould Life | 250000-500000shots |
Minimum Order Quantity | Accept Small Orders |
Packing Details | Outer Packaging Carton Inner Packaging According to Customer Requirement |
Port | According to Your Requirement |
What is Medical Silicone Injection Molding?
Medical silicone injection molding is a highly specialized manufacturing process used to produce precise, durable, and biocompatible silicone components for the medical industry. This technique involves injecting liquid silicone into a mold under high pressure, where it is shaped and cured to form the desired part. The process is known for its accuracy, repeatability, and ability to create complex, intricate designs that meet the stringent standards required in medical applications. Below, we will explore medical silicone injection molding from multiple aspects, including its benefits, key characteristics, and applications.
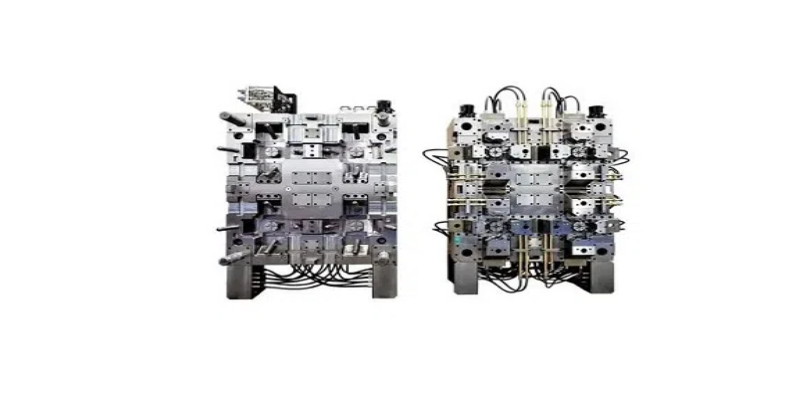
Precision and Accuracy in Manufacturing
Medical silicone injection molding is renowned for its precision and ability to produce parts with tight tolerances. The process uses high pressure to inject liquid silicone into a mold cavity, ensuring that the material fills every detail of the mold. This results in highly accurate and consistent parts, which is crucial for medical devices that require reliable and functional components. The precision of this method helps reduce errors and waste, making it ideal for the production of small and intricate medical parts, such as implants, seals, or surgical tools.
Biocompatibility and Safety
One of the defining characteristics of medical silicone injection molding is the use of medical-grade silicone, which is biocompatible and safe for use within the human body. Silicone is known for its hypoallergenic properties, making it suitable for individuals with sensitive skin or allergies. It is also non-toxic and resistant to bacterial growth, which is vital for preventing infections in medical applications. Silicone’s inert nature means it does not react with the body’s tissues, making it ideal for long-term use in devices like implants, catheters, and prosthetics.
Flexibility and Durability
The molding process itself allows for a high degree of flexibility in terms of design. Medical silicone injection molding can produce parts with varying levels of hardness, flexibility, and other material properties tailored to the needs of specific applications. This adaptability is crucial for creating both rigid and flexible components that need to withstand different levels of stress or movement within the body. Additionally, medical silicone is highly durable, resistant to extreme temperatures, UV light, and chemicals, ensuring longevity and reliability in medical devices.
Applications in the Medical Industry
Medical silicone injection molding is used across a wide range of medical applications, from surgical instruments and wound care products to implants and drug delivery systems. This method is particularly useful for manufacturing high-precision, small parts that are critical to the functioning of medical devices. Silicone’s ability to maintain its integrity and performance in diverse medical environments makes it a go-to material for medical device manufacturers. Additionally, the sterilization compatibility of medical silicone ensures that these devices can be safely reused when necessary.
Cost Efficiency and Scalability
Another important advantage of medical silicone injection molding is its cost efficiency, especially for large-scale production. Once the initial mold is created, it can be used to produce thousands or even millions of identical parts with minimal cost per unit. This makes it an excellent choice for medical device manufacturers looking to reduce costs while maintaining high standards of quality and precision. Additionally, the automated nature of the injection molding process allows for fast production cycles, improving efficiency and making it scalable for both small and large production runs.
