Medical injection molding polymer is a critical material used in the production of medical devices, offering precision, reliability, and scalability. These polymers are specifically designed to meet the stringent requirements of the healthcare industry, ensuring that devices are safe, durable, and compliant with regulatory standards. The use of medical injection molding polymers allows for the creation of complex shapes and intricate designs, which are essential in producing medical components like surgical instruments, drug delivery devices, and diagnostic tools. One of the key benefits of using these polymers is their ability to provide consistency and high-performance characteristics, ensuring that medical devices maintain quality and functionality throughout their lifecycle. The versatility and efficiency of medical injection molding polymers make them a top choice for plastic medical device manufacturers worldwide. Medical injection molding polymer types like polypropylene, polyethylene, and PEEK ensure precision, biocompatibility, and durability for medical devices.
Low-Volume to High-Volume Production Capabilities
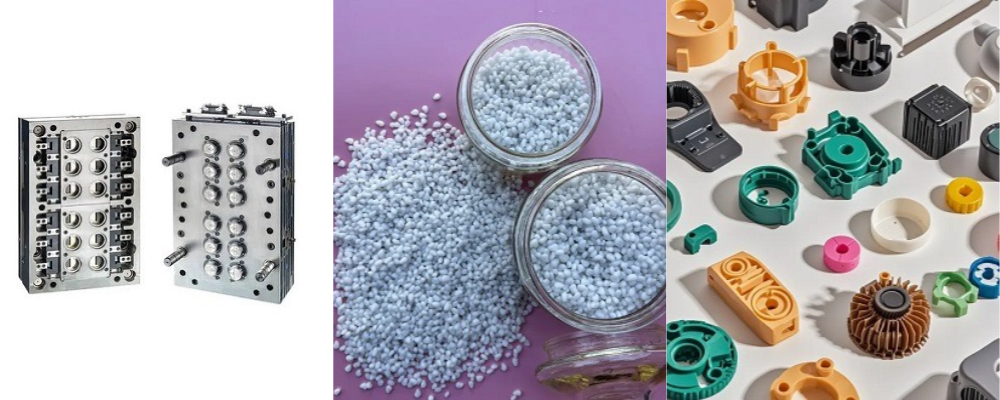
Attributes | Details |
---|---|
Place of Origin | Dongguan, Guangdong, China |
Brand Name | LY Medical Injection Mold |
Product Name | Medical Injection Molding |
Molding Mode | Plastic Injection Mold |
Product Material | Plastic |
Surface Treatment | Custom Surface Texture |
Features | High Precision, Environmentally Friendly, Durable |
Color | Customized |
Size | Customized |
Length | Customized |
Service | OEM ODM |
Processing Service | Molding, Cutting |
Logo | Customized Logo Acceptable |
Mould Life | 300000~1000000shots |
Application | Medical Grade |
Minimum Order Quantity | Small Order Accepted |
Packing Details | Outer Packaging Carton Inner Packaging According to Customer Requirement |
Port | According to Your Requirement |
Medical Injection Molding Polymer and Injection Molding Medical Polymers
Injection molding medical polymers are high-performance materials specifically designed for the manufacturing of medical devices through the medical injection molding process. These polymers are chosen for their ability to provide excellent mechanical properties, durability, and biocompatibility, all of which are essential in healthcare product production. The use of medical injection molding polymers ensures that devices meet stringent regulatory requirements while maintaining the high quality necessary for safe patient care.
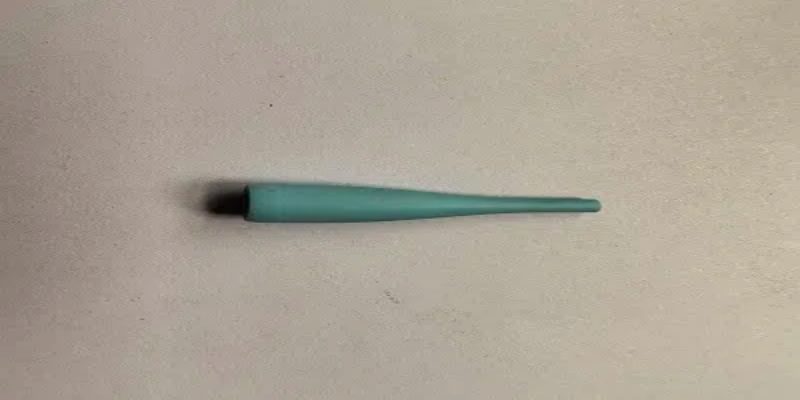
Types of Polymers Commonly Used in Medical Injection Molding
In medical injection molding, the choice of polymer is critical to the success of the medical device, as it impacts the device’s performance, durability, and safety. Several types of polymers are commonly used, each offering unique properties suited to different applications in the medical field. Below is a comprehensive overview of the most widely used polymers in medical injection molding, detailing their specific benefits and typical uses.
Polypropylene (PP)
Polypropylene is a widely used polymer in the medical industry, known for its strength, chemical resistance, and low cost. It is particularly favored for disposable medical devices due to its durability and ease of processing.
- Properties: Polypropylene has excellent resistance to chemicals, moisture, and heat, making it suitable for sterilization processes like autoclaving. It is also lightweight and has a relatively low cost, which makes it ideal for mass production.
- Applications: Polypropylene is commonly used for medical packaging, syringes, diagnostic tools, and surgical instruments. Its use in medical packaging ensures the safety and sterility of medical supplies.
Polyethylene (PE)
Polyethylene is one of the most versatile and commonly used polymers in medical applications. It has high impact resistance, flexibility, and a low coefficient of friction, which makes it a preferred choice for many medical devices.
- Properties: Polyethylene is known for its excellent impact resistance, toughness, and flexibility, making it suitable for medical devices that need to endure mechanical stresses. It is also resistant to chemicals and moisture, ensuring the longevity and safety of medical devices.
- Applications: Polyethylene is commonly used in medical tubing, prosthetic components, and containers. Its flexibility makes it ideal for tubing used in intravenous lines and catheters, as well as in prosthetics, where a combination of strength and flexibility is crucial.
