Medical precision machining factories, including precision medical machining manufacturers, play a critical role in modern healthcare by delivering high-quality, life-saving medical devices. These factories utilize advanced CNC machining technology to produce components with exceptional precision, ensuring their accuracy and reliability for use in critical medical applications. Leading medical precision machining factories delivering high-quality parts for medical devices, implants, and tools with exact tolerances. From implants and surgical instruments to diagnostic equipment, the parts manufactured in medical precision machining factories meet the highest standards of quality, biocompatibility, and safety. Precision machining is indispensable in this industry, as it allows for the creation of intricate designs and tight tolerances essential for healthcare devices. Additionally, medical precision machining factories adhere to strict regulatory requirements, such as ISO certifications and FDA guidelines, ensuring compliance and consistent performance in the production of vital medical components.
Low-Volume to High-Volume Production Capabilities
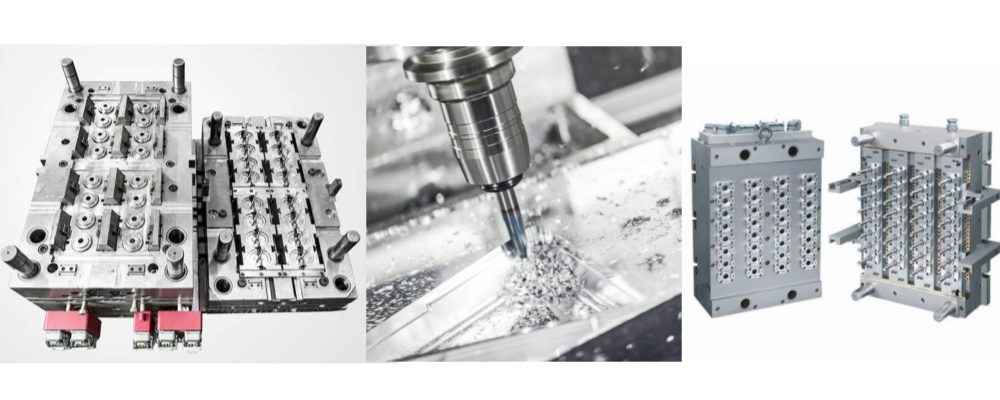
Attribute | Details |
---|---|
Brand Name | LY Medical Injection Mold |
Place of Origin | Dongguan, Guangdong, China. |
CNC Machining or Not | Options: CNC or Non-CNC Machining based on the specific product requirements. |
Material Capabilities | Aluminum, Brass, Bronze, Copper, Hardened Metals, Precious Metals, Stainless Steel, Steel Alloys, Titanium, Cobalt Chrome, Plastic, and other alloys. |
Machining Types | Broaching, Drilling, Etching/Chemical Machining, Laser Machining, Milling, Turning, Wire EDM, Rapid Prototyping, and other customized machining services. |
Micro Machining | Available for products requiring intricate and detailed work. |
Tolerance | ±0.005mm to ±0.1mm |
Surface Treatments | Polishing, Anodizing, Nickel Plating, Zinc Plating, Electroplating, Sandblasting, Painting, Powder Coating, Clear Anodizing, and Oil Printing. |
Service Options | OEM/ODM, One-Stop Services (includes Machining, Assembly, Packaging), Custom Logo Acceptance, and Small Order Accommodations. |
Inspection & Quality | 100% Inspection (Dimension and Quality Control for each product). |
Equipment Used | 3/4/5 Axis CNC Machining Centers, Advanced 3D Printing Equipment, and Precision Tools for Surface Treatments. |
Applications | Medical Devices |
Drawing Formats | 2D (PDF/CAD), 3D (IGES/STEP). |
MOQ | Small Orders Accepted. |
Quotation Lead Time | Within 24 hours. |
Production Lead Time | 12–15 days (may vary depending on the complexity of the order). |
Payment Methods | PayPal, Western Union, Trade Assurance...... |
What is Medical Precision Machining?
Medical precision machining factories play an essential role in creating critical components for the medical industry. Below are the key aspects of this vital process:
Definition and Importance
- Precision machining refers to the process of creating highly accurate and detailed parts, often with tolerances as tight as a few microns.
- In the medical industry, this precision ensures the safety, functionality, and reliability of devices used in life-saving applications.
- The work performed by medical precision machining factories supports both patient care and medical innovation.
Types of Medical Components Produced
- Implants: Examples include orthopedic joint replacements, dental prosthetics, and spinal implants.