Customization and Innovation
The versatility of medical silicone injection molding allows for extensive customization, enabling manufacturers to create medical components tailored to specific patient or device requirements. This is particularly important in the development of specialized medical devices, such as implants that need to match the unique anatomy of a patient. Manufacturers can also innovate by incorporating advanced features into silicone parts, such as antimicrobial coatings or specific texture patterns, to enhance functionality and improve patient outcomes.
Medical silicone injection molding is a highly advanced and versatile manufacturing process that offers numerous benefits, including precision, biocompatibility, flexibility, and cost efficiency. It is an essential technology in the production of medical devices, allowing manufacturers to create safe, reliable, and high-quality components for a wide range of applications. From ensuring patient safety to enabling innovation in medical technology, medical silicone injection molding plays a crucial role in advancing healthcare solutions worldwide.
Medical Silicone Injection Molding Near Me
Finding reliable local suppliers and service providers for medical silicone injection molding can significantly streamline the production process, offering many benefits. When searching for manufacturers nearby, consider the following factors to ensure you select the right partner for your medical device needs.
How to Find Local Suppliers and Service Providers
- Search online using keywords like “medical grade silicone rubber near me” to find manufacturers in your area.
- Network within industry events and trade shows to connect with reputable local providers.
- Reach out to industry associations that specialize in silicone molding and medical device production for recommendations.
- Ask for referrals from other businesses that use medical silicone injection molding services.
Advantages of Choosing Local Manufacturers
- Faster delivery times: Working with local manufacturers can significantly reduce lead times for prototypes and bulk orders.
- Reduced shipping costs: Local suppliers lower transportation expenses, making your overall project more cost-effective.
- Easier communication: Proximity makes it easier to establish clear communication with the supplier, ensuring smoother project coordination.
- Access to industry expertise: Local manufacturers often have deep knowledge of regional medical device regulations and standards.
Tips for Evaluating Nearby Options for Silicone Injection Molding Services
- Review certifications and compliance: Ensure the manufacturer complies with relevant medical device regulations, such as FDA and ISO certifications.
- Assess quality control processes: Evaluate the supplier’s commitment to quality, such as their use of precise medical molding techniques and post-production testing.
- Consider scalability: Determine whether the manufacturer can handle your production needs, whether you require small batches or large-scale manufacturing.
- Request samples: Ask for test runs or samples to assess the quality and precision of their medical silicone injection molding work.
By focusing on these key factors, you can find a local provider that offers high-quality and reliable medical silicone injection molding services, helping you efficiently meet the needs of your medical device projects.
Medical Silicone Injection Molding Suppliers
When sourcing medical grade silicone injection molding services, selecting the right supplier is crucial to ensuring high-quality, compliant products for medical devices. Providers of medical injection molding services play a vital role in meeting industry standards, and the following sections will help you identify key suppliers, understand the essential qualities of a reliable provider, and explore the supplier’s role in the production process.
Key Suppliers in the Industry
- Established silicone injection molding companies: Look for suppliers with a proven track record in the medical industry. Companies with extensive experience can offer high precision and meet the complex requirements of medical applications.
- Local and regional suppliers: Many suppliers specialize in certain regions, providing benefits such as quicker lead times and personalized service.
- Global suppliers: Some international suppliers are equipped to handle large-scale, high-volume production, with the ability to meet stringent global regulatory standards.
- Niche specialists: Certain suppliers may focus on niche areas such as micro-molding or high-precision medical silicone components, which are often needed for specialized devices.
What to Look for in a Reliable Supplier
- Certifications and compliance: Ensure that the supplier complies with industry standards, such as ISO 13485 for medical devices and FDA regulations for manufacturing.
- Expertise in medical silicone injection molding: Choose a supplier with specific expertise in medical-grade silicone, as it requires a deeper understanding of biocompatibility and durability for critical applications.
- Quality assurance systems: Reliable suppliers should have robust quality control systems in place, including routine testing and validation, to ensure the silicone components meet the required specifications.
- Manufacturing capabilities: Suppliers should have state-of-the-art equipment, such as liquid silicone rubber (LSR) injection medical molding machines, to produce highly detailed and intricate medical components.
- Production flexibility: A good supplier should be able to scale production according to your needs, whether it’s a small batch or a large-scale manufacturing run.
