China has firmly established itself as a global leader in plastic medical injection molding, with a significant focus on medical applications. The country’s dominance in the molding industry is driven by advanced technology, cost efficiency, and a highly skilled workforce. China medical molding factories play a crucial role in producing medical-grade plastic molds and parts, meeting the increasing demand for healthcare products. As the medical industry grows, so does the need for high-precision molding solutions for devices such as syringes, diagnostic equipment, surgical tools, and other essential medical components. These factories offer a wide range of services, including medical mold design, prototyping, and manufacturing, to ensure products meet stringent quality and regulatory standards for global markets.
Low-Volume to High-Volume Production Capabilities
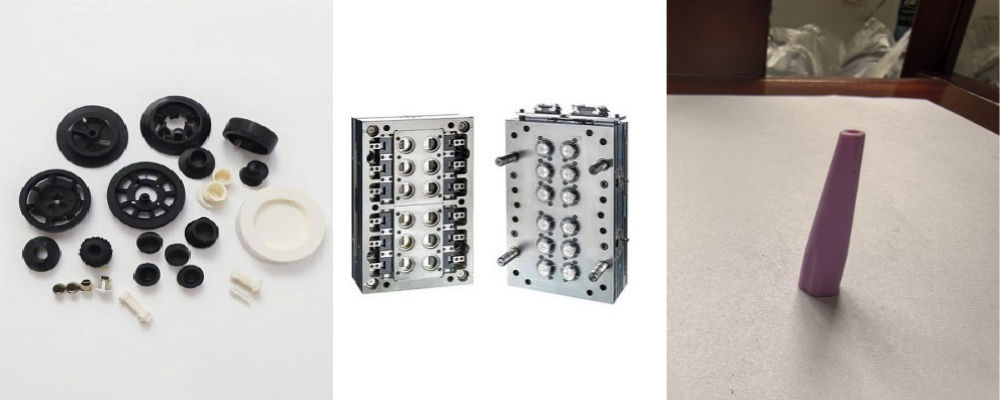
Attributes | Details |
---|---|
Place of Origin | Dongguan, Guangdong, China |
Brand Name | LY Medical Injection Mold |
Product Name | China Medical Molding |
Technology | Injection Molding |
Processing Services | Molding, Cutting |
Color | Customized Color |
Size | Accept Customer's Design |
Shape | Customized Shape |
Service | One-Stop Service |
Feature | Environmentally Friendly |
Advantage | High Quality |
Certification | ISO9001:2008 |
Tolerance | +/-0.01mm / OEM |
OEM | Avaliable |
Selling Units | Single item |
Packing Details | According to Customer's Requirement |
Port | According to Customer's Requirement |
Services Offered by Leading China Medical Molding Factory
China medical molding factories offer a wide range of services that are essential in the production of medical-grade plastic molds and components. These services ensure that medical devices meet the highest standards of quality, safety, and precision.
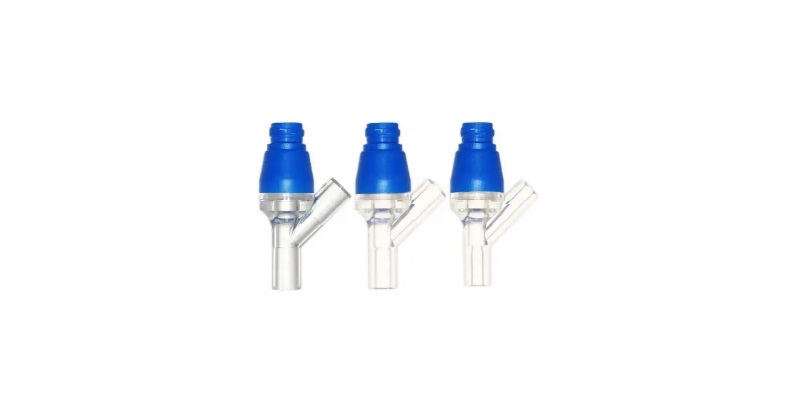
Mold Design and Engineering
One of the key services provided by China medical molding factories is custom mold design and engineering. Medical applications require highly specialized molds that meet stringent regulatory requirements. Custom mold designs ensure that each part is perfectly suited for its intended purpose, whether it’s for a diagnostic tool or a surgical instrument. Leading factories use advanced techniques like 3D modeling, where digital designs are created and tested before physical production begins. Prototyping services allow for the creation of functional prototypes to test mold designs, ensuring the final product meets the necessary specifications. Mold testing is also critical in this phase to evaluate durability, precision, and performance under real-world conditions.
Plastic Injection Molding Process for Medical Devices
The plastic medical injection molding process is at the heart of any China medical plastic mold factory’s operations. This process begins with selecting the right materials, including medical-grade plastics and biocompatible resins, which are essential for ensuring the safety of medical devices. These materials must meet specific standards for quality, including FDA and ISO certifications. Once the materials are chosen, the molding techniques are carefully executed, with each part being molded under precise temperature, pressure, and timing controls to ensure consistency and accuracy. After the molding process, quality control procedures are conducted to confirm that each component meets the required specifications for functionality, safety, and durability.