- Surgical Instruments: Forceps, scalpels, surgical drills, and other high-precision tools.
- Diagnostic Equipment: Components for MRI scanners, CT machines, and blood filtration systems.
- Miniature Parts: Micro-gears for pacemakers, catheter heads, and other intricate components.
Technologies Used
- CNC (Computer Numerical Control) Machines: Central to medical CNC machining factories, CNC machines offer unmatched accuracy and repeatability.
- Multi-Axis Capabilities: Machines like 5-axis CNC systems enable the creation of complex geometries for customized medical devices.
- Material Versatility: CNC machines can process biocompatible metals such as titanium and stainless steel as well as medical-grade plastics like PEEK and PTFE.
Medical precision machining factories combine cutting-edge technology with meticulous quality standards to produce the components that power modern healthcare.
CNC Machining in Medical Precision Machining Factories
Medical precision machining factories rely heavily on CNC machining to produce the precise and reliable components required for medical devices and equipment. CNC, or Computer Numerical Control, is a manufacturing process that uses computer-guided tools to shape materials into detailed and accurate parts. Its advanced capabilities make it indispensable in the medical industry, where precision is critical for ensuring patient safety and device performance.
The Role of CNC Machining in Medical Manufacturing
CNC machining enables medical precision machining factories to meet the stringent demands of the healthcare sector. By leveraging computer-controlled systems, these factories can fabricate components with exceptional accuracy and consistency. The process is ideal for creating custom parts used in life-saving devices like implants, surgical instruments, and diagnostic equipment. The automation of CNC machining ensures minimal human error, a key factor when manufacturing devices that directly impact patient health.
Key Benefits of CNC in Medical Machining
- High Accuracy and Repeatability
CNC machines excel in delivering high-precision results, ensuring that each component meets exact specifications. This repeatability is crucial when producing medical parts in large quantities without compromising quality. - Capability to Work with Complex Geometries and Tight Tolerances
Modern CNC machining systems, including 5-axis machines, allow for the production of intricate parts with complex geometries. Medical devices often require components with tight tolerances and multi-dimensional designs, which CNC machining can achieve with ease. - Customization of Parts Based on Design Specifications
Medical precision machining factories use CNC technology to create bespoke components tailored to specific patient needs or device requirements. For example, customized implants or unique surgical tools can be designed and manufactured using CNC machines.
Medical precision machining factories depend on CNC technology not only for its precision but also for its flexibility, enabling them to adapt to the ever-evolving demands of the healthcare industry.
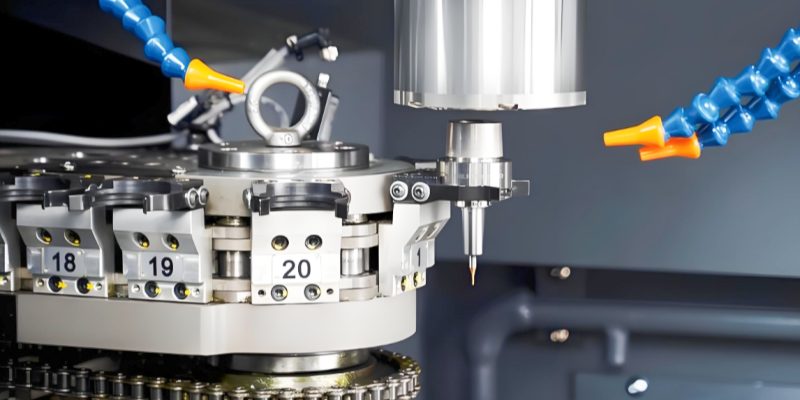
Types of Medical CNC Parts Manufactured by Medical Precision Machining Factories
Medical precision machining factories play a pivotal role in the healthcare industry, producing a wide range of CNC-manufactured parts that are essential for modern medical equipment and devices. These parts, designed with exacting precision, serve various purposes, from life-saving implants to diagnostic tools. Below are the primary categories of medical CNC parts manufactured in these specialized factories.
Implants and Prosthetics
Medical precision machining factories are instrumental in crafting implants and prosthetics that meet the unique needs of patients. These components must not only fit perfectly but also endure the rigors of daily use in the human body.
- Examples:
- Orthopedic Implants: Knee and hip replacements that restore mobility and improve quality of life.
- Dental Implants: Titanium-based components used for permanent tooth replacements.