Silicone Elastomers
Silicone elastomers are highly biocompatible, flexible, and durable, which makes them ideal for medical devices that need to maintain their shape and functionality in complex and dynamic environments.
- Properties: Silicone is known for its exceptional flexibility, elasticity, and resistance to high and low temperatures. It is also chemically inert, which ensures it does not react with body fluids, making it an ideal material for long-term implantation or contact with the body.
- Applications: Silicone elastomers are used in medical gloves, seals, gaskets, and catheters. Its stretchability and softness make it a preferred material for devices that need to bend and stretch without losing functionality. Additionally, silicone is used in implants and pacemaker components due to its biocompatibility.
Polyetheretherketone (PEEK)
Polyetheretherketone (PEEK) is a high-performance thermoplastic polymer used in applications where high temperature, mechanical strength, and resistance to wear are crucial.
- Properties: PEEK has excellent mechanical properties, including high tensile strength, stiffness, and resistance to wear. It also performs well under extreme temperatures and in environments that expose it to harsh chemicals. PEEK is biocompatible and is one of the few polymers that can be sterilized with autoclaving or gamma radiation.
- Applications: PEEK is commonly used for surgical instruments, spinal implants, and orthopedic devices. Its high strength and biocompatibility make it a preferred material for implantable devices and components exposed to high mechanical stresses.
Polystyrene (PS)
Polystyrene is a rigid, clear polymer often used in medical device applications where transparency is required. It is economical, easy to mold, and offers a broad range of applications in the medical field.
- Properties: Polystyrene is a relatively low-cost material with good clarity, making it useful for medical applications requiring visual inspection of contents. It is also resistant to environmental stress cracking and performs well under sterilization processes.
- Applications: Polystyrene is commonly used in laboratory containers, petri dishes, diagnostic trays, and packaging materials. Its clarity allows for easy inspection of samples, making it ideal for diagnostic kits and laboratory tools.
Polyvinyl Chloride (PVC)
Polyvinyl chloride (PVC) is a highly versatile material used in a range of medical applications. It is available in both rigid and flexible forms, making it adaptable to a variety of device requirements.
- Properties: PVC is durable, resistant to environmental stress cracking, and can be easily processed into flexible or rigid forms. Flexible PVC can be made soft through the use of plasticizers, while rigid PVC offers high strength and dimensional stability.
- Applications: Flexible PVC is commonly used in medical tubing, blood bags, and intravenous catheters, while rigid PVC is used in medical device housings, such as in oxygen masks and diagnostic equipment. Its flexibility and ease of processing make it ideal for a wide variety of medical devices.
Acrylonitrile Butadiene Styrene (ABS)
Acrylonitrile Butadiene Styrene (ABS) is a tough, impact-resistant plastic commonly used in applications that require strength, rigidity, and high performance under stress.
- Properties: ABS offers excellent impact resistance, dimensional stability, and high tensile strength. It is also easy to mold and can be used in high-temperature applications. ABS is resistant to chemicals and provides a good surface finish for medical devices.
- Applications: ABS is used in the production of durable medical devices like housings for diagnostic equipment, surgical instruments, and medical electronics. Its impact resistance and ease of molding make it suitable for devices that need to withstand mechanical stresses.
Polyamide (Nylon)
Polyamide, or nylon, is a group of thermoplastics known for their excellent mechanical properties, including strength, toughness, and flexibility.
- Properties: Nylon is highly durable, offering good abrasion resistance and high tensile strength. It is also resistant to chemicals, making it suitable for a variety of medical device applications. Nylon can be molded into complex shapes and offers excellent wear resistance.
- Applications: Nylon is used in surgical instruments, orthopedic devices, and medical device housings. Its high strength and durability make it ideal for devices that undergo frequent use or require enhanced mechanical performance.
Polycarbonate (PC)
Polycarbonate is a durable and transparent polymer with excellent impact resistance and optical clarity, making it ideal for devices requiring both strength and visibility.
- Properties: Polycarbonate is highly resistant to impact, scratches, and high temperatures. It also offers superior clarity, which is useful for applications where visual inspection or transparency is critical.
- Applications: Polycarbonate is commonly used for medical device housings, diagnostic equipment, and transparent medical packaging. It is ideal for applications that require high strength and clarity, such as in protective covers and diagnostic trays.
How These Polymers Meet Regulatory and Safety Standards for Medical Devices
Medical injection molding polymers must meet stringent regulatory and safety standards to ensure the devices produced are safe for use. These standards include compliance with ISO 13485, FDA regulations, and other international guidelines. Some key factors include:
- Biocompatibility: Ensures the polymer will not cause adverse reactions when in contact with the human body.
- Sterilization Resistance: Many medical devices need to withstand sterilization processes without degrading, which requires polymers with high resistance to heat and chemicals.
- Mechanical Performance: The polymers must provide sufficient strength, durability, and flexibility to ensure the device functions effectively throughout its lifecycle.
- Regulatory Approval: Compliance with standards set by regulatory bodies like the FDA ensures that the polymers used are safe for medical applications.
Applications in the Production of Medical Components and Devices
Medical injection molding polymers are used in a wide range of medical components and devices due to their versatility and reliability. Some common applications include:
- Surgical Instruments: Polymer materials are used in the creation of handles, casings, and other parts of surgical instruments that need to be sterile, durable, and ergonomic.
- Implants: Biocompatible polymers like PEEK are used in implants due to their strength and ability to withstand the physiological environment of the human body.
- Diagnostic Devices: From blood collection tubes to diagnostic kits, medical injection molding polymers help produce precise and functional components.
- Drug Delivery Devices: Polymers are used to make reliable and efficient drug delivery devices, such as injectors and inhalers, ensuring they meet regulatory standards and function as intended.
These medical injection molding polymers are indispensable in the medical device plastic manufacturing that require a high degree of safety, functionality, and precision. The ability of these polymers to meet regulatory and safety standards makes them the material of choice in the healthcare industry.