The Role of Suppliers in the Production Process
- Material sourcing: Suppliers play a key role in selecting and sourcing high-quality, medical-grade silicone that meets the necessary standards for medical devices.
- Molding and manufacturing: Suppliers manage the injection molding process, ensuring precision and consistency in the production of medical silicone components.
- Quality control and testing: A reliable supplier will conduct thorough quality checks throughout the production process, from initial prototypes to final components, to ensure that all products meet industry standards.
- Post-production services: Many suppliers offer additional services such as packaging, assembly, and sterilization to ensure that the components are ready for medical use and distribution.
Selecting the right supplier for medical silicone injection molding ensures that your medical components meet the highest standards of safety, quality, and compliance, helping to drive the success of your medical devices.
FUJIU Medical Silicone Injection Molding Manufacturer
At FUJIU Medical Injection Mold, we pride ourselves on being a trusted partner specializing in custom precision medical molds and medical silicone injection molding. With over 20 years of experience in precision mold manufacturing and 11 years in project and supply chain management, we bring unmatched expertise to the medical industry. Our ISO Class 8 cleanroom and 20 state-of-the-art injection molding machines ensure the production of high-quality, precise medical silicone components.
What sets us apart is our commitment to collaboration, ethical practices, and continuous improvement. Our deep expertise in medical silicone injection molding enables us to address production challenges and provide tailored solutions that meet the highest industry standards. By focusing on minimizing risks and adding value, we ensure every product we create aligns with our clients’ goals. Our dedication to quality, precision, and innovation makes us the ideal choice for manufacturers seeking reliable and top-tier medical silicone injection molding solutions.
Medical Silicone Injection Molding Process Steps
Medical silicone injection molding is a precise and efficient manufacturing method used to produce high-quality silicone components for medical applications. The process involves several key stages: clamping, injection, cooling, and ejection. Each stage plays a crucial role in ensuring that the silicone material is properly molded into the desired shape, achieving both precision and durability. Below is a detailed explanation of each of these critical steps in the medical silicone injection molding process.
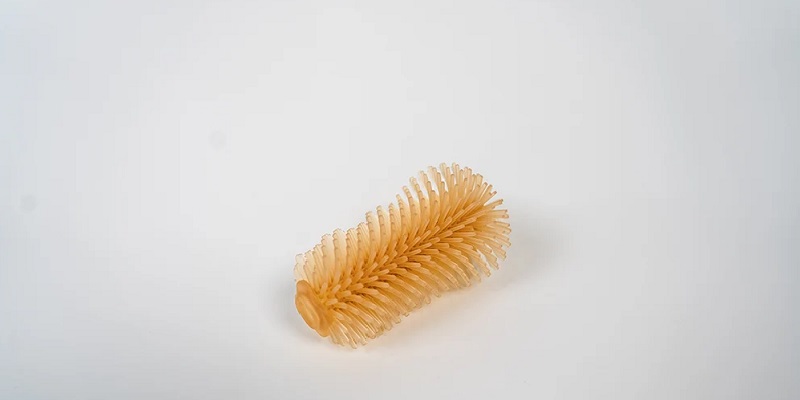
Clamping Stage
The clamping stage is the first step in the silicone injection molding process. During this phase, the mold is closed tightly, and pressure is applied to keep it securely in place while the liquid silicone is injected. The mold is typically heated using electric heaters or water circulating through the mold. A cold runner system can also be used to prevent the silicone from prematurely curing in the runner or surrounding areas. This ensures that the silicone flows smoothly into the mold cavity. In liquid silicone rubber molding, the material is prepared and then delivered into the injection molding machine through a process-controlled pumping kit that feeds the material into a static mixer.
Injection Stage
The injection stage is where the liquid silicone is injected into the mold under high pressure. Silicone rubber material is pumped through pipes or tubes into the injection molding machine, where it is heated to the correct temperature. The material is injected into the mold cavity in a controlled “shot,” referring to the amount of material used in each cycle. This phase is completed once the mold is filled up to 95%-99% of its capacity. During this phase, the silicone undergoes a vulcanization process where the material starts to solidify. The injection mold holding phase occurs next, where continuous pressurization increases the density of the silicone, gradually filling the mold cavity. The pressure builds up as the material solidifies, and this holding flow process continues until the gate hardens, marking the end of the injection phase.