- Joint Replacements: Components designed with tight tolerances to ensure a seamless fit and function within the body.
These implants are manufactured using biocompatible materials like titanium and stainless steel, ensuring safety and longevity.
Surgical Instruments
Surgical tools require exceptional precision and durability, as they are used in critical procedures where accuracy is paramount. Medical precision machining factories create high-quality instruments with ergonomic designs to enhance usability.
- Examples:
- Forceps and Scalpels: Tools used in intricate surgical procedures.
- Surgical Drills: Precision-machined components used in orthopedic surgeries.
These instruments are crafted to be sterilizable and reliable, adhering to stringent medical standards.
Diagnostic and Monitoring Equipment
Accurate diagnostics are the cornerstone of effective treatment, and medical precision machining factories contribute by producing key components for diagnostic machines.
- Examples:
- MRI Components: High-precision parts critical for imaging systems.
- CT Scanner Parts: Components like collimators and rails that ensure smooth operation.
- Pulse Meters: Precision instruments for monitoring patient vital signs.
These components are manufactured with tight tolerances to ensure the accuracy of diagnostic readings.
Micro and Miniature Components
The advancement of medical technology has driven demand for miniaturized components, which are essential for cutting-edge devices. Medical precision machining factories excel in producing these small yet complex parts.
- Examples:
- Miniature Gears for Pacemakers: Tiny yet critical components that power life-saving devices.
- Micro-Tipped Catheter Heads: Delicate components used for minimally invasive procedures.
Using Swiss machining and other advanced processes, factories achieve extreme precision in miniature manufacturing.
High-Precision, Single-Use Medical Devices
Disposable medical devices are an essential part of modern healthcare, ensuring hygiene and reducing the risk of infection.
- Examples:
- Blood Filtration Devices: Disposable filters for dialysis machines.
- Diagnostic Test Equipment: Components used in single-use testing kits.
Medical precision machining factories produce these devices to meet strict regulatory standards, ensuring reliability and safety for every use.
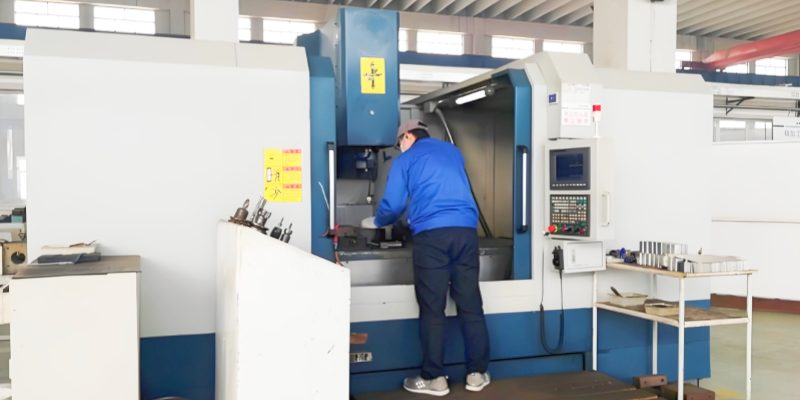
Key Machining Processes in Medical Manufacturing by Medical Precision Machining Factories
By manufacturing such a diverse array of medical precision parts, medical precision machining factories contribute significantly to healthcare advancements, delivering parts that are essential for both patient care and medical innovation. Medical precision machining factories rely on advanced machining techniques to produce components with the exceptional accuracy required for medical devices. These processes ensure that the components meet tight tolerances, adhere to strict regulatory standards, and are biocompatible for use in healthcare applications, including precision mold medical parts. Below are the primary machining processes employed in medical manufacturing.
CNC Turning and Milling
CNC turning and milling are foundational processes in medical precision machining factories, allowing for the creation of complex geometries and surfaces.
- CNC Turning:
- Involves the rotation of the workpiece while cutting tools shape it to the desired dimensions.
- Ideal for cylindrical components such as screws, rods, and pins used in implants and surgical instruments.
- CNC Milling:
- Employs rotary cutting tools to remove material from a workpiece, creating intricate designs and surfaces.
- Suitable for flat or irregularly shaped components, including surgical handles and diagnostic equipment parts.
Both methods ensure high accuracy and repeatability, essential for medical components where precision is critical.
5-Axis Machining
Medical precision machining factories frequently use 5-axis machining to achieve unparalleled precision in multi-dimensional components.
- This advanced process allows for the simultaneous movement of the cutting tool along five axes.