Factors Affecting the Selection of Medical Injection Molding Polymer Materials
The selection of medical injection molding polymers is a crucial aspect of medical device manufacturing, as it directly impacts the performance, safety, and effectiveness of the final product. Various factors must be considered to ensure the right polymer is chosen to meet both regulatory requirements and end-user needs. Key factors influencing material selection include biocompatibility, sterilization compatibility, mechanical properties, chemical resistance, aesthetics, and usability. Each of these factors plays an important role in ensuring that medical devices are both functional and safe. Below, we delve into these factors and how they guide the material selection process for medical injection molding polymers.
Biocompatibility and Sterilization Requirements
Biocompatibility and sterilization compatibility are fundamental considerations when selecting materials for medical devices, as they ensure the safety and hygiene of the product.
- Biocompatibility: Medical devices often come in direct contact with living tissues or body fluids, making biocompatibility a top priority. Materials must not induce adverse reactions, such as toxicity or irritation. Regulatory standards such as ISO 10993 define the tests required to assess the biocompatibility of materials used in medical devices.
- Sterilization Compatibility: Medical devices are subject to various sterilization processes, including autoclaving, gamma radiation, and chemical sterilization. The materials chosen must withstand these processes without degrading, losing strength, or becoming contaminated. High heat resistance and chemical stability are key characteristics to consider in this context.
Mechanical Properties and Chemical Resistance
The mechanical properties and chemical resistance of medical injection molding polymers are essential for ensuring the durability and functionality of medical devices.
- Mechanical Properties: Several mechanical properties must be evaluated when choosing a polymer, including hardness, flexibility, stiffness, and weight. Hardness determines a material’s resistance to indentation, while flexibility and stiffness assess how a material bends under pressure. Weight is an important factor for wearable devices, influencing comfort and portability.
- Chemical Resistance: Medical devices frequently come into contact with body fluids, cleaning agents, and disinfectants. A material’s ability to resist chemical degradation is vital for the longevity and performance of medical devices. Medical polymers must be resistant to common chemicals, including alcohol, solvents, and detergents, to ensure they maintain their integrity over time.
Aesthetics and Usability Issues
Aesthetics and usability are significant factors in the design of medical devices, especially those intended for long-term use or those visible to patients. Materials must be not only functional but also comfortable and appealing to enhance the overall user experience.
- Aesthetics: For prostheses or other visible devices, a material’s appearance is crucial. Polymers like polycarbonate can be colored, allowing for aesthetically pleasing devices that match the patient’s skin tone or specific design requirements.
- Usability: The usability of a device influences patient acceptance. Comfort, ease of operation, and ergonomic design are key considerations. Silicone, for example, is commonly used in wearable medical devices due to its flexibility and comfort against the skin. The design flexibility offered by plastic mold technology allows for complex and user-friendly designs that improve the overall experience for patients.
Durability and Long-Term Performance
Durability and long-term performance are crucial considerations when selecting a medical injection molding polymer, as medical devices are expected to perform reliably for extended periods.
- Wear Resistance: Medical devices, particularly those used in high-traffic or active areas, must exhibit wear resistance to withstand daily use without compromising functionality.
- Long-Term Stability: Polymers chosen for medical devices should retain their mechanical properties and performance over extended periods. Stability against temperature fluctuations, humidity, and other environmental factors ensures long-lasting performance.
Cost-Effectiveness and Regulatory Compliance
While performance and safety are critical, cost-effectiveness and regulatory compliance also play significant roles in material selection.
- Cost-Effectiveness: Medical device manufacturers must balance the cost of materials with the final product’s performance requirements. Economically feasible polymer choices that do not compromise quality help reduce production costs.
- Regulatory Compliance: Medical-grade polymers must meet regulatory standards such as ISO 13485 for quality management systems and the FDA’s medical device regulations. These certifications ensure that the material and manufacturing process align with the medical industry’s strict guidelines.
The process of selecting medical injection molding polymers involves a careful evaluation of these factors to ensure the final product is both safe and effective. By considering biocompatibility, mechanical properties, sterilization compatibility, aesthetics, and regulatory compliance, manufacturers can make informed choices that lead to the production of high-quality medical devices.
What Is Medical Injection Molding Polymer Price
The price of medical injection molding polymer varies depending on several factors. Medical device manufacturers must carefully consider these factors to determine their material costs and optimize their production budgets. Understanding these influences can help companies make informed decisions regarding material selection and manufacturing methods.
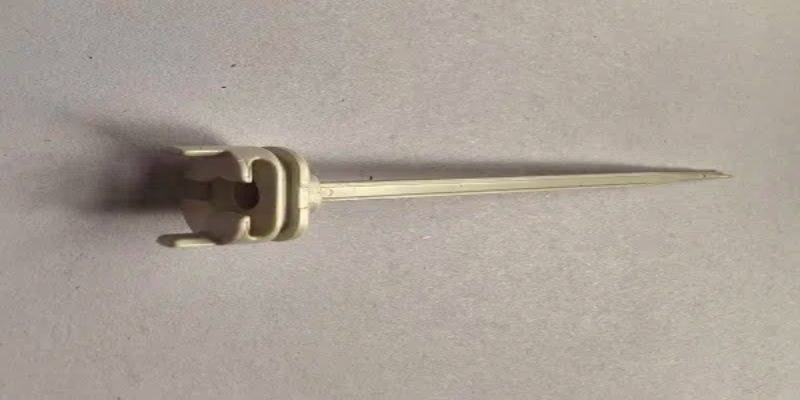
Factors Influencing the Price of Medical Injection Molding Polymers
The cost of medical injection molding polymer is primarily influenced by:
- Material Type: Different polymers come with varying costs based on their properties, such as biocompatibility, strength, flexibility, and sterilization resistance. High-performance polymers like PEEK are generally more expensive than standard materials like polyethylene.
- Polymer Grade: Medical-grade polymers typically cost more than industrial-grade materials due to the strict regulatory and quality control standards they must meet.
- Production Volume: Larger production runs tend to lower the per-unit cost of materials. This is because the cost of molding equipment and setup is spread over a greater number of units, making it more cost-effective for manufacturers.
- Customization and Additives: Custom formulations or the inclusion of specific additives, such as antimicrobial agents or colorants, can increase the price of the polymer.