Cooling Stage
Cooling is one of the most critical stages in the medical silicone injection molding process. The mold is equipped with a cooling system designed to efficiently lower the temperature of the molded silicone product. Proper cooling ensures that the molded part retains its shape and does not deform due to external forces. Cooling time can account for as much as 70%-80% of the entire molding cycle. Therefore, an optimized cooling system is essential to reduce cycle times and enhance production output. As the silicone cools, it solidifies and increases in viscosity, making it more resistant to deformation and allowing for the final shaping of the product.
Ejection Stage
The ejection stage occurs after the molding cycle is completed. Unlike thermoplastic molds that use ejector pins, liquid silicone rubber molding does not always require such mechanisms. When the mold opens, the complete product typically remains in one half of the mold. The product’s design is carefully considered so that it is positioned above the mold’s dividing line surface. This design choice facilitates easy demolding without damaging the finished product. The silicone product is now fully formed and ready for any further processing or packaging.
The medical silicone injection molding process is a well-orchestrated series of steps that work together to produce precise and high-quality silicone components. From clamping and injection to cooling and ejection, each phase plays an essential role in ensuring that the final product meets the strict requirements of the medical industry. The efficiency of this process, combined with the versatility and biocompatibility of silicone, makes it the ideal method for producing medical devices and components that demand high performance and reliability.
Medical Silicone Injection Molding Kit
Medical silicone injection molding kits offer an accessible way to create custom silicone components, particularly for small-scale projects or prototyping in medical device manufacturing. These kits are designed to provide all the necessary materials and tools for creating medical-grade silicone parts, making them a practical option for engineers, designers, and manufacturers.
Overview of Kits for DIY Molding Processes
- Complete DIY solution: A typical silicone injection molding medical kit includes silicone rubber, mixing tools, injection molds, and sometimes even a syringe or injection machine, offering a simplified approach to small-scale applications that complement professional medical molding services for more complex production needs.
- Scalability: Although designed for small batches or prototypes, these kits can provide insight into the molding process and allow for adjustments before committing to large-scale production.
- Customization: Kits often include flexible molds that allow users to create a range of part sizes and shapes, ensuring that medical device components can be tailored to specific needs.
- Learning tool: These kits are also useful for educational purposes, allowing newcomers to the field to gain hands-on experience with medical silicone mold.
How Medical-Grade Silicone Kits Are Different from Regular Silicone Molding Kits
- Material quality: Medical-grade silicone in these kits is specifically selected for biocompatibility, non-toxicity, and resistance to heat and chemicals, making it suitable for medical device components that come in contact with the body.
- Compliance with medical standards: Unlike regular silicone kits, medical silicone injection molding kits are made with materials that adhere to FDA and ISO standards for medical device manufacturing.
- Precision and reliability: Medical-grade silicone offers tighter tolerances and superior durability, which is critical for devices that require high levels of precision, such as seals, gaskets, or flexible components in medical devices.
- Specialized additives: These kits may include additives that improve silicone’s resistance to biofluids, UV radiation, or high-temperature environments—properties essential in medical devices.
Where to Buy and How to Use Medical Silicone Injection Molding Kits
- Where to buy: Medical silicone injection molding kits can be found at specialized suppliers who focus on medical-grade materials. They may be available online through distributors of medical supplies or directly from manufacturers of silicone materials.
- How to use:
- Prepare the mold: Begin by preparing the mold cavity using the provided mold material, ensuring it is clean and free from any contaminants.
- Mix the silicone: Mix the liquid silicone rubber according to the manufacturer’s instructions, ensuring the correct ratio of components for optimal curing and performance.
- Inject the silicone: Use the included injection syringe or small-scale injection machine to fill the mold cavity with the silicone mixture. Make sure the silicone is injected evenly to avoid air pockets.
- Cure the silicone: Allow the silicone to cure as per the manufacturer’s guidelines, which may involve heating or room-temperature curing, depending on the kit’s instructions.
- Post-processing: After the component has cured, carefully remove it from the mold and conduct any necessary finishing steps, such as trimming excess silicone or cleaning the component.