- Enables the creation of intricate designs and undercuts without repositioning the workpiece.
- Commonly used for manufacturing complex implants, surgical guides, and custom prosthetics.
5-axis machining ensures seamless production of detailed parts, improving their performance and reducing lead times.
EDM (Electrical Discharge Machining)
EDM is a non-contact machining process ideal for cutting hard materials and intricate shapes.
- Process Highlights:
- A high-frequency electrical spark erodes the material, creating highly precise cuts.
- Used for components that require tight tolerances and smooth finishes, such as surgical instrument handles and diagnostic device components.
Medical precision machining factories leverage EDM to produce parts with minimal thermal damage, preserving material integrity.
Wire EDM
Wire EDM is a specialized form of electrical discharge machining tailored for creating intricate and tiny components.
- Involves the use of a thin, electrically charged wire to cut through the material.
- Perfect for small, detailed parts like stents, micro screws, and pacemaker components.
- Offers precision down to microns, crucial for advanced medical applications.
Wire EDM ensures that medical devices meet exacting dimensional and functional requirements.
Swiss Machining
Swiss machining is a go-to method in medical precision machining factories for producing small, high-volume components.
- Features of Swiss Machining:
- Combines turning and milling capabilities in a single setup.
- Workpieces are fed through a guide bushing, allowing for stability during machining.
- Ideal for long, slender parts like pins, tubes, and valves used in surgical and diagnostic equipment.
Swiss machining delivers unparalleled precision and efficiency, making it indispensable for high-demand medical applications.
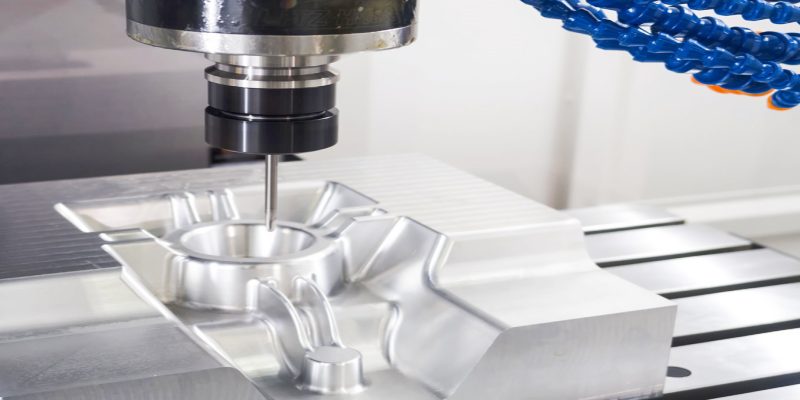
Materials Used in Medical Precision Machining by Medical Precision Machining Factories
The selection of materials plays a crucial role in the effectiveness and safety of medical devices. Medical precision machining factories utilize a diverse range of materials tailored to the unique demands of healthcare applications. Each material is chosen based on its compatibility with the human body, durability, and ability to withstand sterilization and use in critical environments.
Metals in Medical Precision Machining
Metals are a cornerstone in the production of medical components due to their strength, reliability, and biocompatibility.
- Titanium:
- A preferred choice for implants like joint replacements and dental fixtures due to its exceptional biocompatibility and lightweight nature.
- Titanium resists corrosion, making it ideal for long-term use inside the human body.
- Stainless Steel (303, 316, 17-4 PH):
- Frequently used for surgical instruments and diagnostic equipment.
- Offers high strength, excellent resistance to rust, and the ability to endure sterilization processes.
- Inconel and Other Specialized Alloys:
- Known for their ability to withstand extreme conditions, these materials are often used in components for advanced diagnostic devices.
- Brass:
- Utilized for components requiring electrical conductivity and corrosion resistance, such as in monitoring equipment.
Metals processed by medical precision machining factories meet stringent standards to ensure safety and efficacy in medical settings.
Plastics in Medical Precision Machining
Plastics provide versatility and cost-effectiveness while maintaining durability and safety in medical device applications.
- PEEK (Polyetheretherketone):
- A high-performance polymer with excellent thermal and chemical resistance.
- Frequently used in implants and diagnostic device components due to its biocompatibility.
- PTFE (Polytetrafluoroethylene):
- Commonly referred to as Teflon, it is non-reactive and resists chemicals, making it ideal for tubing and other medical components.
- Nylon:
- Lightweight and strong, used in disposable and reusable components across various medical applications.