How Volume, Material Type, and Complexity Affect Pricing
The price of medical injection molding polymer is directly impacted by:
- Production Volume: High-volume production allows manufacturers to reduce costs per unit due to economies of scale. Small batches, on the other hand, usually incur higher material and setup costs.
- Material Type: The choice of polymer significantly affects price. Standard polymers like polypropylene may be less expensive than advanced options like silicone elastomers, which offer superior biocompatibility and flexibility.
- Design Complexity: The complexity of the design also influences the cost. Devices with intricate geometries or tight tolerances require more advanced molding techniques, which can increase both material and labor costs.
- Processing Requirements: Some medical polymers require specific molding conditions (e.g., high-temperature molding) or additional processing steps, which can further drive up the cost of production.
Budget Considerations for Medical Device Manufacturers
When budgeting for medical injection molding polymer, manufacturers must account for:
- Material Selection: Choosing the right polymer that balances cost and performance is key. While high-performance polymers offer superior qualities, they come with higher upfront costs.
- Tooling and Setup Costs: Injection molding requires molds, which can be expensive, particularly for custom designs. These costs must be factored into the overall budget.
- Volume of Production: Determining whether high-volume production is feasible will help in estimating per-unit costs. Smaller production runs can increase costs due to setup and lower material efficiency.
- Regulatory Compliance: The cost of meeting medical device standards, such as FDA approval or ISO certification, may require additional testing and validation, impacting the overall budget.
By understanding the factors that influence the price of medical injection molding polymer, manufacturers can make informed decisions that optimize costs while meeting the necessary standards for safety and quality.
Medical Injection Molding Polymer and Poly Molding Equipment Medical Devices: The Technology Behind Medical Molding
Poly molding equipment is a critical component in the production of medical devices, allowing manufacturers to create high-quality, complex, and precise parts with medical injection molding polymers. This equipment is designed to handle the unique requirements of medical device production, ensuring that each part meets stringent safety and performance standards. The use of advanced molding equipment in combination with medical injection molding polymers results in devices that are not only functional but also durable and biocompatible, making them suitable for a wide range of medical applications.
Introduction to Poly Molding Equipment Used in Medical Device Production
Poly molding equipment plays a vital role in the manufacturing process of medical devices. These machines are designed to process various types of medical injection molding polymers, shaping them into the final products required by the healthcare industry. Poly molding equipment includes machines that handle everything from the injection process to the cooling and ejection of molded components. The precision and automation of this equipment are essential in ensuring that the final products meet the exacting standards required for medical devices.
How Poly Molding Equipment Contributes to the Manufacturing Process
Poly molding equipment significantly enhances the manufacturing process by enabling:
- Efficiency: High-speed production capabilities that reduce cycle times, allowing for faster output and increased production capacity.
- Precision: Automated systems and precise injection mechanisms ensure that each part meets the exact tolerances required for medical devices.
- Consistency: Reproducibility of the molding process ensures that each component produced is identical to the previous one, which is critical for medical device reliability.
- Cost Reduction: Automation and high-volume capabilities reduce labor costs and waste, making production more cost-effective.
These factors ensure that poly molding equipment is indispensable in the medical molding process, helping manufacturers produce high-quality parts efficiently.
Types of Equipment Used, Such as Injection Molding Machines, Molds, and Automated Systems
Several types of poly molding equipment are used in the production of medical devices, each contributing to different stages of the molding process:
- Injection Molding Machines: These machines inject the medical injection molding polymer into molds to create the desired shapes. They are equipped with precise temperature and pressure control systems to ensure the polymer flows smoothly and solidifies correctly.
- Molds: Custom medical molds are created to produce specific medical components, such as surgical instruments, diagnostic devices, or packaging. The molds must be carefully designed to accommodate the desired geometry and functionality of the device.
- Automated Systems: Automation is used to handle material feeding, part removal, and post-molding operations, ensuring efficiency and consistency across production runs. These systems can also integrate quality control measures, such as automated inspections.
These pieces of equipment work together seamlessly to create medical devices from medical injection molding polymers, ensuring high efficiency and precision in manufacturing.
The Role of Poly Molding Equipment in Ensuring the Precision and Quality of Medical Devices
Poly molding equipment is essential in ensuring that medical devices meet the required standards of precision and quality. The role of this equipment includes:
- Precision Manufacturing: The equipment is designed to produce components with extremely tight tolerances, which is crucial for devices like implants or surgical instruments that must function correctly under various conditions.
- Material Handling: Poly molding machines ensure that medical injection molding polymer is processed efficiently, maintaining the integrity and properties of the material throughout the molding process.
- Regulatory Compliance: Equipment is designed to meet industry standards and regulatory requirements, such as ISO 13485 and FDA regulations, ensuring that the final products are safe for use in medical applications.
- Customization: Poly molding equipment allows for customization of parts to meet specific medical needs, including multi-component parts, specialized textures, and unique geometries.
By incorporating advanced molding technologies, manufacturers can ensure the high-quality production of medical devices, reducing the risk of defects and enhancing patient safety. The use of poly molding equipment in conjunction with medical injection molding polymers allows for the creation of reliable, functional, and compliant medical components.
Medical Injection Molding Polymer: The Role of Medical Molding in Healthcare Device Production
Medical molding, specifically through the use of medical injection molding polymer, is a cornerstone of modern healthcare device manufacturing. The injection molding process allows manufacturers to produce high-precision, complex, and high-volume components required for medical devices. By utilizing advanced polymers designed for medical injection molding applications, this process ensures the consistent production of reliable and biocompatible parts.
Explanation of the Medical Molding Process
The medical molding process involves the use of medical injection molding polymer to create components by injecting molten polymer into a mold cavity. The process can be broken down into several key stages:
- Polymer Selection: The choice of polymer is critical to ensure that the final product meets the necessary properties, such as strength, biocompatibility, and flexibility.
- Molding: Once the polymer is selected, it is heated and injected into a mold under high pressure. The mold shapes the polymer into the desired form.
- Cooling: After the polymer is injected into the mold, it is cooled to solidify the material and take the shape of the mold cavity.
- Ejection: The final component is ejected from the mold, typically through an automated system, and undergoes post-molding processes like cleaning and inspection.