Post-Molding Services
In addition to the primary molding process, China medical molding factory also offers essential post-molding services to enhance the performance and appearance of medical parts. These services include surface finishing, such as polishing, texturing, and coating, to provide the final aesthetic and functional properties needed for medical devices. CNC machining is often employed to add intricate details or make adjustments to the molded parts. Overmolding, a process that involves adding a second layer of material over the molded part, is frequently used for creating complex components like handles, grips, or seals, which require multi-material structures to meet the specific needs of medical applications.
Major Applications of China Medical Molding Factory in Healthcare
China medical molding factory plays a critical role in the production of high-quality medical devices, and China medical molding factories are at the forefront of this process. From disposable items to complex surgical instruments, these factories provide the precision and reliability needed in healthcare applications worldwide. Below are some of the major applications and specialized needs of medical molding in the healthcare industry.
Common Medical Applications
China medical molding factories are involved in the production of a wide array of common medical devices. These include syringes, IV catheters, blood collection tubes, and surgical instruments. Each of these products requires specialized molds to meet the rigorous standards of the healthcare industry. Syringes and IV catheters, for example, must be designed to ensure accurate delivery of fluids, while blood collection tubes require high precision to prevent contamination and ensure accurate test results. Surgical instruments, ranging from scalpels to forceps, demand not only functionality but also durability and sterilization compatibility.
In addition to these widely used devices, China medical molding factories also produce molds for diagnostic kits, medical disposables, and implants. Diagnostic kits, which include items like test tubes, reagent containers, and specimen holders, must be made from medical-grade plastics that can withstand chemical reactions without compromising the sample integrity. Similarly, medical disposables such as gloves, masks, and wound dressings are often produced using advanced injection molding techniques to achieve high volumes of consistent quality. For implants, which are often made from biocompatible materials, the molding process ensures that each piece fits precisely within the body, promoting healing while minimizing the risk of complications.
Specialized Molding Needs
In addition to common applications, China medical molding factories are also skilled in handling more specialized molding needs for complex medical devices. Molding for medical products like respiratory masks and prosthetics requires not only advanced techniques but also a deep understanding of the specific requirements for these products. For example, respiratory masks must be precisely engineered to ensure a perfect seal for patient safety, which requires molds that allow for flexible materials and exact fit. Prosthetics, on the other hand, demand molds that can produce complex shapes and contours to match the unique anatomy of patients. This level of customization calls for the highest precision in the molding process, making it a highly specialized service.
To meet the demanding requirements of medical devices, China medical molding factories often use cleanroom and sterile molding practices. Cleanrooms are controlled environments designed to minimize contamination, making them essential for the production of medical devices that must meet strict hygiene standards. In these controlled environments, factors like air quality, humidity, and particulate levels are carefully monitored to ensure that every part produced is free from contaminants that could harm patients. Sterile molding practices go a step further by ensuring that the products undergo sterilization either during the molding process or post-production, making them ready for safe use in medical environments.
How China Medical Molding Factory Ensure Quality
China medical molding factories are renowned for their ability to consistently deliver high-quality medical devices and components. The emphasis on precision, quality control, and adherence to international standards is central to the success of these factories in the competitive global market. Here’s a detailed look at how these factories ensure the quality of their products.
Certifications and Standards
One of the most important factors that contribute to the high standards maintained by China medical molding factories is their compliance with internationally recognized certifications and regulations. A crucial certification for medical device plastic manufacturing is ISO 13485, which sets the requirements for a comprehensive quality management system specific to the medical device industry. This certification ensures that factories consistently produce medical products that are safe and effective, meeting both customer and regulatory requirements.
Additionally, China medical molding factories must comply with other key regulatory standards, such as FDA (Food and Drug Administration) approval in the United States and CE marking in Europe. These certifications demonstrate that the factory’s products meet rigorous quality, safety, and performance standards required for medical devices. Compliance with these regulations is essential for factories seeking to market their products in international markets and provides clients with confidence in the factory’s ability to deliver high-quality, compliant products.
Precision and Quality Control
The precision required for manufacturing medical devices and components is extremely high. China medical molding factories employ a variety of advanced techniques to ensure that every product meets stringent specifications. One of the key aspects of ensuring quality is through thorough testing and validation processes. This includes functional testing, sterilization verification, and dimensional checks to confirm that the molds and finished products are accurate and reliable.
Furthermore, many China medical molding factories utilize CPK (Process Capability Index) testing, which measures the capability of a manufacturing process to produce parts within specified tolerance limits. This data-driven approach allows factories to assess their production process’s precision and consistency, helping to identify areas for improvement and minimize variability. In addition to CPK testing, mold acceptance checks are carried out to ensure that each mold is correctly designed and capable of producing consistent, high-quality parts throughout the production cycle.
Client Success Stories
China medical molding factories have a proven track record of successful collaborations with international medical companies, helping to solidify their reputation for quality and reliability. For example, many of these factories have worked with leading global plastic medical device manufacturers to produce components for critical healthcare products such as surgical instruments, diagnostic equipment, and implantable devices.
One notable success story involves a China medical molding factory partnering with a multinational medical device company to develop high precision medical molds for a new line of disposable surgical tools. The collaboration resulted in significant cost savings, faster production timelines, and consistent product quality. This partnership allowed the client to enter the market more efficiently while maintaining the highest standards of patient safety and performance.
Through certifications, rigorous testing, and successful client collaborations, China medical molding factories ensure the production of high-quality, reliable, and compliant medical products, making them a trusted partner for the global healthcare industry.