Medical precision machining factories utilize these plastics for lightweight, flexible designs that deliver reliability without compromising on precision.
Specialty Materials in Medical Precision Machining
Some applications require materials that go beyond traditional metals and plastics, pushing the boundaries of performance.
- Ceramics:
- Widely used in high-performance implants such as joint replacements and dental crowns.
- Ceramics are biocompatible, wear-resistant, and can withstand the body’s environment without degrading.
- Composites:
- Materials combining the strengths of metals and plastics are employed for lightweight yet robust components in advanced medical devices.
Quality Control and Regulatory Standards in Medical Precision Machining Factories
In the medical industry, the stakes are high, and every component produced must adhere to strict quality and regulatory standards. Medical precision machining factories and medical molding play a pivotal role in ensuring that the products they manufacture meet the rigorous demands of healthcare applications. From certification compliance to advanced quality assurance processes, these factories prioritize patient safety and device reliability.
The Importance of Adhering to Stringent Quality Standards
To maintain excellence, medical precision machining factories must conform to globally recognized standards that ensure the reliability, safety, and biocompatibility of their components.
- ISO 9001:2015 Certification:
- This certification focuses on quality management systems, ensuring consistency in manufacturing processes and continuous improvement in operations.
- Factories with ISO 9001:2015 demonstrate their commitment to meeting customer and regulatory requirements.
- ISO 13485:2016 (Medical Devices Certification):
- A specific standard for medical device manufacturers, this certification ensures the production of safe and effective medical devices.
- It includes controls for risk management, traceability, and regulatory compliance.
- FDA Compliance:
- Factories producing components for the U.S. market must comply with the FDA’s stringent guidelines.
- Products must meet requirements for sterility, biocompatibility, and performance to ensure patient safety.
By achieving and maintaining these certifications, precision medical machining factory builds trust with their clients and the healthcare industry.
Key Inspection and Testing Processes
Medical precision machining factories employ advanced inspection and testing protocols to ensure every component meets exact specifications and regulatory standards.
- Dimensional Analysis:
- Precision instruments like coordinate measuring machines (CMM) verify that components conform to design specifications down to micrometer tolerances.
- Surface Finish Testing:
- Ensuring a smooth and accurate surface is critical, especially for implants and surgical tools that come into direct contact with tissues.
- Material Testing:
- Comprehensive testing of raw materials ensures they meet necessary strength, corrosion resistance, and biocompatibility requirements.
- Biocompatibility Verification:
- Essential for components used in implants or devices exposed to bodily fluids, this testing ensures materials will not cause adverse reactions.
By integrating these processes, precision medical machining factories produce medical machined components that meet stringent healthcare industry standards.
Example of a Factory’s Quality Management System
A well-established medical precision machining factory will typically employ a sophisticated quality management system (QMS). For instance:
- Traceability Systems:
- Every part manufactured is logged with detailed documentation, from raw materials to the finished product, ensuring full traceability.
- Automated Inspection:
- Advanced inspection systems such as laser scanners and vision systems streamline quality checks for consistent results.
- Real-Time Monitoring:
- Machines equipped with IoT-enabled sensors monitor production processes, minimizing errors and downtime.
The Role of a Precision Medical Machining Parts Factory in Healthcare Innovation
A precision machining medical parts factory serves as a cornerstone of modern healthcare innovation. These specialized facilities produce intricate components critical for advanced medical devices, including implants, diagnostic equipment, and surgical instruments. By leveraging cutting-edge technologies such as CNC machining, these factories ensure that every part is crafted with utmost accuracy, meeting the tight tolerances required in medical applications.
With their ability to work with biocompatible materials like titanium, stainless steel, and PEEK, precision medical machining parts factories deliver parts that are not only durable but also safe for patient use. These factories support the healthcare industry’s demand for both high-volume production and custom-made solutions, driving advancements in medical technology and improving patient outcomes worldwide.
Leading Medical Precision Machining Factories
At FUJlU Medical Injection Mold, we take pride in offering industry-leading medical precision machining services. With a commitment to exceeding the stringent expectations of the healthcare industry, we provide cutting-edge solutions for manufacturing critical medical components. Our ISO 9001:2015-certified facilities utilize advanced technology, including CNC Swiss machining, CNC turning, and CNC milling, to deliver precision-engineered parts that meet the highest quality standards.