This process allows for high-precision manufacturing and the ability to produce complex designs, which are essential for medical devices that require intricate details and exact dimensions.
Types of Medical Devices Made Through Injection Molding
Medical injection molding polymer is used in the production of a wide range of medical devices, including:
- Surgical Instruments: These devices, including handles, grips, and functional components, require high precision and durability. Polymers like polypropylene or silicone are commonly used in the production of surgical tools that need to be sterilized or endure repeated use.
- Diagnostic Devices: Components such as diagnostic test kits, blood collection tubes, and sample containers are made using medical injection molding polymer to ensure accuracy and reliability in the diagnostic process.
- Drug Delivery Systems: Inhalers, syringes, and insulin pens are commonly produced using medical molding techniques. These devices require biocompatible polymers that can withstand frequent use and maintain the integrity of the delivered medication.
- Implants and Prosthetics: Medical polymers like PEEK and silicone elastomers are used to produce implants and prosthetic components due to their strength, flexibility, and biocompatibility.
Benefits of Using Injection Molded Components in Medical Device Manufacturing
Using medical injection molding polymer for producing medical device components offers several advantages:
- Precision and Accuracy: Injection molding allows for the production of highly precise parts, which is critical for the performance and safety of medical devices.
- High Throughput and Efficiency: Once the mold is created, the injection molding process can produce a large number of parts quickly, making it ideal for high-volume production runs.
- Cost-Effectiveness: While the initial tooling cost for precision medical molds can be high, the ability to mass-produce components at low per-unit costs makes injection molding an economically efficient method for manufacturing medical devices.
- Material Versatility: Medical injection molding polymers offer a wide range of material properties, from flexible elastomers for seals to rigid polymers for structural components. This versatility allows manufacturers to choose the most suitable material for each device.
- Consistency and Quality Control: Injection molding ensures that each part is identical in quality and functionality, which is essential for medical devices that must meet rigorous regulatory standards and safety requirements.
Through these advantages, the use of medical injection molding polymer has revolutionized the production of medical devices, ensuring the creation of safe, reliable, and high-performance products that meet the needs of both healthcare providers and patients.
7 Technologies for Medical Device Injection Molding Using Medical Injection Molding Polymer
Medical device manufacturing relies heavily on advanced injection molding technologies to meet stringent precision, durability, and safety requirements. Using medical injection molding polymer, manufacturers can produce components tailored to specific medical applications. Each molding technique offers unique advantages and applications. This detailed guide explains seven key injection molding technologies and their roles in medical device production.
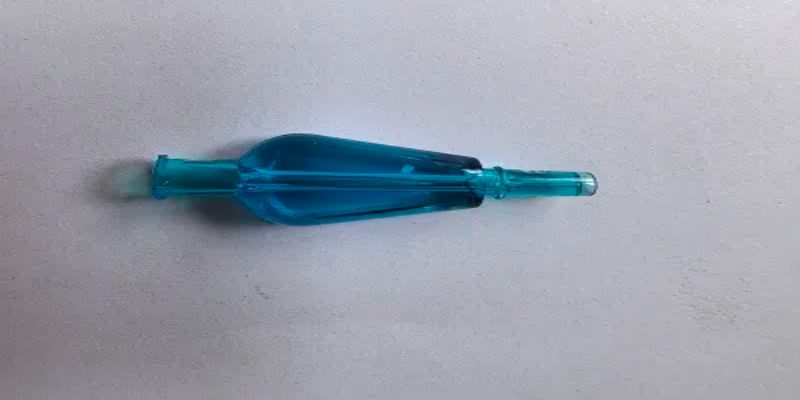
Traditional Plastic Injection Molding
Traditional plastic injection molding is the foundation of medical device manufacturing.
- Overview: This process involves heating medical injection molding polymers until molten and injecting them into precision-engineered molds under high pressure.
- Applications: It is ideal for producing components such as syringes, connectors, and housings for medical devices.
- Advantages: Offers high repeatability, cost-effectiveness for large volumes, and compatibility with a wide range of medical-grade polymers like polyethylene and polycarbonate.
Thin-Wall Injection Molding
Thin-wall injection molding specializes in producing lightweight, high-strength components with thin profiles.
- Overview: This technology focuses on creating thin-walled parts by optimizing polymer flow and cooling systems during injection.
- Applications: Commonly used for disposable medical products like syringes, packaging, and test kits.
- Advantages: Reduces material usage, improves production speed, and enhances product portability without compromising durability.
Gas-Assisted Injection Molding
Gas-assisted injection molding incorporates pressurized gas to enhance part design and functionality.
- Overview: In this method, gas is injected into the polymer-filled mold to hollow out sections, reducing material use and cycle time.
- Applications: Suitable for large, complex components like medical equipment enclosures or ergonomic handles.
- Advantages: Minimizes weight, reduces warping, and ensures uniform wall thickness for enhanced aesthetics and performance.
Secondary Molding
Secondary molding, also known as overmolding, is used to combine multiple materials into a single component.
- Overview: This process involves injecting a secondary polymer over or around a pre-molded part, often of a different material.
- Applications: Ideal for creating multi-material components, such as medical devices with soft-touch grips or seals.
- Advantages: Enhances product functionality and design while reducing the need for assembly.
LSR Injection Molding
Liquid Silicone Rubber (LSR) injection molding is a specialized technique for creating flexible, biocompatible components.
- Overview: LSR is injected into molds to create elastic parts with superior chemical resistance and durability.
- Applications: Commonly used for implants, seals, and wearable medical devices.
- Advantages: Provides excellent biocompatibility, heat resistance, and adaptability for intricate designs.
HCR Injection Molding
High-Consistency Rubber (HCR) injection molding focuses on producing durable rubber components.
- Overview: This process uses high-viscosity silicone materials to create parts requiring excellent tensile strength and flexibility.
- Applications: Often employed for medical tubing, gaskets, and diaphragms.
- Advantages: Offers enhanced tear resistance and reliable performance in demanding medical environments.
Metal Injection Molding (MIM)
Metal injection molding allows for the creation of high-strength, miniature metallic components.
- Overview: Fine metal powders are mixed with a polymer binder, injected into molds, and sintered to form solid metal parts.