Advantages of Choosing China Medical Molding Factory
China medical molding factories offer a multitude of advantages for companies looking to produce high-quality medical components and devices. From cost savings to cutting-edge technologies, these factories provide a wide range of benefits that make them a preferred choice for the global medical industry. Below are some of the key reasons why choosing a China medical molding factory can be a strategic decision for your medical molding needs.
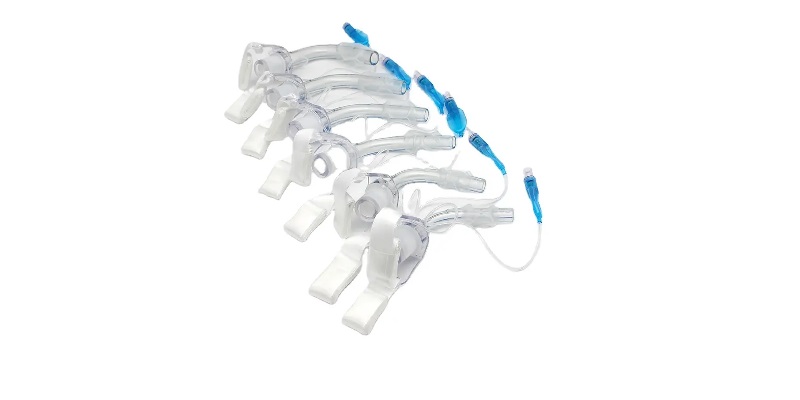
Cost-Effectiveness and Scalability
One of the most compelling reasons to choose China medical molding factories is their cost-effectiveness. China’s manufacturing infrastructure has long been known for its ability to produce high-quality products at competitive prices. This is particularly important for medical companies, where manufacturing costs are a critical factor in ensuring affordability without compromising on quality. The lower labor and production costs in China, combined with efficient processes and economies of scale, enable factories to deliver medical-grade products at a fraction of the cost compared to Western manufacturers.
Additionally, China medical molding factories have the ability to scale production quickly to meet the increasing demand for medical products. Whether you’re looking to produce small batches for prototyping or large quantities for global distribution, Chinese factories are equipped to handle both with ease. Their ability to scale operations helps ensure that manufacturers can fulfill global orders on time, providing flexibility to meet market demands without delays. This scalability is a key reason why many international companies choose to partner with China medical molding factories to meet their production needs.
Advanced Technology and Innovation
Another significant advantage of China medical molding factories is their continuous investment in advanced technology and innovation. These factories employ cutting-edge molding technologies that allow them to produce highly specialized medical components with precision and reliability. For example, multi-component molding is used for producing parts that require multiple materials in a single process, which is essential for creating complex medical devices such as handles for surgical instruments or multi-material implants. Another advanced technique is LSR (Liquid Silicone Rubber) molding, which is often used in medical applications that require biocompatibility, flexibility, and durability, such as seals, gaskets, and surgical masks.
In addition to these innovative molding technologies, China medical molding factories are also equipped with state-of-the-art machinery, including high-precision CNC equipment (Computer Numerical Control) and injection medical molding machines. These machines enable the production of highly detailed components with tight tolerances, ensuring that every part is manufactured with exact precision. Furthermore, these factories maintain clean and controlled manufacturing environments, essential for producing medical-grade products that comply with regulatory standards such as FDA, CE, and ISO.
Rapid Turnaround Times
A significant advantage of choosing China medical molding factories is their rapid turnaround times. In the fast-paced medical industry, the ability to quickly bring a product to market can provide a competitive edge. China medical molding factories are known for their ability to quickly produce prototypes and bring them into full-scale production. With the use of rapid prototyping services such as 3D printing and CNC machining, these factories can create functional prototypes in a matter of days, allowing medical companies to test and iterate on their designs quickly. This speed in prototyping helps minimize development time, accelerating the time to market for new medical devices and components.
Moreover, China medical molding factories are capable of optimizing production timelines for bulk manufacturing. Their well-established supply chains, skilled labor force, and efficient processes allow for shorter production cycles without sacrificing quality. This efficiency is crucial for medical companies that need to meet urgent deadlines or respond to sudden spikes in demand, such as during a global health crisis or when launching a new product line.
China Factory Injection Molding of Medical Atomization Mask
In recent years, the demand for medical atomization masks—a critical tool in the treatment of respiratory diseases—has grown significantly. China factory injection molding of medical atomization masks plays an essential role in the production of these devices, which are used in hospitals, clinics, and homes for aerosol drug delivery. These masks require precise molding techniques to ensure that the components are made from biocompatible materials and are capable of withstanding sterilization processes.
The medical atomization mask injection molding processing involves the use of high-precision injection molding technology to create the intricate and delicate parts needed for these devices. This process allows manufacturers to form the mask’s body, filters, and air pathways with consistent accuracy. China medical molding factories specializing in injection molding for medical atomization masks utilize advanced equipment and technology to meet stringent quality standards, ensuring that each component is made to the highest specifications.
Moreover, these factories ensure that the masks comply with strict ISO 13485 and FDA regulations, guaranteeing safety and effectiveness in treating patients. The combination of rapid prototyping, cleanroom environments, and advanced molding techniques in the medical atomization mask injection molding processing enables these factories to meet the growing global demand for high-quality medical atomization masks.