Medical silicone injection molding kits are an excellent way to prototype or produce small quantities of high-quality silicone components for medical applications. They offer a hands-on approach to molding while ensuring the end products meet the necessary medical-grade standards.
Advantages of Medical Silicone Injection Molding
Medical silicone injection molding offers a wide range of advantages, making it a highly effective and efficient process for producing precision components for the medical industry. The process ensures high-quality, durable, and biocompatible silicone parts that meet strict medical standards. Below, we will explore the key advantages of medical silicone injection molding, from reduced cycle times and flash-free tooling to the ability to create insert molded parts and minimize material waste.
Reduced Cycle Time
One of the main advantages of medical silicone injection molding is the reduced cycle time, which significantly increases production efficiency. Cycle times for parts such as keyboards or medical components range from as little as 30 seconds to 2 minutes, depending on the complexity of the part. This rapid processing time allows manufacturers to produce a high volume of parts in a short period, boosting the overall output compared to alternative methods like compression molding, which often have longer cycle times. Faster cycle times contribute to cost savings and improved production efficiency, making the process ideal for mass production of medical components.
Flash-Free Tooling
Flash-free tooling is another significant benefit of medical silicone injection molding. The use of a well-designed gate and runner system, along with flash rings and vent rails, helps ensure that there is minimal or no flash around the molded part. Flash refers to the excess material that escapes from the mold and forms around the edges of the part, which then requires trimming. By preventing flash from forming, medical silicone injection molding reduces the time and labor involved in post-production trimming and finishing. This results in cleaner, more precise parts and reduces material waste, contributing to lower production costs.
No Preforms Required
Unlike compression molding, medical silicone injection molding does not require preforms. Preforms are the basic shape of the finished product that must be inserted into each mold cavity to ensure the material fills the cavity completely. In compression molding, these preforms are made with excess material, which often leads to flash around the mold. Since medical silicone injection molding directly injects liquid silicone into the mold, the process eliminates the need for preforms, reducing complexity and material waste. This simplification of the production process not only saves time but also enhances the efficiency of part creation.
Ability to Make Insert Molded Parts
Medical silicone injection molding offers the unique advantage of making insert molded parts. This is especially beneficial when integrating clear silicone inserts into the final product. For example, medical devices such as keyboards or buttons can be overmolded with silicone, creating a seamless connection between the insert and the overmolded silicone material. This process is ideal for applications requiring additional features, such as leak-proof seals or enhanced functionality, like incorporating displays or buttons into medical devices. The cross-linked bonds created during the overmolding process provide a strong, durable connection that improves the overall quality and integrity of the final product.
Minimal Material Waste
Medical silicone injection molding is highly efficient in terms of material usage, with only minimal waste produced during the process. The primary material waste is confined to the gate and runner system, which delivers silicone to the mold. However, manufacturers can use a cold runner system to prevent the silicone from hardening in the runner, which helps reduce material waste. This system is particularly beneficial for large-volume orders, where waste could otherwise become more significant. The ability to recycle and minimize material waste ensures that the production process is cost-effective and environmentally friendly, especially when producing large quantities of medical parts.
Medical silicone injection molding offers several advantages, including reduced cycle times, flash-free tooling, the elimination of preforms, the ability to create insert molded parts, and minimal material waste. These benefits make it an ideal choice for producing high-quality, precise, and biocompatible silicone components used in medical devices. With its efficiency, precision, and cost-effectiveness, medical silicone injection molding is the preferred manufacturing method for producing reliable and durable medical parts that meet the stringent requirements of the healthcare industry.
Customized Medical Silicone Injection Molding Steps
Customized medical silicone injection molding is a detailed and multi-step process that ensures high-quality, precision components for medical applications. This approach involves several stages, each tailored to meet the specific needs of the medical devices or parts being produced. From silicone injection molding to value-added processes, each step plays a crucial role in shaping the final product. Below, we will describe the customized steps involved in medical silicone injection molding, from initial molding to final assembly.