- Applications: Suitable for surgical instruments, dental devices, and components requiring superior strength and durability.
- Advantages: Combines the precision of injection molding with the strength of metal, enabling complex geometries and small-scale production.
By leveraging these seven technologies, manufacturers can optimize the use of medical injection molding polymers to produce innovative, high-quality medical devices that meet diverse industry needs. Each method addresses specific challenges, ensuring versatility and reliability in medical manufacturing.
Requirements for Manufacturers Using Medical Injection Molding Polymer
Manufacturers using medical injection molding polymer must adhere to strict industry standards and possess specialized equipment to ensure safety, precision, and compliance. This includes obtaining the necessary certifications, maintaining cleanroom environments, and utilizing advanced injection molding machines. Each aspect is critical to producing high-quality medical devices that meet regulatory and patient safety requirements. This guide provides an in-depth exploration of these conditions.
Essential Industry Certifications
Medical injection molding requires manufacturers to meet stringent certification standards that demonstrate adherence to quality, safety, and regulatory compliance.
- ISO 13485 Certification: This certification focuses on quality management systems specific to medical devices, ensuring that manufacturing processes meet regulatory requirements.
- FDA Registration and Compliance: Manufacturers must register with the FDA and adhere to its guidelines for medical device production.
- ISO 10993 Testing Compliance: Materials, including medical injection molding polymers, must pass biocompatibility tests under ISO 10993 to ensure they are safe for medical applications.
- GMP Compliance: Good Manufacturing Practices (GMP) certification ensures that facilities maintain cleanliness, documentation, and quality throughout production.
Cleanroom Environment Requirements
A controlled cleanroom environment is essential for manufacturing with medical injection molding polymers to minimize contamination risks.
- ISO Class Standards: Cleanrooms must meet ISO 7 or ISO 8 standards, depending on the sensitivity of the medical device being produced.
- Air Filtration: HEPA filters must be installed to control airborne particles and maintain sterile conditions.
- Controlled Access: Strict protocols for entering and exiting cleanrooms prevent contamination. Employees must wear protective gear, including gloves, masks, and gowns.
Advanced Equipment for Medical Injection Molding
State-of-the-art equipment is crucial for ensuring precision and consistency in the injection molding process.
- Specialized Injection Molding Machines: These machines must support precise temperature control, pressure monitoring, and the ability to process medical-grade polymers.
- Automation Systems: Robotic arms and automated handling systems reduce human contact and improve consistency during production.
- Validation and Monitoring Tools: Equipment should have integrated systems for real-time monitoring and validation to ensure compliance with quality standards.
- Mold Design and Maintenance: High-quality, precision-engineered molds are necessary for creating complex medical components. Regular maintenance prevents defects and ensures longevity.
Material Handling and Storage Requirements
Proper handling and storage of medical injection molding polymers are critical to preserving material integrity and compliance with safety standards.
- Segregated Storage: Medical-grade polymers must be stored in separate, labeled areas to prevent cross-contamination with non-medical materials.
- Temperature and Humidity Control: Storage facilities should maintain specific environmental conditions to preserve polymer properties.
- Traceability: Manufacturers must maintain records for all materials used, including batch numbers and supplier certifications, to ensure traceability in case of issues.
By meeting these conditions, manufacturers can ensure that medical injection molding polymer processes produce reliable, high-quality medical devices that meet stringent industry and regulatory standards.
FUJIU Medical Injection Mold: Your Trusted Partner in Medical Injection Molding Polymer Solutions
At FUJIU Medical Injection Mold, we bring over two decades of excellence as a third-generation, employee-owned company specializing in medical injection molding polymer solutions. Each member of our team is an empowered stakeholder, driving our shared passion for innovation, quality, and collaboration.
We focus on OEM contract manufacturing for the medical device industry, delivering high-precision plastic consumables for equipment and diagnostic kits. From concept to production, we partner with our clients to deliver exceptional outcomes using advanced injection molding technologies.
Our facilities include ISO Class 8 cleanrooms, ensuring the highest standards of cleanliness and precision. With ISO 13485 certification and compliance with FDA and global regulations, we guarantee exceptional quality control throughout every phase of production.
At FUJIU, we believe in fostering strong partnerships. Through open communication and collaboration, we tackle challenges together, leveraging cutting-edge technologies to meet your unique needs while enhancing the value of your products.
FAQs about Medical Injection Molding Polymer
Injection molding involves using a variety of polymers depending on the specific requirements of the product being manufactured. In the medical field, the selection of polymer materials is particularly important due to the need for biocompatibility, strength, durability, and regulatory compliance. Commonly used polymers in medical injection molding include:
Polypropylene (PP): Known for its chemical resistance, low cost, and versatility, polypropylene is widely used in medical applications like syringes, diagnostic devices, and medical packaging.
Polyethylene (PE): This polymer is favored for its flexibility and toughness, making it ideal for products like medical tubing and containers.
Silicone Elastomers: Used for applications requiring flexibility and biocompatibility, such as medical seals, gaskets, and various implantable devices.
Polyetheretherketone (PEEK): A high-performance polymer with excellent mechanical properties, used in demanding applications such as implants and surgical instruments.
Polystyrene (PS): Known for its clarity, it is commonly used for disposable medical devices such as Petri dishes and diagnostic trays.
ABS (Acrylonitrile Butadiene Styrene): This polymer is used in medical products requiring impact resistance and is commonly used for housings of medical equipment.
Each of these polymers is chosen for its ability to meet the specific needs of medical applications, ensuring safety, reliability, and performance.
Injection molding is a crucial process in the production of a wide range of medical devices and components. The versatility and precision offered by this process allow manufacturers to create high-quality products that meet strict medical standards. Some of the medical products commonly made through injection molding include:
Surgical Instruments: Handles, grips, and parts of surgical instruments are often produced using injection molding. These components require high precision, durability, and resistance to repeated sterilization cycles.
Diagnostic Devices: Components for devices such as blood collection tubes, diagnostic trays, and test kits are produced through injection molding. The process ensures accurate and reliable parts for medical diagnostics.