China Medical Plastic Injection Molding Factory
A China medical plastic injection molding factory is specialized in manufacturing plastic components used across a wide range of medical applications. These factories employ advanced plastic injection molding techniques to produce components for medical devices, diagnostic tools, and other healthcare products. The use of medical-grade plastics, such as biocompatible resins and polycarbonate, ensures that the parts meet stringent healthcare regulations.
These China plastic medical injection molding factories are equipped with modern machinery and technology, such as CNC machines and automated assembly lines, to deliver precise, high-quality components. These factories are capable of creating a variety of medical plastic parts, including housings for medical equipment, surgical instruments, and sterilization trays. Furthermore, the use of cleanroom facilities ensures that parts are manufactured in sterile environments, minimizing the risk of contamination.
Materials Used by China Medical Molding Factory for Medical Injection Molding
China medical molding factory stands at the forefront of producing high-quality medical components, driven by its expertise in material selection for medical injection molding. The choice of materials plays a critical role in ensuring that medical devices meet stringent industry standards, including biocompatibility, durability, resistance to sterilization, and compatibility with medical-grade applications. Factories carefully evaluate each material’s properties to guarantee compliance with regulatory requirements while maintaining functionality, reliability, and cost-effectiveness. This process involves matching materials to the specific needs of medical devices, from disposable items to long-term implants. Below, we delve deeper into the material categories commonly used in medical injection molding, highlighting their importance and applications within this specialized manufacturing process.
Biocompatible Materials
Biocompatibility is the foundation of all medical injection molding materials, ensuring safety for patient contact. These materials are rigorously tested to minimize risks such as allergic reactions, cytotoxicity, and long-term degradation in biological environments.
- Medical-Grade Polypropylene (PP): Lightweight and cost-effective, PP is commonly used for disposable medical items like syringes, IV bags, and laboratory equipment. It is resistant to moisture, chemicals, and fatigue, making it ideal for single-use products.
- Polycarbonate (PC): A versatile material known for its clarity, impact resistance, and sterilization compatibility. It is extensively used in applications such as blood oxygenators, dialysis equipment, and surgical instrument housings, where transparency and strength are critical.
- Thermoplastic Elastomers (TPE): Combining the benefits of plastics and rubber, TPE offers flexibility and softness. It is frequently used for seals, catheters, and other components requiring a comfortable interface with the human body.
Sterilization-Resistant Materials
Medical devices often undergo rigorous sterilization to ensure patient safety. Materials chosen for these applications must endure repeated exposure to high temperatures, chemicals, or radiation without degradation.
- Polyetherimide (PEI): A high-performance thermoplastic, PEI excels in high-temperature sterilization environments such as autoclaving. Its exceptional strength and resistance to thermal deformation make it a preferred choice for reusable surgical instruments.
- Polyphenylsulfone (PPSU): PPSU offers even greater sterilization resistance than PEI, maintaining its mechanical properties and transparency after hundreds of steam sterilization cycles. It is used for surgical trays, dental instruments, and sterilization containers.
High-Strength and Durable Materials
Many medical devices require materials capable of withstanding mechanical stress, prolonged use, or harsh operating conditions. These materials ensure product longevity and reliability in critical medical applications.
- Acrylonitrile Butadiene Styrene (ABS): Known for its excellent balance of toughness and rigidity, ABS is commonly used for durable device enclosures, such as electronic monitors or ventilator housings. Its ability to maintain structural integrity under stress makes it a staple in the medical industry.
- Nylon (PA): With high tensile strength and abrasion resistance, nylon is ideal for components that require flexibility and durability, such as catheter fittings and surgical tools. Its lightweight nature further enhances its usability in intricate medical designs.
Transparent and UV-Resistant Materials
For applications requiring visibility, such as fluid flow monitoring or diagnostic instruments, transparent materials are critical. These materials must also resist UV degradation to maintain clarity over time.
- Cyclic Olefin Copolymer (COC): Known for its superior optical clarity and resistance to UV light, COC is widely used in diagnostic lenses, microfluidic devices, and sample vials. Its low water absorption also enhances its suitability for sensitive medical environments.
- Polymethyl Methacrylate (PMMA): Commonly referred to as acrylic, PMMA combines excellent transparency with a high resistance to scratching and weathering. It is frequently used in optical medical devices such as endoscopes and light guides.
Specialized Materials for Drug Delivery Systems
Drug delivery systems demand materials with exceptional chemical resistance and the ability to maintain their structural integrity when exposed to various pharmaceutical formulations.
- Fluoropolymers: These non-reactive materials are ideal for coatings in drug delivery devices, where chemical stability is paramount. Fluoropolymers are also hydrophobic, making them suitable for applications that require minimal moisture absorption.
- Polyethylene (PE): Low-density polyethylene (LDPE) and high-density polyethylene (HDPE) are frequently used for pharmaceutical containers, tubing, and IV bags. Their inertness ensures that drugs remain uncontaminated during storage and delivery.
China medical molding factory combines advanced materials with cutting-edge manufacturing techniques to produce medical components that meet stringent global standards. Each material is carefully selected based on its properties and specific application, ensuring the production of safe, durable, and highly reliable medical devices.
Essential Equipment for China Medical Molding Factory in Medical Injection Molding
China medical molding factories require a comprehensive array of equipment to meet the stringent demands of medical injection molding. These facilities are designed to produce high-precision medical components while adhering to strict regulatory standards. The equipment spans several critical areas, from injection molding machines and molds to auxiliary systems and quality control tools. Each type of equipment plays a vital role in ensuring that the factory operates efficiently, consistently delivering high-quality medical products. Below is a breakdown of the essential equipment used in these factories, categorized under key functional areas.