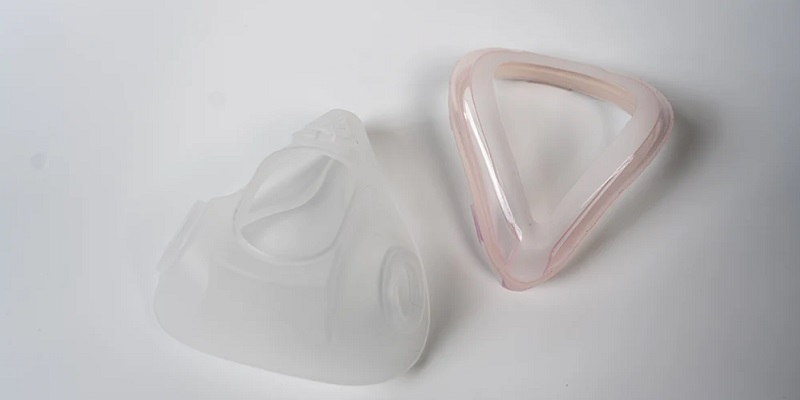
Silicone Injection Molding
Silicone injection molding is the first and most critical step in the customized medical silicone injection molding process. In this phase, liquid silicone rubber (LSR) is injected into a mold under high pressure. The mold is typically preheated to ensure optimal curing conditions for the silicone material. The material is injected into the mold cavity and allowed to cool and solidify, forming the base shape of the medical component. This step is highly precise and ensures that the silicone parts meet strict specifications for size, shape, and quality. The liquid silicone used is often biocompatible, making it ideal for use in medical devices that require high safety standards.
Silicone Compression Molding
Silicone compression molding is another critical step that can be used in combination with silicone injection molding to achieve specialized shapes or properties. In this step, silicone material is placed into a mold cavity and then compressed under high heat and pressure. This process helps the material conform to the mold’s shape while ensuring a high-quality finish. Compression molding is often used for larger or more intricate components, offering advantages in terms of material consistency and minimizing defects. While injection molding is more common, compression molding can be a useful technique when specific features are required that cannot be achieved by injection molding alone.
Silicone Die Cutting
Silicone die cutting is an additional step used to create precise silicone parts with specific shapes. After molding, sheets of silicone material may be cut into customized shapes using a die. This process ensures that parts such as gaskets, seals, or membranes are cut to the exact size and dimensions needed for medical devices. Die cutting allows for efficient mass production of uniform silicone parts, reducing manual labor and increasing consistency. The cutting process can also be combined with various finishes or surface textures to enhance the performance and appearance of the parts.
Silicone Dipping
Silicone dipping is used for creating protective coatings or layers on medical components. In this process, medical parts are dipped into liquid silicone, which then forms a uniform coating over the part. The coated part is then heated to cure the silicone, ensuring that it bonds securely and provides a protective, biocompatible layer. Silicone dipping is often used for creating soft, flexible coatings on tools or medical instruments that require a smooth, non-slip surface. It is also used for applications where parts need to be insulated or protected from wear and tear.
Silicone Component Assembly
Once the silicone parts are molded, die-cut, or coated, they may require assembly to create a finished medical device or component. This step involves putting together multiple parts to form a functional unit. For instance, parts may be bonded together using medical-grade adhesives or secured using mechanical fastening methods. Assembly also includes testing the functionality of the final product to ensure it meets the necessary medical standards and specifications. This stage is crucial for ensuring that the silicone components work seamlessly together and are ready for use in medical devices, such as surgical tools or diagnostic equipment.
Value-Added Process
The value-added process is the final stage in the customized medical silicone injection molding procedure, where additional features or enhancements are applied to the molded parts. These processes can include overmolding, inserting components such as wires or electrical parts, or adding specific coatings to improve the performance or appearance of the silicone components. Value-added processes can also involve testing, packaging, and labeling of the final products to ensure they meet regulatory standards for medical devices. By adding value through these additional processes, manufacturers can ensure that their medical silicone components are ready for use in the most demanding healthcare environments.
Customized medical silicone injection molding involves several steps, each tailored to ensure the production of high-quality, precise, and reliable silicone components. From silicone injection molding and compression molding to die cutting, dipping, assembly, and value-added processes, each phase plays a vital role in producing medical components that meet stringent safety and performance standards. By following these detailed steps, manufacturers can deliver customized silicone parts that are integral to the functionality of medical devices, ensuring patient safety and optimal device performance.