Unmatched Precision and Capabilities
Our precision machining capabilities are tailored to produce the intricate components required for medical devices. With tolerances as tight as ±0.0001 inches, our CNC Swiss machining services ensure the production of the smallest and most complex parts. Our turning and milling centers are equipped to handle high volumes while maintaining exceptional consistency, making them ideal for repetitive production of intricate components.
Core Machining Services
- CNC Swiss Machining: Equipped with up to 9-axis lathes, our Swiss machining process excels at producing highly detailed parts with extreme precision. This service is perfect for creating components with intricate geometries required for surgical instruments, orthopedic implants, and more.
- CNC Turning and Milling: Our CNC turning and milling processes deliver complex parts with exceptional accuracy and repeatability. These methods are particularly suited for manufacturing components used in diagnostic equipment and other medical devices.
Materials for Medical Components
We specialize in machining a wide range of materials commonly used in medical manufacturing, including:
- Stainless Steel: Durable and biocompatible, ideal for surgical instruments and implants.
- Aluminum: Lightweight and corrosion-resistant, used in various medical devices.
- Titanium and Titanium Alloys: Strong and biocompatible, perfect for implants and bone screws.
- Medical-Grade Plastics: Ensures sterility and precision for components like housings and insulators.
- Gold, Brass, and Bronze: Used for specific high-precision applications.
Additional Finishing Services
To ensure flawless products, we offer comprehensive finishing services:
- Internal Finishing: Includes deburring, polishing, and surface grinding to achieve smooth, sterilizable surfaces.
- Coordinated Services: We collaborate with industry leaders to provide essential services like passivation and specialized coatings for enhanced durability and biocompatibility.
Commitment to Quality
Our success stems from a steadfast dedication to quality. Every component undergoes rigorous inspection to ensure compliance with FDA guidelines and industry standards. Our facilities employ Esprit CAD/CAM systems, enabling the accurate production of complex geometries with unparalleled precision.
Why Choose FUJlU Medical Injection Mold?
- ISO 9001:2015 Certification: Guarantees quality management and manufacturing excellence.
- Advanced Machinery: State-of-the-art CNC equipment for unmatched precision.
- Comprehensive Solutions: From prototyping to production, we cover every aspect of medical component manufacturing.
- Collaborative Approach: We work closely with clients to deliver tailored solutions that meet unique specifications.
FUJlU Medical Injection Mold stands at the forefront of medical precision machining, delivering reliable, high-quality components that contribute to life-saving medical advancements.
FAQs about Medical Precision Machining Factories
CNC (Computer Numerical Control) in the medical field refers to the use of computerized machinery to manufacture precision components for medical devices. CNC technology allows for the automation of machining processes, resulting in consistent and highly accurate parts. In medical applications, CNC machines are used to create implants, surgical tools, diagnostic equipment, and other essential healthcare components. The high precision and repeatability of CNC machining are critical in ensuring the safety and efficacy of these devices. For example, a CNC machine can mill or turn titanium orthopedic implants with exact specifications, ensuring they fit perfectly and perform reliably in a patient’s body. Furthermore, CNC systems can process biocompatible materials, such as stainless steel or PEEK, into complex shapes with tight tolerances. The role of CNC in the medical industry is indispensable, as it helps meet stringent quality standards while enabling innovative advancements in healthcare technology.
CNC machining is widely used to manufacture a range of surgical instruments essential for modern healthcare. Precision surgical tools like scalpels, forceps, clamps, and surgical scissors are commonly made using CNC processes, ensuring consistent quality and sharpness. More complex instruments, such as bone saws, surgical drills, and robotic-assisted surgical tools, are also produced with CNC machining due to its ability to handle intricate designs and tight tolerances. Stainless steel is the most commonly used material, given its strength, durability, and ability to be sterilized repeatedly. CNC machining also allows for the production of custom surgical tools tailored to specific procedures or patient needs. In minimally invasive surgeries, CNC machining is critical for creating miniature instruments and components, such as laparoscopic forceps or micro-drill bits, that require exceptional precision. Overall, CNC technology ensures that surgical instruments meet rigorous standards for performance, reliability, and safety.