Injection Molding Machines
Injection molding machines are the backbone of any medical molding factory. These machines inject molten plastic into molds to produce medical components with high precision.
- Types of Machines: Most factories use electric or hybrid machines due to their accuracy, efficiency, and ability to meet tight tolerances required for medical products.
- Cleanroom Compatibility: Medical molding often requires machines that can operate within cleanroom environments to prevent contamination. These machines are equipped with features like minimal oil usage and enclosed designs to maintain cleanliness.
- Capacity: Machines with varying clamping forces (from 20 tons to over 500 tons) are used to accommodate parts of different sizes and complexities.
Molds and Tooling
Molds are critical for shaping the final product and must be manufactured with extreme precision.
- Medical-Grade Materials: Molds are typically made from hardened steel or aluminum to ensure durability and compatibility with medical-grade plastics.
- High Precision: China medical molding factories use advanced CNC machines and EDM (Electrical Discharge Machining) to create molds with intricate details and tight tolerances.
- Multi-Cavity Molds: For high-volume production, multi-cavity molds are used to produce multiple components simultaneously, improving efficiency.
Auxiliary Equipment
Auxiliary equipment supports the injection molding process, ensuring consistent quality and efficiency.
- Material Dryers: These are used to remove moisture from medical-grade plastics, such as polycarbonate or polypropylene, before molding, as moisture can compromise product integrity.
- Temperature Controllers: Accurate mold temperature control is crucial for maintaining part consistency. Factories use water or oil-based systems to regulate mold temperatures.
- Robotic Systems: Robots are often integrated to handle tasks like part removal, assembly, or packaging, reducing human contact and contamination risks.
- Material Conveyors: These systems transport raw materials automatically to the machines, ensuring continuous production without interruptions.
Cleanroom Equipment
Cleanrooms are essential in medical molding to maintain a sterile production environment.
- Cleanroom Certification: Most factories operate ISO Class 7 or Class 8 cleanrooms, depending on the product requirements.
- HEPA Filters: High-efficiency particulate air (HEPA) filters are installed to remove airborne particles and contaminants.
- Airflow Systems: Laminar flow hoods ensure clean airflow around critical processes like molding and assembly.
Quality Control and Testing Equipment
To meet medical standards, rigorous quality checks are essential, requiring specialized testing equipment.
- Inspection Machines: Optical and coordinate measuring machines (CMMs) are used to inspect dimensions and ensure products meet design specifications.
- Biocompatibility Testing: Equipment for testing material compatibility with biological systems is crucial for ensuring the safety of medical devices.
- Tensile and Compression Testers: These test the mechanical properties of molded parts to ensure strength and durability.
- Visual Inspection Tools: Microscopes and automated vision systems detect defects like warping, flash, or contamination.
Software and Automation Systems
Automation and software tools are essential for managing and optimizing production processes.
- CAD and CAM Software: These are used for mold design and machining, ensuring precision and minimizing errors.
- Production Monitoring Systems: Real-time monitoring systems track parameters like temperature, pressure, and cycle time, allowing factories to maintain consistent quality.
- ERP Systems: Enterprise Resource Planning (ERP) software helps in managing inventory, scheduling, and compliance with medical regulations.
China medical molding factories rely on this extensive range of equipment to produce high-quality, reliable medical components efficiently. By combining advanced machinery, cleanroom environments, and robust quality assurance systems, these factories meet the rigorous demands of the global healthcare industry.
Importance of Medical Plastic Injection Molding to China Medical Molding Factory
Medical plastic injection molding plays a crucial role in the success of a China medical molding factory. It is the cornerstone of manufacturing high-quality, cost-effective medical components with precision, consistency, and scalability. Leveraging this technology allows Chinese factories to meet the rigorous demands of global medical industries while offering competitive pricing. Below, we explore the importance of medical plastic injection molding through various aspects, including its control and reliability, ability to support high-volume production, suitability for enclosures, and the versatility it offers in medical device manufacturing.
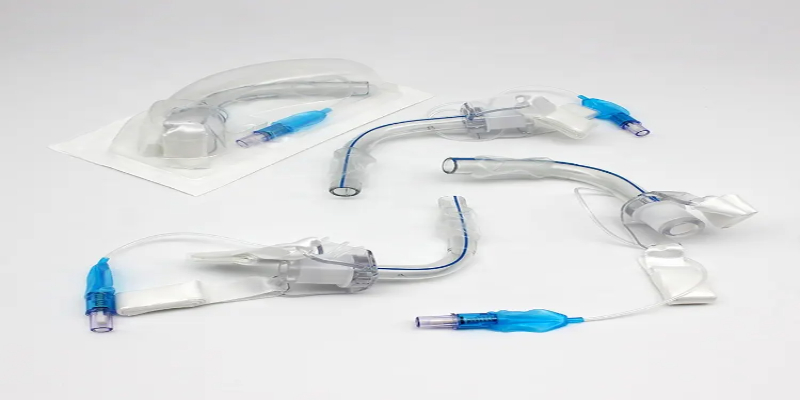
Provides Control and Reliability
The stability and reliability of medical plastic injection molding make it indispensable for Chinese medical molding factories.