Medical Silicone Injection Molding for Sale
When looking to purchase medical silicone injection molding products, it is essential to know where to find them, what price ranges to expect, and what factors influence the cost. Medical silicone components are used in a wide variety of devices and applications, from implants to surgical instruments, and sourcing these products requires careful consideration.
Where to Find Medical Silicone Injection Molding Products for Sale
- Specialized suppliers: Medical silicone injection molding products can be purchased from suppliers that specialize in medical-grade materials. These suppliers typically offer a range of silicone products, including molded parts, raw silicone for molding, and custom solutions for various medical applications.
- Distributors of medical equipment: Companies that distribute medical equipment often carry silicone components, including gaskets, seals, tubing, and other molded silicone parts used in medical devices.
- Direct from manufacturers: Some manufacturers offer the option to purchase medical silicone injection molding products directly, allowing for more customization and a direct connection to the production process.
- Online marketplaces: Certain online platforms and industry-specific marketplaces may offer medical silicone components, especially for smaller orders or prototyping. These platforms often feature both ready-made and custom silicone products for medical use.
Price Ranges for Different Products
The price of medical silicone injection molding products can vary widely depending on several factors. Below are general price ranges for some common products:
- Standard molded components: For simple, standard silicone parts such as seals and gaskets, prices can range from $0.10 to $5.00 per unit, depending on the quantity and complexity of the part.
- Custom-molded parts: More intricate or custom-designed components, especially those that require complex molds or specific biocompatibility testing, can cost anywhere from $5.00 to $50.00 or more per unit.
- Raw silicone for molding: Purchasing raw silicone rubber for molding typically costs between $20.00 and $50.00 per pound, depending on the quality and type of silicone needed (e.g., LSR or HCR).
- Small batch orders: Small-batch production or prototype orders can have a higher per-unit price due to setup costs, with prices potentially ranging from $100 to $1,000 for small quantities.
Factors That Influence the Cost of Medical Silicone Molding Products
- Complexity of the design: The more intricate the mold and design of the silicone part, the higher the cost. Custom medical silicone molds, tight tolerances, and detailed features increase production time and tooling costs.
- Material quality: Medical-grade silicone, which must meet strict standards for biocompatibility, durability, and performance, tends to be more expensive than general-purpose silicone. The quality and specifications required (e.g., heat resistance, chemical resistance) can affect pricing.
- Volume of production: Higher production volumes generally lead to lower per-unit costs due to economies of scale. Smaller batches, especially for prototypes or limited runs, tend to be more expensive per unit.
- Regulatory compliance: Products that require additional testing or certification, such as FDA approval for use in medical devices, can incur higher costs due to the regulatory requirements for quality control, validation, and documentation.
- Tooling and setup fees: The cost of molds, including initial tooling and setup for custom parts, plays a significant role in the overall cost of production. Custom molds can be expensive, and the larger the volume, the more cost-effective the tooling becomes over time.
Purchasing medical silicone injection molding products involves understanding the different factors that can influence both the availability and pricing of components. By working closely with experienced suppliers, you can ensure you get the right materials at the right price for your specific medical application.
Medical Silicone Injection Molding: Silicone Molded Medical Device Components
Silicone molded medical device components are critical elements in the production of medical devices, offering unparalleled benefits in terms of safety, durability, and functionality. Medical silicone injection molding is the process used to create these high-performance components that meet the stringent demands of the healthcare industry. This process ensures precise molding of silicone materials into parts that serve vital functions in medical applications.
Overview of Silicone Molded Medical Device Components
Silicone molded components are created using medical silicone injection molding, which involves injecting liquid silicone into a mold to form parts with intricate details and high precision. These components are often used in applications that require biocompatibility, flexibility, and resistance to harsh conditions such as extreme temperatures, moisture, and chemicals. Silicone’s unique properties make it an ideal material for use in medical devices, as it provides both durability and patient safety.
Types of Medical Devices Made with Silicone Components
Various medical devices rely on silicone molded components to function effectively. Some common medical devices made with silicone include:
- Seals and gaskets: Used to provide airtight and watertight seals in medical devices such as infusion pumps, syringes, and respiratory equipment.