CNC and precision machining involve the use of advanced technologies to manufacture high-accuracy components with tight tolerances. CNC (Computer Numerical Control) machining refers to the automated control of machining tools such as lathes, mills, and grinders through computer programming. Precision machining focuses on achieving exceptional detail and consistency in the final product. Together, CNC and precision machining are vital in industries that demand high-quality components, such as aerospace, automotive, and especially healthcare. In the medical field, CNC and precision machining are used to create complex parts like implants, surgical instruments, and diagnostic equipment. These processes allow manufacturers to work with various biocompatible materials, including metals like titanium and plastics like PEEK. The accuracy and repeatability of CNC and precision machining ensure that parts meet strict regulatory and performance standards. By combining cutting-edge technology with skilled engineering, CNC and precision machining enable the production of life-saving medical devices with unparalleled reliability.
CNC, or Computer Numerical Control, in the medical industry refers to the use of automated machining processes to create medical devices, implants, and surgical tools. These machines are controlled by pre-programmed software that dictates their movements with extreme precision. CNC machining is essential in the healthcare sector for manufacturing components with intricate designs and high accuracy, such as orthopedic implants, dental crowns, and custom prosthetics. Materials like titanium, stainless steel, and biocompatible plastics are often used, ensuring durability and compatibility with the human body. CNC technology allows for rapid prototyping and production of highly specialized tools tailored to patient-specific needs, contributing to better outcomes and advancements in medical science.
In hospitals, CNC processes are indirectly involved in patient care by providing precisely manufactured medical devices, implants, and instruments. While CNC machines themselves are not typically found in hospitals, the products created using CNC machining are indispensable in modern healthcare. Examples include custom surgical guides, bone plates, stents, and diagnostic equipment components. Some hospitals collaborate with specialized manufacturers to create patient-specific devices, like prosthetics or implants, ensuring they meet the precise anatomical requirements of each patient. This collaboration enhances surgical precision, reduces recovery time, and improves overall patient outcomes.
In the pharmaceutical industry, CNC technology plays a critical role in manufacturing high-precision equipment used for drug production and delivery systems. CNC machining is used to create parts for capsule fillers, tablet presses, and sterile drug manufacturing systems. Precision is paramount in pharma to maintain stringent quality and safety standards. CNC is also employed in producing medical-grade molds for syringes, vials, and other packaging materials that meet regulatory requirements. Additionally, CNC machining ensures the scalability of production processes, which is vital for large-scale pharmaceutical manufacturing.
In the context of the human body, CNC machining relates to the creation of medical implants and devices designed to interact seamlessly with biological tissues. Examples include dental implants, artificial joints, spinal implants, and cranial plates. These components are manufactured using CNC machining to achieve precise shapes and dimensions, ensuring proper fit and function. Materials used for such applications are biocompatible and often include titanium alloys or cobalt-chromium. CNC technology allows for customization based on individual anatomy, enhancing comfort, performance, and long-term success.
An RN CNC is a Registered Nurse who has earned a Certified Nurse Credentialing (CNC) designation. This certification signifies expertise in a specialized area of nursing, such as oncology, orthopedics, or critical care. Earning the CNC credential involves meeting rigorous education and practice requirements, often accompanied by passing a certification exam. This qualification demonstrates a nurse’s advanced knowledge and commitment to professional excellence, ensuring they deliver high-quality, specialized care in their field.
CNC certification in the medical context refers to a credential that validates a healthcare professional’s expertise in a specific area of care. For nurses, CNC certification signifies advanced clinical skills and knowledge, demonstrating the ability to provide specialized care. For machinists in the medical industry, CNC certification represents proficiency in operating computer numerical control machines to produce precision medical components. Both types of certification highlight a commitment to excellence and adherence to industry standards, ensuring safety and quality.
In the medical field, CNC as a title often stands for Certified Nurse Credentialed. It signifies that the nurse has specialized training and certification in a particular area of care, such as case management, critical care, or oncology. This title ensures the nurse’s expertise and dedication to maintaining high standards of patient care, often involving additional education, clinical experience, and passing a certification exam. It underscores professionalism and advanced competency.
In healthcare, CNC qualifications include expertise in either the operation of precision CNC machines for medical manufacturing or certification in specialized nursing. For machinists, CNC involves mastery of software and hardware that produce accurate medical devices. For nurses, CNC involves meeting specific certification criteria, such as advanced education and clinical practice hours, demonstrating specialized skills in patient care. Both applications ensure precision, safety, and quality in their respective fields.
The highest accuracy machining in the medical industry involves ultra-precision CNC machining, achieving tolerances as tight as ±0.001 mm. This level of accuracy is essential for producing components like micro-surgical tools, dental implants, and prosthetics. Advanced CNC machines, combined with high-precision measurement systems like Coordinate Measuring Machines (CMMs), enable consistent production of highly detailed and accurate medical components critical for patient safety and performance.