- Enhanced Design and Process Optimization: Advanced modeling software reduces design guesswork, enabling moldmakers to perfect tool designs and streamline production processes. This ensures components meet strict medical industry tolerances.
- Consistency in Quality: Medical injection molding ensures repeatability, producing identical parts in every cycle. This is crucial for medical devices that require high reliability, such as syringes, test kits, and surgical tools.
- Cost Efficiency: By minimizing lead times and maximizing process efficiency, this method lowers overall production costs, which is a significant advantage for competitive markets like China.
Supports High-Volume Production
China’s medical molding factories excel in high-volume production thanks to injection molding’s scalability and efficiency.
- Upfront Investment with Long-Term Benefits: While the initial costs for mold design and development are high, the low cost per unit over time offsets these expenses. This is ideal for manufacturing thousands or even millions of identical medical parts.
- Efficient Manufacturing: Injection molding allows factories to produce complex components quickly and in large quantities, ensuring rapid turnaround times for high-demand medical devices.
Ideal Solution for Medical Device Enclosures
Medical device enclosures and housings are best manufactured using plastic injection molding due to its cost-effectiveness and precision.
- Material Efficiency: Unlike other methods, injection molding uses minimal raw materials, reducing waste and overall production costs.
- Rapid Production: With shorter production times and the ability to mass-produce housings, factories can deliver orders faster.
- Medical-Grade Plastics: Using biocompatible and sterilizable plastics ensures that the enclosures meet stringent medical safety standards.
Versatility in Medical Device Manufacturing
The versatility of medical plastic injection molding allows factories to manufacture a wide range of devices for diverse applications.
- Customizable Material Properties: Plastic resins can be selected based on specific requirements, such as biocompatibility, chemical resistance, or thermal stability. For example, polyethylene is used for flexible parts, while polycarbonate is chosen for transparent components.
- Diverse Applications: From disposable items like catheter tips to durable implants and diagnostic equipment parts, injection molding supports a broad spectrum of medical device production.
- Environmental Compatibility: Biodegradable plastics can be used for sustainable medical products, aligning with growing global demand for eco-friendly solutions.
Medical plastic injection molding is indispensable to a China medical molding factory, driving the production of reliable, cost-effective, and high-quality medical devices. Its ability to ensure precision and scalability while using versatile materials makes it a preferred manufacturing method. By leveraging advanced injection molding technologies, Chinese factories continue to play a vital role in meeting global healthcare needs with innovative and affordable solutions.
Factors to Consider When Choosing a China Medical Molding Factory
Choosing the right China medical molding factory is a critical decision for businesses in the medical industry. It affects the quality, durability, and safety of medical components, as well as production efficiency and overall project success. From production capacity to internal quality assurance, many factors must be evaluated to ensure the factory can meet your requirements and deliver optimal results. Below, we explore these factors in detail, providing a layered perspective on what makes a factory the right choice for medical injection molding projects.
Production Volume & Capacity
Before selecting a factory, it is essential to evaluate its production capabilities and capacity. This ensures the factory can handle the required volume while maintaining consistent quality.
- Injection Molding Expertise: The factory should specialize in medical plastic injection, as this process demands high precision and expertise.
- Material Quality: High-quality plastic raw materials are vital to produce durable medical devices and consumables that meet industry standards. Factories must use biocompatible and safe materials to maintain patient safety.
- Scalability: Ensure the factory can scale production based on your needs, whether for small batch runs or high-volume production.
A Range of Services
A factory offering comprehensive, one-stop manufacturing services can streamline the production process and save time and costs.
- Design and Concept Development: The factory should assist from the design stage, ensuring that your medical components are functional, cost-effective, and manufacturable.
- Prototyping and Testing: Factories with prototyping capabilities can help refine your designs and test functionality before full-scale production.
- Mold Flow Analysis: Advanced analysis ensures efficient material flow during injection molding, reducing defects and optimizing production.
Experienced Design Team
The design phase is one of the most critical steps in medical injection molding. Working with a factory that has a skilled design team can make a significant difference in achieving your goals.
- Collaborative Design Process: The factory should involve its design team early in the production process to ensure manufacturability and minimize material waste.
- Maximizing ROI: A well-designed medical plastic part can reduce material usage and enhance performance, helping to lower costs while achieving high functionality.
- Innovative Problem-Solving: An experienced team can identify potential issues and suggest design improvements to ensure the success of your project.
Applications for All Products
A top-tier factory should have the capability to provide tailored solutions for a wide range of medical applications.
- Material Selection: The factory must help select the best plastic resin based on the product’s end use and budget. For example, choosing biocompatible and sterilization-resistant materials is crucial for medical applications.
- End-to-End Guidance: Factories should offer guidance through every stage of manufacturing, from material selection to final assembly, to ensure a smooth production process.
Specifications & Technology
The ability to meet specific requirements and leverage advanced technology is essential when choosing a China medical molding factory.
- Custom Specifications: The factory should produce components to exact specifications, ensuring they meet the strict tolerances required for medical devices.
- Advanced Machinery: Factories equipped with state-of-the-art technology, such as precision molding machines, can deliver consistent quality and efficiency.
- Expert Recommendations: The factory must provide expert advice and adjustments based on the product’s unique requirements.
Internal Quality Assurance
Quality assurance is non-negotiable in the medical industry, where precision and reliability are paramount.