Drug Delivery Systems: Syringes, insulin pens, inhalers, and other drug delivery devices are commonly made using medical injection molding polymers. These devices must be both functional and safe, ensuring that patients receive the correct dosage of medication.
Implants and Prosthetics: Biocompatible polymers like silicone elastomers and PEEK are used to create implants and prosthetics, offering strength, flexibility, and long-term performance.
Medical Packaging: Packaging materials for sterile products, including blister packs and containers, are produced using injection molding. This ensures that the packaging is secure, durable, and safe for healthcare products.
Through injection molding, medical manufacturers can achieve the necessary precision, quality, and regulatory compliance required for these products, ensuring their safety and effectiveness for patient care.
Medical injection molding is a manufacturing process used to produce precision medical components by injecting molten polymers into a mold. This method ensures high accuracy, repeatability, and cleanliness, which are essential for medical devices and equipment. It is commonly used to create parts like syringes, surgical tools, and diagnostic equipment. Medical injection molding is performed in cleanroom environments to minimize contamination and meet strict regulatory standards. The materials used are typically medical-grade polymers, which are biocompatible, durable, and resistant to chemicals and sterilization processes.
Medical-grade polymers are made from specialized plastic resins designed to meet biocompatibility, durability, and safety standards for medical applications. Common types include polycarbonate, polyethylene, polypropylene, and medical-grade silicone. These polymers are often modified with additives to enhance properties like strength, heat resistance, and sterilizability. For example, polycarbonate is known for its clarity and impact resistance, while polypropylene offers chemical resistance. Medical-grade polymers are free from toxic substances, meet ISO 10993 or USP Class VI standards, and are tested for compatibility with sterilization methods like autoclaving or gamma irradiation.
Medical-grade plastics are identified by their compliance with stringent standards and certifications. They must meet ISO 10993 or USP Class VI requirements, which test for biocompatibility, toxicity, and safety. Additionally, medical-grade plastics are subjected to specific sterilization testing to ensure they can withstand methods like autoclaving, ethylene oxide (EtO) treatment, or gamma radiation without degradation. Manufacturers provide certificates of compliance and detailed technical datasheets for such plastics. Labels like “medical-grade” also indicate they are free from harmful substances like BPA, phthalates, and heavy metals, ensuring patient safety.
High-density polyethylene (HDPE) can be formulated as a medical-grade polymer when manufactured to meet the required biocompatibility and safety standards, such as ISO 10993 or USP Class VI. Medical-grade HDPE is often used for items like laboratory containers, surgical trays, and prosthetics because it is lightweight, strong, and resistant to chemicals and moisture. Its compatibility with sterilization methods like EtO and gamma radiation further enhances its suitability for medical applications. However, not all HDPE is medical grade, so verifying compliance with medical standards is essential.
Medical-grade silicone is not classified as a plastic but as an elastomer. It is a synthetic polymer made from silicon, oxygen, carbon, and hydrogen. Unlike plastic, silicone is flexible, highly durable, and resistant to extreme temperatures and sterilization processes. Medical-grade silicone is biocompatible, making it ideal for long-term implantation, wound care products, and prosthetics. It meets strict standards such as ISO 10993 and USP Class VI for medical use and offers properties like hypoallergenic performance, chemical inertness, and resistance to microbial growth.
Medical-grade TPU (thermoplastic polyurethane) is a versatile polymer that combines elasticity, strength, and resistance to chemicals and abrasion. It is biocompatible and commonly used in medical devices such as catheters, tubing, and orthopedic components. Medical-grade TPU offers excellent flexibility, transparency, and durability, making it suitable for applications requiring frequent bending or stretching. It is resistant to sterilization methods, including EtO and gamma radiation. Additionally, TPU can be customized to exhibit properties such as softness or rigidity, depending on the specific requirements of the medical application.
For outdoor applications, UV-resistant and weatherproof materials are the best choices for injection molding. Polycarbonate (PC), polyethylene (PE), and polypropylene (PP) are commonly used due to their durability, resistance to sunlight, and tolerance to temperature fluctuations. Polycarbonate is especially suitable for outdoor medical equipment because of its impact resistance and transparency. If flexibility is needed, thermoplastic elastomers (TPEs) or thermoplastic polyurethanes (TPUs) are excellent options. Additives like UV stabilizers can further enhance the performance of these materials in outdoor environments.
Polypropylene (PP) and polyethylene (PE) are among the cheapest plastics for injection molding. They are widely available, easy to process, and cost-effective for high-volume production. Polypropylene is often used in disposable medical devices due to its lightweight, chemical resistance, and ability to withstand sterilization processes. While these materials are economical, they may not be suitable for all medical applications, especially those requiring stringent biocompatibility or mechanical properties. For specific uses, balance cost with material performance and compliance with medical standards.
Injection molding and plastic casting are two distinct manufacturing processes. Injection molding involves forcing molten polymer into a mold under high pressure, which solidifies to form a part. It is ideal for mass production due to its speed, precision, and repeatability.
Plastic casting, on the other hand, involves pouring liquid polymer resin into a mold, allowing it to cure without applied pressure. Casting is better suited for low-volume production or complex, detailed designs. While injection molding is faster and more cost-efficient for large-scale manufacturing, casting offers more flexibility for intricate or prototype designs.
Injection molding involves injecting molten plastic into a mold cavity to create a single-component part. Insert molding, on the other hand, integrates additional components, such as metal inserts or pre-formed parts, into the mold before plastic injection. The molten plastic then encapsulates the insert, creating a composite part in a single process.
In medical applications, insert molding is preferred when combining plastic with metal components, such as surgical instruments or medical device connectors. It enhances the strength and functionality of medical-grade polymers while reducing assembly steps. Injection molding, widely used for producing high-precision disposable medical items like syringes, remains the standard for single-material products.
China’s medical injection molding industry uses both techniques, offering precision and cost-effectiveness for producing medical-grade components. Advanced machinery and expertise in insert molding enable Chinese manufacturers to deliver high-quality medical parts meeting stringent standards like ISO 10993 and USP Class VI.
“Molding” is a general term that refers to shaping materials into desired forms using molds, encompassing various techniques like injection molding, compression molding, and blow molding. Injection molding is a specific method where molten plastic is injected into a mold cavity under high pressure to create detailed, high-volume parts.