The most accurate CNC machines used in the medical industry are multi-axis machining centers equipped with advanced control systems. Brands and machines capable of achieving sub-micron tolerances are considered industry leaders. These machines use high-resolution feedback systems, thermal compensation, and specialized cutting tools to ensure precision. Their accuracy makes them ideal for producing intricate components like heart valves, stents, and orthopedic screws.
The world’s most accurate Coordinate Measuring Machine (CMM) is used extensively in medical manufacturing for verifying the precision of complex components like implants, surgical tools, and diagnostic devices. Machines like those from Zeiss or Hexagon offer nanometer-level accuracy, ensuring the highest tolerances are met. These CMMs utilize advanced sensors, software, and temperature compensation to ensure reliability. In the medical field, their accuracy ensures that life-critical devices meet stringent standards for safety, compatibility, and performance. These machines are indispensable for quality control in the production of medical components requiring extreme precision.
In medical manufacturing, the top accuracy metric is typically tolerance, measured in microns (µm). For precision CNC machining, tolerances of ±0.001 mm or tighter are standard. This metric is crucial for ensuring the fit and functionality of medical devices, such as orthopedic implants, which must seamlessly integrate with the human body. The tolerance metric reflects the allowable deviation from design specifications, directly influencing device safety and efficacy. High-accuracy metrics are critical in medical applications where even the smallest error can lead to complications or device failure.
The smallest machining tolerance achievable in the medical field is in the range of ±0.0001 mm (0.1 µm), achieved using ultra-precision CNC machining and advanced equipment. This level of tolerance is critical for applications like micro-surgical instruments, dental implants, and cardiovascular stents, where even minute discrepancies can affect performance. Achieving such tolerances requires high-end machinery, stringent environmental controls, and advanced metrology techniques to verify precision. This ensures that the devices meet the strict quality requirements demanded by the medical industry.
The highest tolerance CNC machines, often used in medical manufacturing, can achieve tolerances as tight as ±0.001 mm or better. These machines are designed to produce high-precision components like surgical implants, prosthetics, and robotic-assisted surgical tools. Factors such as multi-axis capabilities, thermal stability, and advanced software contribute to their performance. In the medical field, these machines ensure that devices meet stringent regulatory standards and provide reliable outcomes for patients, minimizing risks associated with inaccuracies.
CNC machining in the medical industry is highly accurate, with tolerances commonly ranging from ±0.01 mm to ±0.001 mm. The accuracy depends on factors such as machine type, material, and design complexity. For example, producing orthopedic implants requires extreme precision to ensure proper anatomical fit and biomechanical performance. Advanced CNC machines with multi-axis capabilities, combined with real-time quality checks, help achieve this accuracy. In medical applications, precision directly impacts patient safety and device reliability, making CNC machining an essential technology.
In precision machining for the medical industry, tolerances typically range from ±0.01 mm to ±0.001 mm, depending on the application. For critical components like surgical instruments and implants, tighter tolerances of ±0.0001 mm may be required. These tolerances ensure that parts fit together perfectly and perform reliably under medical conditions. Meeting such stringent tolerances requires advanced CNC machines, rigorous quality control, and specialized tools. Maintaining precise tolerances is critical for patient safety and regulatory compliance in healthcare.
Ultra-precision CNC machining is the most accurate process for manufacturing medical components. Compared to other methods like injection molding or casting, CNC machining offers superior dimensional accuracy, surface finish, and repeatability. Processes like electrical discharge machining (EDM) are also highly accurate and are often used for intricate parts like stents or surgical tools. The choice of machining process depends on the material, design complexity, and required tolerances. For medical applications, accuracy is paramount, and CNC machining ensures the highest standards of quality and performance.
Precision machining is challenging due to the high level of skill, technology, and attention to detail required. In the medical industry, the complexity increases because components must meet strict tolerances, biocompatibility standards, and regulatory requirements. Factors like thermal stability, tool wear, and machine calibration must be carefully managed to achieve the desired precision. Additionally, medical devices often involve complex geometries and materials like titanium or ceramics, which are difficult to machine. Despite these challenges, advancements in CNC technology have made it possible to produce highly accurate medical components efficiently and reliably.
Contact our professional team now for a same-day quote and risk-free project evaluation. Benefit from ISO 8 cleanrooms, advanced machines, and 12-hour fast response in medical injection molding.