- ISO Certification: Look for factories with ISO certifications, which demonstrate their commitment to maintaining global quality standards.
- Rigorous Testing Processes: A robust internal quality assurance team should monitor every stage of production, from raw materials to the finished product, ensuring that all components meet regulatory requirements.
- Reputation and Track Record: Conduct background checks to verify the factory’s reputation, performance history, and ability to deliver high-quality medical parts consistently.
Choosing a China medical molding factory requires careful consideration of these factors to ensure the production of safe, reliable, and high-performing medical components. A factory that combines expertise, advanced technology, and strict quality assurance processes is the ideal partner for achieving success in the highly competitive medical industry.
FAQs about China Medical Molding Factory
Injection molding can last for a long time, particularly when it comes to high-quality molds and materials. The lifespan of an injection mold depends on factors such as the material used, the complexity of the design, and the maintenance of the mold. In a China medical molding factory, medical-grade injection molds are designed to withstand thousands to millions of cycles before requiring replacement or refurbishment. For medical applications, durability is crucial, and factories ensure their molds are made from high-quality steels or alloys to handle repetitive use without compromising the safety or performance of the medical parts. Regular maintenance and timely repairs help extend the lifespan of molds. Typically, molds can last for 1 to 5 years or longer, depending on usage, mold care, and the type of medical device being produced.
The cost of injection molding per hour can vary widely based on several factors, including the complexity of the design, the type of material used, the size of the parts being produced, and the production volume. In China medical molding factories, costs are often lower than in other regions due to labor cost advantages and efficient production processes. On average, injection molding costs range from $50 to $150 per hour, though this can fluctuate based on the specific requirements. In medical molding applications, where strict quality and compliance standards are necessary, costs may be on the higher end, reflecting the specialized equipment and expertise needed for precision manufacturing. Additionally, setup fees, mold creation, and post-production testing may affect the overall cost.
The cost of creating a plastic injection mold in a China medical molding factory can range significantly depending on the complexity, size, and material of the mold. On average, mold costs can vary from $1,000 to over $100,000. For medical applications, which require precision, high-quality materials, and compliance with strict regulatory standards, the cost tends to be on the higher end. Medical-grade molds typically use durable materials like steel, which can increase mold costs. The mold’s design complexity, the number of cavities, and the size of the part being molded also contribute to the cost. In some cases, medical molding factories may offer lower-cost options by using more streamlined manufacturing techniques while ensuring that the final mold meets stringent regulatory standards for biocompatibility and safety.
Injection molding can be quite profitable, especially when producing high-demand products in large quantities. China medical molding factories benefit from cost-effective labor and a well-developed manufacturing infrastructure, which helps reduce production costs and increase profitability. In medical applications, profitability also comes from the high precision and specialized nature of the parts produced. Molds are typically used for large production runs, which can help spread the cost of mold creation over a large volume, improving profitability. Additionally, China’s medical molding factories often focus on producing high-quality, biocompatible medical parts, which command premium prices due to their essential role in the healthcare industry. Overall, when managed efficiently, injection molding in the medical field can be highly profitable, especially when producing complex, high-precision parts that are critical for patient safety.
Yes, injection molding is generally cheaper than machining, especially for mass production of parts. This is especially true in a China medical molding factory, where labor costs and economies of scale help keep prices low. Injection molding is an efficient process for producing large volumes of identical parts, which allows the initial cost of mold creation to be amortized across many pieces, making the per-unit cost significantly lower as production quantities increase. Machining, on the other hand, involves removing material from a solid block, which is more time-consuming and typically more expensive for large-volume production. While machining may be preferred for small quantities or highly intricate parts, injection molding is more cost-effective for large-scale production of parts, such as those used in medical devices, where precision and volume are key factors.
Injection molding is a specialized process that can be challenging for those who are not familiar with it. However, with the right equipment, expertise, and experience, it becomes easier to manage. In a China medical molding factory, professionals are well-versed in the intricacies of the process, especially when it comes to the production of medical parts that require precise tolerances and biocompatibility. The complexity of injection molding lies in the mold design, material selection, and the fine-tuning of injection parameters to ensure consistent quality in each produced part. For medical applications, strict regulatory compliance and quality standards must be met, which adds an additional layer of complexity. Overall, while injection molding can be challenging, the advanced technology and skilled workforce in China medical molding factories make it manageable, ensuring high-quality outcomes.
Injection molding is generally more cost-effective than 3D printing for large production runs, but 3D printing can be a more economical option for smaller production quantities or prototyping. In a China medical molding factory, where high-volume production is common, injection molding tends to be cheaper due to economies of scale. The cost per unit decreases as the quantity increases, especially after the initial investment in molds. On the other hand, 3D printing does not require mold creation, making it a cost-effective option for low-volume production or custom prototypes. However, 3D printing can be slower and more expensive per unit for large quantities of parts, especially in medical applications where precision and material properties are crucial. While 3D printing is an excellent option for rapid prototyping or low-volume runs, injection molding is generally more economical for large-scale production of medical parts.
Injection molding is widely popular in China’s medical manufacturing industry due to its ability to produce high-precision components at a low cost per unit. The process ensures consistent quality, which is critical for medical devices. It is also scalable, making it ideal for both small and large production runs. Additionally, Chinese factories have adopted cutting-edge technology, including automation and cleanroom facilities, to meet stringent medical standards. The versatility of injection molding allows manufacturers to work with a wide range of materials, including biocompatible and sterilizable options, catering to diverse medical applications. Combined with China’s competitive pricing, extensive supply chain, and skilled workforce, injection molding has become the go-to choice for producing reliable and affordable medical components on a global scale.