- Tubing: Flexible silicone tubing is commonly used in applications such as catheters, IV lines, and feeding tubes, offering both flexibility and biocompatibility.
- Stoppers and plugs: Silicone molded stoppers and plugs are used to prevent contamination and ensure safety in medical vials, syringes, and other containers.
- Valves: Silicone is used in the manufacture of valves for medical devices that require controlled flow of fluids, such as in heart pumps and dialysis machines.
Advantages of Using Silicone in Medical Devices
Medical-grade silicone offers several advantages that make it an optimal material choice for molded components in medical devices. Some of the key benefits include:
- Biocompatibility: Medical silicone is non-toxic and non-reactive with body tissues and fluids, making it safe for use in devices that come into contact with the human body.
- Flexibility and elasticity: Silicone’s flexibility allows for easy adaptation in devices that need to conform to various shapes or maintain structural integrity under stress.
- Durability: Silicone molded components are highly resistant to aging, UV exposure, and wear, ensuring long-lasting performance even in challenging environments.
- Resistance to temperature extremes: Silicone retains its properties in both high and low-temperature environments, making it suitable for medical devices that require sterilization or need to function in extreme conditions.
How Silicone Molded Medical Device Components Contribute to Improved Patient Care and Device Performance
Silicone molded components play a crucial role in enhancing both patient care and the overall performance of medical devices. Some ways these components contribute to healthcare include:
- Enhanced patient safety: Silicone’s biocompatibility ensures that there is no adverse reaction when in contact with human tissues or fluids, minimizing the risk of infection or irritation.
- Improved functionality: Components like silicone seals and valves improve the reliability and precision of medical devices, ensuring that they perform consistently and accurately.
- Longer lifespan: The durability of silicone components means that medical devices are more reliable over time, reducing the need for replacements and maintenance.
- Comfort and adaptability: The flexibility of silicone makes it ideal for components that require patient comfort, such as tubing or seals in respiratory devices, ensuring a more pleasant experience for the patient.
Incorporating silicone molded components into medical devices helps manufacturers meet the demanding standards for safety, performance, and patient care. The versatility and reliability of medical silicone injection molding, combined with medical component molding, make it an essential process in the creation of high-quality medical devices that improve both outcomes and patient well-being.
FAQs about Medical Silicone Injection Molding
Medical silicone and regular silicone differ primarily in terms of their composition and intended use. Medical silicone is specifically formulated to meet strict regulatory standards and is designed for applications where biocompatibility is essential. It is non-toxic, non-reactive, and safe for prolonged contact with human tissues and bodily fluids. This makes it ideal for use in medical devices such as catheters, seals, gaskets, and implants, where the safety and well-being of the patient are paramount.
In contrast, regular silicone, while still a versatile and durable material, may not meet the rigorous biocompatibility standards required in medical applications. It is typically used in industrial, commercial, and consumer products where direct contact with the human body is not a concern. The main difference lies in the higher purity, strict testing, and certifications (such as FDA approval and ISO standards) that medical silicone undergoes to ensure it is safe for medical use.
Therefore, when considering materials for medical devices, it’s essential to use medical-grade silicone, which guarantees safety, durability, and performance under demanding conditions.
Yes, silicone can be used in injection molding, and in fact, it is one of the most popular materials for this process, especially in medical and industrial applications. Silicone injection molding involves injecting liquid silicone rubber (LSR) into a mold to create precise, high-quality components. This process is ideal for manufacturing complex shapes with high accuracy and consistency, which is especially important for medical devices that require strict tolerances.
Silicone’s flexibility, durability, and resistance to extreme temperatures make it an excellent material for injection molding. It is commonly used to produce seals, gaskets, tubing, and other medical components that must withstand harsh environments while maintaining their shape and functionality.
Moreover, silicone injection molding allows for the production of both small and large batches, offering scalability for both prototyping and mass production. The process also ensures minimal waste, making it cost-effective for manufacturing. Because of its ability to produce intricate designs, medical silicone injection molding has become an essential technique for the medical industry, ensuring that parts are made with high precision and meet the necessary safety standards.
Contact our professional team now for a same-day quote and risk-free project evaluation. Benefit from ISO 8 cleanrooms, advanced machines, and 12-hour fast response in medical injection molding.