In the medical field, injection molding is particularly important due to its ability to produce intricate, high-precision components, such as syringes and IV connectors, using medical-grade polymers. Other molding techniques, like compression molding, may be better suited for simpler parts or lower production volumes.
China’s expertise in medical injection molding ensures consistent quality for complex medical components, while other molding processes are employed for less demanding applications. The choice of molding method depends on factors like material, design complexity, and production scale, all critical for medical-grade manufacturing.
Injection molding and reaction injection molding (RIM) differ primarily in the materials used and the processing method. Injection molding involves melting thermoplastic polymers and injecting them into a mold, where they cool and solidify. RIM, on the other hand, involves mixing two liquid reactants (often polyol and isocyanate) that chemically react and cure inside the mold to form a thermoset polymer.
In the medical field, injection molding is commonly used for disposable items and high-precision components like syringes or IV connectors made from thermoplastics. RIM, with its ability to create lightweight yet durable parts, is used for applications requiring structural strength, such as casings for medical devices.
China’s medical manufacturing sector leverages both processes to meet diverse requirements. Injection molding is favored for mass production of small, precise parts, while RIM is employed for specialized applications requiring enhanced durability.
ISO 10993 and USP Class VI are two standards for evaluating the biocompatibility of materials used in medical devices, but they differ in scope and application. ISO 10993 is a globally recognized standard for assessing the biological safety of medical devices, covering a wide range of tests like cytotoxicity, sensitization, and systemic toxicity. USP Class VI, a standard from the United States Pharmacopeia, focuses on plastics used in pharmaceuticals and medical devices, testing for biological reactivity through systemic, intramuscular, and subcutaneous injections in animals.
ISO 10993 provides a more comprehensive evaluation, suitable for a broad range of medical devices. USP Class VI is specific to plastics, often serving as a baseline requirement for materials in pharmaceutical applications. In China’s medical injection molding industry, manufacturers frequently comply with both standards to meet international market demands and ensure safety for medical-grade polymers.
Polypropylene (PP) is one of the most common materials used in injection molding, particularly for medical applications. Its chemical resistance, durability, and affordability make it ideal for producing syringes, pill containers, and other disposable medical products.
China’s medical injection molding industry extensively uses polypropylene, alongside other medical-grade polymers like polyethylene (PE), polycarbonate (PC), and thermoplastic elastomers (TPE). The choice of material depends on the specific requirements, such as biocompatibility, sterilization resistance, or flexibility.
By leveraging advanced material technologies and precise molding techniques, Chinese manufacturers produce high-quality medical components meeting stringent standards like ISO 10993. Polypropylene’s versatility and cost-effectiveness make it a cornerstone material in this sector, supporting global healthcare needs.
The material used in injection molding depends on the application, with common options including polypropylene (PP), polyethylene (PE), polycarbonate (PC), and thermoplastic elastomers (TPE). For medical applications, biocompatible and sterilization-resistant materials like medical-grade polycarbonate and polyethylene are widely used.
In China, manufacturers of medical injection-molded parts often utilize materials certified under ISO 10993 and USP Class VI to ensure safety and compliance. These materials are tailored to meet the specific needs of medical devices, such as transparency for diagnostic components or flexibility for tubing and seals.
By offering a diverse range of polymers, the Chinese medical injection molding industry supports the production of high-quality, cost-effective medical devices for global markets, catering to stringent regulatory requirements.
In metal injection molding (MIM), the “plastic” is not traditional plastic but a thermoplastic binder mixed with fine metal powders. This binder temporarily holds the metal particles together during injection molding and is removed during the debinding process, leaving a solid metal part.
For medical applications, the binder systems are designed to ensure compatibility with medical-grade metals like stainless steel or titanium. These materials are commonly used for surgical instruments or implantable devices. In China, MIM is increasingly employed for producing high-precision metal components with complex geometries, supporting the global medical device industry.
Polyether ether ketone (PEEK) is one of the strongest plastics used in injection molding, offering exceptional mechanical strength, thermal stability, and chemical resistance. It is particularly valuable for medical applications requiring high performance, such as spinal implants and dental devices.
In China, PEEK is utilized in advanced medical manufacturing due to its superior biocompatibility and sterilization resistance. Although it is more expensive than other materials, its properties make it indispensable for critical applications where durability and safety are paramount. Chinese manufacturers specializing in medical injection molding use PEEK for producing precision components, meeting global standards for high-strength medical polymers.
Medical grade tubing is typically made of thermoplastic elastomers (TPE), polyvinyl chloride (PVC), or silicone. PVC is widely used due to its flexibility, chemical resistance, and cost-effectiveness, while silicone is preferred for its biocompatibility and resistance to extreme temperatures.
In China’s medical manufacturing industry, these materials are used extensively to produce high-quality tubing for IV lines, catheters, and respiratory devices. Manufacturers ensure compliance with standards like ISO 10993 to guarantee patient safety. Advances in material technologies are also driving the development of eco-friendly alternatives for medical tubing.
Injection molding tools, or molds, are typically made from hardened steel, stainless steel, or aluminum. For medical applications, stainless steel is often preferred due to its corrosion resistance, durability, and ability to withstand sterilization processes.
In China, the production of high-precision molds for medical injection molding involves advanced CNC machining and surface treatments to ensure the molds meet strict quality standards. The choice of material for the mold depends on factors like production volume, complexity, and the material being molded.
Several polymers are used in the medical field, including polycarbonate (PC), polypropylene (PP), polyethylene (PE), and thermoplastic elastomers (TPE). Each polymer has unique properties that suit specific medical applications, such as biocompatibility, sterilization resistance, and mechanical strength.
China’s medical injection molding industry uses these polymers to manufacture a wide range of medical devices, from disposable syringes to implantable components. Manufacturers prioritize compliance with standards like ISO 10993 and USP Class VI to ensure safety and performance in healthcare settings.
Contact our professional team now for a same-day quote and risk-free project evaluation. Benefit from ISO 8 cleanrooms, advanced machines, and 12-hour fast response in medical injection molding.