Polypropylene (PP) is the most common raw material used in medical injection molding due to its versatility, affordability, and biocompatibility. It is widely used in Chinese medical molding factories for manufacturing disposable medical items such as syringes, test tubes, and specimen containers. PP’s chemical resistance and ease of processing make it ideal for high-volume production. Other popular materials include polyethylene (PE), polystyrene (PS), and acrylonitrile butadiene styrene (ABS), depending on the application. Chinese factories often source raw materials locally to reduce costs while maintaining strict quality control to meet international medical standards. The availability of diverse materials, combined with advanced molding technology, allows China’s medical molding industry to offer cost-effective solutions for a wide range of healthcare applications.
Polyetheretherketone (PEEK) is considered one of the hardest plastics for injection molding, known for its strength, durability, and resistance to high temperatures. In the medical industry, PEEK is often used for implants and components requiring exceptional mechanical performance and biocompatibility. However, PEEK’s hardness also makes it challenging to mold, requiring specialized machinery, high processing temperatures, and precision tooling. Many medical molding factories in China have the expertise and advanced equipment to handle PEEK efficiently, although it comes with a higher cost compared to other materials. Despite its challenges, PEEK is highly sought after for medical applications due to its performance, and Chinese manufacturers leverage their cost advantages and technical expertise to produce high-quality PEEK components at competitive rates.
The key difference lies in the material and application. Silicone injection molding uses liquid silicone rubber (LSR), which is highly flexible, biocompatible, and heat-resistant, making it ideal for soft medical components like seals, tubing, and baby products. In contrast, plastic injection molding uses thermoplastics, which are better suited for rigid or semi-rigid medical devices such as syringe barrels or surgical instrument handles. Chinese medical molding factories often specialize in both processes, with silicone molding being more complex due to the material’s properties. Silicone molds generally require more advanced machinery and precise temperature control, increasing costs slightly compared to plastic. Both processes ensure high precision, but the choice depends on the product’s intended use. Chinese factories excel at delivering both options, offering cost-effective and high-quality solutions for global medical device manufacturers.
Medical molding factories in China commonly use medical-grade plastics like polypropylene (PP), polycarbonate (PC), and polyethylene (PE). Polypropylene is widely regarded as one of the best materials due to its biocompatibility, chemical resistance, and cost-effectiveness. It is ideal for disposable medical items like syringes and test tubes. Polycarbonate is preferred for applications requiring transparency and high impact strength, such as surgical instruments. Medical-grade PE is another excellent choice, particularly for flexible components. Chinese factories often collaborate with clients to select the most suitable material based on part specifications and medical application requirements. Regulatory compliance is critical, so materials are chosen to meet international standards such as FDA and ISO certifications. The combination of material quality and precise injection molding processes makes Chinese manufacturers reliable partners for medical-grade production.
Manufacturing costs in China vary depending on factors like the complexity of the part, material used, and production volume. For medical injection molding, costs tend to be higher due to the need for specialized medical-grade resins, cleanroom manufacturing, and compliance with certifications like ISO 13485. On average, mold creation costs can range from $5,000 to $30,000 depending on part complexity, while unit production costs can be as low as $0.10 to $5 per piece for high-volume production. Chinese medical molding factories keep costs competitive through efficient labor, modern equipment, and large-scale operations. These factories also benefit from proximity to raw material suppliers, further reducing expenses. For businesses, outsourcing to China is a cost-effective option for medical molding while still maintaining high-quality standards.
For medical molding factories in China, the disadvantages of injection molding primarily revolve around high upfront costs and the need for specialized expertise. Designing and manufacturing molds for medical components require significant investment due to tight tolerances and regulatory requirements. Additionally, making modifications to the mold can be complex and expensive, especially for medical applications where precision is paramount. Another disadvantage is the material limitation—only thermoplastics and specific grades of medical-grade resins can be used, which may restrict design flexibility. Cycle times can be slow for intricate parts, affecting production efficiency. Furthermore, improper quality control can lead to product defects, particularly in medical molding where accuracy is crucial. However, leading Chinese medical molding factories mitigate these drawbacks through advanced machinery, strict quality assurance processes, and cost-effective mold production, ensuring compliance with international medical standards.
Injection molding offers significant cost efficiency for high-volume production, making it popular for medical molding in China. The initial setup, including mold design and manufacturing, is expensive due to the precision required for medical-grade parts. However, once the mold is ready, the per-unit production cost is relatively low, especially in large quantities. In China, the combination of lower labor costs, advanced manufacturing facilities, and economies of scale reduces overall costs. Medical molding in particular requires stringent quality controls and certifications, which may slightly increase costs compared to other industries. However, Chinese factories excel in balancing affordability and quality, leveraging advanced technology and competitive pricing to attract global clients. Ultimately, while initial expenses are high, injection molding becomes economically viable as production volumes increase, making it ideal for producing medical components with consistent precision and reliability.
Contact our professional team now for a same-day quote and risk-free project evaluation. Benefit from ISO 8 cleanrooms, advanced machines, and 12-hour fast response in medical injection molding.